Лазерная резка — Википедия
Материал из Википедии — свободной энциклопедии
Текущая версия страницы пока не проверялась опытными участниками и может значительно отличаться от версии, проверенной 31 августа 2018; проверки требует 21 правка. Текущая версия страницы пока не проверялась опытными участниками и может значительно отличаться от версии, проверенной 31 августа 2018; проверки требует 21 правка. Лазерная резка листа стали.Лазерная резка — технология резки и раскроя материалов, использующая лазер высокой мощности и обычно применяемая на промышленных производственных линиях. Сфокусированный лазерный луч, обычно управляемый компьютером, обеспечивает высокую концентрацию энергии и позволяет разрезать практически любые материалы независимо от их теплофизических свойств. В процессе резки, под воздействием лазерного луча материал разрезаемого участка плавится, возгорается, испаряется или выдувается струей газа. При этом можно получить узкие резы с минимальной зоной термического влияния. Лазерная резка отличается отсутствием механического воздействия на обрабатываемый материал, возникают минимальные деформации, как временные в процессе резки, так и остаточные после полного остывания. Вследствие этого лазерную резку, даже легкодеформируемых и нежестких заготовок и деталей, можно осуществлять с высокой степенью точности. Благодаря большой мощности лазерного излучения обеспечивается высокая производительность процесса в сочетании с высоким качеством поверхностей реза. Легкое и сравнительно простое управление лазерным излучением позволяет осуществлять лазерную резку по сложному контуру плоских и объемных деталей и заготовок с высокой степенью автоматизации процесса.
Для лазерной резки металлов применяют технологические установки на основе твердотельных, волоконных лазеров и газовых CO2-лазеров, работающих как в непрерывном, так и в импульсно-периодическом режимах излучения. Промышленное применение газо-лазерной резки с каждым годом увеличивается, но этот процесс не может полностью заменить традиционные способы разделения металлов. В сопоставлении со многими из применяемых на производстве установок стоимость лазерного оборудования для резки ещё достаточно высока, хотя в последнее время наметилась тенденция к её снижению. В связи с этим процесс лазерной резки становится эффективным только при условии обоснованного и разумного выбора области применения, когда использование традиционных способов трудоемко или вообще невозможно.
Лазерная резка осуществляется путём сквозного прожига листовых металлов лучом лазера. Такая технология имеет ряд очевидных преимуществ перед многими другими способами раскроя:
- Отсутствие механического контакта позволяет обрабатывать хрупкие и легко деформирующиеся материалы;
- Возможна высокоскоростная резка тонколистовой стали;
- При выпуске небольших партий продукции целесообразнее провести лазерный раскрой материала, чем изготавливать для этого дорогостоящие пресс-формы или формы для литья;
- Для автоматического раскроя материала достаточно подготовить файл рисунка в любой чертёжной программе и перенести файл на компьютер установки, которая выдержит погрешности в очень малых величинах.
Для лазерной резки подходит любая сталь любого состояния, алюминий и его сплавы, другие цветные металлы. Обычно применяют листы из таких металлов:
Для разных материалов применяют различные типы лазеров.
Лучше всего обрабатываются металлы с низкой теплопроводностью, так как в них энергия лазера концентрируется в меньшем объеме металла, и наоборот, при лазерной резке металлов с высокой теплопроводностью может образоваться грат.
Также могут обрабатываться многие неметаллы — например, дерево.
Лазер и его оптика (включая фокусирующие линзы) нуждаются в охлаждении. В зависимости от размеров и конфигурации установки, избыток тепла может быть отведен теплоносителем или воздушным обдувом. Вода, часто применяемая в качестве теплоносителя, обычно циркулирует через теплообменник или холодильную установку.
Эффективность промышленных лазеров может варьироваться от 5% до 45%. Энергопотребление и эффективность будут зависеть от выходной мощности лазера, его рабочих параметров и того, насколько хорошо лазер подходит для конкретной работы. При определении целесообразности использования того или иного типа лазера учитывается как стоимость лазера в совокупности с обслуживающим его оборудованием, так и стоимость содержания и обслуживания лазера. В 10-х годах XXI столетия эксплуатационные издержки оптоволоконного лазера составляют около половины от эксплуатационных издержек углекислотного лазера.
Величина необходимой затрачиваемой мощности, необходимой для резки, зависит от типа материала, его толщины, среды обработки, скорости обработки.
- С. А. Астапчик, В. С. Голубев, А. Г. Маклаков. Лазерные технологии в машиностроении и металлообработке (рус.). — Белорусская наука, 2008. — ISBN 978-985-08-0920-9.
- Черпаков Б.И., Альперович Т.А. Металлорежущие станки (неопр.). — ISBN 5-7695-1141-9.
- Colin E. Webb, Julian D.C. Jones. Handbook Of Laser Technology And Applications (Справочник по лазерным технологиям и их применению) book 1 (рус.). — IOP. — ISBN 0-7503-0960-1.
Colin E. Webb, Julian D.C. Jones. Handbook Of Laser Technology And Applications (Справочник по лазерным технологиям и их применению) book 2 (рус.). — IOP. — ISBN 0-7503-0963-6.- Steen, Wlliam M. Laser Material Processing (неопр.). — 2nd edition. — Great Britain: Springer-Verlag, 1998. — ISBN 3-540-76174-8.
Лазерная резка металла — преимущества и недостатки технологии
Из школьного курса элементарной физики вы знаете о сильном тепловом воздействии сфокусированного света. Познавательный трюк с увеличительным стеклом ясно показывает возможности преломленного потока солнечного луча.
Принципом действия работы лазера может служить его перевод с английского: усиление света вынужденным излучением. По-простому — это световое излучение, вызванное атакой фотонов на рабочую среду с усилением за счет ответной реакции. Световой поток через систему оптических призм и зеркал фокусируется в узконаправленный луч импульсной или непрерывной модуляции. Мощность и интенсивность лазера зависит от используемого активатора и сложности резонирующих систем.
В качестве первичного активного вещества используют все возможные агрегатные состояния: твердое, газообразное, жидкое и плазменное. Важнейшим критерием является способность к возбуждению и отдаче свободных квантов-фотонов. Накачка первичных световых атомов производится разными способами. Это может быть сфокусированное солнечное излучение, специальные лампы, другие лазеры, электрическое воздействие или химические процессы. Для увеличения силы потока делают многоуровневые атакующие каскады. В основе резонаторов применяют плоскопараллельные и сферические зеркала или их комбинации. Главный параметр хорошего прибора — устойчивое сохранение светового луча и его точная фокусировка.


Принцип лазерной резки
Первый лазер был сделан на рубине в 1960 году, он работал в инфракрасном диапазоне и являлся началом эры световых помощников человека. История развития прикладной квантовой науки шла по пути усиления первоначальных систем накачки и совершенствования оптических резонаторов для достижения мощного и управляемого луча. Выискивались новые рабочие среды, были испробованы и получили путевку в жизнь лазерные установки на красителях, на свободных электронах, химические модели и полупроводниковые исполнения.
Производственное использование лазера
Лазер называют самым красочным и одним из важнейших изобретений XX века. Многие годы никто не понимал его практического применения, прибор называли устройством, которое само ищет задачи для решения. Теперь лазерные аппараты лечат людей, исследуют звезды и применятся для развлекательных мероприятий.
Машиностроительные производства давно начали использовать резку металла лазером. Пионерами выступили судостроительные верфи, авиационные заводы и автомобильные гиганты, искавшие передовые методы работы для увеличения производительности труда. Возрастающая конкуренция стимулировала появление инновационных обрабатывающих центров с принципиально новыми системами влияния на рабочий процесс.
К настоящему времени на промышленных предприятиях лазерная резка металла представлена следующими видами установок:
- твердотельные — основанные на кристаллических драгоценных камнях или соединениях редкоземельных элементов, для накачки фотонов используется импульсные лампы или лазерные диоды;
- газовые — в качестве активаторов применяются смеси инертных газов с источником возбуждения в виде электрических разрядов или направленной химической реакции;
- волоконные — активная среда и резонатор сделаны целиком из оптического волокна или скомбинированы с другими конструктивными элементами.
Следующее видео представляет волоконный лазерный станок.
Для работы с цветными металлами и антикоррозионными сталями, имеющими высокую отражающую способность, прикладными исследовательскими институтами разработаны специальные модели традиционных лазеров с резонатором из оптико-волоконной трубки. Световой луч в таких установках более сфокусированный и концентрированный и не рассеивается о зеркальную поверхность алюминиевых, титановых или нержавеющих заготовок.
Широко распространенные газовые СО₂-лазеры работают на рабочей смеси углекислого газа, азота и гелия, зеркала резонатора покрыты серебряным или золотым напылением для увеличения отражающей способности.
Технология лазерной резки металлов постоянно совершенствуется: пробуются новые типы установок, усложняются системы управления процессом, применяются компьютерные комплексы для контроля режимов обработки. Основной упор делается на увеличение точности, чистоты реза и производительности.
Особенности технологического процесса
В результате воздействия светового луча материал заготовки проходит несколько промежуточных изменений для превращения в обработанную деталь:
- первая стадия — воздействие лазера на металл в точке начала реза вызывает нагревание вещества до температуры плавления и появлению усадочной раковины;
- вторая стадия — энергия излучения приводит к кипению и испарению металла;
- третья стадия — при проплавлении заготовки на полную глубину начинается поступательное движение рабочего органа в соответствии с заданной траекторией.
В действительности, процесс испарения металла наблюдается только у тонких заготовок, при средней и большой толщине реза удаление остатков вещества из рабочей зоны производится с помощью струи вспомогательного газа (азот, кислород, воздушная смесь или инертные газы).
Такие установки, работа которой представлена на видео, называют газолазерными резаками.
Активный кислород, подаваемый в зону резания не только выводит продукты плавления металла и охлаждает поверхность среза, но и способствует поддержанию температуры и ускоряет режимы обработки. При лазерной резке не происходит деформации заготовки, следовательно, отсутствуют затраты материала на припуск линейных размеров и необходимость в дополнительных чистовых операциях.

Сравнительные характеристики лазерной и плазменной резки приведены
Современные лазерные комплексы
Мировая станочная индустрия идет в ногу со временем и предлагает своим потребителям самое разнообразное оборудование для лазерной резки металла. Многокоординатные аппараты призваны заменить шумные и низко производительные механические резаки. Мощность лазера зависит от специфики производства и экономического обоснования выбранного агрегата.
Новое поколение прецизионных обрабатывающих станков с ЧПУ позволяют проводить обработку материалов с точностью до 0,005 мм. Площадь обработки некоторых моделей лазерных установок достигает нескольких квадратных метров. Большим достоинством является минимизация человеческого фактора, заключающаяся в высокой автоматизации производственного процесса.
Геометрия детали задается в программный блок, осуществляющий управление лазером и рабочим столом с заготовкой. Системы настройки фокуса автоматически выбирают оптимальное расстояние для эффективного резания. Специальные теплообменники регулируют температуру лазерной установки, выдавая оператору контрольные данные текущего состояния инструмента.
Лазерный станок оснащается клапанными механизмами для подключения газобаллонного оборудования, чтобы обеспечить подачу вспомогательных газов в рабочую зону. Система дымоулавливания призвана оптимизировать расходы на вытяжную вентиляцию, включая её непосредственно в момент обработки. Область обработки полностью экранируется защитным кожухом для безопасности обслуживающего персонала.
Лазерная резка листового металла на современном оборудовании превращается в легкий процесс задания числовых параметров и получения на выходе готовой детали. Производительность оборудования напрямую зависит от параметров станочного комплекса и квалификации оператора, создающего программный код. Технология лазерной резки металлов гармонично вписывается в концепцию роботизированного производства, призванного полностью освободить человека от тяжелого труда.
Производители предлагают различные типы лазерных станков: универсальные и специализированные. Стоимость первых на порядок больше, но они позволяют производить несколько операций и выпускать детали более сложной формы. Большое количество рыночных предложений дает возможность выбора для заинтересованных потребителей.
Преимущества и недостатки
Специалисты машиностроительных предприятий понимают перспективы использования данной технологии для получения точных деталей с хорошей шероховатостью. Область применения обширна: от простого раскроя листового металлопроката до получения сложных кузовных деталей автомобилей. Явные плюсы лазерной резки металлов сводятся к нескольким резюмирующим аспектам:
- высокое качество обработанной поверхности;
- экономия материала;
- способность работы с хрупкими материалами и тонкими заготовками;
- возможность получения деталей сложной конфигурации.
Среди минусов: высокая стоимость оборудования и расходных материалов.
Лазерная резка стали и цветных металлов пользуется большим рыночным спросом. Способность быстро выдавать чистовые детали нестандартной формы привлекает в профильные предприятия заказчиков малых партий разнообразных изделий. Лазерные технологии активно используются в декоративном творчестве при изготовлении дизайнерских украшений и оригинальных сувениров.
Решение о применении лазерной обработки должно приниматься с учетом расчета окупаемости оборудования и величине эксплуатационных расходов. В настоящее время такие установки могут себе позволить, в основном, крупные предприятия с большим производственным циклом. С развитием технологии будут снижаться стоимость станков и количество потребляемой энергии, поэтому в будущем лазерные аппараты вытеснят своих конкурентов из сферы резки любых материалов.
разновидности, оборудование для процесса, преимущества и недостатки
Среди большого количества технологий по обработке железа лазерная резка выделяется экономичностью и производительностью. Эта технология позволяет не только сверхточно производить изделия со сложным геометрическим контуром, но и обеспечивает высокую скорость изготовления этих изделий.
Описание технологии
При применении лазерной резки вальцуемый металл подвергается влиянию эффектов отражения и поглощения излучения от лазера. Изменение габаритов и формы элементов при лазерной обработке достигается благодаря воздействию двух результатов излучения: плавления и испарения. Описание процесса заключается в следующем:
- Лазерный луч оказывает воздействие на железо в определенной точке.
- Сначала элементы оплавляются до оптимальной температуры, потом начинается процесс плавки металла.
- В фазе плавления возникают углубления.
- Влияние энергии излучения лазера приводит ко 2 фазе процесса — кипит и испаряется металлическое вещество.
Однако, последний механизм требует высоких энергозатрат и осуществим лишь для достаточно тонкого металла. Поэтому на практике резку выполняют плавлением. При этом в целях существенного сокращения затрат энергии, повышения толщины обрабатываемого металла и скорости разрезания применяется вспомогательный газ, вдуваемый в зону реза для удаления продуктов разрушения металла. Обычно в качестве вспомогательного газа используется кислород, воздух, инертный газ или азот. Такая резка называется
Разновидности лазерных приборов
Лазер состоит из элементов:
- Особенного ключа энергии (системы накачки).
- Рабочего объекта, обладающего возможностью вынужденного излучения.
- Оптического резонатора (набор специализированных зеркал).
Принадлежность обработки к той или иной вариации определяется по методу применяемого лазера и его мощи. Сейчас имеется следующее классифицирование лазеров:
- Твердотельные (мощь не более 7 квт).
- Газовые (мощь до 22 квт).
- Газодинамические (мощь от 110 квт).
В производственных целях большей известностью пользуется обработка железа с твердотельным прибором. Светоизлучение может подаваться в импульсном или сплошном режиме. В качестве трудового тела применяется рубин, стекло с добавкой неодима или CaF2 (флюорит кальция). Главным достоинством твердотельных лазеров считается способность создания мощного импульса энергии за несколько секунд.
Газовые лазеры используются для обработки железа в технологических и научных целях. Активным катализатором выступает смесь газообразного азота, углекислого газа и гелия, элементы которых активизируются электрическим разрядом и дают лазерному лучу монохромность и направленность.
Огромной мощностью отличаются газодинамические устройства. Рабочее тело — углекислый газ. Сначала газ прогревается до самой высокой температуры, потом он пропускается через небольшой канал, где случается расширение и последующее охлаждение углекислого газа. В результате этой процедуры выделяется энергия, применяемая для лазерной обработки железа.
Газодинамические устройства можно применять для обработки железа с любой поверхностью. Благодаря небольшому расходу лучевой энергии, их можно разместить на расстояние от обрабатываемой части и при этом сберечь качество резки железа.
Оборудование
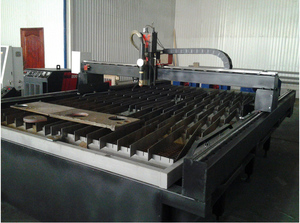
- Специализированного излучателя (твердотельный или газовый прибор). Должен обладать нужными энергетическими и оптическими показателями.
- Система формирования лучей и газа. Отвечает за подачу луча от цели излучения к детали, которая обрабатывается, и изменение показателей поступающего к точке рабочего газа.
- Устройство передвижения (координации) как самого железа, так и воздействующего на него лазерного луча. А также включает в себя электроисполнительный механизм, привод и мотор.
- АСУ (автоматизированная система управления). Регулирует лазерный луч и управляет координатным механизмом и системой транспортирования и формирования луча и газа. Снабжена разнообразными датчиками и подсистемами.
Современный прибор резки железа способен исполнять любые трудные задачи, даже художественную резку. Их изготовлением занимаются как российские фирмы («Технолазер»), так и иностранные предприятия (немецкая фирма «Trumpf»).
Лазерная резка тонкого железа
Промышленным изготовителям удобнее применять листы металла для нарезки, чем необработанные части большой толщины. При этом можно экономить электроэнергию и применять методы резки листового железа с большей мощностью.
Методы нарезки железа, лист которого подготовлен к обработке, — это кислородная нарезка (выжигание), резка группой газов (аргон, азот) и сжатым воздухом. Среди достоинств лазерной нарезки листового железа перед прочими видами обработки возможно выделить:
- Большую точность отдачи и нарезки лазерного луча.
- Возникает меньше пыли на плоскости детали.
- Маленькая вероятность нанесения повреждений листу железа.
- Понижение энергетических затрат.
- Формирование объемных простых конструкций с высокий скоростью и наименьшей площадью отделываемого материала.
Благодаря своим плюсам и применению точного передового оборудования, резка железа используется для создания:
- Частей машиностроительной техники.
- Декоративных подставок, полок, стеллажей и оснащения для торговой промышленности.
- Составляющих котлов, емкостей, дымоходов и печей.
- Звеньев дверей и ворот, кованных ограждений.
- Личного дизайна шкафов и корпусов.
- Своеобразных вывесок, букв и трафаретов.
Использование резки имеет массу преимуществ перед иными видами отделки металла. Потому все больше предприятий употребляют в своем производстве именно лазерную обработку железа.
Инновационные лазерные комплексы
Всемирная станочная индустрия идет в ногу со временем и дает своим потребителям всевозможное электрооборудование для резки железа. Многокоординатные аппараты призваны сменять громкие и низко плодотворные механические резаки. Энергия лазера зависит от специфичности производства и финансового обоснования избранного агрегата. Новейшее поколение прецессионных разделывающих станков с ЧПУ разрешают проводить отделку материалов с верностью до 0,005 мм. Метраж обработки отдельных моделей лазерных установок достигает многих квадратных метров.
Огромным достоинством считается минимизирование человеческого фактора, содержащаяся в высокой автоматизации промышленного процесса. Геометрия компонентов задается в макропрограммный блок, исполняющий управление лазером и трудовым столом с болванкой. Системы настройки фокуса машинально выбирают приемлемое расстояние для действенного резания.
Специфические теплообменники регулируют температуру лазерного агрегата, выдавая оператору контрольные сведения настоящего состояния инструмента. Лазерный механизм оснащается клапанными приспособлениями для подключения газобаллонного снабжения, чтобы снабдить подачу запасных газов в рабочую часть. Система дымоулавливания призвана улучшить расходы на вытяжную вытяжку, включая её прямо в момент обработки. Зона обработки полностью экранируется предохранительным кожухом для защищенности обслуживающего персонала.
Резка листового железа на современном оборудовании преобразуется в легкий процесс задания числовых характеристик и получения на выходе готового компонента. Продуктивность оборудования впрямую зависит от характеристик станочного комплекса и квалификации оператора, формирующего программный код. Методика резки железа пропорционально вписывается в концепцию роботизированного изготовления, призванного полностью избавить человека от тяжелого труда.
Изготовители предлагают разные типы лазерных станков:
- Многоцелевые.
- Специальные.
Стоимость первых больше, но они дают возможность производить некоторое количество операций и выпускать детали более трудной формы. Немалое количество рыночных услуг дает возможность выбора для заинтересованных покупателей.
Профессионалы машиностроительных предприятий понимают возможности использования предоставленной технологии для изготовления точных деталей с превосходной шероховатостью. Область использования обширна: от обычного раскроя листового металлопроката до приобретения сложных кузовных деталей автомашин.
Видимые плюсы нарезки железа сводятся к нескольким аспектам:
- Высокое качество отделанной поверхности.
- Бережливость материала.
- Умение работы с непрочными материалами и мелкими заготовками.
- Вероятность получения компонентов сложной конфигурации.
Среди минусов:
- Высокая цена оснащения.
- И расходных материалов.
Нарезка железа и цветных металлов пользуется огромным рыночным спросом. Лазерные технологии интенсивно применяются в декоративном творчестве при создании дизайнерских украшений и уникальных сувениров.
Решение об использовании обработки должно приниматься с учетом расчета окупаемости оснащения и величине рабочих расходов. В настоящее время подобные установки могут себе разрешить в основном большие предприятия с немаленьким производственным циклом. С раскручиванием технологии будут уменьшаться стоимость станков и величина употребляемой энергии, поэтому в будущем лазерные агрегаты вытеснят своих конкурентов.
Преимущества и недостатки технологии
Нарезка железных изделий имеет множество значимых преимуществ по сравнению с иными способами резки. Из многочисленных достоинств настоящей технологии стоит в обязательном порядке отметить следующие:
- Интервал толщины изделий, которые можно успешно подвергать гравировке, довольно широкий: сталь — от 0,2 до 22 мм, медь и латунь — от 0,3 до 16 мм, сплавы на базе алюминия — от 0,3 до 22 мм, нержавеющая сталь — до 55 мм.
- При применении лазерных аппаратов исключается надобность механического контакта с обрабатываемой составной частью. Это позволяет производить, таким образом, резки просто деформирующиеся и хрупкие детали, не волнуясь за то, что они будут испорчены.
- Получить с помощью нарезки продукт требуемой конфигурации просто для этого довольно загрузить в блок регулирования лазерного агрегата чертеж, сделанный в специальной программе. Все остальное с наименьшей степенью погрешности (достоверность до 0,2 мм) осуществит оборудование, оснащенное компьютерной системой управления.
- Агрегаты для выполнения нарезки могут с большой скоростью обрабатывать нетолстые листы из стали, а также фабрикаты из твердых сплавов.
Лазерная обработка способна полностью заменить дорогостоящие научно-технические операции литья и штамповки, что уместно в тех случаях, когда нужно изготовить маленькие партии продукции. Можно существенно снизить первоначальную стоимость продукции, что достигается за счет более высокой скорости и выработки процесса обработки, снижения объема остатков, отсутствия потребности в последующей механической обработке.
Наряду с высокой мощностью, приборы для лазерной обработки имеют необыкновенную универсальность, что дает возможность вычислять с их помощью задачи любого уровня сложности. В то же время для лазерной обработки характерны и определенные недостатки.
Из-за высокой силы и значительного энергопотребления оснащения для лазерной резки, первоначальная стоимость изделий, изготовленных с его использованием, выше, чем при их производстве способом штамповки. Однако это можно причислить только к тем ситуациям, когда в себестоимость штампованного элемента не включена цена производства технологической оснастки.
принципы работы, виды и особенности
Лазерную резку используют для раскроя листовых материалов, чаще всего – металлов. Одно из ее главных отличий – возможность изготовления деталей со сложным контуром.
Принципы работы лазерной резки
Использование этого метода основано на тепловом воздействии лазерного излучения на материалы. При этом разрезаемый металл нагревается сначала до температуры плавления, а потом до температуры кипения, при которой он начинает испаряться. Лазерная резка испарением требует высоких энергозатрат, поэтому ее используют для работы с тонкими металлами.
Относительно толстые листы разрезают при температуре плавления. Чтобы облегчить этот процесс, в зону резки подается газ: азот, гелий, аргон, кислород или воздух. Его задача – удалять из зоны резки расплавленный металл и продукты его сгорания, поддерживать горение металла и охлаждать прилегающие зоны. Наиболее эффективен для этого кислород. Он заметно увеличивает скорость и глубину резки.
Подробнее о процессе лазерной резки можно узнать из видео ниже:
Параметры резки разных металлов
Скорость резки зависит не только от мощности лазера и толщины металла, но и от его теплопроводности. Чем она выше, тем интенсивнее отводится тепло из зоны резки и тем более энергозатратным будет весь процесс. Так, если лазером мощностью 600 Вт можно легко разреза́ть черные металлы или титан, то алюминий или медь, обладающие высокой теплопроводностью, обрабатывать значительно сложнее. Средние параметры для работы с разными металлами выглядят следующим образом:
Малоуглеродистая сталь | Инструментальная сталь | Нержавеющая сталь | Титан | |||||||
Толщина, мм | 1,0 | 1,2 | 2,2 | 3,0 | 1,0 | 1,3 | 2,5 | 3,2 | 0,6 | 1,0 |
Мощность лазера, Вт | 100 | 400 | 850 | 400 | 100 | 400 | 400 | 400 | 250 | 600 |
Скорость резания, м/мин | 1,6 | 4,6 | 1,8 | 1,7 | 0,94 | 4,6 | 1,27 | 1,15 | 0,2 | 1,5 |
Виды лазерной резки
Лазерные установки состоят из трех основных частей:
- Рабочей (активной) среды. Она является источником лазерного излучения.
- Источника энергии (системы накачки). Он создает условия, при которых начинается электромагнитное излучение.
- Оптического резонатора. Система зеркал, усиливающих лазерное излучение.
По типу рабочей среды лазеры для резки делят на три вида:
- Твердотельные. Их основным узлом является осветительная камера. В ней находятся источник энергии и твердое рабочее тело. Источником энергии служит мощная газоразрядная лампа-вспышка. В качестве рабочего тела используют стержень из неодимового стекла, рубина или алюмо-иттриевого граната, легированного неодимом или иттербием. По торцам стержня устанавливают два зеркала: отражающее и полупрозрачное. Лазерный луч, излучаемый рабочим телом, многократно отражается внутри него, усиливается в ходе отражений и выходит через полупрозрачное зеркало.
К твердотельному виду относятся и волоконные лазеры. В них излучение усиливается в стекловолокне, а источником энергии служит полупроводниковый лазер.
Так устроен твердотельный лазер
Для понимания механизма работы лазера можно рассмотреть установку с рабочим телом в виде стержня из граната, легированным неодимом. Ионы последнего и служат активными центрами. Поглощая излучение газоразрядной лампы, ионы переходят в возбужденное состояние, то есть у них появляется излишек энергии.
Ионы возвращаются в исходное состояние и отдают энергию в виде фотона – электромагнитного излучения или по-другому света. Фотон вызывает переход в обычное состояние других возбужденных ионов. В итоге процесс нарастает лавинообразно. Зеркала способствуют движению луча в определенном направлении. Многократно возвращая фотоны в рабочее тело при отражении, они способствуют образованию новых фотонов и усилению излучения. Его основные характеристики – малая расходимость луча и высокая концентрация энергии.
- Газовые. В них рабочим телом является углекислый газ или его смесь с азотом и гелием. Газ прокачивается насосом через газоразрядную трубку. Он возбуждается с помощью электрических разрядов. Для усиления излучения устанавливают отражающее и полупрозрачное зеркало. В зависимости от особенностей конструкции такие лазеры бывают с продольной и поперечной прокачкой, а также щелевые.
Так устроен газовый лазер с продольной прокачкой
- Газодинамические. Эти лазеры самые мощные. В них рабочим телом является углекислый газ, нагретый до 1 000–3 000 °К (726–2726 °С). Он возбуждается с помощью вспомогательного маломощного лазера. Газ со сверхзвуковой скоростью прокачивается через суженный посередине канал (сопло Лаваля), резко расширяется и охлаждается. В результате его атомы переходят из возбужденного в обычное состояние и газ становится источником излучения.
Схема работы газодинамического лазера
Преимущества и недостатки лазерной резки
Можно выделить следующие преимущества лазерной резки металлов:
- Нет механического контакта с поверхностью разрезаемого металла. Это делает возможным работу с легкодеформируемыми или хрупкими материалами.
- Можно разрезать металлы разной толщины. Сталь в пределах 0,2–30 мм, алюминиевые сплавы – 0,2–20 мм, медь и латунь – 0,2–15 мм.
- Высокая скорость резки.
- Возможность изготовления изделий с любой конфигурацией.
- Чистые кромки разрезаемого металла и низкое количество отходов.
- Высокая точность работы – до 0,1 мм.
- Экономный расход листового металла за счет более плотной раскладки деталей на листе.
Недостатками лазерной резки считаются высокое энергопотребление, дорогое оборудование.
Назначение и критерии выбора лазерной резки
Лазерную резку используют для обработки не только металлов, но и резины, линолеума, фанеры, полипропилена, искусственного камня и даже стекла. Она востребована при изготовлении деталей для различных приборов, электротехнических устройств, сельскохозяйственных машин, судов и автомобилей. Такой способ раскроя материала используют для получения жетонов, трафаретов, указателей, табличек, декоративных элементов интерьера и многого другого.
Основной критерий выбора вида лазерной резки – тип обрабатываемого материала. Так, углекислотные лазеры подходят для резки, гравировки, сварки разных материалов – металла, резины, пластика, стекла.
Твердотельные волоконные установки оптимальны при раскрое латунных, медных, серебряных или алюминиевых листов, но не подходят для неметаллов.
Лазерная резка: технологии, преимущества, виды оборудования
Изначально человек разделял металлические детали ручными инструментами. Это был медленный процесс, который требовал большого количества времени, сил. Рез часто получался неровным, детали браковались. С развитием технологического прогресса появились новые способы разделения металлических заготовок. Лазерная резка — современный метод обработки деталей из металла.


Лазерная резка
Технология
Технология лазерной резки металла подразумевает под собой процесс нагревания металла в определённом месте свыше его температуры плавления. Рабочий привод генерирует сфокусированный луч, которые проходит через систему линз, становится мощнее. Раскалённый пучок света попадает на поверхность детали, начинает расплавлять её. Передвигаясь по направляющим, рабочая головка делает рез заданного размера, формы.
Простые аппараты для разрезания металла не позволяют разделять детали большой толщины. Чтобы работать с листами большой толщины, необходимо выбирать установку, оборудованную подачей инертного газа. Он выдувает расплавленный металл наружу, чтобы не мешать процессу плавки.
Сфокусированный луч обладает некоторыми характеристиками:
- Постоянством длины. Благодаря этому его легко сфокусировать на любой поверхности используя оптические линзы.
- Низкий угол расходимости света луча. Это позволяет получить мощный направленный поток света на заданную точку.
- Суммарная мощность излучения увеличивается благодаря когерентности.
При разрезании металла, материал может плавиться или испаряться. Это зависит от мощности оборудования.
Режимы
Резка лазером металлических заготовок зависит от следующих факторов:
- диаметра луча;
- мощности привода;
- обработки материалов защитными составами;
- количества линз, их расположения;
- вида металла или сплава, который подвержен обработке;
- толщины заготовки;
- предварительной очистки металла от ржавчины, грязи.
Также на скорость разделения деталей влияет используемый инертный газ. Например, если заменять кислород обычным воздухом, производительность аппарата снизится вдвое.
От выбранного режима создания реза зависит его качество. Главные факторы, которые влияют на состояние готового реза — скорость движения рабочей головки, толщина детали. Раскрой по металлу желательно совершать не спеша, чтобы не испортить рез.
Виды лазерной резки
Лазерная резка листового металла выполняются с помощью специальных аппаратов разных видов. Оборудование состоит из следующих элементов:
- Источника питания, который передаёт напряжение на рабочий привод.
- Генератора, который создаёт направленный поток.
- Ряда фокусирующих линз, которые усиливают, концентрируют излучение в одной точке.
Все элементы устанавливаются на рабочем столе с направляющими, шаговыми двигателями.
В зависимости от мощности выделяют три группы аппаратов:
- Твердотельные — до 6 кВт. Установки, на которых закрепляется рубин или другой кристалл для создания направленного потока энергии. Работают импульсами или постоянным излучением.
- Газовые — мощность от 6 до 20 кВт. Оборудование, для работы которого используют газовую смесь. Она нагревается под воздействием электрического тока.
- Газодинамические — от 20 до 100 кВт. Аппарат, работающий на основе углекислого газа. Отличаются высокой мощностью, небольшим расходом энергии.
Выбор зависит от целей мастера. Чем толще листы нужно разрезать, тем мощнее оборудование нужно выбирать.


Лазерная резка листового металла
Преимущества и недостатки лазерной резки
У обработки материалов лазером есть ряд сильных и слабых сторон.
Преимущества:
- Зависимо от мощности выбранного оборудования, можно разделять листы большой толщины.
- Резка металла лазером выполняется без соприкосновения рабочей части с поверхностью изделия. Это исключает механические повреждения материала.
- Высокая скорость проведения технологического процесса.
- Если установка для лазерной резки комплектуется ЧПУ, можно добиться высоких показателей точности, производительности.
- Выделение минимального количества отходов.
- Возможность создавать резы разных размеров, формы.
Недостатки:
- Установка расходует много электроэнергии.
- Простые модели не могут разделять листы шириной свыше 20 мм.
Виды оборудования для лазерной резки
Резка металла лазером проводится с помощью специальных установок, которые бывают трех типов:
- Твердотельные аппараты. Устройства для лазерной резки малой мощности. Состоят из рубинового стержня, лампы накачки. Модели могут работать импульсами или в постоянном режиме.
- Газовое оборудование. Газ нагревается до высоких температур под воздействием электрического тока. Раскалённые частицы испускают свет, который фокусируется линзами на рабочую поверхность.
- Газодинамические установки. Газ нагревается до критических температур — свыше 3-х тысяч градусов. Далее раскалённый газ пропускается на высокой скорости через сопло, проходит процесс охлаждения. Высокая мощность таких аппаратов делает их нерентабельными при редком использовании.


Оборудование для лазерной резки
Как сделать лазерный резак в гараже
Лазерная резка стали проводится на покупных и самодельных устройствах. Если нет возможности купить станок, можно изготовить его самостоятельно. Для этого нужно подготовить материалы, инструменты:
- мощный фонарик на батарейках;
- лазерную указку;
- привод из DVD-ROM;
- паяльник, отвертки.
Пошаговая инструкция сборки:
- Изначально необходимо разобрать дисковод, чтобы вытащить рабочую головку. Делать это нужно аккуратно, чтобы не повредить линзу.
- Вытащить диод из указки. На его место припаять рабочую часть из дисковода.
- Внутренности указки нужно вытащить, чтобы собрать для них новый корпус. Закрепить все элементы в корпус фонарика. Убрать защитное стекло, запитать устройство батарейками.
Дополнительно можно укрепить корпус скотчем, клеем.
Усиление самодельной установки
Мастера экспериментируют с набором линз, чтобы усилить мощность луча. Дополнительно можно запитать его от подзарядки для аккумуляторных батареек. Чтобы удобнее было проводить технологические процессы, собирается конструкция, удерживающая самодельную установку. Она устанавливается над рабочим столом на направляющих.
Лазерная резка представляет собой современный технологический процесс, который позволяет разделять металлические листы разной толщины. Зависимо от размеров обрабатываемых заготовок нужно выбирать мощность привода.
Что такое лазерная резка: технология резки, достоинства, недостатки
Содержание:
Технология лазерной резки
Технология лазерной резки позволяет резать материалы из пластика или металла с максимально высокой точностью. Это особенно важно именно в случае с металлом, ведь для того, чтобы его можно было использовать во время работ, материала должен сохранить все свои изначальные параметры. В противном случае использовать его будет невозможно.
Важно отметить, что лазерная резка — это относительной новый способ обработки металла, отличающийся предельно высокой производительностью. Именно поэтому процесс изготовления самых разных конструкций из металла и пластика существенно облегчается. В случае мелкосерийного производства лазерная резка позволяет сделать производство куда более простым и быстрым. Это отражается и на конечной цене того либо иного продукта. Стоит ли говорить о том, что лазерная резка — это коммерчески оправданный метод, который позволяет сэкономить время и деньги.
Сферы применения и преимущества (плюсы)
Если бы не многочисленные преимущества этого метода, он вряд ли стал бы таким популярным. Каковы же главные достоинства этого метода?
- Сфокусированное излучение лазером способно обеспечить высочайший уровень концентрации энергии, что позволяет добиться разделения любого вида пластика или металла вне зависимости от свойств теплофизического характера. Также стоит отметить и то, что таким образом можно получить максимально узкие разрезы, имеющие минимальную зону термического влияния.
- Ещё одно крайне важно достоинство материала касается возможности обработки самых разных материалов. Более того, лазерная резка не может оказывать какое-либо механическое воздействие на металл. Это особенно важно, если речь идёт о создание нестандартной конструкции, которая будет использоваться во время возведения какого-либо сооружения. Более того, все мелкие деформации, которые могут возникнуть непосредственно во время резки, незначительны. Как раз поэтому лазерная резка — это метод, для которого характерная высочайшая точность.
- Данный способ можно применять как в случае с недостаточно жёсткими, так и легкодеформируемыми конструкциями, деталями или заготовками. Так как для лазерного излучения характерна большая мощность, с помощью этого способа можно достичь завидной производительности труда, которая будет сочетаться с непревзойдённым качественным уровнем поверхности реза.
- Ещё одно достоинства имеет большое значение для тех, кто занимается лазерной резкой самостоятельно. Как известно, некоторые методы подходят только профессионалам, которые обладают определённым знаниями, а также богатым опытом. В случае с лазерной резкой всё обстоит совершенно иначе. В частности, управлять лучом лазер очень легко и просто. С этой задачей справится даже неподготовленный человек, который впервые видит перед собой лазер. Поэтому лазерным лучом можно работать с контурами самых сложных форм. Более того, таким образом можно вырезать объёмы детали, а также заготовки с высочайшим степенью автоматизации процесса.
- Если сравнить лазерную резку с любыми другими методами работы с пластиком или металлом, то окажется, что ему просто нет равных. Традиционные способы обработки металла не обладают и малой частью тех преимуществ, которые характерны для лазерной резки. Стоит ли говорить о том, что традиционные методы обработки не могут похвастаться тем же уровнем коммерческой выгод, что метод резки лазером.
- Нельзя не упомянуть и про важное значение лазера в современном производственном секторе экономики, для которого характерно понижение уровня серийности производства. Также в последнее время требования к выпускаемым изделиям меняются всё чаще и чаще. Из-за этого возникла потребности ориентироваться на различные гибки автоматизированные решения, поэтому многие специалисты вынуждены констатировать тот факт, что лазерная резка стала просто незаменимой. Она обладает поразительным удобством и гибкостью.
- Если же речь идёт о художественной или фигурной резке, то без лазера и вовсе обойтись не получится. Любые другие методы не позволят достичь требуемой точности.
Среди менее значимых преимуществ стоит отметить следующие:
- Полное отсутствие каких бы то ни было механических воздействий на обрабатываемый материал, что даёт возможность обрабатывать даже самые хрупки или деформируемые предметы.
- С помощью лазера можно обрабатывать самые разные виды металла, а также пластика. Речь идёт даже о цветных металлах.
- Во время выпуска малой партии какой бы то ни было продукции эффективнее провести именно лазерный раскрой, чем пытаться изготовить дорогостоящие формы, предназначенные для литья. Таким образом можно сэкономить весьма большую сумму денег.
- Также во время использования подобного метода можно достичь уникальной точности. Речь идёт о 0.001 мм на 1 лист, чья толщина достигает 2 мм.
- Для проведения автоматического раскроя материал нужно подготовить чертёж выбранного изделия, для чего достаточно простейшей инженерной программы. После этого нужно перенести чертёж на компьютер, предназначенный для установки. Всё это существенно проще, нежели использование других способов обработки.
- Стоит упомянуть ещё и то, что подобным образом можно существенно сократить долю человеческого фактора именно за счёт автоматизации производства. Это самым лучшим образом скажется на ходе производства и даже качестве выпускаемой продукции. К тому же, это приведёт к сокращению издержек на рабочую силу.
Что можно изготовить при помощи лазерной резки
- элементы для машиностроительных производств;
- элементы для стеллажей, подставок, полок всех назначений, торгового оборудования;
- элементы для корпусов и шкафов различного назначения;
- шаблоны, буквы, трафареты, вывески;
- детали для декоративных кованных изделий;
- части современного интерьера и многое другое.
Обрабатываемые материалы (максимальный размер заготовки 3000 х 1500 мм)
- черная сталь, чья толщина может достигать 20 мм;
- нержавеющая сталь с толщиной до 12 мм;
- алюминий толщиной до 10 мм.
Особенности лазерной резки металла
Эксперты в области обработки метала считают, что во время резки металла необходимо использовать инновационные технологии, так это позволит сократить издержки и достичь куда лучшее результата, нежели при использовании традиционных методов и технологий.
Чего можно достичь благодаря лазерной резки
Данный способ позволяет резать пластик и металл с исключительно высокой скоростью, достичь которую другими методами просто невозможно. Это может быть очень важно, если речь идёт о компании, которая занимается резкой в больших объёмах. С помощью лазерной резки она сможет удовлетворить запросы куда большего количества клиентов, что самым положительным образом скажется на её уровне заработка.
Также благодаря этому методу можно вести работы даже с твердосплавными материалами.
Нельзя забывать и про то, что данный способ отлично подходит для работы в импульсном режиме.
Ещё один результат, который представляет интерес для компаний, работающих в сфере производства, касается минимизации теплового воздействия на материал.
Характеристики лазерного луча, которые важны во время обработки пластика и металла
Лазерный луч отличается такими свойствами, как монохроматичность, а также когерентность и направленность. Именно высочайший уровень когерентности может дать нужный резонанс, способный значительно повысить силу излучения. Направленность же, в свою очередь, позволит сосредоточить луч на выбранном участке поверхности даже в том случае, если площадь участка ничтожно мала.
Монохроматичность позволяет сфокусировать оптическую линзу с куда меньшими усилиями оператора.
Недостатки лазерной резки
Недостатков у лазерной резки сравнительно немного. В частности, этот метод ни в коем случае нельзя назвать универсальным, ведь для каждого типа обрабатываемого материала существует сразу несколько параметров: по мощности лазера, использовании дополнительного газа, соблюдения высоких мер безопасности и других особенностей ведения работ.
Также не получится провести раскрой с некоторыми видами материалов. Среди них есть и достаточно популярные материалы, используемые повсеместно: поликарбонат, гетинакс, сотовый поликарбонат и полипропилен, текстолит и другими.
Итог
Лазерная резка — это лучший выбор, если речь идёт о работе с металлами или пластиком. Эти материалы отлично подходят для ведения работ, ведь достоинства лазерной резки позволят сэкономить силы, время и деньги.
Лазерная резка металла – технология обработки лазером
Лазерная резка – инновационная технология обработки металлических заготовок, которая применяется в производственных масштабах компаний, а также умещается в небольших частных мастерских. Благодаря уникальной установке, продуцирующей лазер, на определенном участке материала создает фигурные формы деталей.
Способ лазерной обработки подходит для каждого металлического материала, но индивидуальные особенности конкретного сырья все-таки имеются.
В чем заключается изюминка технологии?
Исходя из названия метода обработки, основное действие выполняется специальным лазером. Дорогостоящее оборудование фокусирует луч на маленькой площади, в результате чего образуется неимоверное количество энергии.

Лазерная резка металла
Под воздействием высокоплотного излучения происходит разрушение любого металла – он плавится, сгорает, иногда моментально испаряться.
Рассматривая характеристики лазерного воздействия, выделяют следующие аспекты процесса:
- отличительной чертой луча в сравнении с обычными световыми волнами является постоянная длина и частота продуцируемой волны. Это свойство обеспечивает отличную фокусировку с помощью системы линз на любой имеющейся поверхности;
- направленность луча всегда поддерживается в высокой концентрации, усиливает эффективность маленький угол рассеивания энергии;
- когерентность – способность сосредоточить в одной области множество однотипных процессов, ведущих к преобразованию материала. Суммарная мощность установки увеличивается за счет полного резонанса, всех происходящих внутри лазера процессов.
Подобные особенности обуславливают энергетическое постоянство, благодаря чему лазерная резка металла считается уникальным высокоэффективным методом получения необходимых деталей.
Тонкости технологического процесса
Современная лазерная установка – идеал оборудования, одновременно воплощающий скорость, невероятную точность обработки и простоту управления сложной машиной.

Многоцелевое устройство для лазерной резки
Благодаря внедрению компьютерного оснащения стало возможным устранить фактор человеческой ошибки, избегать излишков, обеспечить качество каждой выпущенной детали.
Работающая автоматизированная машина поддерживает постоянство сфокусированных лучей, совмещая линзами всю энергию в одном мощном потоке – лазере. При соприкосновении с поверхностью происходит нагревание исключительно намеченной линии разреза, при этом остальная часть заготовки остается незадействованной в процессе. Отсутствует лишняя деформация, чрезмерного нагревания всей детали с дальнейшим повреждением особо уязвимых областей не происходит.
Технология лазерной резки металла позволяет работать с мягкими сплавами и тонкими листами заготовок. Способы выполнения обработки подразделяются на два типа:
- лазерную резку плавлением детали;
- выполнение обработки путем испарения.
Плавление наиболее распространенный и дешевый способ достижения результата. Воздействие фокусированных лазерных волн на металл приводит к его нагреванию. Высокая температура на определенном участке становится причиной расплавления детали, а при равномерном смещении луча получают желаемую форму.
Если воздействие луча чрезмерное и энергия достигает второго физического рубежа – молекулы материала начинают закипать. При кипении наблюдается мгновенное испарение частичек детали.
На заметку: процесс испарения считается наиболее эффективным и точным методом обработки. Но для поддержания запредельного уровня энергии требуется множество ресурсов и производственных мощностей. Резку металла лазером по методу испарения считают дорогостоящим этапом производства, он существенно увеличивает себестоимость конечного результата.
Новый лазер – преимущества внедрения технологии
Создание некоторых важных элементов производственных машин и любого профессионального оборудования требует максимальной точности обработки металлических заготовок.
Достигнуть требуемого высокого результата позволяет лазерная резка металла, обладающая весомыми преимуществами в сравнении с известными альтернативными методами обработки:
- автоматизированный программный контроль качества и заложенный алгоритм работы позволяют увеличить точность резки, это является предпосылкой создания сложных элементов;
- скорость процесса существенно превосходит остальные способы;
- лазерное воздействие ограничивает чрезмерный перегрев заготовки, мягко разрезает материал;
- производительность любой лазерной установки обеспечивает заблаговременное выполнение крупных срочных заказов;
- температурному нагреву подвержена исключительно область разреза;
- допускается выполнение контурной резки любой сложности;
- объемы излишков регламентирует компьютер. Программа рассчитывает наиболее рациональное расположение всех необходимых форм;
- отверстия характеризуются минимальным диаметром, равным 0,5 мм.
Лазерную обработку металлов приравнивают к передовым производственным технологиям, что заставляет многих заказчиков уходить от старых производителей деталей к современным методикам.
Если компания внедряет этот метод обработки, то существенно возрастает качество выпускаемой продукции, появляется возможность выполнения индивидуальных заказов.
Резка алюминия – основные нюансы и характеристики процесса
Обработка алюминиевых заготовок происходит по определенному автоматизированному шаблону. В программу загружаются чертежи будущей детали, этот процесс позволяет избежать дорогостоящего привлечения узких специалистов. Дополнительная экономия заключается в рациональном расположении формы детали на имеющейся заготовке, снижается процентное количество излишков.
Распространенным производственным действием считается лазерная резка стали, а также работа с деревянными материалами.

Лазерная резка по дереву
В процессе обработки алюминиевых листов совместно с основным лазерным лучом в сфокусированную зону подается поток воздуха, он увеличивает общую энергию луча, а также служит своеобразным мусоропроводом для образующихся шлаков и продуктов плавления.
Мягкий алюминий характеризуется высокой теплопроводностью, это позволяет ему отлично поглощать энергию лазера. Эта особенность является камнем преткновения многих рядовых производственных цехов, поскольку лишь профессиональный высокомощный лазер способен справиться с этим материалом.

Станок с мощным лазером для резки алюминия
Основными нюансами в работе с алюминиевыми заготовками являются:
- небольшие производственные скорости – высокоскоростные установки не контролируют образование на поверхности заготовки деформаций;
- в процессе работы отсутствует прямой контакт с материалом, лазер просто прожигает поверхность алюминия;
- продувная зона обеспечивает полную очистку контура, эта функция весьма актуальна при дальнейшем сваривании;
- автоматизированная установка при правильно заложенном чертеже справляется с неимоверно сложным проектом детали.
- алюминий не приемлет исправлений – человеческий фактор полностью исключается за счет системы ЧПУ.
При обработке мягких металлов часто появлялся фактор статического влияния крепежных элементов, особенно устаревших производственных машин, но лазерная резка нержавеющей стали не требует закрепления заготовок. Достаточно просто положить заготовку в рабочую зону, а машина выполнит все необходимые операции в точности с заявленным электронным чертежом.
Лазерный станок с ЧПУ
Выполнение резки других материалов
Сложное выполнение художественной резки, раскройка рядовых материалов при работе с автоматизированной лазерной машиной ЧПУ становятся довольно обычной заводской работой. Кроме алюминиевых листов, подобные установки легко справляются с несколькими видами металла:
- нержавеющими материалами;
- листами из других материалов;
- стальными заготовками;
- латунью.
Работа с нержавейкой приравнивается к сложным энергозависимым проектам, поскольку материал отличается высокой сопротивляемостью к любому типу энергетического и физического воздействия. Мощный лазер и компьютеризированная начинка установки позволяют получить сложные фигуры и уникальные детали, прочность которых будет на высоком уровне.
Обработка нержавеющей стали
Лазерная резка нержавейки получила особую популярность. Особенностями процесса обработки нержавейки выступают:
- вся раскройки материала производится бесконтактным способом, что исключает даже минимальную деформацию деталей в местах воздействия машины;
- даже при работе с этим сложных материалов отсутствует фактор погрешности;
- лазерная резка материала исключает шансы образования отслоения краев, заусениц, а кромка края не деформируется;
- общие временные затраты существенно ниже, что обуславливает небольшое снижение стоимости подобных услуг;
- показатель мощности лазера не имеет ограничений по толщине заготовок из нержавейки. Любой лист материала будет равномерно разрезан с учетом заложенного чертежа.
Достоинством процесса лазерной обработки нержавеющих материалов считается отсутствие какого-либо влияния на качественные свойства детали, это не снижает длительность эксплуатационного периода.
Этот материал обладает уникальной защитой от коррозии, а прошлые технологические процессы всегда способствовали снижению способности противостоять окислению. Лазер не способен снижать физические свойства.
Медь и латунь – обработка материала лазером
Для обеспечения раскройки медных листов требуется правильно выставить параметры установки ЧПУ, что во многом предопределяет качество конечных форм. Выполнять резку необходимо на низких скоростях и при максимальной мощности луча. Только такое соотношение условий позволит создать идеальный требуемый продукт. Пренебрежение технологичными нюансами приводит к деформированию кромок и нарушению структурной целостности.
Латунь, как материал, не требует определенной скрупулезной настройки программы резки, допускается проведение раскройки при стандартных параметрах оборудования. Но именно лазерная методика обработки гарантирует отсутствие любых структурных повреждений. Нарушения физических свойств, перегрева детали в процессе работы не происходит. Лазерная резка металла – современный способ ювелирной обработки материалов.