Станки для производства шпона — особенности, виды, применение и назначение
Дорогостоящие сорта лесоматериалов являются прекрасным сырьем для создания предметов мебели, однако не все люди могут себе позволить такую дорогую продукцию. С целью экономии ценных пород древесины и снижения стоимости конечного продукта и был придуман шпон. Этот материал сегодня крайне популярен для облицовки мебели. Шпон на 100% повторяет узор, текстуру и оттенок натуральной древесины.
Для создания шпона на производствах пользуются специальными станками. Шпон бывает:
- лущеный
- строганый
- пиленый.
Соответственно и станок для производства шпона бывает трех типов.
Лущильный станок для производства шпона
Для реализации лущения шпона сырье необходимо предварительно обработать паром для того, чтобы увеличить пластичность. После этого кряжи подаются на окорочный станок, где с заготовки удаляется кора, а вместе с ней грязь и песок, которые часто становятся причиной быстрого затупления лущильных ножей. При помощи пилы кряжи раскраивают на чураки определенной длины. Чурак нужно предварительно оцилиндровать, после чего можно приступать к лущению. Лента шпона, которая выходит из лущильного станка, кладется на конвейер, подающий ее к ножницам. Ножницы режут шпон на листы необходимого формата. По конвейеру шпон укладывается в пачку, которая выносится из-под ножниц и при помощи электрического погрузчика доставляется в сушилку. Сушат продукцию в роликовой сушилке, далее на конвейере его сортируют и складывают по сортам в пачки. Дефектные листы можно склеить. Если на листах имеются сучки, их отправляют на шпонопочиночный станок, где удаляют изъяны и декорируют их вставками из шпона.
Такой станок для шпона позволяет получить листовой материал толщиной от 1,5 до 5 мм из разнообразных сортов лесоматериалов. На большинстве станков имеется система, которая позволяет в автоматическом режиме устанавливать бревно для последующей обработки.
Чтобы повысить производительность и удобство работы оператора станки оборудуют гидравлическими подъемниками-центроискателями, которые сами определяют подходящую ось вращения заготовки и совмещают ее с осью вращения центровочных валов.
Лущение пропаренной древесины используется для сосновых, ольховых, березовых лесоматериалов. Из лущеного шпона изготавливают фанеру.
Станок для строгания шпона
Прежде всего, кряжи подвергают поперечному раскрою. Во время этой процедуры кряжи распиливают на отрезки необходимой длины. Все отрезки распиливают вдоль, вследствие чего образуется двухкантный брус. Иногда его распиливают пополам. После этого ванчесы подвергают тепловой обработке в пропарочной камере или автоклаве.
Далее ванчесы нужно острогать на шпонострогальном станке. Строганный шпон сушат в роликовых сушилках, торцуют и пакуют в пачки. В каждом наборе составляется конкретный рисунок. Оттенок и узор древесины должны совпадать в каждом наборе. Именно по этой причине листы шпона, которые получаются из каждого ванчеса во время строгания, складывают, сушат и пакуют в пачки точно в том порядке, в каком они выходили из строгального станка. Когда строгаются одновременно три ванчеса, шпон из каждого из них складывают в три разные пачки. Укомплектованную, высушенную, запакованную и перетянутую шпагатом пачку шпона называют кнолем.
Станок для изготовления шпона позволяет создать из дорогостоящих сортов лесоматериалов, которые отличаются необычной текстурой, тонкие листы. Такой материал отлично подходит для фанерования. Методы создания шпона:
- радиальный
- тангенциальный
- радиально-тангенциальный
- тангенциально-торцовый.
Наиболее привлекательным сырьем для создания шпона является дубовая древесина. Такой шпон используют для облицовки рустикальных предметов мебели элитного сегмента.
Кроме дубового шпона в специализированных магазинах можно встретить кленовый, буковый, липовый материал, а также из красного дерева.
Станок для сшивки шпона
Шпон режут на специализированных аппаратах. Он отличается довольно тонкой и хрупкой структурой. Для того, чтобы отделать поверхность шпоном, его необходимо соединить между собой для получения полотна, скатываемого в рулоны. Шпон соединяют двумя способами:
- склейка
- сшивка.
Эти методы одинаково популярны на мебельных производствах. Сшивку шпона осуществляют на станке или ручным способом. Для небольших мастерских разработаны ручные устройства для склейки или сшивки шпона. При помощи особого устройства клеевую или термонить разогревают, и в виде зигзага наносят на основную сторону.
Сегодня станки для сшивки шпона представляют собой небольшие аппараты, функционирующие в автономном режиме. Управление такой машиной осуществляет один специалист. Вся работа на них производится четко, качественно и достаточно быстро.
Ручная сшивка встречается все реже, главным образом, в антикварных, реставрационных и авторских мастерских.
Изготовление строганого шпона
Содержание страницы
1. Состав основных технологических операций и применяемое оборудование для изготовления строганого шпона
1.1. Характеристика строганого шпона и сырья для его изготовления
Строганый шпон изготавливается из древесины красивой текстуры и цвета (см. цв. вкл., ил. 22) и применяется как облицовочный материал для деталей из малоценной древесины, фанеры и ДСтП.
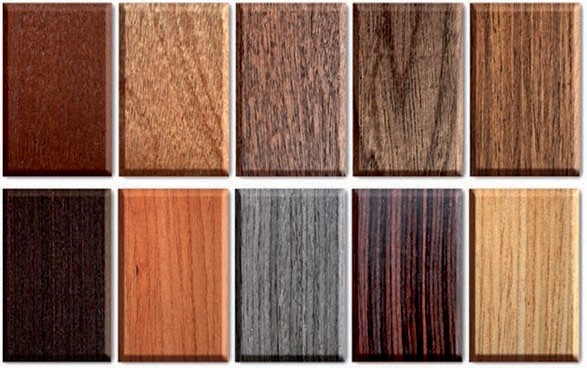
Из древесины рассеяннососудистых пород (красное дерево, бук, орех, клен, груша, яблоня, тополь, береза) изготавливается шпон толщиной 0,4; 0,6; 0,8 мм. Из кольцесосудистых пород (дуб, ясень, ильм) и хвойных пород (лиственница, сосна) изготавливается шпон толщиной 0,8 и 1 мм. Толщина шпона обусловливает удобство работы с ним, исключение просачивания клея, возможность шлифования и отделки.
В зависимости от направления волокон различают радиальный, полурадиальный, тангентальный и тангентально-торцовый шпон. В радиальном шпоне годичные слои расположены в виде параллельных линий на всей площади листа. В полурадиальном шпоне годичные слои в виде параллельных линий занимают 3/4 общей площади. В торцовом шпоне годичные слои в виде острых углов, а в тангентально-торцовом шпоне годичные слои располагаются в виде замкнутых кривых линий.
В зависимости от вида дефектов древесины и обработки шпон подразделяют на первый и второй сорт. Ширина делянок шпона первого сорта — от 100 до 400 мм. Ширина делянок второго сорта — от 70 до 150 мм. Длина от 1 до 3,5 м — первого сорта, от 0,5 до 3,5 м — 2 сорта. Влажность 8 ± 2%. Шероховатость поверхности: для лиственных пород — от 100 до 200 мкм, для хвойных пород — от 100 до 250 мкм.
Для изготовления строганого шпона используются ценные породы древесины с ярко выраженной текстурой. Лиственные породы: дуб, ясень, ильм, бук диаметром 26 см и более, красное дерево диаметром 40 см и более, длиной 3 м и более; хвойных пород: лиственница диаметром 32 см и более, длиной не менее 2,5 м.
1.2. Схема технологического процесса изготовления строганого шпона. Подготовка сырья к строганию
Схема технологического процесса изготовления строганого шпона представлена на рисунке 1.
Подготовка сырья к строганию заключается в поперечном и продольном раскрое сырья и его гидротермической обработке. Сырье раскраивается по длине при помощи цепных пил. Продольный раскрой на ванчесы и брусья производится на горизонтальных лесопильных рамах или ленточных станках. Способы разделки выбираются в зависимости от породы древесины, диаметра сырья и его формы (рис. 2).
Двухкантнобрусовый применяется для древесины, не содержащей ярко выраженных сердцевинных лучей (практически не применяется). Тупокантный способ раскроя используется при диаметре сырья от 30 до 40 см (встречается очень редко).
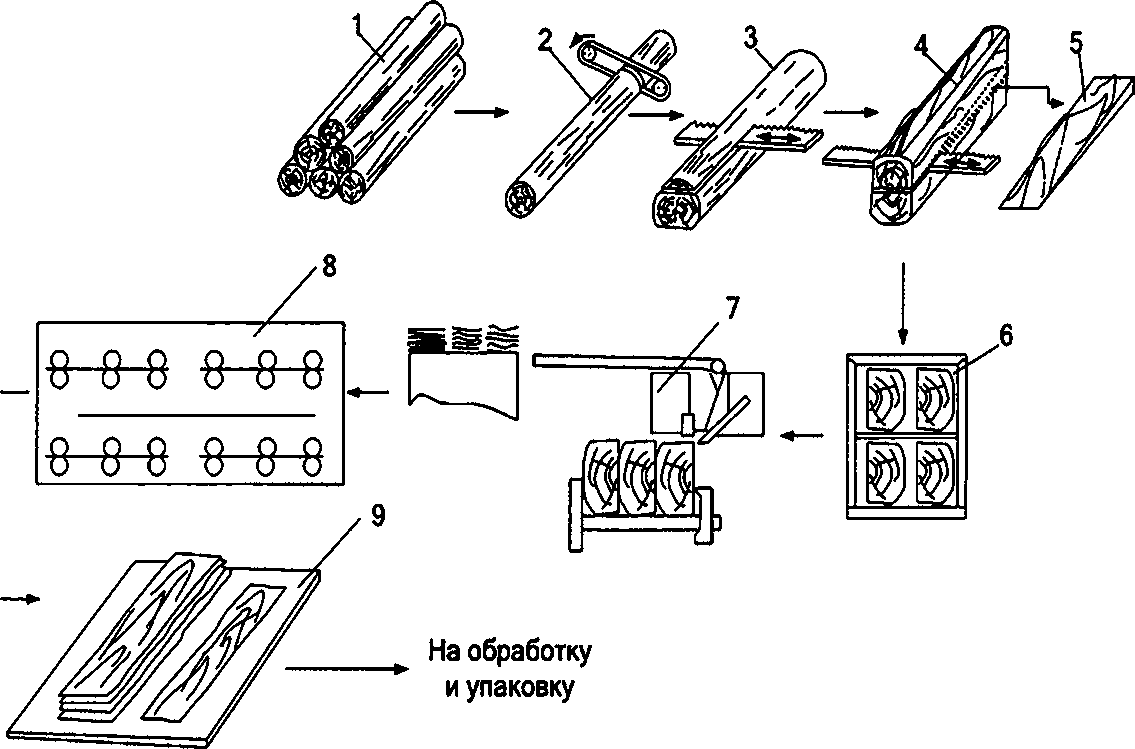
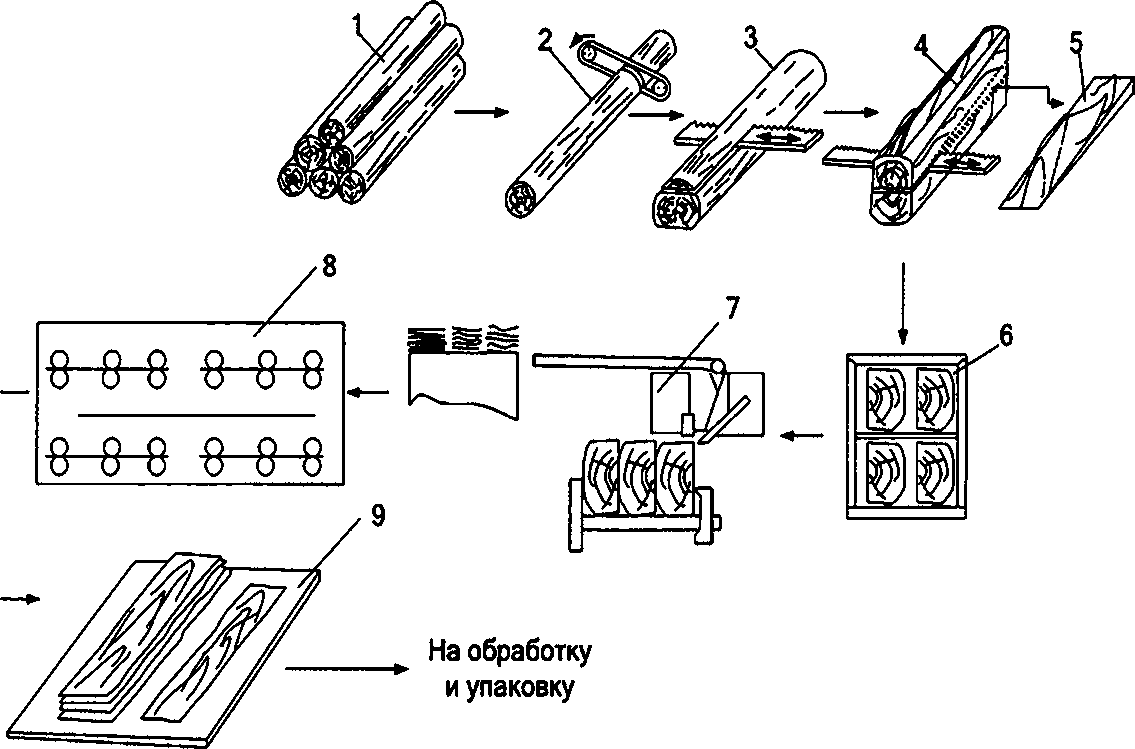
Рис. 1 Схема процесса изготовления строганого шпона: 1 — хранение; 2 — продольный раскрой; 3 и 4 — поперечный раскрой; 5 — переработка отходов; 6 — гидротермическая обработка; 7 — строгание шпона; 8 — сушка шпона; 9 — сортировка и упаковка.
Ванчесный четырехсторонний — основной способ для переработки сырья диаметром от 30 до 80 см. Для древесины с овальной формой в поперечном сечении применяется способ асимметричной разделки.
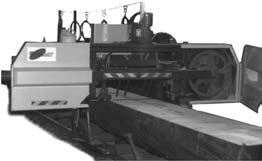
Рис. 2 Продольный раскрой бревен на ленточнопильном станке
Сырье диаметра 80 см и более раскраивается на четверти. Секторный способ разделки применяется при изготовлении радиального шпона. Ванчесный четырехсторонний способ применяется для древесины с внутренней гнилью.
Гидротермическая обработка ванчесов перед строганием шпона производится в автоклавах для придания древесине пластических свойств. Обычно производится пропарка с использованием мягких режимов.
Оптимальная температура: дуб, ясень, ильм, вяз 40– 50°C; бук, орех, клен, береза 45–50°C; лиственница 70– 75°C; красное дерево 50–60°C или 70–75°C в зависимости от породы. Продолжительность обработки выбирается в зависимости от размеров ванчеса.
1.3. Строгание шпона, применяемое оборудование и расчет его производительности
Процесс строгания шпона отличается от процесса лущения только траекторией движения ножа — возвратнопоступательной. Существует два основных способа строгания: вертикальный и горизонтальный (рис. 3). Основным режущим инструментом режима строгания является нож, а для предотвращения образования трещин применяется прижимная линейка. Основными параметрами режима строгания являются угол заточки ножа (β = 16–17°) и степень обжима Δ.
При изготовлении строганого шпона применяются горизонтальные и вертикальные шпонострогальные станки.
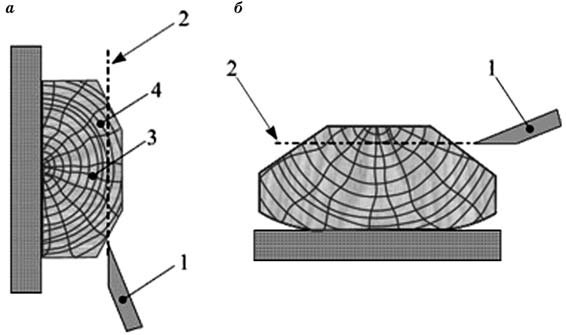
Рис. 3 Способы строгания: а — вертикальный; б — горизонтальный; 1 — нож; 2 — траектория строгания; 3 — сердцевинные лучи; 4 — годичные слои.
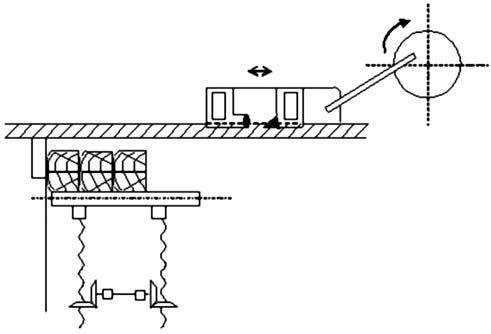
Рис. 4 Схема горизонтального шпонострогального станка
В горизонтальных станках суппорт перемещается по горизонтальным направляющим за счет кулисного механизма (рис. 4).
Ванчесы устанавливаются на подъемном столе в количестве до четырех. После срезания слоя древесины стол поднимается каждый раз на шаг, равный толщине шпона. Станки этой конструкции имеют следующие преимущества: хорошее базирование ванчесов, высокая производительность за счет установки нескольких ванчесов и одновременного их строгания. Их недостатком является трудность удаления шпона из зоны резания, что требует применения специальных выносных устройств. Более прост отбор шпона в вертикальных шпонострогальных станках (см. рис. 5). Заготовка в этих станках закрепляется в вертикальных направляющих, совершающих возвратно-поступательное движение. Суппорт перемещается после каждого движения на величину, равную толщине шпона. Производительность шпонострогальных станков П, м2/час, определяется по формуле
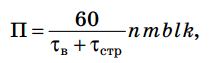
где τв — продолжительность установки ванчеса, мин; τстр — время строгания, мин; n — количество одновременно строгаемых ванчесов; m — количество листов, получаемых из одного ванчеса; b, l — соответственно ширина и длина листов, м; k — коэффициент использования рабочего времени.
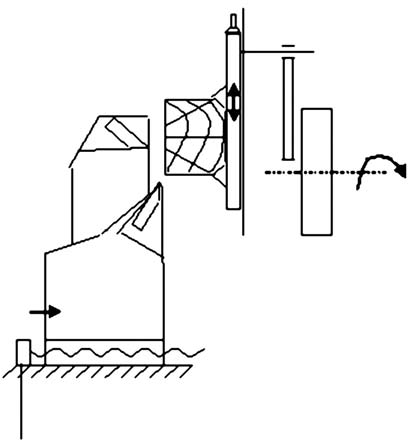
Рис. 5 Схема вертикального шпонострогального станка
Производительность горизонтальных шпонострогальных станков составляет 400–700 м2/час, вертикальных — 1400–1500 м2/час.
1.4. Сушка, сортировка, обрезка и упаковка шпона. Выход строганого шпона
Обработка шпона производится с учетом кнольности. Кноль — пачка листов шпона, срезанного из одного и того же ванчеса, одной текстуры и качества.
Сушка шпона обычно производится в сетчатых сушилках, т. е. сетка натянута на ролики. Роликовые сушилки не применяются из-за малого коэффициента их загрузки. Строганый шпон сушится при температуре 120°C. После сушки производится обрезка с четырех сторон на гильотиновых ножницах. После обрезки сортировка производится по кнолям.
Пачка кнолей не менее 10 штук обвязывается шпагатом в двух местах.
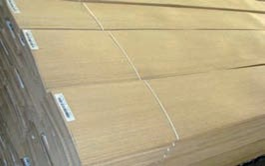
Пачка укладывается в пакеты, оборачивается слоями полиэтиленовой пленки и обвязывается стальной лентой. На каждой пачке ставится этикетка с указанием породы, сорта и стандарта. Учет продукции производится в м2. Расход древесины при изготовлении 1000 м2 строганого шпона (выход шпона) составляет для дуба 1,9 м3, для ясеня и красного дерева 2,1 м3.
Просмотров: 473
ШПОНОСТРОГАЛЬНЫЙ СТАНОК — это… Что такое ШПОНОСТРОГАЛЬНЫЙ СТАНОК?
- ШПОНОСТРОГАЛЬНЫЙ СТАНОК
специализир. (используется преим. в производстве фанеры) дереворежущий станок для получения способом строгания листовой стружки — полуфабриката из древесины ценных пород — строганого шпона. В горизонтальном Ш. с. (см. рис.)вончесы закрепляются нa столе. Режущий инструмент (нож и прчжимная линейка), закрепл. в суппорте, совершает возвратно-поступат. движение от кривошипно-ползунаого или реечного механизма. При каждом рабочем ходе суппорта нож срезает с ванчесов поперечные стружки (шпон) пост. толщины. Ванчесы подаются на толщину шпона (вверх) с помощью спец. механизма. Длина ножа (макс, длина ванчесов) — 3100 — 5500 мм, Макс. ширина блока ванчесов — 800 — 1200 мм, диапазон толщин шпона — 0,025 — 6 мм. За рубежом распространены Ш. с. вертик. компоновки.
Схема горизонтального шпонострогального станка: 1 — стол; 2 — заготовки; 3 — суппорт; 4 — прижимная линейка; 5 — нож; 6 — кулачок; 7 — храповой механизм; 8 — зубчатая передача; 9 — винтовые передачи
Большой энциклопедический политехнический словарь. 2004.
- ШПОНКА
- ШПОНОЧНАЯ ПРОТЯЖКА
Смотреть что такое «ШПОНОСТРОГАЛЬНЫЙ СТАНОК» в других словарях:
шпонострогальный станок — Ндп. фанерострогальный станок Станок, предназначенный для получения шпона из бруса или ванчеса. [ГОСТ 15814 70] Недопустимые, нерекомендуемые фанерострогальный станок Тематики оборуд. для производства слоистой древесины … Справочник технического переводчика
способ изготовления строганого шпона и станок для его осуществления — патент РФ 2090358
Использование: изобретение относится к деревообрабатывающей промышленности и может быть использовано в изготовлении строганого шпона. Сущность изобретения: способ строгания шпона из древесины, имеющей крупные сердцевинные лучи, усовершенствуют путем изменения направления строгания относительно сердцевинных лучей таким образом, чтобы избежать зон, в которых шпон имеет некачественную поверхность, путем расположения режущих кромок ножей в плоскостях, наименьший угол между которыми равняется 84y 0,897 x + 2,2
/Плахов В. H. Производство строганого шпона. М. Лесная промышленность, 1975/. Из уравнения следует, что граница качественного шпона при сгорании против сердцевинных лучей очерчена прямой линией, проходящей через сердцевинный луч, угол наклона которого к плоскости резания в поперечном направлении составляет 42o. При угле встречи между поперечным направлением строгания и сердцевинными лучами менее 42o, даже при правильной подготовке и установке ножа, получить дубовый шпон с шероховатостью поверхности Rm
,
где
Hc величена перемещения стола 6;
Hш толщина срезаемых листов шпона 14. После включения подачи происходит перемещение суппорта 3 в сторону заготовки 11. Режущие кромки 16 ножей 15 срезают по пластям 12 листы шпона 14, которые под собственным весом опускаются вниз и ложатся на тележку 13. В конце холостого хода суппорта 3 датчик 17 подает сигнал на опускание стола 6 на величину, соответствующую толщине срезаемых листов шпона 14. Цикл повторяется. Строгание продолжается до тех пор, пока заготовка 11 не приобретет форму сектора. После этого подачу отключают, стол 6 поднимают вверх и устанавливают ролики 5. Затем стол 6 опускают вниз. Когда пласти 12 заготовки 11 коснутся роликов 5, зажимы 10 разводятся, и заготовку 11, имеющую форму сектора, удаляют из зон резания и подают на следующий станок, у которого кромки 16 ножей 15 расположены углом назад относительно направления рабочего хода. Конструкция и порядок на этом станке идентичны описанному станку.
ФОРМУЛА ИЗОБРЕТЕНИЯ
1. Способ изготовления строганого шпона путем формирования на кряже двух пластей с последующим срезанием за рабочий ход в продольно-поперечном направлении листов шпона, отличающийся тем, что пласти на кряже формируют в плоскостях с наименьшим углом между ними 84o, листы шпона срезают за рабочий ход по двум пластям, при этом срезание в поперечном направлении на заготовке осуществляют от центра к периферии, а отструга, имеющего форму сектора, в обратном направлении. 2. Шпонострогальный станок, содержащий станину, суппорт с установленными ножами, перемещающийся стол и привод, отличающийся тем, что режущие кромки ножей расположены под углом в двух плоскостях, вперед или назад относительно рабочего хода, с наименьшим углом между ними 84o.Ножи и прижимные линейки шпонострогальных станков
Нож — это режущий инструмент в виде пластины с вырезами для крепежных элементов или без них. Лезвие ножа (рис. 1а,б) образовано гранью (фаской), расположенной под углом заточки к плоскости ножа. Вырезы под болты на тыльной части пластины идут не перпендикулярно кромке, а под некоторым углом (5… 10°) к ней, что обусловлено наклонным расположением суппорта шпонострогального станка на направляющих. Длина ножа определяет наибольший размер строгаемого шпона по длине и достигает 5500 мм; ширина ножей 150… 265 мм; толщина 3 ..22 (обычно 15) мм. Толстые ножи изготовляют из двухслойной стали (компаунд): рабочая часть—из легированной стали 85ВФ; основание — из мягкой углеродистой стали 10. Толщина рабочей части составляет от 1/4 до 1/3 толщины ножа, а ширина— от 1/3 до 1/2 ширины ножа. Твердость режущей части ножа после термообработки должна быть в пределах HRC 54… 60.
Прижимные линейки станков для строгания шпона имеют вид пластины с рабочей кромкой (рис. 1в) либо бруса с выступающим ребром (рис. 1г). Изготовляют их из углеродистой стали.
Детали конструкции инструментов определяются устройством механизма резания шпонострогального станка той или иной конкретной модели.
К точности, качеству изготовления и подготовке к работе ножей и прижимных линеек предъявляют повышенные требования, так как ими во многом определяются качество получаемого шпона. Рабочие поверхности должны иметь ровную и гладкую чисто-шлифованную поверхность без царапин и рисок. На них не допускаются раковины, вмятины, трещины и прочие дефекты. Лезвие ножа и рабочая кромка линейки должны быть строго прямолинейными (допускается отклонение не более 0,05 мм на 1 м длины). Выполнение этих требований возможно только путем тщательной заточки.
Только с помощью качественных инструментов можно получить шпон дуба, сосны, ясеня, берёзы и других пород, соответствующий требованиям ГОСТ.
Рис. 1. Конструкции ножей и прижимных линеек шпонострогальных станков:
а — нож к станку ФММ-31О0 толстый, б — то же, тонкий, в — поперечное сечение линейки к станку TH-35. г — то же к станку ФММ-310О
Шпонострогальный станок
О П-Й- (!—А—И—И Е
ИЗОБРЕТЕНИЯ
Союз Соеетскик
Социалистических
Реслублик
729052
К АВТОРСКОМУ СВИДЕТЕЛЬСТВУ (61) Дополнительное к авт. свид-ву (22) Заявлено 070878 (21) 2654946/29-15 (51)М. Кл.2 с присоединением заявки ¹â€”
В 27 L 5/00
Государственный комитет
СССР по делам изобретений и открытий (23) Приоритет
Опубликовано 25.04.80. Бюллетень ¹15
Дата опубликования описания 280430 (53) УДК674.056 Ф
:621.912.252 (088. 8) (72) Автор изобретени я
И.И. Михеев (71) Заявитель
Брянский технологический институт (54 ) ШПОНОСТРОГАЛЬНЫИ СТАНОК
Изобретение относится к деревообрабатывающей промышленности, в частности к производству строганого шпона. 5
Известно устройство для строгания шпона, включающее станину, подвижный стол, суппорт и привод- (1) .
Известен также шпонострогальный станок, включающий станину, стол с узлами крепления ванчесов, механизм резания и привод (2).
Однако эти устройства отличаются высокими динамическими нагрузками .
Цель изобретения — снижение динамических нагрузок шпонострогального
15 станка.
Это достигается тем, что стол выполнен в виде пустотелого кольца, внутри которого по радиусам размещены узлы крепления, причем каждый узел имеет подвижную плиту, опорную и прижимную стоЯки, одни концы которых смонтированы на подвижной плите, а другие пропущены через верхнюю стен-25 ку кольца, при этом прижимная стойка оснащена механизмом перемещения, смонтированным на подвижной плите, а механизм резания снабжен узлом скнхронного опускания, который выполнен в виде горизонтальной балки с винтовыми парами и зубчатым блоком, На фиг. 1 изображена схема шпонострогального станка; на фиг. 2 — то же, вид сверху.
Шпонострогальный станок включает станину 1, стол 2 с узлами 3 крепления ванчесов 4. Над столом 2 смонти» рован механизм 5 резания, а внутри станины 1 размещен привод 6. Стол 2 выполнен в виде пустотелого кольца 7, поперечное сечение которого имеет прямоугольную форму, причем нижняя стенка 8 охвачена зубчатым венцом 9, который соединен с приводной шестерней 10, а верхняя стенка 11 выполняет функции стола 2 и имеет отверстия 12, через которые пропущены опорные 13 и прижимные 14 стойки.
Внутри пустотелого кольца 7 по радиусам размещены узлы 3 крепления, причем каждый узел имеет подвижную плиту 15, на которой вертикально смонтированы опорная 13 и прижимная 14 стойки, при этом последняя снабжена механизмом 16 перемещения, который смонтирован на подвижной плите 15.
Механизм 5 резания снабжен. узлами ускоренного возврата и синхронного
729052 опускания 18, который выполнен в виде горизонтальной балки 19 с винтовыми парами 20 и зубчатым блоком 21, связанным с приводом б.
Работа шпонострогального станка осуществляется следующим образом, Ванчесы 4 загружают на стол 2 напротив узлов 3 крепления и фиксируют с помощью опорных 13 и прижимных 14 стоек.
После заполнения рабочей поверхнос-10 ти стола 2 ванчесами 4 подводят механизм 5 резания, включают узел 18 синхронного опускания и привод б, который через приводную шестерню 10 и зубчатый венец 9 вращает стол 2, в результате чего производится процесс строгания ванчесов 4 и получение шпона требуемой толщины.. формула из обрете ни я 20
Шпонострогальный .станок, включающий станину, стол с узлами крепления ванчесов, механизм резания и привод, отличающийся тем, что, с целью снижения динамических нагрузок, стол выполнен в виде пустотелого кольца; внутри которого по радиусам размещены узлы крепления, причем каждый узел имеет подвижную плиту, опорную и прижимную стойки, одни концы которых смонтированы на подвижной плите, а другие пропущены через верхнюю стенку кольца, при этом прижимная стойка оснащена.механизмом перемещения, смонтированным на подвижной плите, а механизм резания снабжен узлом синхронного опускания, который выполнен в виде горизонтальной балки с винтовыми парами и зубчатым блоком.
Источники информации, принятые во внимание при экспертизе
1. Авторское свидетельство СССР
9 329011,кл, В 27 L 5/00, 1972, 2. Авторское свидетельство СССР
9 б29069, кл. В 27 L 5/00, 3978 (прототип) .
729052
Составитель А. Сафонов
Техред X,Кастелевич Корректор H. Стец
Редактор П. Горькова
Закаэ 1886/16
Тирам 559 Подписное
ЦНИИПИ Государственного комитета СССР по делам иэобретений и открытий
113035, Москва, Ж-35, Раушская наб., д. 4/5
Филиал ППП П
Патент, r. Уагород, ул. Проектная, 4
I !




Технология строгания и обрезки шпона
Резание шпона ведется плоским ножом, а для получения качественного шпона резание необходимо вести с обжимом прижимной линейкой при оптимальной степени обжима, приведенной в табл.1
Таблица 1. Степень обжима при строгании
Как видно из табл.1, для основных толщин шпона величина степени обжима устанавливается в пределах 5… 20%. Для толщин более 1 мм степень обжима следует увеличивать, однако не выше 30…35%, так как чрезмерный обжим приводит к раздавливанию структурных элементов древесины. Шпон получается шероховатым, дряблым и непрочным.
Прижимную линейку относительно ножа устанавливают по координатам х и у, которые вычисляют по специальным формулам и по табл.2.
Таблица 2. Значения оптимальных координат x и у, мм
Качественный шпон получается лишь при правильном выборе направления строгания по отношению к сердцевинным лучам и годичным слоям древесины кряжа. Рассмотрим процесс строгания неразделенного кряжа без перекантовки, представленный на рис. 1.
Рис. 1. Схема строгания кряжа без перекантовки:
1 — нож, 2 — кряж
При строгании нож 1 совершает главное движение резания Dг в плоскости Rг, параллельной горизонтальной оси кряжа хх, и движение подачи Ds, по оси уу. Для каждой текущей точки n соответственно в I, II, III и IV четвертях сечения кряжа 2 процесс резания кроме основных параметров v, δ, β, α, ρ, Δ будет характеризоваться углами перерезания сердцевинных лучей φл и годичных слоев φс, величина которых по мере строгания кряжа изменяется.
В результате проведенных опытов по выявлению изменчивости шероховатости поверхности листов строганого шпона из различных зон сечения кряжа получены графики зависимости шероховатости шпона при строганин без разделки и перекантовки кряжа (рис. 2).
Рис. 2. Зависимость шероховатости поверхности шпона от расположения листов шпона в кряже:
а -для I и II четвертей сечения кряжа, б — для III и IV четвертей
Анализ полученных результатов показывает, что шероховатость шпона при резании от периферии кряжа к центру (I четверть) сначала увеличивается и достигает максимального значения 220…280 мкм на расстоянии примерно 2/3 от центра кряжа (φл= 15… 45°), а затем резко уменьшается и достигает минимума 50… 80 мкм у периферии (φл=180°). При строгании III и IV четверти и движении ножа от периферии кряжа к центру вначале шпон имеет шероховатость 50 …80 мкм, а затем 270… 320 мкм.
Усредненные значения шероховатости лицевой поверхности шпона толщиной 0,8 мм при Δ=10% для различных четвертей кряжа (рис. 3) при строгании кряжевым способом показывают, что более высокого качества шпон получают из II и III четвертей сечения кряжа, а из I и IV четверетей часть шпона дуба не соответсвует ГОСТу, а из лиственницы имеет пониженную шероховатость. Понижение качества шпона из I и IV частей, т. е. при строгании с острыми углами перерезания сердцевинных лучей и тупыми углами перерезания годичных слоев для пород с ярко выраженными сердцевинными лучами, обусловлено появлением сколов древесины в виде вырывов в местах выхода сердцевинных лучей на поверхность листа.
Рис.3. Шероховатость поверхности строганого шпона толщиной 0,8 мм при строганин с обжимом Δ=10% для различных сечений кряжа
С учетом приведенных выше положений необходимо строгание заготовок вести таким образом, чтобы угол перерезания сердцевинных лучей был тупым или близким к нему, что возможно лишь при строгании от центра кряжа к периферии с перекантовкой заготовок (ванчесов) после разработки половины заготовки.
Рекомендуемые способы раскроя кроме кряжевого и тупокантно-брусьевого предусматривают данное условие, поэтому кряжевой и тупокантно-брусьевой способы необходимо применять в минимальных объемах для сырья минимальных диаметров.
Нормативы расхода сырья в производстве строганого шпона устанавливаются на 1000 м2 шпона (для шпона дуба нормативы приведены в табл. 3). Зависит норма расхода от качества исходного сырья, способа раскроя кряжей на заготовки, толщины строгаемого шпона, совершенства технологии его производства и состояния используемого оборудования.
Таблица 3. Нормативы расхода дуба на 1000 м2 строганого шпона толщиной 0,8 мм
Примечание. Ко II группе дубового сырья относится сырье, заготавливаемое в Закарпатской, Винницкой. Ивано-Франковской, Крымской, Львовской, Одесской, Ровенской, Тернопольской, Черкасской. Черновицкой, Хмельницкой областях, а также Молдавской, Татарской и Башкирской, к III группе — сырье, заготавливаемое в Краснодарском к Ставропольском краях, остальное сырье относится к I группе.
Норму расхода сырья на производство строганого шпона других толщин получают путем умножения табличных значений на поправочный коэффициент Кт (табл.4).
Таблица 4. Поправочные коэффициенты на толщину шпона
Норму расхода сырья определяют по среднему диаметру кряжей и табличным нормативам путем умножения их на поправочный коэффициент в зависимости от толщины строгаемого шпона.
Для строгания заготовки в виде ванчесов или брусьев после окорки устанавливают на стол шпонострогальных станков (рис.3) и крепят так, чтобы строгание осуществлялось в направлении Dг, обеспечивающем наилучшее качество поверхности шпона.
Рис.3. Схема крепления ванчесов на столе шпонострогального станка:
а) в начале строгания, б) после перекантовки;
1 – стол станка, 2 – упорная стенка, 3 – ванчесы, 4,5 – крючья, 6 – упорная прокладка, 7 – вторая половина ванчеса, 8 — отструг
Установленные на столе 1 ванчесы 3 крепят крючьями 5 и 4 так, чтобы предотвратить выпучивание ванчесов при строгании. Крайний ванчес упирается в стенку 2, а на последний действует крюк 4, который прижимается винтовым или гидравлическим устройством. Между стенкой 2 и первым ванчесом укладывают упорную прокладку 6.
Перед началом строгания стол устанавливают на такую высоту, чтобы лезвие ножа при холостом движении суппорта на 2… 3 мм не доходило до ванчесов, затем станочник включает в работу храповой механизм подачи.
Строгание начинается с выравнивания ванчесов под одну плоскость и сопровождается сострагиванием сначала мелких, а затем более крупных срезков. Срезки по мере их накопления в полости суппорта выбираются вручную или механизированным устройством в момент подхода суппорта к переднему мертвому положению и сбрасываются в люк дробилки.
Полноформатные листы шпона выносятся из полости суппорта и укладываются в кноли, количество которых соответствует количеству ванчесов на столе станка. Продолжительность одного рабочего хода составляет 1,5 …2 с, в течение которых и совершается процесс выноса и укладки листов шпона в кноли.
При выносе и укладке листов шпона в кноли станочник следит за подходом ножа к крюкам. Как только нож приблизится к ним на расстояние 25… 30 мм, станочник останавливает станок для перемещения крюков вниз или для перекантовки ванчесов.
После перекантовки ванчесы крепят так (рис. 3, б), чтобы верхняя кромка крюка 4 находилась в зоне отструга 8, толщина которого 25… 40 мм. Конструкция станков предусматривает винтовое перемещение зажимных крюков, а на ряде предприятий ручное винтовое крепление заменено гидравлическим, состоящим из гидронасоса, системы трубопроводов и гидроцилиндров. Применение гидрозажима облегчает труд станочников и повышает производительность станка. При строгании первых листов проверяют их толщину микрометром в трех точках по длине. При ее соответствии требованиям технологической инструкции строгание продолжают. При этом необходимо обеспечить раскладку листов шпона в последовательности, соответствующей их срезанию по каждой заготовке. При появлении дефектов строгание прекращают до их устранения.
После сушки шпон обрезают до стандартных размеров или прирезают до размеров по согласованию с потребителем на ножницах гильотинного типа.
Одновременно обрезают по 5… 10 листов одного вида. При обрезке вырезают дефектные места, не допускаемые по ГОСТу, а при прирезке эти места (зоны) допускается очерчивать, но площадь этих зон исключают из объемов. При обрезке необходимо сохранять кноль. Косина обрезного шпона не должна превышать величины предельных отклонений по ширине листа.