Технология изготовления пружин

Как известно, существуют различные виды пружин, которые отличаются не только по конструкции, но еще и по способу взаимодействия с остальными механизмами в узлах. Так, например, пружины сжатия работают на сжатие, пружины растяжения — на растяжение, ну а пружины кручения, соответственно, на изгиб и скручивание. При этом данные виды пружин имеют витую форму, в отличии от той же тарельчатой пружины или от любого типа пружин-рессор. Само собой, технология изготовления пружин витого типа будет отличаться от того как происходит производство пружин с другой конструкцией.
В целом, технология изготовления пружин подразумевает под собой совокупность последовательного использования специальных технологических инструментов, например, станочного оборудования и каких-либо сырьевых материалов. При этом, само
Пожалуй, наиболее распространенными в промышленности и быту считаются как раз таки витые виды пружин, а именно, кручения, сжатия, растяжения. По этой причине нами сегодня будет рассмотрено, что представляет технология изготовления пружин из данной классификации. Вообще, наличие специальной навивки в конструкции позволяет подобным пружинам многократно воспринимать повторяющиеся нагрузки, проявляя высокую степень устойчивости к разным механическим воздействиям без потери своих характеристик, в числе которых имеются следующие физико-химические свойства:
- Коэффициент упругости
- Предел воспринимаемой нагрузки
- Усталостная прочность
Именно эти параметры влияют на продолжительность, а главное, на качество работы пружин. Собственно, для того, чтобы обеспечить данным изделиям максимально возможную долгосрочность эксплуатации, производство пружин должно осуществляться из надежного сырьевого материала, посредством поэтапного применения разных технически процессов на специальном оборудовании. Как правило, навивка осуществляется оператором из стальной проволоки на токарных станках либо вручную, либо через автомат одним из двух основных способов: горячим методом или же холодным методом.
Холодная технология изготовления пружин
Производство пружин холодным способом в Российской Федерации выполняют чуть чаще, нежели горячим, ввиду наиболее низкой себестоимости производства. Для таких работ не требуются дополнительные дорогостоящие станки, кроме навивочного. Собственно, такой метод предполагает использование оборудования, оснащенного двумя основными валиками, через которые и происходит навивка. Верхний из валиков позволяет регулировать натяжение, а также задавать направление завивки, используя для этого специально установленный винт. Сам процесс изготовления выполняется примерно так:
- Подготавливается специальная сталь для изготовления пружин (стальная проволока).
- Проволока просовывается через планку в суппорте.
- Ее конец прочно закрепляется на оправке при помощи зажима.
- Через верхний валик устанавливается необходимое натяжение.
- В зависимости от диаметра проволоки выбирается скорость вращения.
- Запускается в работу валик, наматывающий пружину.
- По мере достижения необходимого числа витков, проволока обрезается.
- В завершении деталь обрабатывается механически и термически.
Несмотря на то, что форма изготавливаемого изделия может быть как бочкообразной, так и цилиндрической, или даже конической, холодная технология изготовления пружин не позволяет использовать для изготовления пружин сталь диаметром более 16 миллиметров. Механическая обработка проводится для устранения зазубрин, сколов или же любых других дефектов на поверхности метиза, полученных в результате предыдущего проката проволоки, либо во время непосредственного процесса навивки с целью обеспечения наиболее лучшего качества изделия и повышения срока его эксплуатации.
Кроме того, немаловажным этапом является последующая термическая обработка, за счет проведения которой заготовка сможет избавиться от всех полученных во время навивки внутренних напряжений. При этом сам метод обработки выбираю исходя из того, какая была использована сталь для изготовления пружин. В некоторых случаях используют и отпуск и закалку, в некоторых, например, в бронзе, только лишь низкотемпературный отпуск. Так или иначе, каждый из данных процессов позволяет изделию достичь основных своих критериев, в числе которых состоит их великолепная упругость.
Горячая технология изготовления пружин
В отличии от холодного способа, горячее производство пружин подразумевает лишь изготовление изделий с диаметром от 10 миллиметров. То есть метизы меньших габаритов не получится сделать таким способом априори. Горячая технология изготовления пружин для создания заготовок требует проводить процедуру равномерного нагрева. При этом сам нагрев производится очень быстро на специальном станке. После чего разогретый до красна пруток необходимо просунуть через фиксирующую планку в навивочный станок и закрепить концы заготовки в зажимах и выполнять следующие этапы:
- Задать необходимое натяжение через верхний валик.
- Выбрать скорость вращения, в зависимости от диаметра.
- Включить станок, начав процесс навивки проволоки.
- По окончании работ снять цельную заготовку.
- Отправить изделие на термическую обработку.
- Максимально охладить спираль в масле.
- Провести механическую обработку поверхности.
- Нанести защитный антикоррозийный слой.
Обратите внимание, что горячая технология изготовления пружин для экономичного расходования сырьевых материалов не предусматривает разрезание пружины по мере того, как будет достигнут необходимый размер изделия. Это значит, что навивка происходит сразу на всю длину заготовки, а уже потом от нее отрезают куски необходимой длины. Повторная термическая обработка изделия необходима для снятия внутреннего напряжения. Охлаждать заготовку в масле, а не в воде рекомендуется по причине того, что во время долгой закалки в воде горячая сталь может попросту пустить трещину.
Тем не менее, если
Сталь для изготовления пружин

Поскольку пружины зачастую используются для гашения каких-либо типов нагрузок, сталь для изготовления пружин должна иметь очень высокие технические характеристики. В зависимости от предназначения итоговых изделий, для их создания могут использоваться самые различные марки стали. Однако, наиболее часто, производство пружин выполняется из углеродистой и высоколегированной стали. Как правило, заводы-изготовители используют такие марки, как 50ХФА, 50ХГФА, 55ХГР, 55С2, 60С2, 60С2А, 60С2Н2А, 65Г, 70СЗА, У12А, 70Г, а также ещё множество других стальных сплавов.
Среднеуглеродистые и высокоуглеродистые марки стали, а также низколегированные стальные сплавы, которые задействует любое
Дело в том, что при наличии, например, трещин на поверхности изделий, в процессе их эксплуатации при тяжелых различных тяжелых условиях, все усталостные явления будут концентрироваться как раз в наименее устойчивых дефектных местах. Именно поэтому вся
Достичь этого помогает, во-первых, химический состав того или иного сплава, так как под конкретные рабочие условия подбирается конкретная сталь для изготовления пружин. Во-вторых, противостоять напряжению и разрушению позволяют процесс закалки и отпуска изделий. Проведение данных технологических процессов подразумевает любая технология изготовления пружин, однако для каждой марки стали есть свои нюансы. В частности, этим нюансом является среда закаливания, в роли которой выступают масло или вода, а также еще и сама температура, при которой идет закаливание.
Собственно, температура при которой закаливается сталь для изготовления пружин, варьируется в пределах от +800°С до +900°, в зависимости от конкретного сплава. А отпуск проводится уже при диапазоне от +300°С до +480°С. Это обусловлено тем, что именно при подобных температурах возможно достичь одного из самых важных параметров пружинной стали — наибольшего предела упругости стали. Твердость получаемой продукции равняется 35 — 45 единицам твердости по Шору, что равнозначно значению от 1300 до 1600 килограмм на один квадратный миллиметр поверхности.
Характеристики стали для изготовления пружин
Марка сплава |
Термический режим |
Характеристики |
|||||
σ т |
σ в |
δ5 |
φ |
||||
Температура закалки |
Среда закалки |
Температура отпуска |
|||||
Не менее |
|||||||
65 |
840°С |
Масло |
480°С |
80кгс/мм2 |
100кгс/мм2 |
10% |
35% |
70 |
830°С |
85кгс/мм2 |
105кгс/мм2 |
9% |
30% |
||
75 |
820°С |
90кгс/мм2 |
110кгс/мм2 |
||||
85 |
100кгс/мм2 |
115кгс/мм2 |
8% |
||||
60Г |
840°С |
80кгс/мм2 |
100кгс/мм2 |
||||
65Г |
830°С |
80кгс/мм2 |
100кгс/мм2 |
||||
70Г |
85кгс/мм2 |
105кгс/мм2 |
7% |
25% |
|||
55ГС |
820°С |
80кгс/мм2 |
100кгс/мм2 |
8% |
30% |
||
50С2 |
870°С |
Масло или вода |
460°С |
110кгс/мм2 |
120кгс/мм2 |
6% |
30% |
55С2 |
120кгс/мм2 |
130кгс/мм2 |
|||||
55С2А |
|||||||
60С2 |
Масло |
25% |
|||||
60С2А |
420°С |
140кгс/мм2 |
160кгс/мм2 |
20% |
|||
70С3А |
860°С |
460°С |
160кгс/мм2 |
180кгс/мм2 |
25% |
||
50ХГ |
840°С |
440°С |
110кгс/мм2 |
130кгс/мм2 |
7% |
35% |
|
50ХГА |
120кгс/мм2 |
||||||
55ХГР |
830°С |
450°С |
125кгс/мм2 |
140кгс/мм2 |
5% |
30% |
|
50ХФА |
850°С |
520°С |
110кгс/мм2 |
130кгс/мм2 |
8% |
35% |
|
50ХГФА |
120кгс/мм2 |
6% |
|||||
60С2ХФА |
410°С |
170кгс/мм2 |
190кгс/мм2 |
5% |
20% |
||
50ХСА |
520°С |
120кгс/мм2 |
135кгс/мм2 |
6% |
30% |
||
65С2ВА |
420°С |
170кгс/мм2 |
190кгс/мм2 |
5% |
20% |
||
60С2Н2А |
880°С |
160кгс/мм2 |
175кгс/мм2 |
6% |
|||
60С2ХА |
870°С |
180кгс/мм2 |
5% |
||||
60СГА |
860°С |
460°С |
140кгс/мм2 |
160кгс/мм2 |
6% |
25% |
Условные обозначения:
σ т — предел текучести
σ в — предел кратковременной прочности
δ5 — относительное удлинение при разрыве
φ — относительное сужение
s-agroservis.ru
Технология изготовления пружин и требования к ним
Технология изготовления пружин играет важную роль и имеет большое значение для их беспроблемной долгосрочной эксплуатации. Упругие элементы – это высокотехнологичные изделия, требующие наличия квалификации и опыта от инженеров-конструкторов и технологов, а также хорошего парка оборудования на предприятии-производителе.
От того, насколько правильными были расчеты пружины, подбор материала с учетом требуемых характеристик и особенностей ее применения, а также используемые технологии и точность изготовления, зависит работа целого агрегата, где эта деталь будет комплектующей.
Витые пружины сжатия: особенности конструкции и эксплуатации
Данный тип пружин в процессе эксплуатации воспринимает нагрузки, прилагаемые в продольно-осевом направлении. Пружины сжатия изначально имеют просветы между витками, приложение внешней силы приводит к деформации, характеризующейся уменьшением длины изделия, и ограничивается тем моментом, когда витки соприкасаются. При отмене воздействия пружина должна восстановить свою форму и геометрические размеры, какими они были до приложения нагрузки.
Основными размерами, определяющими вид отдельной детали, являются:
- — Диаметр проволоки (прутков).
- — Количество витков.
- — Шаг навивки.
- — Диаметр изделия.
Наиболее распространенными являются цилиндрические винтовые пружины сжатия, у которых диаметр изделия одинаков по всей длине. Эти детали широко используются в разных отраслях промышленности: приборо- и машиностроении, горношахтной отрасли, газонефтедобыче, других.
Вообще же пружины сжатия могут иметь не только цилиндрическую форму, но и конусную, бочкообразную, более сложную. Шаг витков может быть постоянный и переменный, а навивка – по или против направления движения часовой стрелки.
Это вносит особенности в общепринятую технологию их изготовления.
Требования к пружинам
Чтобы выполнять свою работу эффективно и правильно, эти элементы должны обладать хорошей прочностью, пластичностью, упругостью, выносливостью и релаксационной стойкостью.
Достижение этих качеств возможно при соблюдении многих факторов, в том числе:
- — Правильном выборе материала.
- — Грамотно проведенных расчетах.
- — Соблюдении технологии изготовления.
Качественные пружины должны соответствовать требованиям ГОСТ и техническому заданию конкретного заказчика.
Согласно стандарту предусмотрены три группы точности по контролируемым деформациям:
- — С допускаемым отклонениями до 5% (+/-).
- — До 10%.
- — До 20%.
В соответствии с этим определены три группы точности по геометрическим параметрам.
Важное требование к этим деталям – чистота поверхности, здесь не допускаются царапины и другие дефекты, так как они приводят к снижению прочности и надежности.
Требования к материалу
Пружины для работы в определенных условиях выбираются по типоразмерам с учетом характера и величины нагрузок, характерных для условий эксплуатации. Надежность работы этих деталей определяется многими факторами, в том числе – качеством и структурным состоянием металла/сплава после термической обработки, наличием остаточных внутренних напряжений. Кроме того, важно металлургическое качество стали/ сплава. Так что долговечная беспроблемная эксплуатация начинается с выбора материала с определенным комплексом свойств.
Винтовые пружины сжатия в зависимости от размеров, выполняемой работы и других факторов изготавливаются из различных сталей/сплавов, в том числе из конструкционных рессорно-пружинных, нержавеющих, других.
Наиболее широко используемыми материалами можно назвать сталь 60С2А ГОСТ 14959-79, а также 50ХФА, 51ХФА, 60С2ХФА и аналогичные сплавы. Из нержавеющих самое широкое применение находит сталь 12Х18Н10Т.
Особенности технологии
В зависимости от предусмотренного назначения таких деталей и их спецификации уместно говорить об особенностях технологии их производства. Изготовление изделий из материалов, имеющих круглое сечение, может быть выполнено путем холодной или горячей навивки. Первым способом обычно изготавливают мелкие/средние пружины (из проволоки до 8 мм в диаметре), а вторым – крупные.
Кроме того, различие обуславливается применение различных видов термической обработки, что связано с необходимостью придать изделиям определенные характеристики.
Технология холодной навивки пружин без закалки
Навивка заготовок выполняется из проволоки, которая производителем заранее была подвергнута патентированию. Этот процесс представляет собой нагрев до температуры, превышающей интервал превращений, что отлично подготавливает материал для последующей холодной пластической деформации.
В сформированных навивкой заготовках обеспечиваются соответствие таких обязательных параметров, как:
- Диаметр (этот параметр может быть внутренним, средним или наружным).
- Количество предусмотренных витков (рабочих и общих).
- Шаг и размер по высоте изготавливаемой детали (учитываются изменения, возможные в результате последующей обработки).
- Правильность выполнения поджатия крайних витков.
Следующий этап – механическая отделка (торцевание), в процессе которой концевые витки (нерабочие) обрабатываются до образования поверхности, перпендикулярной оси. После этого производится термическая обработка – в данном случае – только низкотемпературный отпуск. Это придает постоянные упругие свойства и нивелирует созданные при навивке напряжения. Важный технологический момент – правильно определить температуру и время воздействия, ориентируясь на диаметр выбранного материала и требования стандартов. Термообработанные пружины подвергаются контролю и испытаниям на соответствие параметров требованиям чертежей.
Если по требованиям эксплуатации предусмотрено антикоррозионное покрытие, его нанесение становится последним этапом производства таких деталей. Только в том случае, если применялась гальваника, детали прогреваются для обезводороживания.
Технология холодной навивки пружин с закалкой и отпуском
Отличие данной технологии от описанной ранее начинается только на этапе термической обработки. Предыдущие действия: навивка и необходимая механическая обработка, выполняются точно так же.
Первым этапом термической обработки выполняется закалка: нагрев до определенной температуры (в зависимости от используемого материала), выдержка детали в течении указанного времени и принудительное (быстрое) охлаждение специальной среде, в основном в масле (иногда в воде, солевом растворе, других). Важно: для нагрева пружин под закалку их располагают горизонтально во избежание просадки под собственным весом.
Завершается термообработка отпуском – прогревом до сравнительно небольшой температуры и выдержкой строго определенное время для придания необходимых качеств.
После этого производится контроль таких параметров, как твердость, правильность сжатия/восстановления. Если предусмотрено технологией изготовления конкретной детали – применяется очистка пескоструем, упрочнение дробью, нанесение предотвращающего коррозию защитного покрытия.
Технология горячей навивки пружин с закалкой и отпуском
Горячая навивка подразумевает предварительный прогрев материала в электрической или газовой печи (возможный вариант – применение токов высокой частоты).
Подготовленная таким образом заготовка подвергается навивке согласно требованиям техзадания, разводке, а также торцовке и доводке геометрических значений с помощью инструментов. После этого деталь подается на закалку, параметры которой определяются используемым материалом, а потом – на отпуск.
По окончании термообработки производится контроль параметров и, если это необходимо, обжатие, заневоливание, другие дополнительные операции и обработка поверхности. Завершается процесс производства окрашиванием и сушкой.
Используемое оборудование и оснастка
Для изготовления пружин требуется различное оборудование, которое лучше всего соответствует требованиям каждого шага технологического процесса.
Навивка осуществляется или на специальных пружинонавивочных станках, или на переоборудованном для этих целей токарном оборудовании. Возможно также использование ручной оснастки или специализированных полуавтоматов. Дальнейшая обработка – механическая – осуществляется торцешлифовальными станками, а термическая – в закалочных и отпускных печах. Важно: для предотвращения коробления при термообработке используются специальные оправки. Для деталей небольшого размера они применяются при отпуске, а большие проходят закалку на оправке.
Контроль качества также проводится на специальном, предназначенном именно для этого процесса оборудовании.
kurskmk.com
Технологический процесс изготовления пружин.
Пружины и рессоры обычно работают в условиях многократных повторных нагружений. Такие детали должны обладать высокими упругими свойствами и выдерживать при эксплуатации большое число повторных нагружений без поломок и без осадки. Последнее означает, что при снятии нагрузки пружина или рессора должна полностью восстанавливать свои первоначальные размеры и форму. Многочисленными исследованиями установлено, что на долговечность работы пружин и рессор большое влияние оказывает качество и чистота обработки поверхности. Риски, волосовины, царапины и другие дефекты поверхности недопустимы, поскольку они резко снижают работоспособность таких деталей.
Пружины небольших размеров навиваются из твердой холоднотянутой проволоки диаметром до 6—8 мм. Проволока изготовляется из углеродистой стали и упрочняется путем особой термической обработки — патентирования. По существу это сочетание изотермической закалки с холодным волочением. После такой закалки проволока приобретает структуру сорбита и затем протягивается последовательно через несколько отверстий (фильер). Диаметр отверстия немного меньше диаметра проволоки, протягиваемой через него. В результате проволока постепенно утоняется до нужных размеров. Уменьшение диаметра проволоки происходит путем пластической деформации, которая сопровождается наклепом. Благодаря этому проволока приобретает высокие упругие и прочностные свойства.
После навивки пружин из такой проволоки термическая обработка нужна только для снятия напряжений, возникших при навивке. С этой целью проводится отпуск при 200—250 °С с выдержкой в течение 20 мин.
Для изготовления пружин небольших и средних размеров наряду с патентированной проволокой используется проволока, полученная методом деформационного упрочнения, который разработан на Горьковском автозаводе. Он заключается в том, что проволоку из сталей 45, 65Г и др. подвергают вначале нормализации, а затем холодному волочению. Из такой проволоки навивкой изготовляют пружины, а затем нагревают их до 280—300 °C и выдерживают в течение 20—40 мин. При этом происходит процесс, называемый деформационным старением, в результате которого получается необходимое упрочнение проволоки. Аналогичным образом можно изготовлять рессоры, производя вместо волочения холодную прокатку листов.
Пружины средних и больших размеров, а также рессоры изготовляют из легированных сталей 50Г, 60С2 и др. Углеродистые стали вследствие их низкой прокаливаемости не используются. Кремнистые стали имеют повышенную прокаливаемость, но склонны к обезуглероживанию. Марганцовистые стали обладают также повышенной прокаливаемостью, но в то же время склонны к трещинам при закалке.
Навивка пружин средних и больших размеров производится из прутков в горячем состоянии. После этого следует термическая обработка.
При этом рекомендуется руководствоваться следующими правилами:
1) нагрев пружин под закалку нужно проводить в горизонтальном положении либо подвешивать их на приспособлении типа елочки; в противном случае пружина под тяжестью собственной массы может дать осадку;
2) пружины растяжения, имеющие витки, прилегающие вплотную один к другому, нужно зажимать или обвязывать так, чтобы их не развело при нагреве;
3) длинные пружины малого диаметра во избежание коробления перед нагревом надо насаживать на оправку;
4) пружины в закалочную жидкость во избежание коробления нужно погружать в вертикальном положении;
5) независимо от марки стали закалку производить в масле;
6) для получения равномерных свойств отпуск пружин лучше проводить в селитряных ваннах, а если в камерных электропечах, то обязательно с вентиляторами;
7) проводить отпуск на твердость HRC 40—47.
Технологический процесс изготовления пружин больших размеров включает следующие операции: горячую навивку; разводку витков на заданный шаг; закалку; отпуск; шлифовку торцов; очистку. При механизированном производстве пружин можно совместить нагрев под навивку и закалку.
Основная трудность при изготовлении пружин — предупреждение коробления при закалке. С этой целью применяют оправки. При изготовлении пружин небольших размеров оправку применяют при отпуске. Если: такая пружина при закалке покоробилась, то при насаживании на оправку перед отпуском она выпрямляется, и в условиях нагрева при отпуске размеры ее фиксируются по оправке. Пружину больших размеров, покоробленную при закалке, трудно зафиксировать на оправке перед отпуском. В таких случаях следует производить закалку на оправке. Однако при этом конструкция оправки должна обеспечивать достаточно полный доступ закалочной жидкости к пружине.
studfile.net
Как делают пружины растяжения и сжатия
Прежде чем давать ответ на вопрос, как делают пружины растяжения или сжатия, необходимо прояснить их назначение, характеристики и их зависимость от геометрических размеров, свойств материалов и других влияющих факторов.
Определение
Пружина – это свёрнутая в спираль металлическая проволока. Её назначение – восстановление своих первоначальных размеров после деформации, вызванной растяжением или сжатием, а также упругое сопротивление такой деформации.
Геометрические особенности
В зависимости от назначения витки могут прилегать один к другому или иметь между собой некоторое расстояние. Также они бывают постоянного (цилиндрические) или переменного (конические) диаметров.
Крайние витки у пружин растяжения, как правило, отгибаются перпендикулярно остальным, чтобы за них можно было зацепиться. У пружин сжатия в некоторых случаях их шлифуют для получения плоской опорной поверхности.
Требования к материалам. Механические характеристики и термообработка
Процесс растяжения или сжатия – это деформация. Чтобы она могла происходить многократно, возникающие при изменении размеров напряжения не должны превышать предел упругости, т. е. некую величину, после которой возможно полное восстановление размеров.
Механические характеристики металлов, из которых изготавливают пружины, зависят от термообработки. В частности, у большинства углеродистых и легированных сталей упругость повышается после закалки. Чтобы избежать хрупкости металла или сплава, повысить его выносливость – способность воспринимать многократные деформации – его дополнительно подвергают отпуску.
У других пружинных материалов, не являющихся сталями – например, сплава 36НХТЮ, бериллиевая бронза и др. – улучшение механических параметров происходит после старения (нагрева и выдержки при высокой температуре).
В процессе изготовления – навивке – металл должен хорошо деформироваться. Его предел текучести – напряжение, при котором пластическая (неупругая) деформация происходит без увеличения нагрузки – должен быть как можно более низким. Для этого материал будущего изделия перед началом технологического процесса отжигают.
Как делают пружины растяжения и сжатия
Один из центральных процессов изготовления – получение проволочной спирали. Он производится навивкой проволоки или прутка на оправку. Она может иметь цилиндрическую коническую или другую форму.
В зависимости от назначения изделия витки навиваются вплотную один к другому или с определённым шагом.
Плотная навивка обычно применяется для пружин растяжения, с шагом – для сжатия.
Холодный и горячий способы
Навивка пружинной проволоки на оправку может производиться с предварительным нагревом и без него.
При изготовлении изделий из тонкой проволоки нагрузка на оборудование невелика. Поэтому процесс можно вести холодным способом, без предварительного нагрева материала. Выбирая радиус оправки, следует учесть, что у до начала пластической деформации материалы сохраняют определённый запас упругости. После окончания навивки диаметр витков увеличивается.
Если проволока изготовлена из стали, обладающей в состоянии поставки высоким пределом текучести, перед началом процесса, её отжигают – нагревают и медленно охлаждают вместе с печью.
При изготовлении пружин и прутка большого диаметра (обычно более 16 мм) навивка ведётся горячим способом. Пруток нагревают до температуры, при которой текучесть снижается до минимума (около 600 С) и навивают на оправку, не охлаждая.
После окончания навивки у будущих пружин растяжения отгибают крайние витки, придают им требуемую форму. У пружин сжатия они могут шлифоваться, если последующая эксплуатация потребует плоских опорных поверхностей.
Термообработка после навивки
Как уже отмечалось ранее, механические свойства материалов пружин могут значительно меняться в зависимости от состояния материала.
Стальные — после завершения техпроцессов, связанных с пластической деформацией подвергают закалке и отпуску. Конкретный набор термических процессов определяется свойствами сталей и требованиями к готовым изделиям.
Пружины из других сплавов упрочняют другими способами, например, старением.
Нанесение покрытий
Поверхность готовой продукции для придания ей коррозионной стойкости подвергается химической обработке: оксидирование, анодирование, покрытие цинком и т.д.
Выбор конкретного вида обработки определяется материалом пружины и предполагаемыми условиями эксплуатации.
nmkn.ru
Навивка пружины на токарном станке: способы, видео
Это техпроцесс, в ходе которого проволока или лента подвергается обработке. В результате чего получаются навивка пружин различной формы: цилиндрической, конической, фасонной или плоской. Основным методом производства считается холодный способ. Навивка пружины выполняется на токарном станке, для этого используется специальное приспособление, вручную или с применением автомата. Производство подобных изделий, возможно и горячим методом, диаметр используемой проволоки от 10 мм. Выбор варианта навивки пружины зависит от размера и типа металла.
Холодный способ изготовления
Технология навивки пружин на токарных станках в России считается более предпочтительной. Обусловлено тем, что горячий способ требует серьезных затрат связанных с приобретением дорогостоящего дополнительного оборудования. Холодный метод имеет ограничения по диаметру проволоки, он не превышает 16 мм. Оснастка для этого техпроцесса состоит из оправок, приспособленных для направления металлической нити на вращающейся катушке.
Вид зависит от формы пружины (цилиндрической, бочкообразной или конической). Приспособление для натяжения и направления проволоки представлено в виде двух вращающихся роликов. Причём верхний имеет винт, который позволяет регулировать натяг и направление. При холодной завивке пружин берется металл с необходимыми качествами, из него делают нужную деталь. В конце проводят термообработку с целью избавления от внутренних напряжений.
Сама технология выглядит так. Стальную проволоку подают через планку, установленную на суппорте оборудования, а конец фиксируется зажимом на оправке. Роликовое приспособление выполняет натяг металлической нити, который важен при изготовлении изделия. После включения станка, начинается намотка пружины, при этом скорость в зависимости от диаметра, используемого материла, находится в пределах 10 – 40 м/мин. Количество витков подсчитывается визуально или счетчиком. По окончании поделка подлежит мехобработке.
Это может быть технология торцовки для пружин сжатия абразивными кругами на специальных автоматах или на промышленных точилах. На изделиях другого профиля технологические концы подлежат обрубке или обрезке, используя специальное приспособление и соответствующий инструмент. Готовый продукт подвергается термообработке в электрических печах.
Технология термической обработки деталей зависит от материала. Для одних марок сталей отпуск и закалка, для других, в том числе и для бронзы – низкотемпературный отпуск, после которого поделки приобретают пружинящие свойства.
Готовую продукцию проверяют и испытывают на соответствие технологическим параметрам (растяжение, сжатие, изгиб, кручение). При необходимости или с согласия заказчика выполняется дополнительная обработка (гальваническое, лакокрасочное или другое покрытие).
Горячий метод изготовления
Навивки пружин на токарных станках таким методом доступны для изготовления изделий из пруткового материала диаметром 10 мм и более. Технологический процесс при этом состоит из ряда этапов:
- обрезка и последующий нагрев;
- оттяжка и вальцовка концов;
- повторный нагрев;
- навивка из нагретого материала;
- отрубаются концы заготовки;
- разводка и правка изделия, последующая термообработка;
- заточка и шлифовка торцов, защита от коррозии, контроль размеров и испытания (прочность, износостойкость и т. п.).
Нагрев заготовки выполняется в короткое время, при этом должно выполниться обязательное условие – равномерный по всему объему прогрев. Для горячей навивки требуется инструмент и оснастка (оправка, молотки, клещи, клинья и т. д.). Все перечисленное навивщику нужно иметь под рукой при выполнении работ по изготовлению пружин. Оправка нужна для навивки пружин на токарных станках, а с помощью клина крепится заготовка на ней. Клещи имеют форму губок обеспечивающих удержание, установку и поворот детали.
В процессе работы нужно руководствоваться технологическими инструкциями, которые обеспечат получение качественных изделий. С целью снижения отходов при изготовлении коротких изделий на оправку укладывается длинная спираль, т. е. делается заготовка на несколько деталей. Процесс навивки пружин на токарных станках большого размера включает практически те же этапы операции, что применяют для средних и мелких заготовок.
Особенности процесса завивки
Полученные после навивки пружины при эксплуатации, находятся в режиме многочисленных повторяющихся нагрузок. Поэтому они должны иметь высокие характеристики по упругости, в процессе работы выдерживать большое количество повторных загрузок без осадки и поломок. Первое означает, что пружины после нагрузки должны быстро восстанавливать заложенную форму и размеры. Практика показывает, что долговечность продукта, изготовленного на станке, напрямую зависит от качества и чистоты обработки проволоки. На поверхности пружин не должны быть царапины, волосовины, риски и другие дефекты, т. к. они приводят к резкому снижению эксплуатационных качеств изделия.
Важным моментом для навивки пружин считается использование оправок (приспособлений), они предупреждают коробление в момент закалки и при отпуске. Даже если деталь покоробилась при закалке, исправить ситуацию можно насадив ее перед процедурой отпуска на оправку. У пружин большого размера дефект, полученный при закалке трудно исправить, т. к. в этом случае затруднена фиксация на оправке. Чтобы этого не случалось нужно термообработку заготовки проводить уже на ней.


Приспособление для навивки пружин на токарном станке
При любом из двух способов навивки пружин на токарных станках должны обеспечиваться следующие параметры:
- внутренний, средний или наружный диаметр продукта;
- общие и рабочие витки, их число;
- высота и шаг пружины с учетом последующей обработки.
Если вы нашли ошибку, пожалуйста, выделите фрагмент текста и нажмите Ctrl+Enter.
stankiexpert.ru
Способ изготовления пружин с повышенной прочностью
Изобретение относится к изготовлению стальных винтовых пружин сжатия с повышенной конструкционной прочностью, работающих в агрессивной сероводородсодержащей среде. Способ включает навивку пружины из прутка, ее термообработку и наклеп. Навивку пружины производят на оправке, выполненной на рабочей поверхности со спиральной канавкой, направление и шаг которой соответствуют направлению и шагу навивки изготавливаемой пружины, и с поперечным сечением в виде окружности. Наклеп производят обкаткой внутренней и внешней поверхности пружины устройством упрочнения, содержащим два деформирующих ролика, расположенных под углом 180° друг относительно друга и под углом 90° между осью вращения ролика и осью навиваемого на оправку прутка пружины. Деформирующие ролики выполнены с канавкой на своей цилиндрической поверхности, соответствующей размерам канавки оправки. Наклеп осуществляют по завершению навивки пружины и после ее термической обработки. Повышается сопротивляемость пружины против усталости, коррозии под нагрузкой и износа. 3 ил.
Изобретение относится к области изготовления стальных винтовых пружин сжатия с повышенной конструкционной прочностью, работающих в агрессивной сероводородсодержащей среде.
Из существующего уровня техники известны различные способы, которые позволяют изготовить пружины или со стабильными упругими характеристиками, или особо выносливые пружины, но с низкими упругими характеристиками во времени. Все способы трудоемки, энергозатратны и склонны к рассеиванию геометрических параметров и силовой характеристики пружин.
Специально разработанный процесс, в производстве изготовления пружин, — наклеп при дробеметной обработке, также как и термическая обработка, позволяет значительно улучшить механические свойства изготавливаемой пружины. Этот процесс создает остаточное напряжение сжатия на обрабатываемой поверхности для повышения сопротивляемости пружины против усталости, коррозии под нагрузкой и износа.
Как известно, в процессе приложения осевой нагрузки, возникающие в материале витка пружины напряжения распределены по длине и поперечному сечению неравномерно. Наиболее напряженными оказываются слои металла на наружной и внутренней поверхностях витка пружины. При этом напряжения на внутренней поверхности витка пружины больше, чем на наружной в 1,4÷1,6 раза [1].
Величина этого неравенства зависит от конструктивных параметров пружины, в том числе величины кривизны витка пружины. Повышенный уровень напряжений на внутренней поверхности витка пружины приводит к тому, что усталостная трещина зарождается на внутренней поверхности витка пружины. Поэтому, с целью эффективного упрочнения пружин при дробеметной обработке, внутренние слои пружины обрабатываются наиболее интенсивно. Это удается выполнить только у пружин, имеющих относительно небольшие диаметры пружины и прутка, из которого она навивается, и большой межвитковый зазор (более чем в 2÷3 раза превышающий диаметр прутка). При таких конструктивных параметрах поток дроби достигает внутренней поверхности витков пружины и производит их наклеп.
В пружинах, имеющих большие диаметры и малый межвитковый зазор (меньший или равный диаметру прутка), поток дроби практически не достигает внутренней поверхности витков и не производит их упрочнения. У таких пружин эффективность дробеметной обработки незначительна, так как она нейтрализует только имеющиеся дефекты на наружной поверхности витка, а разрушение развивается с его внутренней поверхности.
Известен способ упрочнения цилиндрических винтовых пружин сжатия (патент РФ №2595175 «Способ упрочнения цилиндрических винтовых пружин сжатия», B21F 35/00, C21D 7/06, опубликовано 20.08.2016), включающий операции навивки, закалки, отпуска, дробеструйной обработки и заневоливания пружины, после чего производят наклеп внутренней поверхности пружин с использованием устройства упрочнения. Последнее содержит три деформирующих ролика, расположенных друг относительно друга под углом 120°. Усилие наклепа внутренней поверхности пружины создают за счет разворота каждого из деформирующих роликов на угол, величина которого зависит от заданного радиального усилия. Наклеп осуществляют при вращении пружины со скоростью не более 10 об/мин. Повышаются усталостная прочность и долговечность винтовых цилиндрических пружин, снижаются шум, вибрации и усилия протягивания при обработке, повышается период стойкости устройства упрочнения.
К существенным недостаткам известного способа, выбранного в качестве ближайшего аналога-прототипа заявляемого технического решения, следует отнести следующее:
— отсутствие возможности создания определенного по величине и постоянного во времени усилия, необходимого для проведения операции наклепа внутренней поверхности пружины, которое создается за счет разворота каждого из деформирующих роликов на некоторый угол, образуемый за счет наличия некоторого эксцентриситета е между осью каждого из роликов и осью их вращения;
— при развороте каждого из деформирующих роликов на некоторый угол, за счет наличия некоторого эксцентриситета е между осью каждого из роликов и осью их вращения, обеспечивается в большей мере наклеп не внутренней, а боковой — межвитковой поверхности пружины;
— отсутствие элементов крепления пружины в зажимном приспособлении, приводит как к провороту пружины вокруг своей оси, так и к ее сжатию внутри зажимного приспособления при проведении операции наклепа.
Технической задачей, решаемой изобретением, является разработка способа изготовления пружин с повышенной прочностью за счет создания остаточного напряжения сжатия как на внутренней, так и на внешней поверхности витка пружины с целью повышения сопротивляемости изготавливаемой пружины против усталости, коррозии под нагрузкой и износа.
Для решения поставленной задачи предлагается способ изготовления пружин с повышенной прочностью, включающий в себя операции навивки, закалки, отпуска, наклепа при дробеметной обработке и заневоливания, отличающийся тем, что навивку пружины из прутка производят на оправке, содержащей на рабочей поверхности канавку в форме спирали в направлении и с шагом витка соответствующим направлению и шагу навивки изготавливаемой пружины, в поперечном сечении канавка представляет часть окружности с радиусом Rокр равным радиусу прутка и длиной Lокр равной 1/3÷1/2 длины окружности прутка, а процесс наклепа внутренней и внешней поверхности пружины производят обкаткой устройством упрочнения, содержащим два и более кратное двум деформирующих роликов, расположенных друг относительно друга под углом 180°, ось вращения которых образует угол 90° с осью навиваемого на оправку прутка пружины, а на цилиндрической поверхности деформирующих роликов содержится канавка, геометрические размеры которой в поперечном сечении соответствуют геометрическим размерам канавки оправки, при этом, усилие, необходимое для проведения операции наклепа внутренней и внешней поверхности пружины, создается за счет резьбовой фиксации подвижных направляющих деформирующих роликов на боковой поверхности устройства упрочнения, а процесс обкатки пружины устройством упрочнения производят дважды — по завершению процесса навивки и после термической обработки пружины.
Указанная в предлагаемом изобретении совокупность признаков, а именно:
— наличие резьбовой фиксации подвижных направляющих деформирующих роликов на боковой поверхности устройства упрочнения позволяет обеспечить заданное по величине и постоянное во времени усилие в процессе проведения операции наклепа внутренней и внешней поверхности пружины;
— наличие канавки на поверхности оправки и на цилиндрической поверхности ролика со схожими геометрическими размерами, а также наличие угла 90° между осью вращения деформирующих роликов и осью навиваемого на оправку прутка пружины увеличивают эффективность процесса наклепа, обеспечивая после его завершения наличие остаточного напряжения сжатия как на внутренней, так и на внешней поверхности витка пружины для повышения ее сопротивляемости против усталости, коррозии под нагрузкой и износа;
— наличие на рабочей поверхности оправки канавки в форме спирали позволяет обеспечить продольную фиксацию пружины при проведении операции наклепа;
— обкатка пружины устройством упрочнения по завершению процесса навивки позволяет нивелировать созданные при навивке напряжения, а обкатка пружины после термической обработки — создать остаточное напряжение сжатия на внутренней и внешней поверхности витка пружины.
Достигаемым техническим результатом, обеспечиваемым указанной совокупностью признаков, является повышение усталостной прочности и как следствие эксплуатационного ресурса стальных винтовых пружин сжатия, работающих в коррозионных средах.
Сущность изобретения, а также осуществление способа изготовления пружин с повышенной прочностью поясняется чертежами, где на фиг. 1 показана оправка и навитая на оправку пружина, на фиг. 2 — показана навитая на оправку пружина в устройстве упрочнения, на фиг. 3 — устройство упрочнения, вид сбоку. Устройство упрочнения представлено с наименьшим, кратным двум, количеством деформирующих роликов.
Способ осуществляют следующим образом.
После выполнения операции навивки пружины 1 из прутка на оправку 2, последняя крепится на суппорте токарного станка. Устройство упрочнения 3, содержащее два деформирующих ролика 4, устанавливается в патроне токарного станка. Перемещением подвижных направляющих 5 деформирующих роликов 4 задают угол 90° между осью вращения деформирующих роликов 4 и осью навитого на оправку первого прутка пружины 1, а за счет резьбовой фиксации на боковой поверхности устройства упрочнения 3 подвижных направляющих 5 на заданном расстоянии относительно продольной оси устройства упрочнения 3 создают требуемое усилие, необходимое для проведения операции наклепа внутренней и внешней поверхности пружины. Процесс упрочнения пружины 1 осуществляют путем вращения устройства упрочнения 3 с числом оборотов не более 5 об/мин с последовательным движением каждого из деформирующих роликов 4 по внешней поверхности пружины 1.
В процессе упрочнения, предлагаемым в данном изобретении способом, на внутренней и внешней поверхности витка пружины создается упрочненный слой с повышенными механическими свойствами и остаточным напряжением сжатия, который при эксплуатационных нагрузках пружины нейтрализует концентраторы напряжений, имеющих глубину, соизмеримую с глубиной распространения остаточных сжимающих напряжений. Все это оказывает упрочняющее воздействие — увеличивая уровень допустимых рабочих напряжений и срок службы пружины.
После этого производится термическая обработка пружины, обеспечивая тем самым постоянство созданных упругих свойств готового изделия — пружины.
По окончании термообработки производится повторная обкатка пружины устройством упрочнения, далее контроль параметров и, если это необходимо, обжатие, заневоливание и другие дополнительные механические операции: отделка и обработка поверхности. Завершается процесс производства пружины окрашиванием и сушкой.
При осуществлении изобретения получен технический результат, заключающийся в изготовлении стальных винтовых пружин сжатия с повышенной конструкционной прочностью, работающих в агрессивной сероводород содержащей среде.
Из патентной литературы не известны способы изготовлении стальных винтовых пружин сжатия с повышенной конструкционной прочностью с идентичными существенными признаками заявляемому техническому решению, что говорит о его новизне и соответствию этому критерию для изобретения.
Совокупность изложенных выше существенных признаков необходима и достаточна для реализации задачи заявляемого решения. При этом между совокупностью существенных признаков и задачей, поставленной и решаемой изобретением, существует причинно-следственная связь, при которой сама совокупность признаков является причиной, а решаемая ими задача является следствием. Исходя из этих доводов, правомерен вывод о том, что заявляемое техническое решение соответствует установленному критерию — изобретательский уровень (неочевидность).
Заявляемое техническое решение может быть неоднократно реализовано с получением указанного выше технического результата.
Решение, таким образом, соответствует критерию «промышленная применимость».
Предлагаемое решение в качестве изобретения применяется в промышленных масштабах для собственных нужд в Газопромысловом управлении ООО «Газпром добыча Астрахань» при производстве ремонтных работ по восстановлению работоспособности клапана-отсекателя модели «BAAOFVHE» комплекта подземного оборудования производства фирмы «Baker Hughes Inc.» (США), связанных с заменой разрушенной исполнительной пружины на пружину с повышенной конструкционной прочностью, изготовленную в соответствии с предлагаемым изобретением из материала MP35N согласно разработанной спецификации.
Технико-экономическое преимущество заявляемого изобретения заключается в изготовлении пружин, не уступающих по своим технико-эксплуатационным свойствам оригинальным импортным аналогам, при значительно меньших производственных затратах.
Источники информации:
1. Пономарев С.Д., Андреева Л.Е. Расчет упругих элементов машин и приборов. — М.: Машиностроение, 1980; ГОСТ Р 54326-2011. Пружины рессорного подвешивания железнодорожного подвижного состава. Методы испытания на циклическую долговечность.
Способ изготовления стальных винтовых пружин сжатия, включающий навивку пружины из прутка, ее термообработку и наклеп, отличающийся тем, что навивку пружины производят на оправке, выполненной на рабочей поверхности со спиральной канавкой, направление и шаг которой соответствуют направлению и шагу навивки изготавливаемой пружины, и с поперечным сечением в виде окружности с радиусом Rокр, равным радиусу прутка, и длиной Lокр, равной 1/3÷1/2 длины окружности прутка, а наклеп производят обкаткой внутренней и внешней поверхности пружины устройством упрочнения, содержащим два деформирующих ролика, расположенных под углом 180° друг относительно друга и под углом 90° между осью вращения ролика и осью навиваемого на оправку прутка пружины, причем деформирующие ролики выполнены с канавкой на своей цилиндрической поверхности, геометрические размеры которой в поперечном сечении соответствуют геометрическим размерам канавки оправки, при этом наклеп внутренней и внешней поверхностей пружины осуществляют по завершению навивки пружины и после ее термической обработки с усилием, создаваемым посредством резьбовой фиксации подвижных направляющих деформирующих роликов на боковой поверхности устройства упрочнения, с числом оборотов вращения устройства упрочнения не более 5 об/мин.
findpatent.ru
Способ изготовления пружин с повышенной прочностью
Изобретение относится к области изготовления стальных винтовых пружин сжатия с повышенной конструкционной прочностью, работающих в агрессивной сероводородсодержащей среде.
Из существующего уровня техники известны различные способы, которые позволяют изготовить пружины или со стабильными упругими характеристиками, или особо выносливые пружины, но с низкими упругими характеристиками во времени. Все способы трудоемки, энергозатратны и склонны к рассеиванию геометрических параметров и силовой характеристики пружин.
Специально разработанный процесс, в производстве изготовления пружин, — наклеп при дробеметной обработке, также как и термическая обработка, позволяет значительно улучшить механические свойства изготавливаемой пружины. Этот процесс создает остаточное напряжение сжатия на обрабатываемой поверхности для повышения сопротивляемости пружины против усталости, коррозии под нагрузкой и износа.
Как известно, в процессе приложения осевой нагрузки, возникающие в материале витка пружины напряжения распределены по длине и поперечному сечению неравномерно. Наиболее напряженными оказываются слои металла на наружной и внутренней поверхностях витка пружины. При этом напряжения на внутренней поверхности витка пружины больше, чем на наружной в 1,4÷1,6 раза [1].
Величина этого неравенства зависит от конструктивных параметров пружины, в том числе величины кривизны витка пружины. Повышенный уровень напряжений на внутренней поверхности витка пружины приводит к тому, что усталостная трещина зарождается на внутренней поверхности витка пружины. Поэтому, с целью эффективного упрочнения пружин при дробеметной обработке, внутренние слои пружины обрабатываются наиболее интенсивно. Это удается выполнить только у пружин, имеющих относительно небольшие диаметры пружины и прутка, из которого она навивается, и большой межвитковый зазор (более чем в 2÷3 раза превышающий диаметр прутка). При таких конструктивных параметрах поток дроби достигает внутренней поверхности витков пружины и производит их наклеп.
В пружинах, имеющих большие диаметры и малый межвитковый зазор (меньший или равный диаметру прутка), поток дроби практически не достигает внутренней поверхности витков и не производит их упрочнения. У таких пружин эффективность дробеметной обработки незначительна, так как она нейтрализует только имеющиеся дефекты на наружной поверхности витка, а разрушение развивается с его внутренней поверхности.
Известен способ упрочнения цилиндрических винтовых пружин сжатия (патент РФ №2595175 «Способ упрочнения цилиндрических винтовых пружин сжатия», B21F 35/00, C21D 7/06, опубликовано 20.08.2016), включающий операции навивки, закалки, отпуска, дробеструйной обработки и заневоливания пружины, после чего производят наклеп внутренней поверхности пружин с использованием устройства упрочнения. Последнее содержит три деформирующих ролика, расположенных друг относительно друга под углом 120°. Усилие наклепа внутренней поверхности пружины создают за счет разворота каждого из деформирующих роликов на угол, величина которого зависит от заданного радиального усилия. Наклеп осуществляют при вращении пружины со скоростью не более 10 об/мин. Повышаются усталостная прочность и долговечность винтовых цилиндрических пружин, снижаются шум, вибрации и усилия протягивания при обработке, повышается период стойкости устройства упрочнения.
К существенным недостаткам известного способа, выбранного в качестве ближайшего аналога-прототипа заявляемого технического решения, следует отнести следующее:
— отсутствие возможности создания определенного по величине и постоянного во времени усилия, необходимого для проведения операции наклепа внутренней поверхности пружины, которое создается за счет разворота каждого из деформирующих роликов на некоторый угол, образуемый за счет наличия некоторого эксцентриситета е между осью каждого из роликов и осью их вращения;
— при развороте каждого из деформирующих роликов на некоторый угол, за счет наличия некоторого эксцентриситета е между осью каждого из роликов и осью их вращения, обеспечивается в большей мере наклеп не внутренней, а боковой — межвитковой поверхности пружины;
— отсутствие элементов крепления пружины в зажимном приспособлении, приводит как к провороту пружины вокруг своей оси, так и к ее сжатию внутри зажимного приспособления при проведении операции наклепа.
Технической задачей, решаемой изобретением, является разработка способа изготовления пружин с повышенной прочностью за счет создания остаточного напряжения сжатия как на внутренней, так и на внешней поверхности витка пружины с целью повышения сопротивляемости изготавливаемой пружины против усталости, коррозии под нагрузкой и износа.
Для решения поставленной задачи предлагается способ изготовления пружин с повышенной прочностью, включающий в себя операции навивки, закалки, отпуска, наклепа при дробеметной обработке и заневоливания, отличающийся тем, что навивку пружины из прутка производят на оправке, содержащей на рабочей поверхности канавку в форме спирали в направлении и с шагом витка соответствующим направлению и шагу навивки изготавливаемой пружины, в поперечном сечении канавка представляет часть окружности с радиусом Rокр равным радиусу прутка и длиной Lокр равной 1/3÷1/2 длины окружности прутка, а процесс наклепа внутренней и внешней поверхности пружины производят обкаткой устройством упрочнения, содержащим два и более кратное двум деформирующих роликов, расположенных друг относительно друга под углом 180°, ось вращения которых образует угол 90° с осью навиваемого на оправку прутка пружины, а на цилиндрической поверхности деформирующих роликов содержится канавка, геометрические размеры которой в поперечном сечении соответствуют геометрическим размерам канавки оправки, при этом, усилие, необходимое для проведения операции наклепа внутренней и внешней поверхности пружины, создается за счет резьбовой фиксации подвижных направляющих деформирующих роликов на боковой поверхности устройства упрочнения, а процесс обкатки пружины устройством упрочнения производят дважды — по завершению процесса навивки и после термической обработки пружины.
Указанная в предлагаемом изобретении совокупность признаков, а именно:
— наличие резьбовой фиксации подвижных направляющих деформирующих роликов на боковой поверхности устройства упрочнения позволяет обеспечить заданное по величине и постоянное во времени усилие в процессе проведения операции наклепа внутренней и внешней поверхности пружины;
— наличие канавки на поверхности оправки и на цилиндрической поверхности ролика со схожими геометрическими размерами, а также наличие угла 90° между осью вращения деформирующих роликов и осью навиваемого на оправку прутка пружины увеличивают эффективность процесса наклепа, обеспечивая после его завершения наличие остаточного напряжения сжатия как на внутренней, так и на внешней поверхности витка пружины для повышения ее сопротивляемости против усталости, коррозии под нагрузкой и износа;
— наличие на рабочей поверхности оправки канавки в форме спирали позволяет обеспечить продольную фиксацию пружины при проведении операции наклепа;
— обкатка пружины устройством упрочнения по завершению процесса навивки позволяет нивелировать созданные при навивке напряжения, а обкатка пружины после термической обработки — создать остаточное напряжение сжатия на внутренней и внешней поверхности витка пружины.
Достигаемым техническим результатом, обеспечиваемым указанной совокупностью признаков, является повышение усталостной прочности и как следствие эксплуатационного ресурса стальных винтовых пружин сжатия, работающих в коррозионных средах.
Сущность изобретения, а также осуществление способа изготовления пружин с повышенной прочностью поясняется чертежами, где на фиг. 1 показана оправка и навитая на оправку пружина, на фиг. 2 — показана навитая на оправку пружина в устройстве упрочнения, на фиг. 3 — устройство упрочнения, вид сбоку. Устройство упрочнения представлено с наименьшим, кратным двум, количеством деформирующих роликов.
Способ осуществляют следующим образом.
После выполнения операции навивки пружины 1 из прутка на оправку 2, последняя крепится на суппорте токарного станка. Устройство упрочнения 3, содержащее два деформирующих ролика 4, устанавливается в патроне токарного станка. Перемещением подвижных направляющих 5 деформирующих роликов 4 задают угол 90° между осью вращения деформирующих роликов 4 и осью навитого на оправку первого прутка пружины 1, а за счет резьбовой фиксации на боковой поверхности устройства упрочнения 3 подвижных направляющих 5 на заданном расстоянии относительно продольной оси устройства упрочнения 3 создают требуемое усилие, необходимое для проведения операции наклепа внутренней и внешней поверхности пружины. Процесс упрочнения пружины 1 осуществляют путем вращения устройства упрочнения 3 с числом оборотов не более 5 об/мин с последовательным движением каждого из деформирующих роликов 4 по внешней поверхности пружины 1.
В процессе упрочнения, предлагаемым в данном изобретении способом, на внутренней и внешней поверхности витка пружины создается упрочненный слой с повышенными механическими свойствами и остаточным напряжением сжатия, который при эксплуатационных нагрузках пружины нейтрализует концентраторы напряжений, имеющих глубину, соизмеримую с глубиной распространения остаточных сжимающих напряжений. Все это оказывает упрочняющее воздействие — увеличивая уровень допустимых рабочих напряжений и срок службы пружины.
После этого производится термическая обработка пружины, обеспечивая тем самым постоянство созданных упругих свойств готового изделия — пружины.
По окончании термообработки производится повторная обкатка пружины устройством упрочнения, далее контроль параметров и, если это необходимо, обжатие, заневоливание и другие дополнительные механические операции: отделка и обработка поверхности. Завершается процесс производства пружины окрашиванием и сушкой.
При осуществлении изобретения получен технический результат, заключающийся в изготовлении стальных винтовых пружин сжатия с повышенной конструкционной прочностью, работающих в агрессивной сероводород содержащей среде.
Из патентной литературы не известны способы изготовлении стальных винтовых пружин сжатия с повышенной конструкционной прочностью с идентичными существенными признаками заявляемому техническому решению, что говорит о его новизне и соответствию этому критерию для изобретения.
Совокупность изложенных выше существенных признаков необходима и достаточна для реализации задачи заявляемого решения. При этом между совокупностью существенных признаков и задачей, поставленной и решаемой изобретением, существует причинно-следственная связь, при которой сама совокупность признаков является причиной, а решаемая ими задача является следствием. Исходя из этих доводов, правомерен вывод о том, что заявляемое техническое решение соответствует установленному критерию — изобретательский уровень (неочевидность).
Заявляемое техническое решение может быть неоднократно реализовано с получением указанного выше технического результата.
Решение, таким образом, соответствует критерию «промышленная применимость».
Предлагаемое решение в качестве изобретения применяется в промышленных масштабах для собственных нужд в Газопромысловом управлении ООО «Газпром добыча Астрахань» при производстве ремонтных работ по восстановлению работоспособности клапана-отсекателя модели «BAAOFVHE» комплекта подземного оборудования производства фирмы «Baker Hughes Inc.» (США), связанных с заменой разрушенной исполнительной пружины на пружину с повышенной конструкционной прочностью, изготовленную в соответствии с предлагаемым изобретением из материала MP35N согласно разработанной спецификации.
Технико-экономическое преимущество заявляемого изобретения заключается в изготовлении пружин, не уступающих по своим технико-эксплуатационным свойствам оригинальным импортным аналогам, при значительно меньших производственных затратах.
Источники информации:
1. Пономарев С.Д., Андреева Л.Е. Расчет упругих элементов машин и приборов. — М.: Машиностроение, 1980; ГОСТ Р 54326-2011. Пружины рессорного подвешивания железнодорожного подвижного состава. Методы испытания на циклическую долговечность.
Способ изготовления стальных винтовых пружин сжатия, включающий навивку пружины из прутка, ее термообработку и наклеп, отличающийся тем, что навивку пружины производят на оправке, выполненной на рабочей поверхности со спиральной канавкой, направление и шаг которой соответствуют направлению и шагу навивки изготавливаемой пружины, и с поперечным сечением в виде окружности с радиусом R, равным радиусу прутка, и длиной L, равной 1/3÷1/2 длины окружности прутка, а наклеп производят обкаткой внутренней и внешней поверхности пружины устройством упрочнения, содержащим два деформирующих ролика, расположенных под углом 180° друг относительно друга и под углом 90° между осью вращения ролика и осью навиваемого на оправку прутка пружины, причем деформирующие ролики выполнены с канавкой на своей цилиндрической поверхности, геометрические размеры которой в поперечном сечении соответствуют геометрическим размерам канавки оправки, при этом наклеп внутренней и внешней поверхностей пружины осуществляют по завершению навивки пружины и после ее термической обработки с усилием, создаваемым посредством резьбовой фиксации подвижных направляющих деформирующих роликов на боковой поверхности устройства упрочнения, с числом оборотов вращения устройства упрочнения не более 5 об/мин.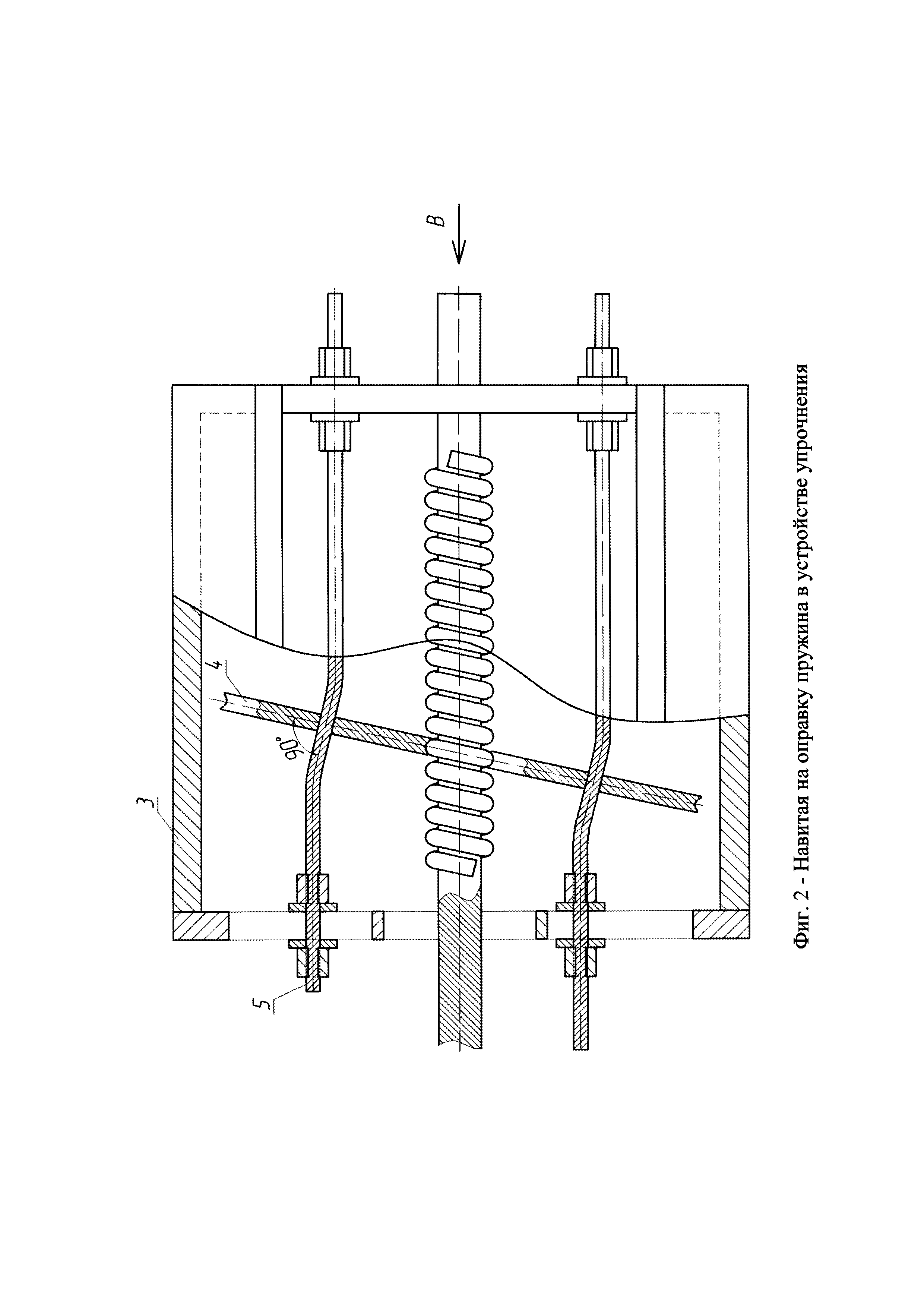
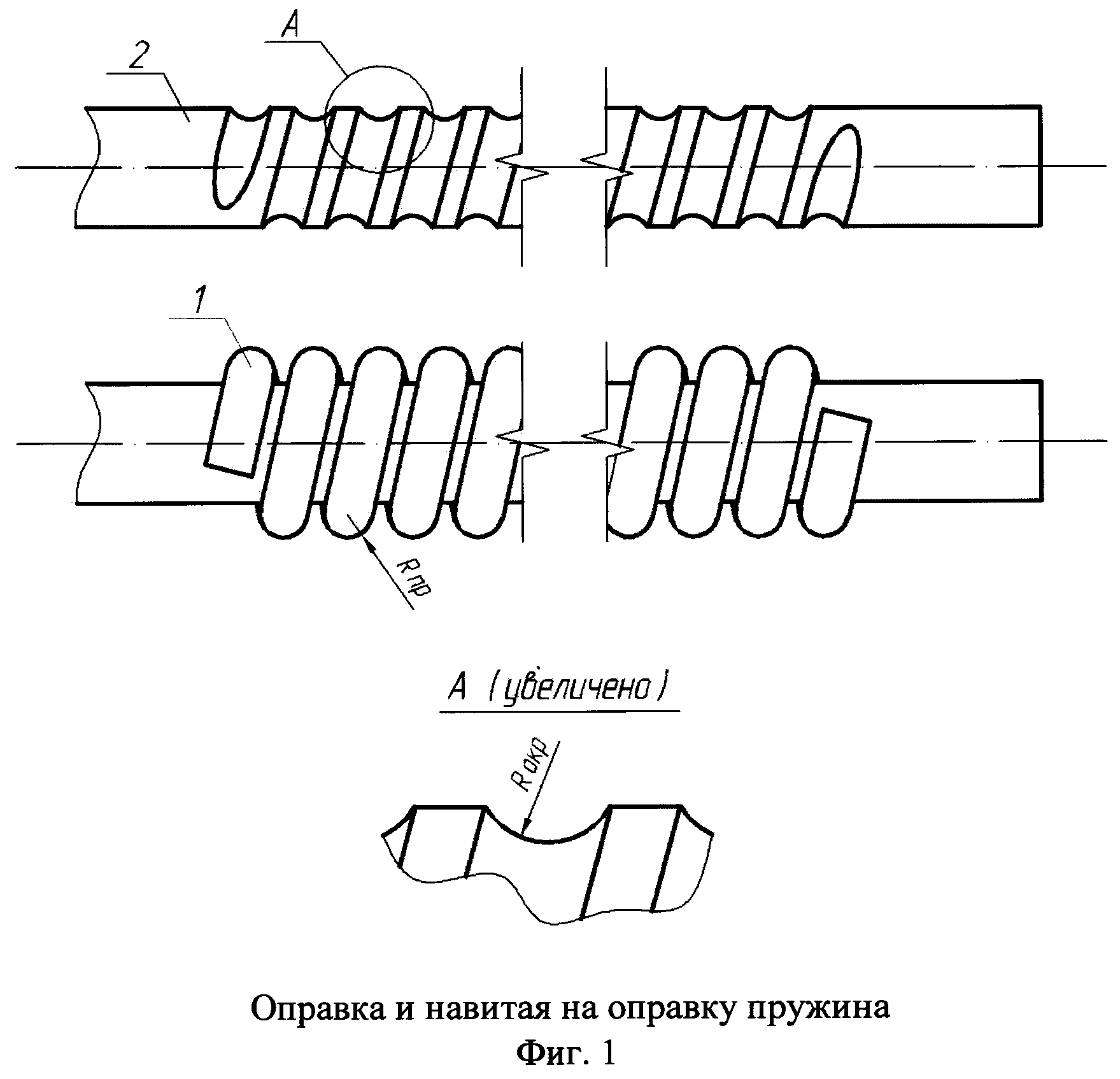
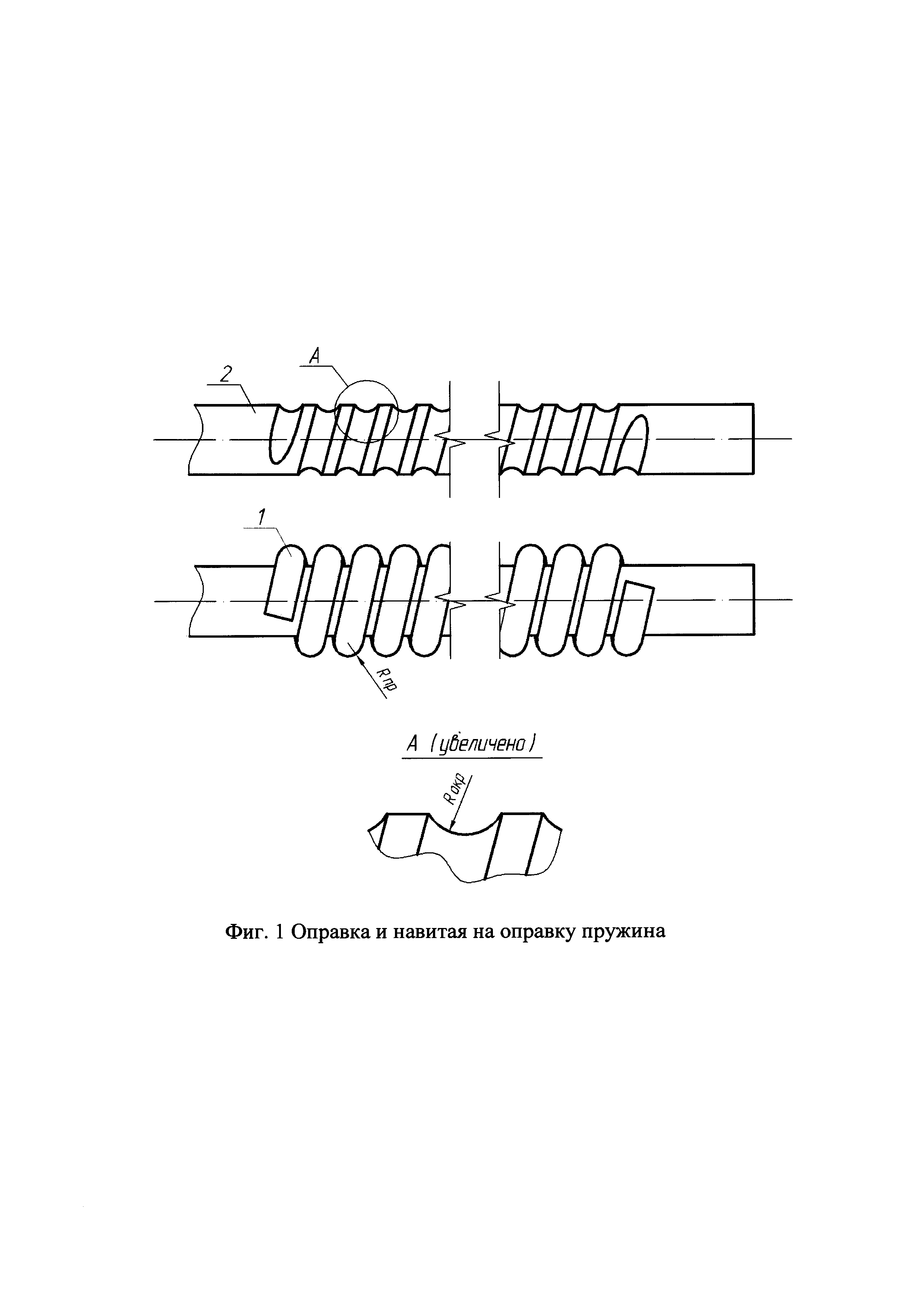
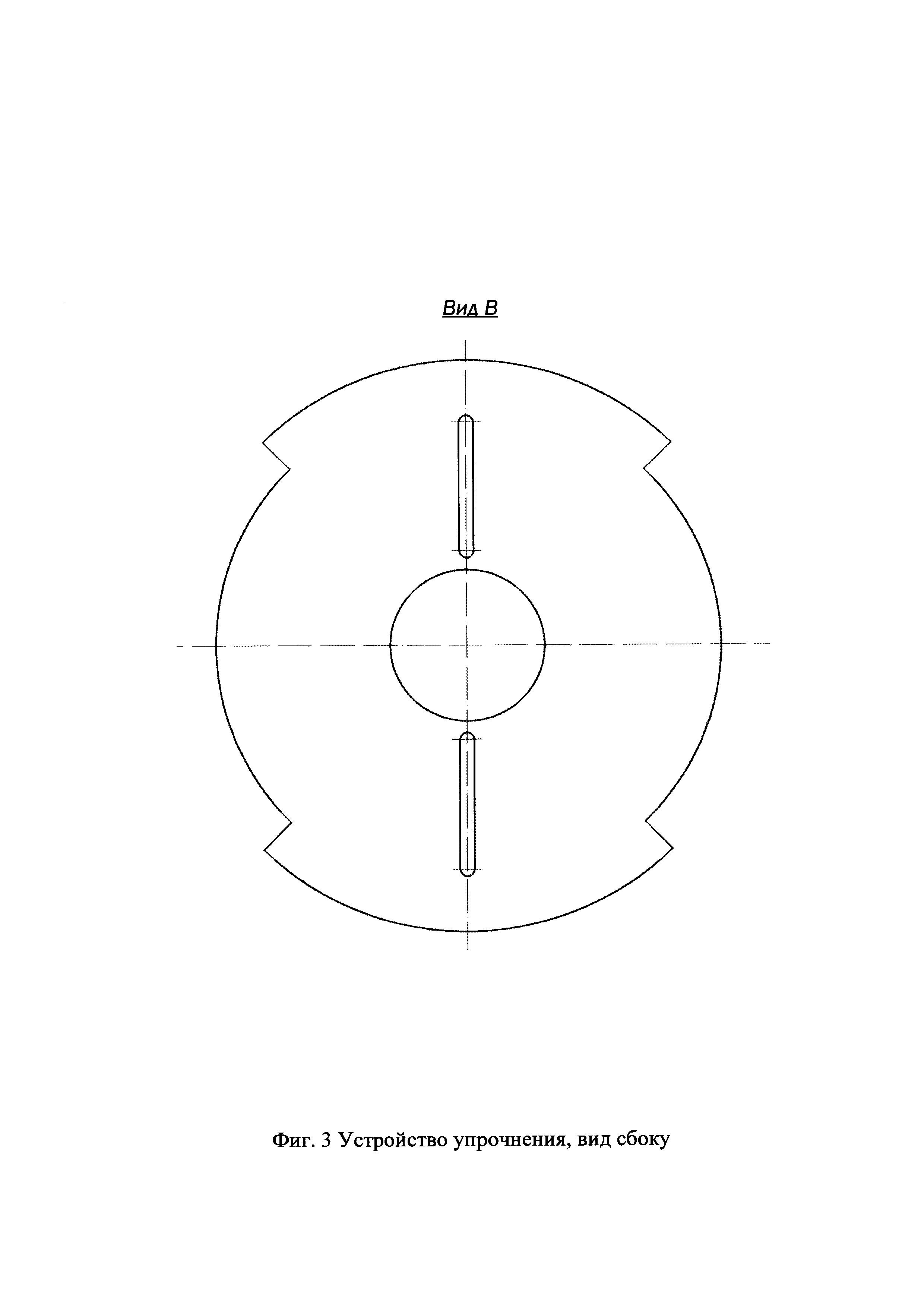
edrid.ru