Миниатюрный ленточный-отрезной станок из подручных материалов


Приветствую всех любителей помастерить, сегодня мы рассмотрим, как из подручных материалов сделать ленточный отрезной станок. При помощи такой машины можно быстро нарезать листовой материал и не только. Машина получилась вполне работоспособной, только плохо сделана отрезная лента, ее автор изготовил из консервной банки, так что долго таким полотном не порежешь. В качестве основы автор использует моторчик на 12В, для такой самоделки отлично подойдет мотор 775, но нужно устанавливать регулятор оборотов. Все прочие детали достать будет легко, да и инструментов для изготовления понадобится мало. Если вас заинтересовал проект, предлагаю изучить его более детально!
Материалы и инструменты, которые использовал автор:
Список материалов:
— фанера;
— железный стержень для оси;
— два колеса от игрушечной машинки;
— консервная банка;
— винты с гайками;
— двигатель 775 или подобный на 12В;
— суперклей;
— гнездо для подключения блока питания;
— включатель.

Список инструментов:
— лобзик;
— ножовка;
— дрель;
— ножницы;
— паяльник;
— плоскогубцы;
— клеевой пистолет.
Процесс изготовления самоделки:
Шаг первый. Сборка основы и установка составляющих
Для изготовления рамы автор использовал фанеру, вырезаем из нее детали, как у автора на фото. Конечно, в идеале фанера должна быть толстой, чтобы все можно было собрать на саморезах, или же можно использовать доски. Автор просто склеивает детали из фанеры суперклеем.
В верхней части стойки нужно будет установить ведомое колесо, для него понадобится подыскать железную ось. Под ось сверлим отверстие в колесе, а ось вклеиваем в отверстие, просверленное в стойке. Двигатель устанавливаем в нижней части, сверлим отверстия и прикручиваем моторчик винтиками. На валу двигателя находится шестерня, под нее сверлим отверстие в колесе и приклеиваем колесо к шестерне. Вот и все, станок готов, остается сделать отрезное полотно.
Отрезное полотно автор решил сделать из консервной банки, но важно понимать, что такой металл не прочный и резать машиной можно разве что картон и другой не слишком твердый материал.
Консервную банку режем на полосы, а затем полосы спаиваются, чтобы получить ленту нужной длины. В итоге должно получиться кольцо, на котором нужно нарезать зубчики. Автор нарезает зубчики ножницами, и она у него довольно больших размеров. Лучше делать зубчики маленькими, тогда они не будут гнуться под нагрузками, и полотно сможет резать твердые материалы.
Шаг третий. Завершающие штрихи
В завершении окончательно собираем корпус станка, а также устанавливаем рабочий столик. Именно столик работает в качестве упора для отрезной ленты. Но для долговечной работы лучше прикрутить железный упор.
Чтобы машина не развалилась, автор стянул ее винтами с гайками. Припаиваем к контактам мотора провода, приклеиваем клеевым пистолетом гнездо для подключения блока питания и выключатель. А чтобы станок не ездил по столу от вибраций, приклеиваем к основе куски резины велосипедной камеры.
Самоделка готова, станок вполне неплохо режет листовой материал, но что это конкретно, понять не удалось. Если машину немного доработать, получится вполне неплохая самоделка. На этом проект окончен, надеюсь, вам самоделка понравилась. Удачи и творческих вдохновений, если решите повторить подобное. Не забывайте делиться с нами своими идеями и самоделками!
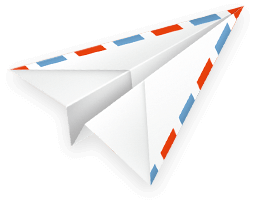
Получайте на почту подборку новых самоделок. Никакого спама, только полезные идеи!
*Заполняя форму вы соглашаетесь на обработку персональных данных
Становитесь автором сайта, публикуйте собственные статьи, описания самоделок с оплатой за текст. Подробнее здесь.usamodelkina.ru
Самодельное заточное приспособление в условиях мастерской
Приветствую, Самоделкины!В данной статье речь пойдет об инструменте, который точно пригодится людям занимающимся деревообработкой. Подобные приспособления конечно имеются в продаже, но цена на них довольно высокая.
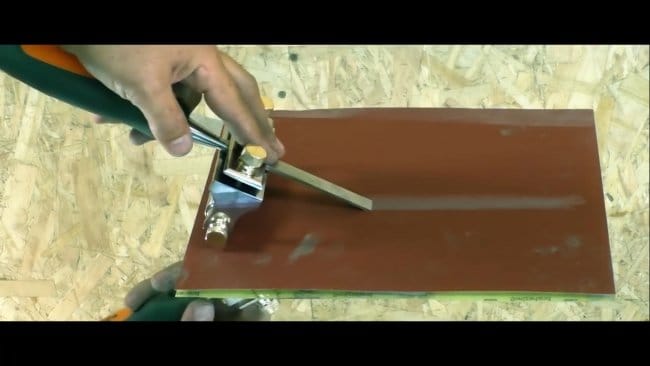
Дальнейшая инструкция взята с YouTube канала «Добрый Мастер». Для начала нам понадобится стальная полоса шириной 40мм.
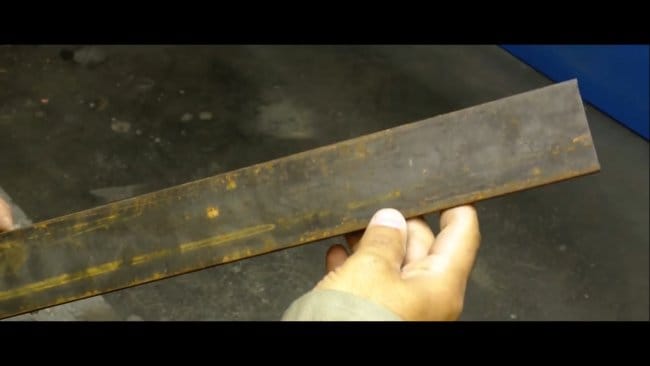
Из данного куска металла получится отличный корпус для будущего инструмента. Первым делом как всегда разметка. Китайский штангенрейсмас станет отличным помощником в этом деле.
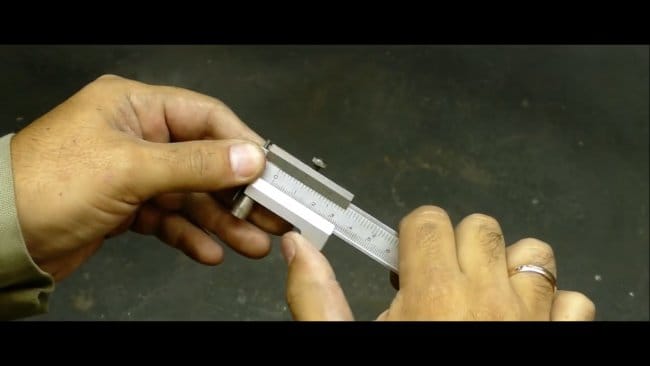
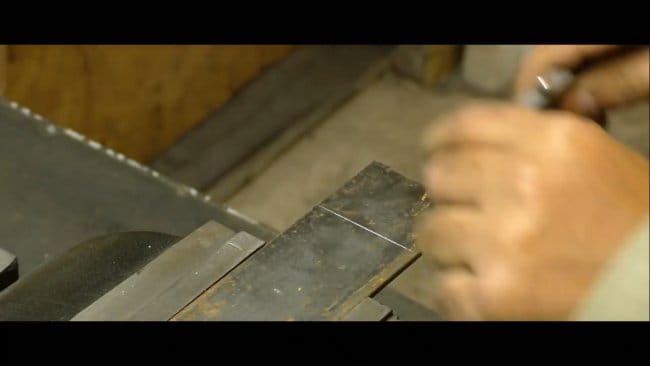
Затем необходимо сделать небольшие пропилы при помощи болгарки.


Это поможет нам согнуть ровный угол в необходимых местах. В дальнейшем место изгиба проварим полуавтоматом. Повторяем операцию еще один раз и можно отрезать лишнее.

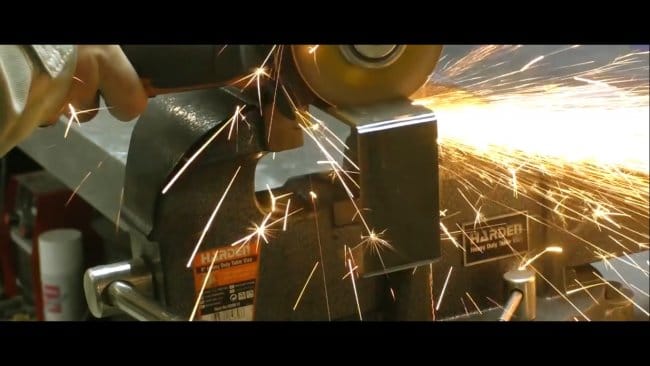
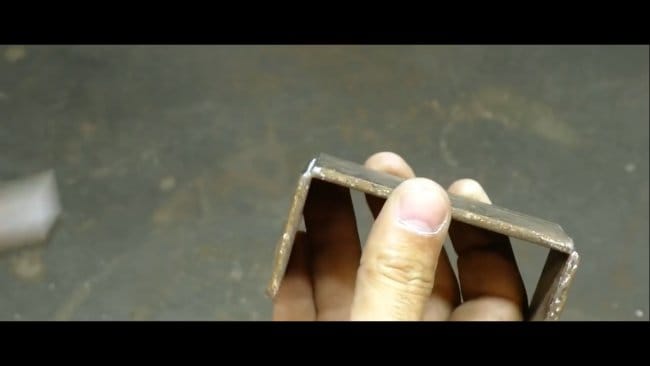
Перед тем, как приступить к сварке, необходимо убедиться, что все углы прямые по 90 градусов. Сделать это проще всего при помощи обыкновенного угольника.
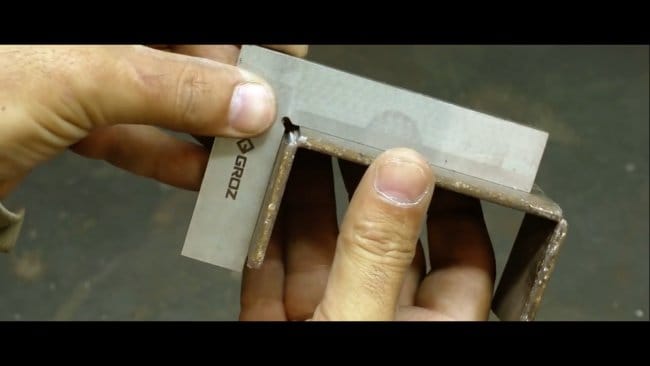
Затем заготовку фиксируем и варим.

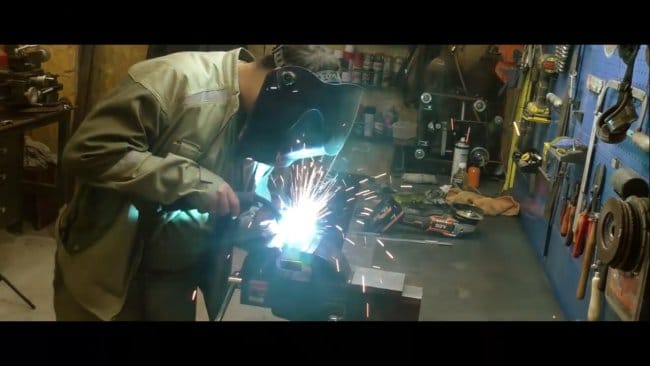
Заготовку можно зажать в обыкновенных тисках, так будет удобней и проще всего. Сварочный шов будет двойной, так мы сохраним прямой угол. Вот, что в итоге получилось на данном этапе:
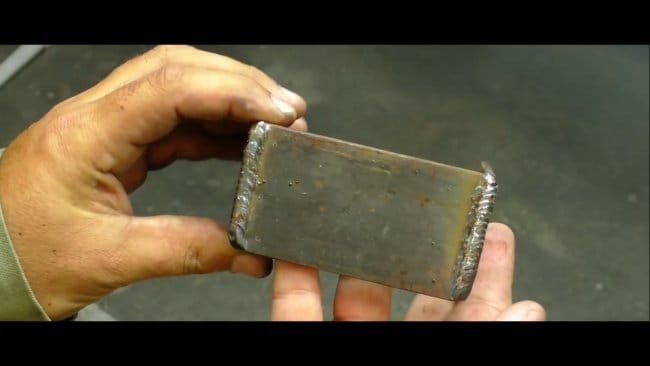

Теперь получившуюся заготовку необходимо обработать. Для этого можно прибегнуть к помощи все той же болгарки, но так как у автора имеется самодельный гриндер, на нем он и решил выполнить данную процедуру периодически охлаждая деталь.
С помощью гриндера эту работу можно выполнить быстрее и качественней. Спустя буквально 5 минут «танцев» возле станка, и мы получаем полностью обработанную деталь с идеальными углами.

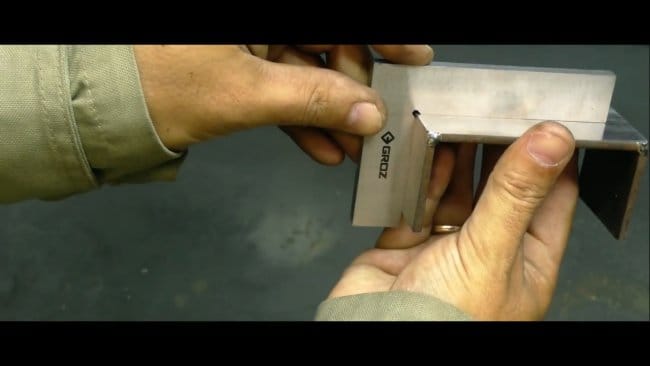
Следующим шагом необходимо произвести разметку, которая поможет определиться с отверстиями.
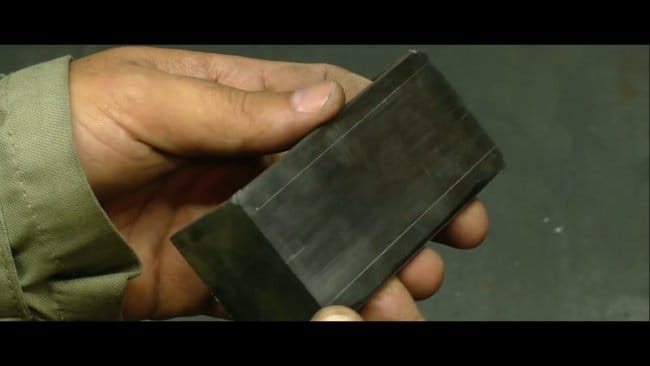

Отверстия должны быть соосными, вал, который будет впоследствии устанавливаться сюда, должен быть полностью параллелен верхней площадке корпуса.
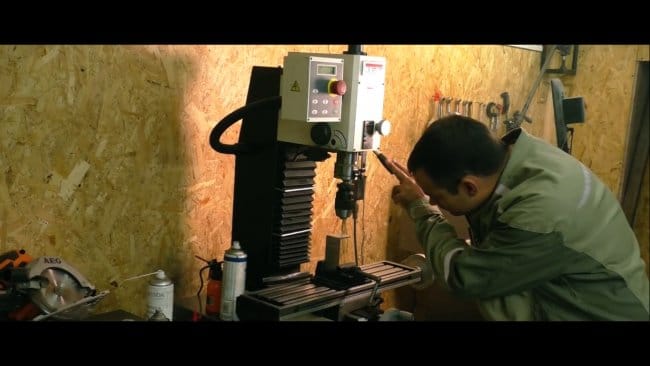

Отверстия просверлены, теперь можно отрезать все лишние части.
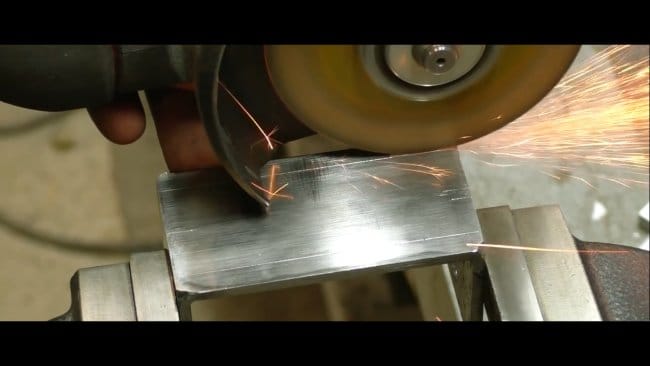
Корпус будущего приспособления можно оставить и таким, а можно еще немножко поработать и тем самым сделать его более красивее. Вот так будет смотреться намного лучше.
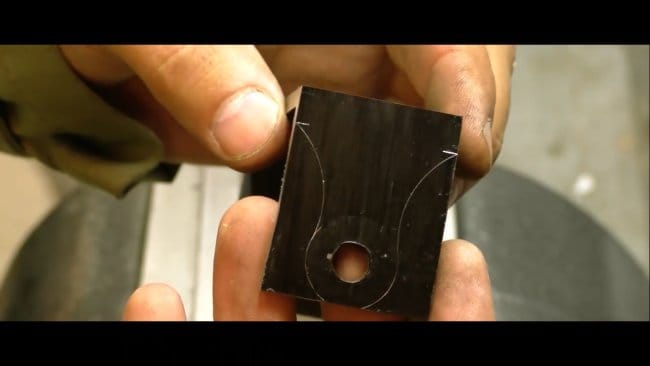
Основную часть металла обрезаем угловой шлифовальной машинкой (УШМ), это один из самых быстрых способов. В этом деле требуется немножко сноровки и подогнать возможно почти до идеала.

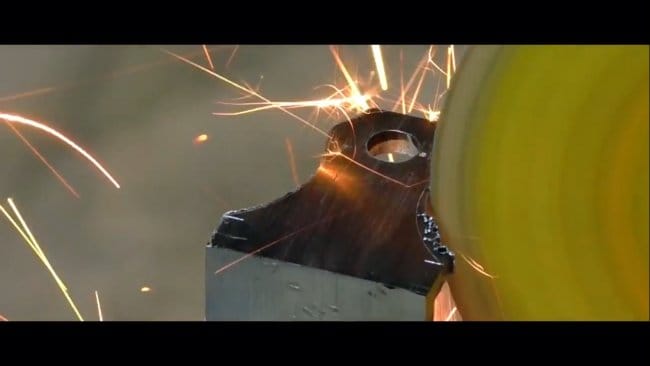
Затем автор пустил в ход бормашину. С ее помощью доведём обработку вплоть до линии разметки.
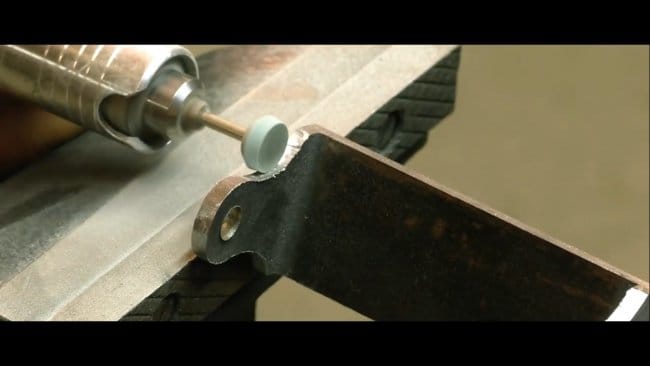
После проделанных манипуляций вот такая деталь у нас получилась.

Из той же полосы шириной 40мм изготовим прижим. Он будет крепиться сверху корпуса и фиксировать режущий инструмент. Прижим необходимо изготовить на 5мм короче корпуса. Также уменьшим и ширину заготовки, и конечно же выровняем стороны на гриндере.
Далее все на том же станке отшлифуем плоские стороны заготовки. При обработке металл нагревается достаточно сильно, поэтому не забываем его своевременно охлаждать.
Поверхность даже после грубой обработки выглядит потрясающе. Далее избавляемся от острых углов с верхней стороны. Их мы просто сточим. Для этого воспользуемся обыкновенной меткой на опорном столике.
Получилось весьма неплохо. В закромах была найдена вот такую вот втулка:

Ее будем использовать в качестве ролика, а ось с эксцентриком выточим на станке. Далее у нас полюбившаяся многим токарка. Протачиваем всю ось в нужный размер, после чего развернем заготовку и сделаем подкладку под один из кулачков токарного патрона. Это поможет нам сместить центр нашей заготовки, а зачем это будет нужно, поймете немного позже.
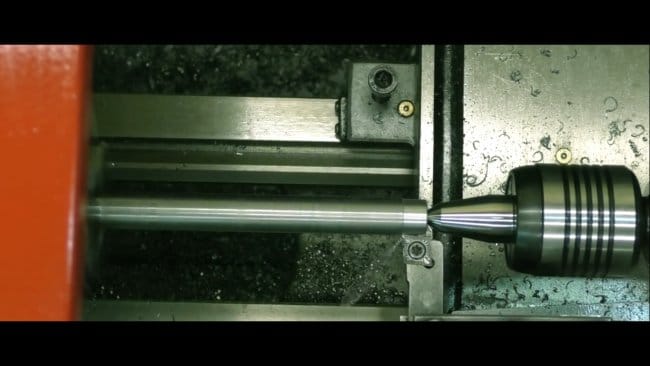

Далее в торцах получившейся заготовки необходимо просверлить отверстия и нарезать резьбу м5.

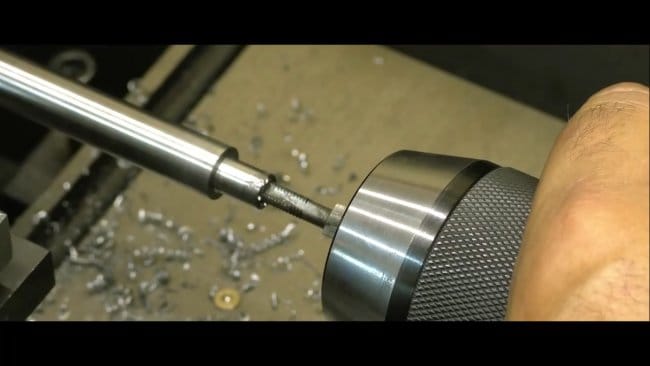
Следующим шагом у нас опять токарная обработка. Необходимо выточить болты для нашего инструмента. Болты будем делать из латуни, они необходимы для фиксации оси с эксцентриком в корпусе инструмента. Всего таких болтов нужно изготовить две штуки.
Теперь остается сделать еще пару болтов. Они нежны для крепления прижима к корпусу. Эти болты будут немного больше предыдущих с резьбой 6мм.

Итак, все необходимые болты и крепления готовы, приступаем к, так сказать, последним штрихам, сверлим отверстие и нарезаем резьбу м6. Сперва проходим тонким сверлом, а затем уже рассверливаем сверлом с необходимым нам диаметром.
Далее примерка по месту и продолжаем дальше.

Следующим шагом необходимо выточить втулку на ось с эксцентриком.
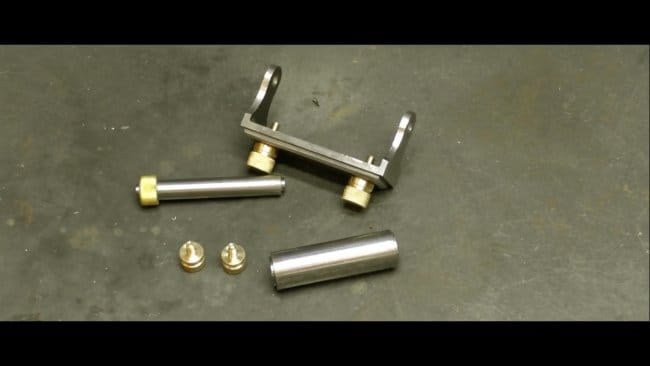
Следующий шаг — полировка готовых деталей.
Такой полировальный круг автор приобрел в Китае. Паста была приобретена в магазине ювелирных инструментов, поэтому ссылки тут не будет.

И вот наконец все детали готовы. Как же здорово блестит латунь после полировки.
Теперь начинаем процесс сборки, он довольно простой и не займет много времени. Главное здесь — это смазать большой ролик маслом.
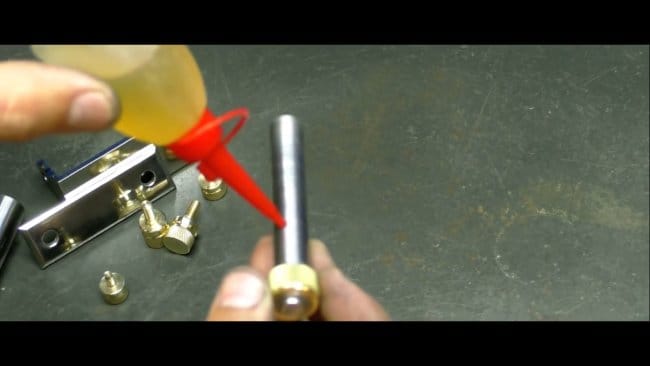

Сборка завершена и перед вами предстает вся конструкция в сборе.

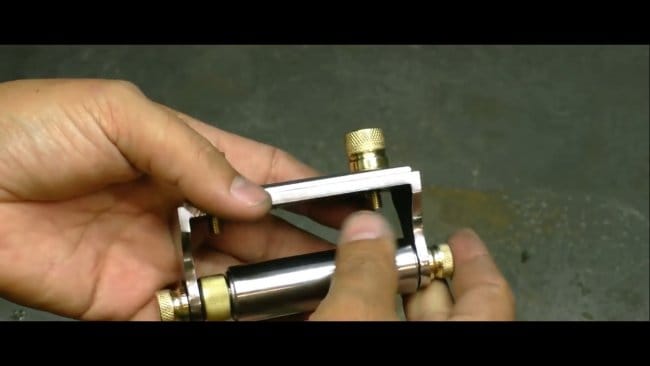
Смотрится такое сочетание металлов весьма не плохо, давайте же приступим к испытаниям получившегося приспособления. Для испытания возьмем дешевую стамеску, ее автор приобрел год тому назад в одном экземпляре.

Стоит отметить, что заточка у нее до сих пор магазинная, то есть никакая. Так давайте же с помощью этого самодельного малыша попробуем довести ее до ума.


Подходящего заточного камня у автора не оказалось, поэтому заточка стамески производилась на стекле с наждачной бумагой. ЭТО ВАЖНО! Ось эксцентрика при первоначальной заточки должна быть смещена вверх.
Возвратно поступательными движениями начинаем производить заточку. Первая бумага с зернистостью 600 грит. После того, как все следы от предыдущей заточки убрали, можно переходить на наждачку с более мелкой зернистостью и так до 2000.


Далее эксцентрик необходимо установить в нижнее положение. Таким образом мы изменяем угол заточки, это позволяет нам получить микро фаску для режущего инструмента.
Здесь достаточно всего нескольких движений и все готово. В итоге заточка получилось бритвенная, что доказывает тест на руке.
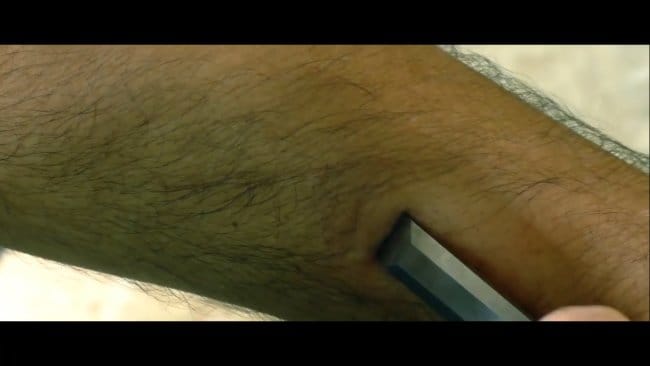

А работать с деревом с этим инструментом, по словам автора, теперь одно удовольствие.


На этом все. Благодарю за внимание. До новых встреч!
Видеоролик автора:
Источник
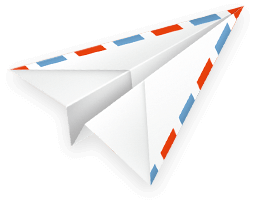
Получайте на почту подборку новых самоделок. Никакого спама, только полезные идеи!
*Заполняя форму вы соглашаетесь на обработку персональных данных
Становитесь автором сайта, публикуйте собственные статьи, описания самоделок с оплатой за текст. Подробнее здесь.usamodelkina.ru
Полезное приспособление, которое пригодится и столяру, и слесарю
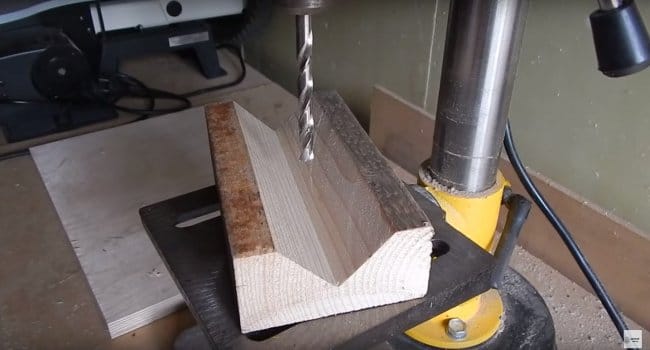
Всем доброго времени. Сегодня автор канала «Дачный умелец» покажет нам, как он сделал простое, но очень полезное приспособление для своей мастерской.
Для изготовления своей самоделки, автор использовал.
МАТЕРИАЛЫ: брус деревянный 100х50;
ИНСТРУМЕНТЫ: пила циркулярная;
Вот и всё, что использовал автор для изготовления данного приспособления.
И так, от бруса автор отрезал, кусок произвольной длины.


После, на циркулярной пиле выставил диск под углом 45 градусов. Затем взял заготовку и сделал в ней пару пропилов.

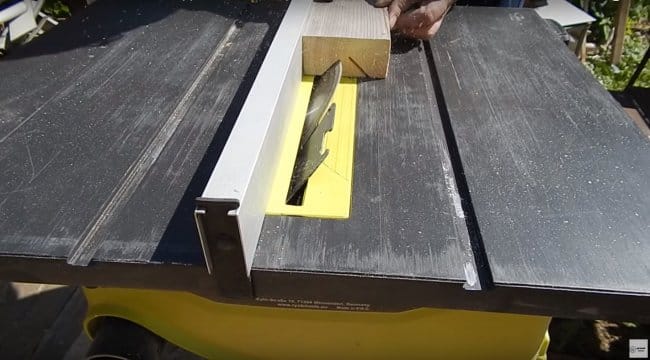
Получилось пока так. Но цель автора, вырезать этот треугольник.

Поэтому он немного поднял диск, и снова прошёл по ранее сделанным пропилам на заготовке.

И так автор делал, до тех пор, пока не добился нужного результата.
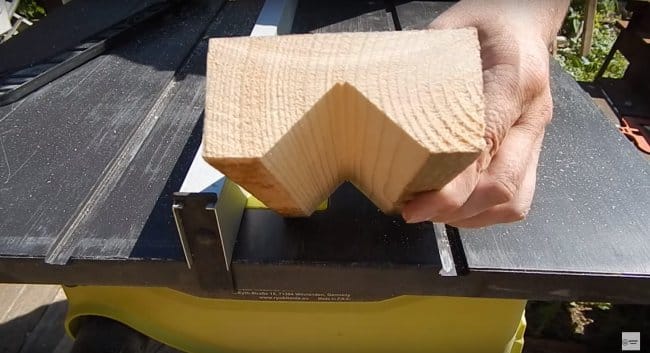
Но вот и всё, самоделка готова.

Настроить её очень просто, достаточно опустить сверло в центр углубления, и немного провернув сверло таким образом, чтобы сверло стало точно по центру углубления.

Ну вот, самоделка настроена и готова к работе. Её можно зафиксировать в таком положении струбциной или просто держать рукой во время работы, как это делает автор.

А работает она так. Допустим вам нужно сделать отверстие в трубе ровно посередине, можно конечно было бы зажать трубу в тисках и сделать отверстие, но в таком случае сверло может уйти немного в сторону, а с данной самоделкой этого не произойдёт, она будет удерживать заготовку точно по центру сверла.

Результат.
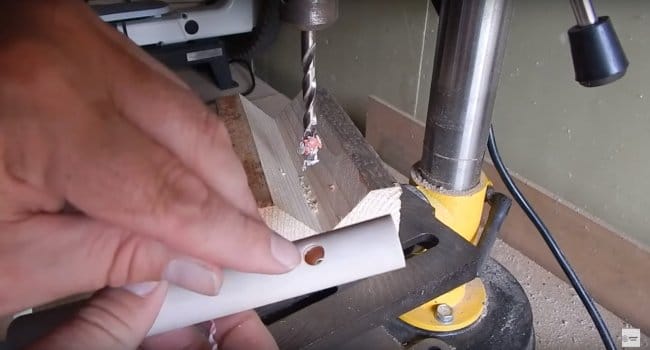
Ещё один пример, вам понадобилось установить шплинт на болт, а для этого в нём нужно сделать отверстие, с данным приспособлением сделать это не составит большого труда.

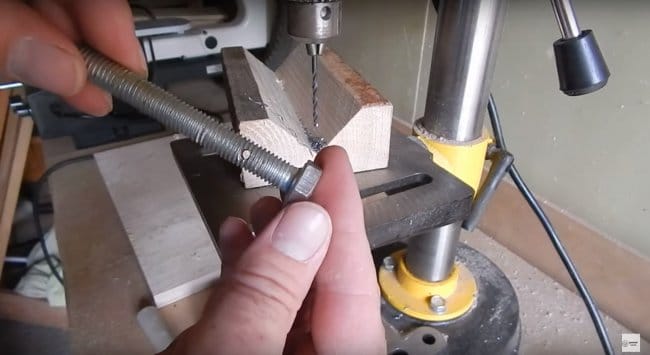
Так же, данную самоделку, можно использовать и в столярном деле. У автора есть круглая заготовка диаметром 10 мм, и часть этой заготовки мастеру нужно сделать диаметром 8 мм.
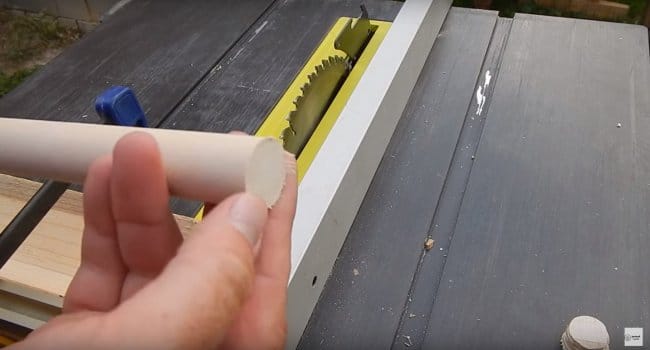
Для этого, он устанавливает приспособление ровно по центру диска, затем в самоделку устанавливает заготовку и регулирует диск таким образом, что бы высота зуба была на 2 мм выше заготовки.

И не спеша круговыми движениями, снимает лишний материал с заготовки.
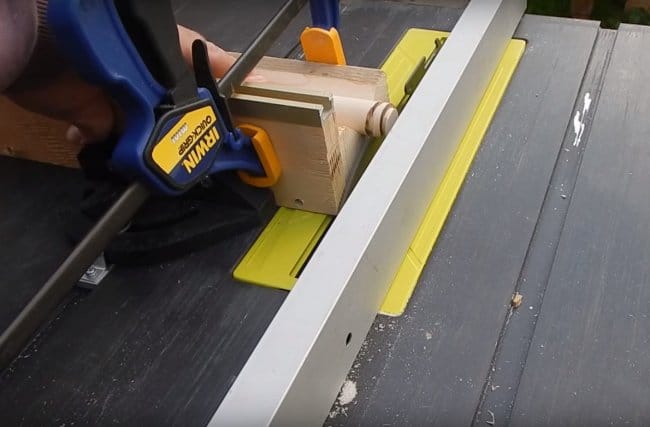
Вот так. Хотелось бы сказать, автору, большое спасибо, за простую, но очень полезную самоделку.

А на этом, у меня всё. Всем спасибо! И до новой встречи!
Источник
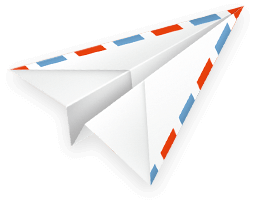
Получайте на почту подборку новых самоделок. Никакого спама, только полезные идеи!
*Заполняя форму вы соглашаетесь на обработку персональных данных
Становитесь автором сайта, публикуйте собственные статьи, описания самоделок с оплатой за текст. Подробнее здесь.usamodelkina.ru
Фуговальный станок (фуганок) своими руками
Здравствуйте, уважаемые читатели и самоделкины!Наверняка многим из Вас хочется иметь в своей мастерской хотя-бы небольшой фуговальный станок.
В данной статье автор YouTube канала «Amazing Woodworking Techniques» расскажет Вам, как он реализовал этот проект достаточно простым способом.
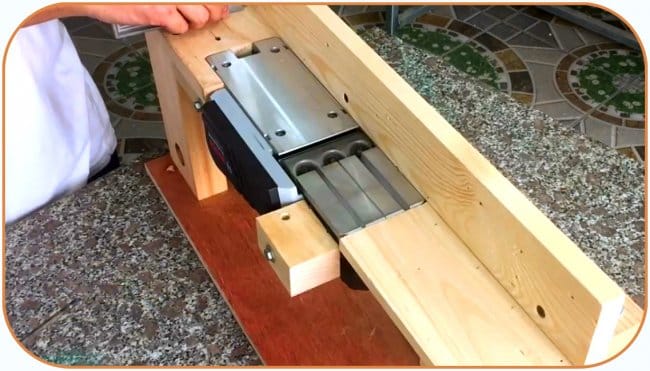
Эта самоделка весьма проста в изготовлении, однако требует высокой точности обработки деталей. Ее достаточно просто изготовить, однако потребуются доски с высоким качеством обработки.
Материалы.
— Сосновая паллетная доска
— Листовая фанера
— Пружина
— Саморезы по дереву, мебельные гайки, винты, гайки, шайбы
— Клей ПВА.
Инструменты, использованные автором.
— Электрический рубанок
— Безопасный толкатель
— Ручной фрезер
— Циркулярная пила
— Шуруповерт
— Сверло с зенковкой
— Угольник, карандаш, линейка, гаечный ключ, отвертка, молоток.
Процесс изготовления.
Первым делом мастер размечает контуры электрического рубанка на сосновой доске.
Также размечаются будущие прорези под рабочую часть, и выемки для корпуса двигателя.
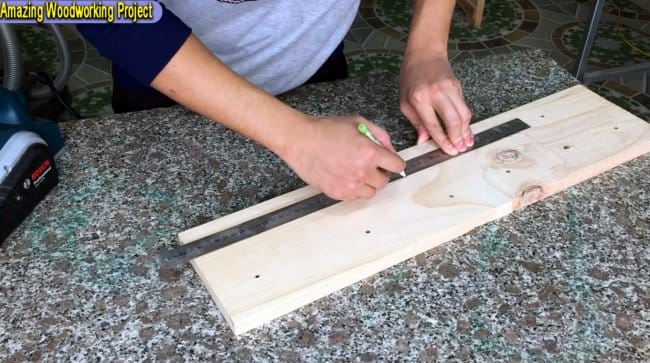
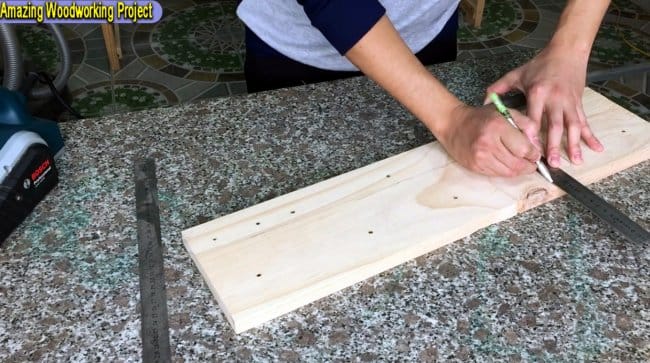
Излишки материала автор срезает на самодельном циркулярном столе с кареткой.
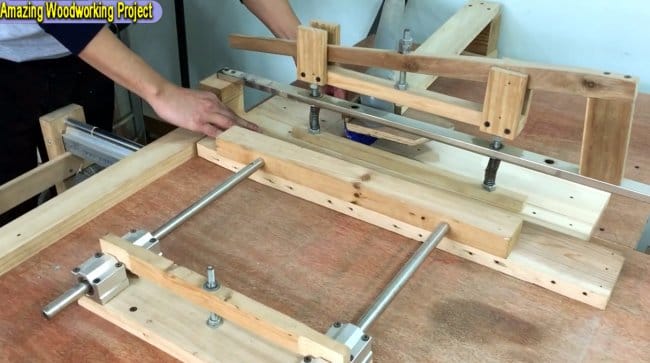
Пазы для корпуса двигателя, и другие технологические выемки он выполняет при помощи фрезерного станка.
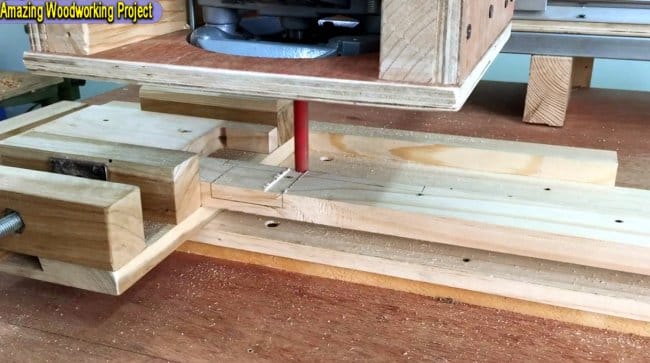

В итоге получается платформа, на которую и садится сам рубанок. Крайне важно, чтобы верхняя часть доски была идеально ровной.


Для крепления инструмента к самому столу, мастер закрепляет его тыльную часть при помощи двух подставок, и болтом, пропущенным сквозь отверстие для рукоятки.
После выравнивания подставок, они прикручиваются к столу саморезами с нижней стороны.
Аналогичным способом крепится и фронтальная часть инструмента, однако в этом случае винт проходит не насквозь, а жестко крепится в отверстии.
Вся полученная конструкция переворачивается в нормальное положение, затем проверяется соосность подошвы и столика при помощи угольника.
Далее потребуется изготовить три подставки, в одной из которых высверливаются сквозные отверстия, и забиваются мебельные гайки.
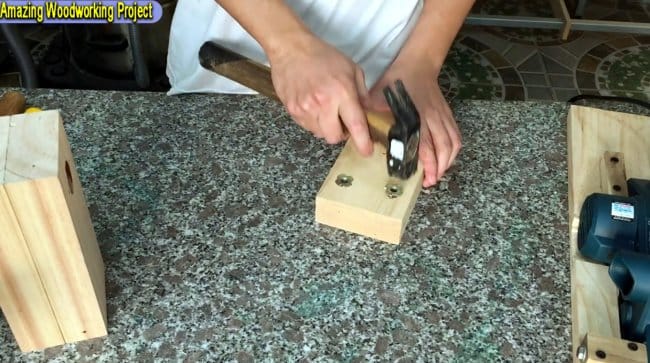
Теперь сам стол можно прикреплять к опорам при помощи длинных саморезов, предварительно просверлив пилотные отверстия, и раззенковав их.
Вся конструкция снова переворачивается, и к ее нижней части прикрепляется основание из листовой фанеры.


Итак, основная конструкция станка весьма проста, и уже готова.

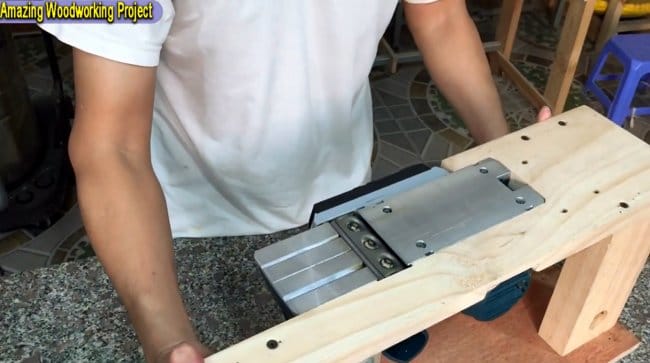
Следующим этапом нужно изготовить небольшую опорную площадку. Ее можно сделать из досок или фанеры подходящей толщины, и скрепить между собой при помощи пары уголков.
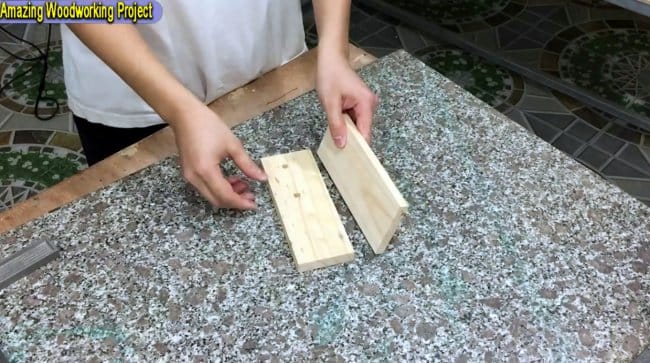
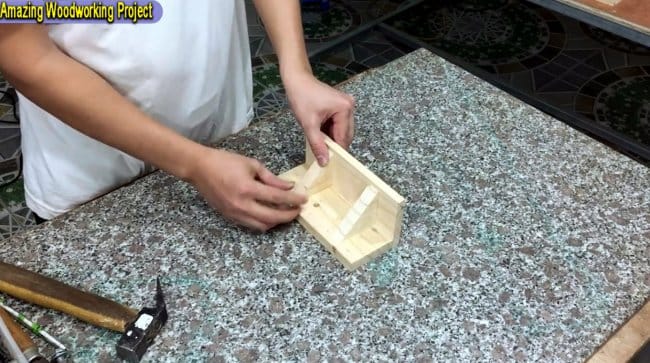
Подпорка прикрепляется к крайней части корпуса, образуя с регулируемой платформой одну плоскость.
За счет отверстий чуть большего диаметра в самой платформе, она имеет возможность регулировки по вертикали, что позволит изменять толщину снимаемого материала.


После выравнивания, и фиксирования болтами, плоскости подошв и подпорки следует проверить при помощи угольника, либо уровня. Это нужно сделать также и по диагоналям.

Пришло время установки бокового параллельного упора. Первой его частью станет сосновый брус. Мастер закрепляет его при помощи барашковых гаек, которые дадут возможность последующей регулировки.
Затем к бруску прикручивается еще одна планка, тоже из выровненной сосновой доски.
Теперь нужно обязательно проверить перпендикулярность плоскости упора относительно подошвы рубанка и самого стола.
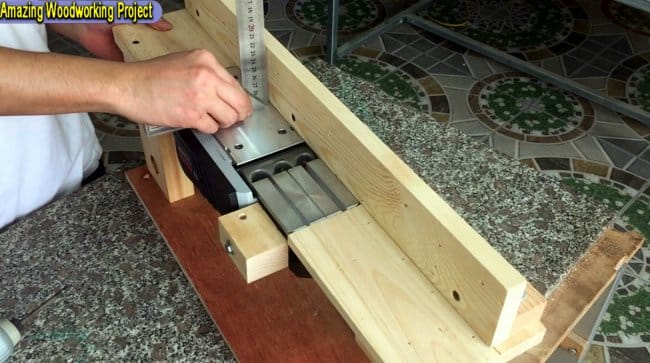
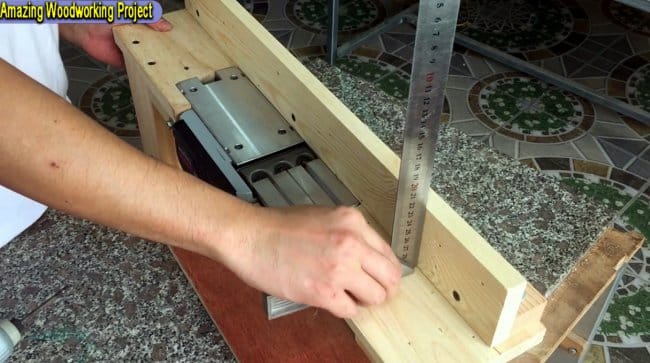
А теперь самый важный момент, это обеспечение безопасной работы. Для этого ко второму отверстию для прижимов прикручивается небольшой деревянный блок.

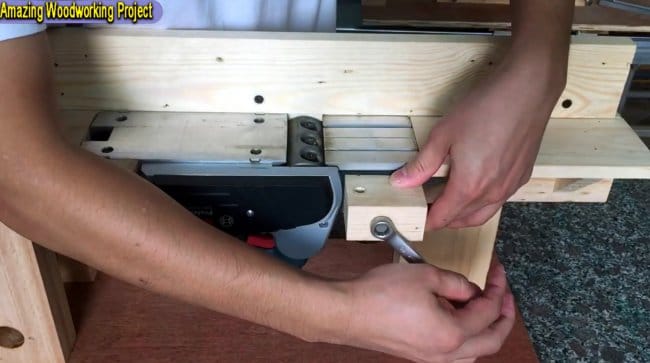
На этот блок устанавливается специальный защитный лепесток, осью для которого станет болт М8, в конце оного просверлено поперечное отверстие для крепления хвостика пружины. Болт жестко прижимается к лепестку, фиксируясь с двух сторон шайбами, и прижимаясь тремя гайками в виде подставки.


Еще одну шайбу мастер подкладывает между гайками и опорным блоком, а затем устанавливает натягивающую пружину.

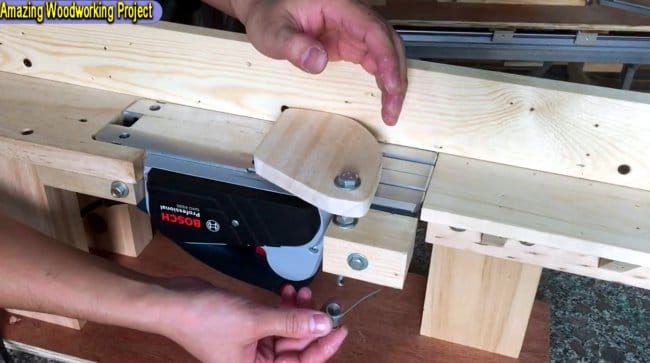
Отрегулировав необходимое усилие пружины, ее второй конец фиксируется саморезом с пресс-шайбой к нижней части блока.
Теперь лепесток будет закрывать рабочие лезвия рубанка в моменты отсутствия заготовок. Вот так работает этот механизм.
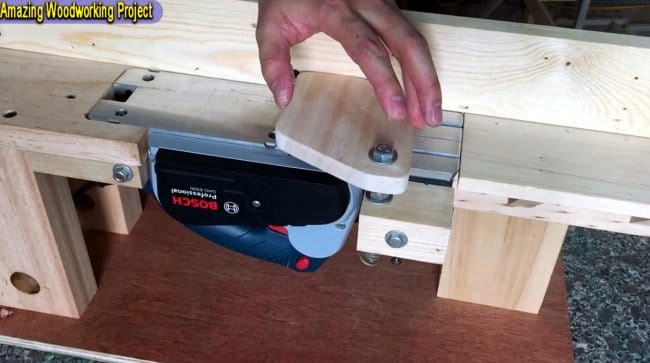

Практически все готово, остается подключить общую систему пылеудаления, и можно приступать к работам. Однако перед этим рекомендуется обработать все поверхности пропиткой для древесины, либо полиуретаном. Для лучшего скольжения деталей по столу стоит использовать аэрозольную силиконовую смазку.

Итак, первой к обработке мастер берет старую доску от паллет. И результат просто идеален.
Следующим клиентом будет деревянный брус 40Х40мм. Автор обрабатывает все его четыре грани.
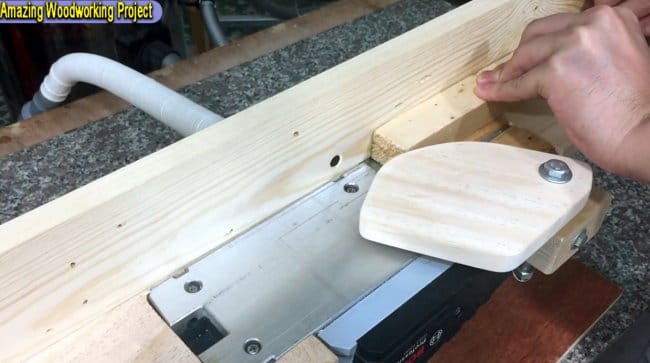

А в итоге как поверхности, так и углы полученного бруса имеют идеальные геометрические формы.
Для улучшения качества обработки деревянных заготовок в качестве стола и упора лучше использовать алюминиевый профиль. А также использовать специальные толкатели, если Вы не хотите остаться без пальцев. Крайне рекомендую использовать безопасный толкатель.
Повторюсь. Автор делает это крайне небезопасно, хотя и защиту на станке придумал. Однако она призвана защитить только при отсутствии заготовки в момент вращения лезвий фуганка. В следующий момент может вырвать заготовку по причине, например, застрявшего гвоздика, или сучка. и палец соскочит на вращающийся барабан с лезвиями.
По поводу обнаружения гвоздей в старых деревяшках можно использовать следующий инструмент. Эта штука умеет искать не только гвозди в древесине, но и обнаруживать арматуру и проводку в стенах.

Соблюдайте правила техники безопасности!
Благодарю автора за простую идею очень полезного станка для небольшой столярной мастерской!
Если у Вас имеются интересные самоделки, делитесь ими на этом сайте. Здесь Вы получите реальное вознаграждение, а не «пучок зеленки» на развлекательном форуме.
Всем хорошего настроения, удачи, и интересных идей!
Авторское видео можно найти здесь.
Источник
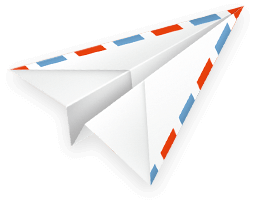
Получайте на почту подборку новых самоделок. Никакого спама, только полезные идеи!
*Заполняя форму вы соглашаетесь на обработку персональных данных
Становитесь автором сайта, публикуйте собственные статьи, описания самоделок с оплатой за текст. Подробнее здесь.usamodelkina.ru
Как сделать мини токарный станок своими руками

Всем доброго времени суток дорогие друзья! В сегодняшней статье я бы вам хотел показать и рассказать классную идею довольно полезной самоделки. Данную самоделку сможет сделать практически каждый, у кого есть мощный моторчик и пара досок. Но по своей значимости, данная самоделка может стать одной из первых у некоторых людей. Многие сейчас пойдут писать в комментариях, что данная самоделка слишком простая и не сможет справляться с нормальными заготовками и задачами, и будут от части и правы и нет. Конечно, справляться со сложными задачами самоделка врядли сможет, ведь автор использует не самый мощный мотор, да и изначально автор делает именно «мини» версию, а увеличить масштаб проекта, я думаю вы и сами сможете.
В общем сегодня рассмотри как сделать мини токарный станок своими руками. С помощью данного станка можно обрабатывать небольшие деревянные заготовки, но делается он очень просто и из всем доступных материалов.
Ну чтож, думаю хватит длинных предисловий, погнали.
И так, для данного мини станка нам понадобится:
-деревянные реечки
-большая деревянная доска
-мощный электрический мотор
-крупные болта и гайки к ним (со шайбочками конечно)
-один шарикоподшипник
-три гвоздя
Из инструментов нам также понадобится:
-малярный клей
-мини дрель
-бор машинка
-шуроповёрт
-циркуль
-линейка
-карандаш или маркер
Приступим.
Первым делом нам необходимо взять большую деревянную доску (на ней будет располагаться весь токарный станок, поэтому лучше берите необходимого вам размера), две деревянные реечки и четыре квадратика, также сделанных из дерева.
Для основания конструкции следует вырезать из доски заготовку с размерами 25 на 45 см. На большую сторону доски, необходимо приклеить одну из деревянных реечек, она, как вы уже наверное поняли, должна быть тоже 45 см в длину. Автор самоделки приклеивал с помощью малярного клея.
На расстоянии ровно 7,5 см, нужно приклеить вторую такую же реечку, приклеиваем тоже малярным клеем.
В итоге, должна получиться конструкция, как показано на фото ниже:
На остатках доски, циркулем чертим круг с диаметром 15 мм. Этот кружочек, нужно будет надеть на вал электрического двигателя, но перед этим сделаем с ним кое-какие манипуляции.
Для начала сверлим тонким сверлом (сверло должно быть такой же толщины, что и вал двигателя) отверстие ровно по центру круга, затем переворачиваем его и сверлим ещё три не сквозных отверстия, конечно же как можно ровнее.
Готово, теперь капаем пару капель клея в центральное отверстие и приклеиваем на вал двигателя:


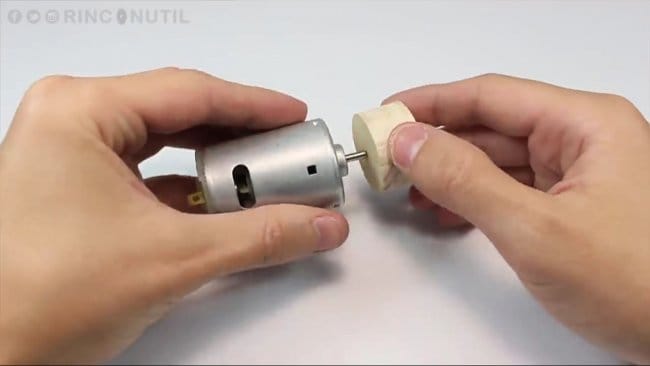

Теперь необходимо взять три гвоздя и с помощью бор машинки отрезать от них острые концы одного и того же размера. Затем снова капаем суперклеем в три отверстия на кружочке, которые делали действием раннее, и вставляем туда отрезки гвоздей, острой частью наружу. Всё должно получиться так, как на фото ниже:



Из двух кусочков доски, равной ширины, но разной длины, делаем одну деталь с помощью малярного клея. Как должна выглядеть деталь, можно посмотреть на фото ниже, а если что-то не понятно сильнее, то смотрите видео, которое будет в конце данной статьи. Ширина обеих досочек должна быть 7,5 см, длина верхней – 6 см, а нижней – см.
На верхнюю данную заготовку устанавливаем электрический мотор, прижимая и фиксируя его металлической клеймой.
Вся эта конструкция должна помещаться между двумя реечками на основной конструкции:




Всё из того же дерева делаем деталь со сторонами 10 на 7,5 см. Её нужно приложить к мотору и обозначить точку, где она пересекается с валом электрического мотора.
Теперь берём специальное «зубило» (постоянно забываю как называется), которое должно быть с таким же диаметром, что и у шарикоподшипника.
Высверливаем сначала им, а потом сверлом несколько несквозных отверстий, должно получиться как то так:
В шарикоподшипник вставляем болт и фиксируем его гайкой и шайбочкой, затем отмеряем небольшое расстояние и отрезаем с помощью бор машинки или болгарки, после чего заостряем конец отрезанного болта. Эту деталь мы вставляем и естественно вкручиваем в деревянную заготовку, которую делали ранее:
Берём ещё одну дощечку с размерами 7,5 на 5-6 см и высверливаем или вырезаем в ней длинное отверстие по центру. Данную заготовку приклеиваем к дощечке с шарикоподшипником:

На задней части основной конструкции размечаем множество отметок на расстоянии 3 см друг от друга, после чего берём мини дрель или шуроповёрт и высверливаем в каждом отметке отверстия, так, как показано на фото ниже.
В данные отверстия должен вкручиваться болт, на который, в свою очередь будет крепиться подвижная заготовка, которую делали ранее. Благодаря такому способу можно будет подгонять станок под нужные размеры изделия.
Ну и тестируем то, что у нас получилось. Всё должно выглядеть именно так:
Ну вот и всё! Простой мини токарный станок готов и осталось только его протестировать. Для этого нам понадобится не слишком толстая веточка, которую и будем обрабатывать. Вставляем её на гвозди (те которые расположены на круге от мотора) и зажимаем с обратной стороны заострённым болтом, зажимаем нижний болт, чтобы конструкция не двигалась и всё, осталось только подвести питание необходимое вашему мотору и наслаждаться обработкой дерева.
Кстати в данной самоделке не предусмотрена ни какая защита, поэтому работать необходимо в защитных очках и лучше всего при изготовлении станка, лучше всего добавить защитный элемент, по типу тех, которые используются в полноценных токарных станках. В общем соблюдайте правила безопасности!
Кстати работает данный станок просто отлично, и как я уже сказал в самом начале статьи, если увеличить масштаб самоделки, добавить более мощный мотор и поставить хорошую защиту, то получится почти полноценный токарный станок, который, к тому же не будет занимать много места и стоить он конечно больших денег не будет.
Вот видео от автора с подробной сборкой и испытаниями данной самоделки:
Ну и всем спасибо за внимание и удачи в будущих проектах самодельщики!
Источник
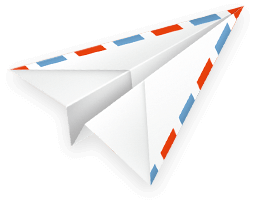
Получайте на почту подборку новых самоделок. Никакого спама, только полезные идеи!
*Заполняя форму вы соглашаетесь на обработку персональных данных
Становитесь автором сайта, публикуйте собственные статьи, описания самоделок с оплатой за текст. Подробнее здесь.usamodelkina.ru
Столярный нож из напильника своими руками
Здравствуйте, уважаемые читатели и самоделкины!Практически каждому из Вас весьма интересна тема ножей, особенно которые служат в мастерской незаменимым и надежным инструментом.
В данной статье, автор YouTube канала «Evgeniy Budilov» расскажет Вам, как он изготовил нож для работы с кожей, пластиком, или столярных работ.
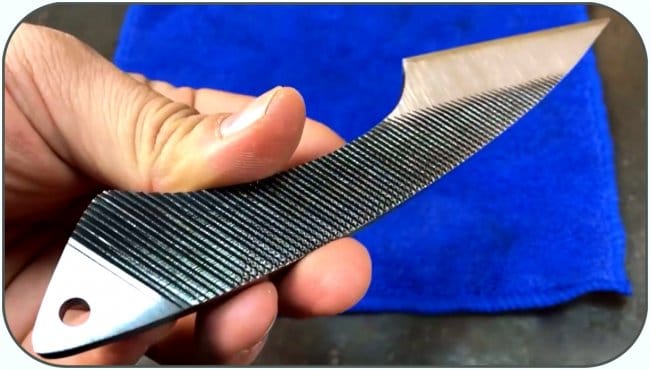
Эта разновидность ножа весьма проста в изготовлении, и может быть повторена с небольшим количеством инструментов и станков.
Материалы.
— Старый напильник
— Силикатный кирпич
— Машинное масло
— Аэрозольная краска.
Инструменты, использованные автором.
— Газовая горелка
— Электрическая или газовая печь
— Струбцины
— Болгарка, отрезной диск
— Ленточный шлифовальный станок
— Инфракрасный цифровой термометр
— Точильный станок
— Дисковая металлическая щетка
— Заточной станок
— Маркер, керн, молоток.
Процесс изготовления.
Итак, основой для этого простого в изготовлении ножа послужит старый советский напильник. А как Вы наверное знаете, они изготавливаются из очень твердой, высококачественной инструментальной стали марок У10А, У13А.

Первым делом автор складывает из силикатного кирпича небольшой горн. В одном верхнем кирпиче есть специальное отверстие, в которое устанавливается газовая горелка. Она подключается к газовому баллону при помощи шланга.
Полностью напильник не помещается в камере горна, поэтому он отрезает хвостовик болгаркой.
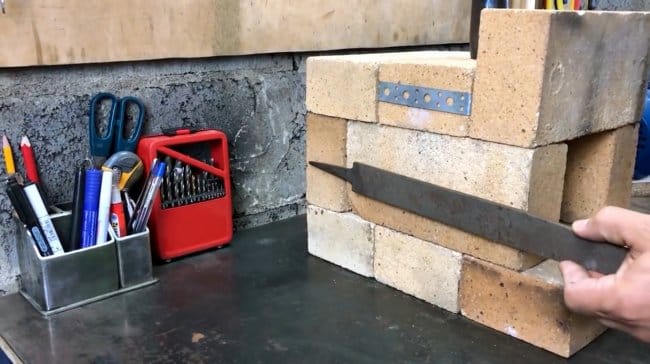

Для того, чтобы металл легче поддавался обработке, его необходимо разогреть в печи.
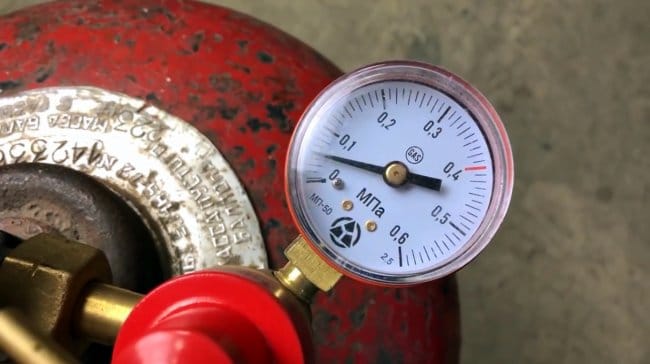

После полного прогрева до малинового цвета, автор закрывает камеру, и дает стали остыть.
Пока заготовка остывает, и происходит процесс отпуска, автор сделал небольшой набросок.
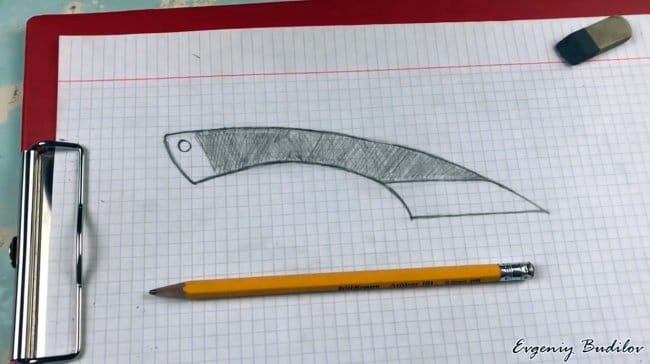
Попытавшись перенести контуры шаблона на заготовку с помощью маркера, стало ясно, что они плохо видны, и расплываются. Лучше сделать разметку при помощи белой аэрозольной краски.
Излишки материала удаляются, и заготовка отрезается.
Далее профиль будущего клинка обрабатывается при помощи ленточного шлифовального станка, периодически требуется охлаждать заготовку в воде.
Также выравнивается закругление рукоятки, и линия режущей кромки.
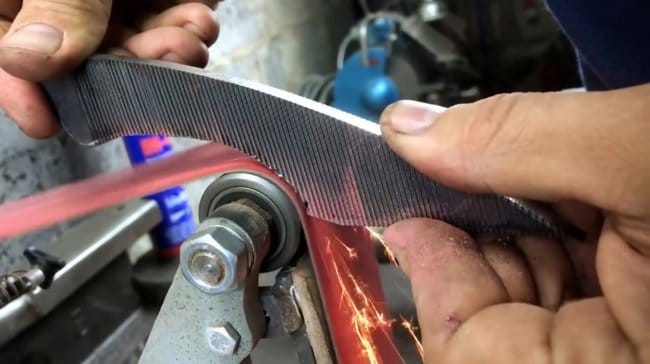

Теперь размечается и кернится хвостовик.


Отверстие в хвостовике высверливается сверлом с корундовой вставкой, обязательно использование смазки и низкие обороты станка.
Для того, чтобы точно сформировать спуски, мастер применяет хитрый прием. Он окрашивает край маркером, и прочерчивает линию кромки керном.
Теперь клинок фиксируется на специальном приспособлении, позволяющем наклонять заготовку под небольшим углом.
С помощью такого приспособления достаточно легко и точно можно сформировать спуски.

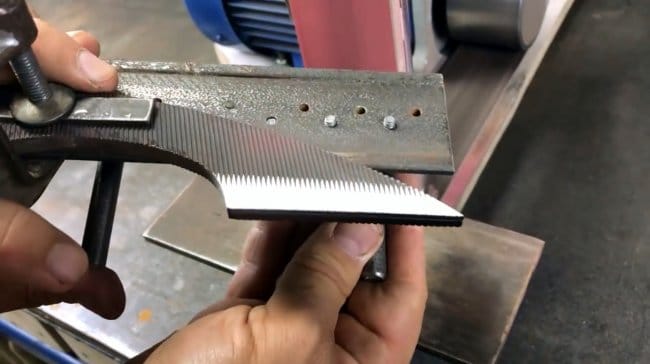
Первая сторона готова, заготовка разворачивается на 180 градусов, и формируется второй спуск.
Ножик получается весьма небольшой, но очень удобно лежит в руке. Лезвие разогревается в горне, и закаливается в машинном масле. Важно не просто опустить его в масло, а слегка помешивать, для более быстрого и равномерного остывания. Кроме того, критическая температура нагрева перед закалкой составляет 1300 градусов, при этом стальная заготовка будет светится белым цветом, а нормальный цвет — малиновый. Также можно контролировать достаточность прогрева при помощи магнита. При достижении необходимой температуры сталь теряет магнитные свойства. Вместо машинного масла лучше применять минеральное.
Итак, клинок остыл, и теперь выглядит вот так.
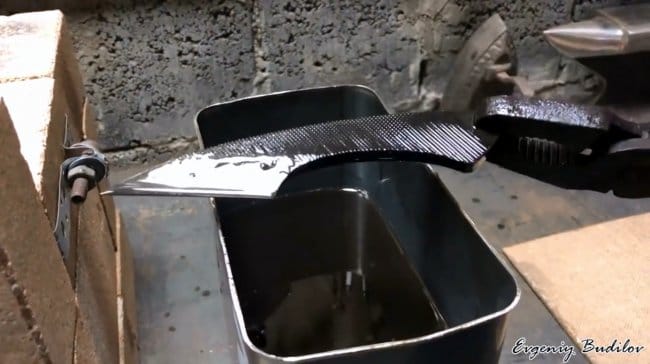
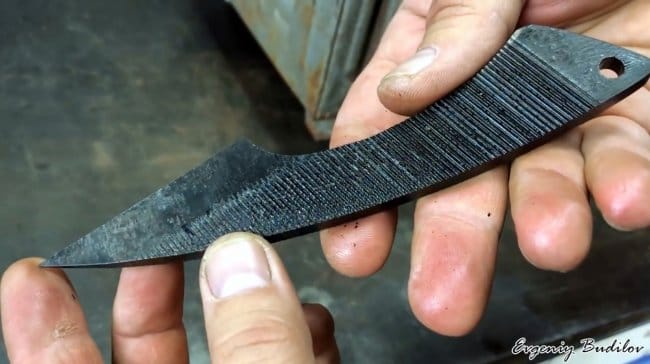
Теперь можно провести первый тест на качество закалки, для этого автор провел еще не заточенным лезвием по стеклянной бутылке. На ней остались весьма глубокие царапины.
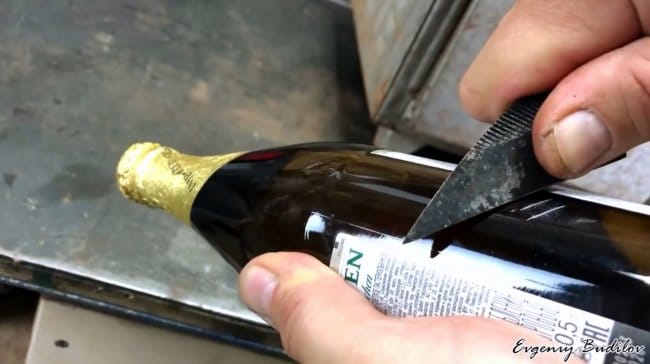
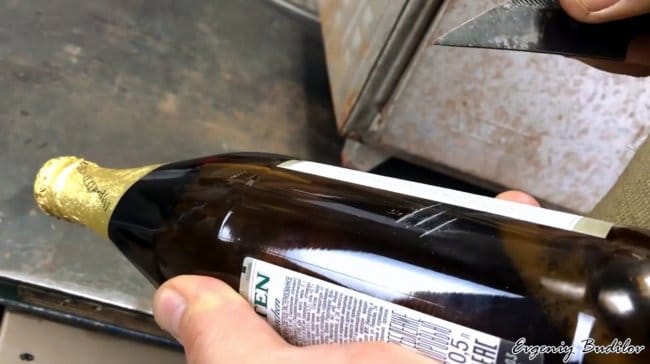
После закалки клинок нужно отпустить в электрической или газовой печи при температуре около 200°C в течении двух часов. Затем печь отключается, и клинок остается в ней до полного остывания.
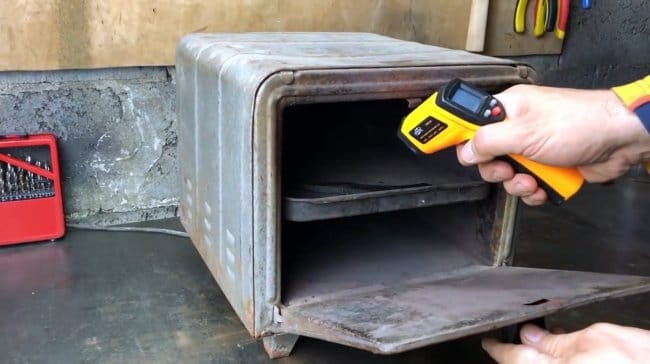
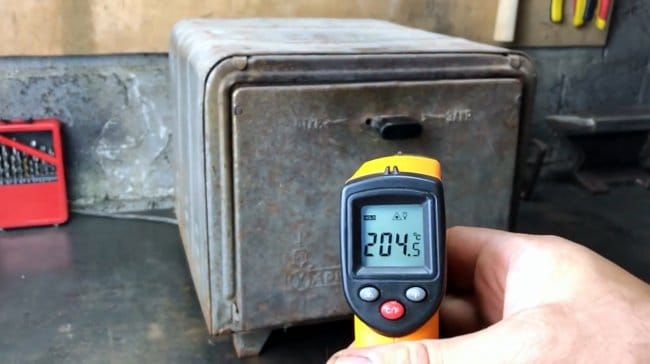
Поверхности клинка обрабатываются на точильном станке с дисковой металлической щеткой. Торцы и грани шлифуются при помощи гравировальной машинки.
Остается последний этап ручной заточки режущей кромки. Автор использует специальный станочек, который позволяет точно контролировать угол заточки.
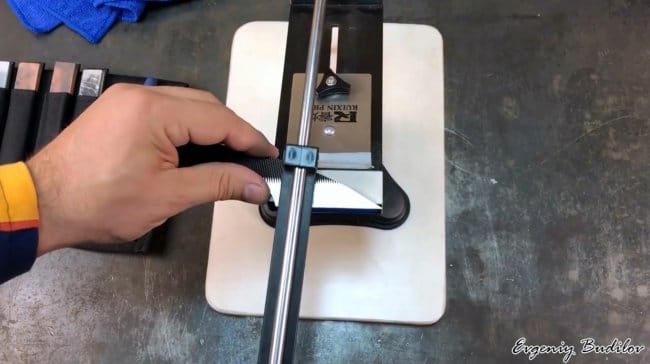
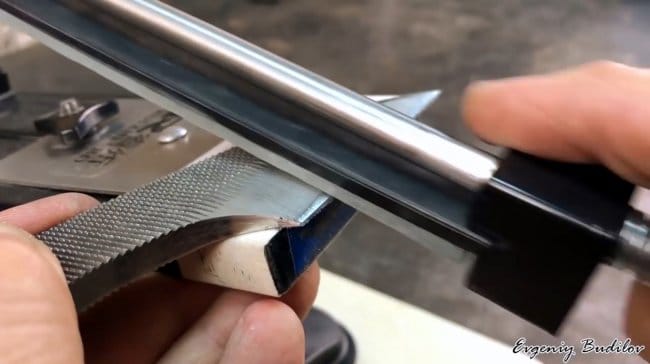
Вот такой небольшой, но весьма функциональный инструмент получился у мастера.
Даже предварительный проект почти полностью совпал с готовым результатом.
Благодарю автора за простой, но интересный мастер класс по изготовлению ножа для мастерской!
Всем хорошего настроения, удачи, и интересных идей!
Авторское видео можно найти здесь.
Источник
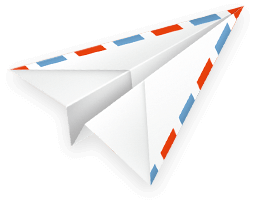
Получайте на почту подборку новых самоделок. Никакого спама, только полезные идеи!
*Заполняя форму вы соглашаетесь на обработку персональных данных
Становитесь автором сайта, публикуйте собственные статьи, описания самоделок с оплатой за текст. Подробнее здесь.usamodelkina.ru
Самодельный отрезной станок
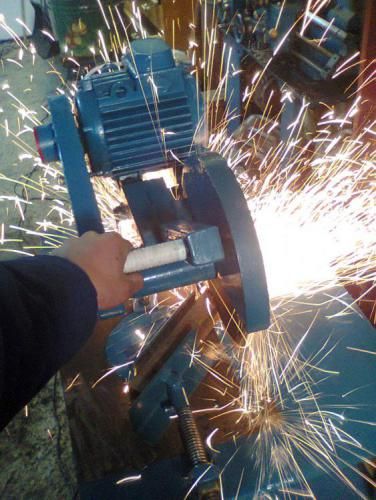
Практически в каждой мастерской имеется такой нужный и сложно заменимый инструмент как болгарка. Он достаточно универсален и применяется для резки метала, дерева, зачистки и полировки различных поверхностей. Но бывает приходиться работать по несколько часов, что сказывается на усталости рук. В таком случае, особенно при каждодневной работе, может очень пригодится такая вещь как отрезной станок. Он требует гораздо меньших затрат физических усилий, к тому же обеспечивает гораздо более высокую точность реза. В данной статье автор представляет фото отчет создании такого станка.
Материалы и инструменты, необходимы для сборки станка, будут перечислены в статье.
Автор начал с изготовки шпинделя. Он точился под 306 подшипники, и имеет диаметр 30 мм.
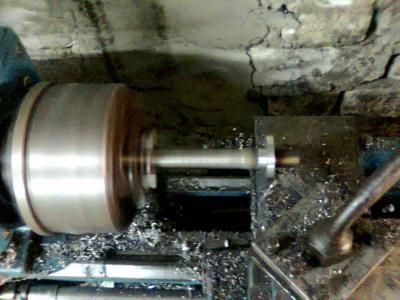
С одной его стороны имеется посадочное место под шкив, с другой стороны нарезана резьба (как на стандартной болгарке) Под крепления отрезного круга.
Из подходящей по диаметру трубы изготавливаются наружные посадочные места подшипников.
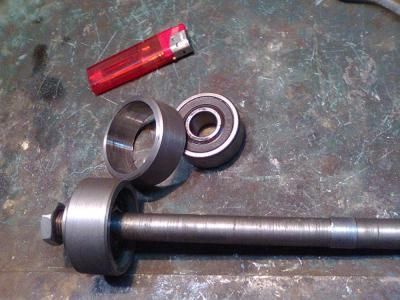
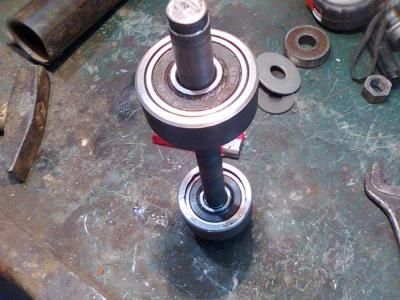
Посадочные места намечаются под подшипники, между ними вваривается труба того же диаметра.
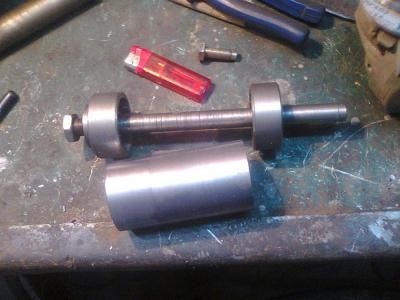
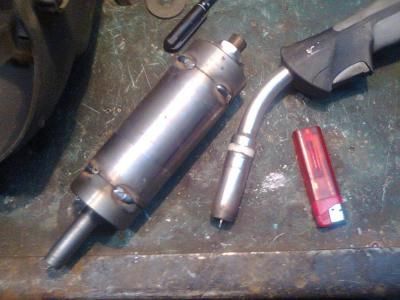
С одной стороны одевается шкив:

Центровочная гайка такая же, как на обычной болгарке.
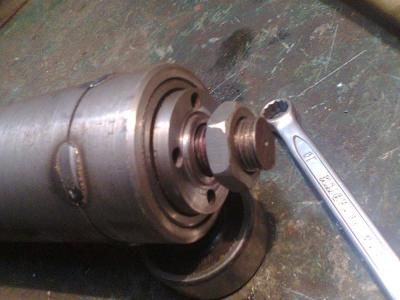
Для станка использовался двигатель мощностью 3 кВт, со скоростью вращения 1500 оборотов в минуту. Для него была изготовлена подставка, с продольными отверстиями, для регулировки натяжения ремня. Между подставкой и шкивом было приварено 2 профиля 40 мм.
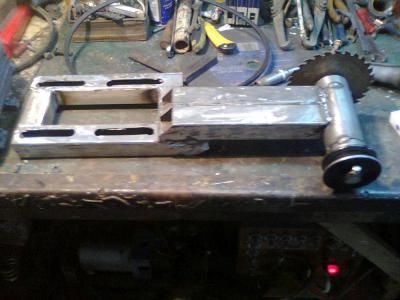
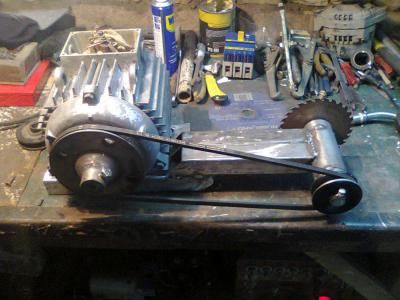
Далее, из листового метала толщиной 2 мм, был вырезан и выварен защитный кожух:
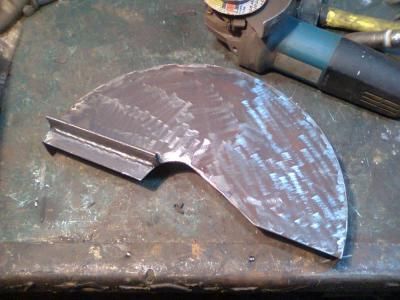
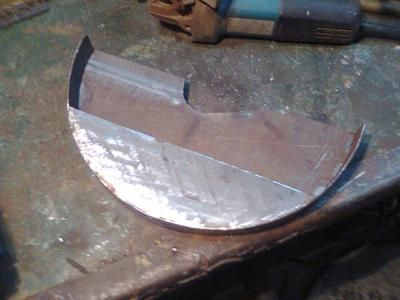
Через уголок кожух приваривается к сороковому профилю. Перед тем как это делать, желательно надеть на шпиндель отрезной круг (на 300 мм) чтобы не прогадать с его положением. Расстояние от круга до внутренней части кожуха не должно быть меньше чем 5 – 6 мм.
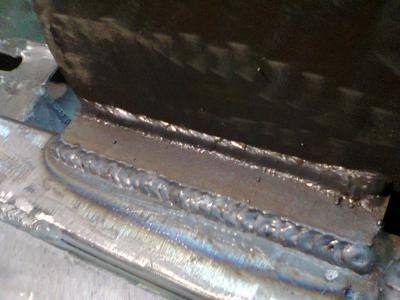
Далее был изготовлен шарнир для крепления всей конструкции. В качестве шарнира были использованы две трубы, вставленные одна в другую с небольшим люфтом.
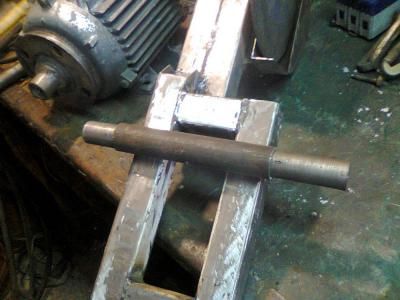
Под станок была изготовлена столешница. Толщина листа рабочей поверхности – 5 мм. Ножки и перегородки изготовлены из 50 уголка.
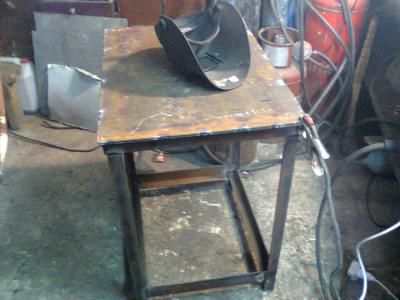
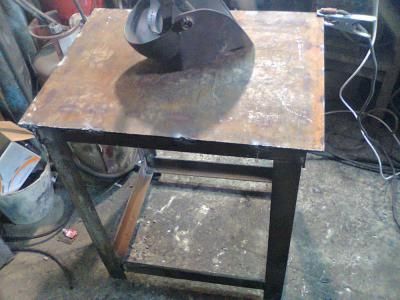
К столешнице приварен шарнир:

В качестве материала для изготовления ручки был использован тот же профиль на 40 мм, и металлический прут подходящий по размеру.
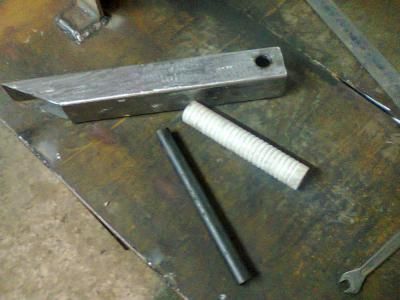
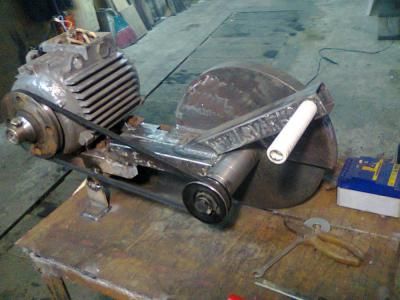
Для жесткой фиксации заготовки во время реза, необходимы тисы. Чтобы изготовить из понадобятся два металлических уголка и шток с резьбой под гайку из 150 водопроводной задвижки и сама гайка.
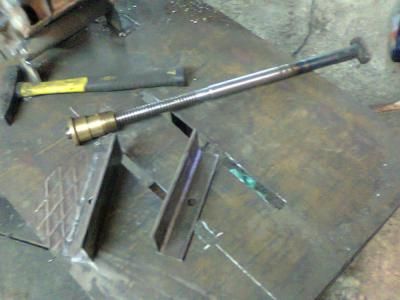
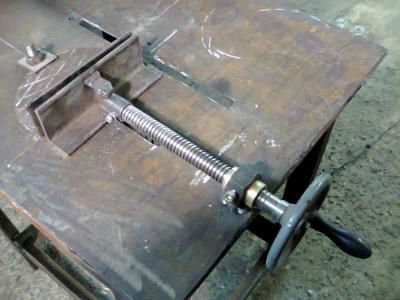
Из листового метала изготавливается защитный кожух для ремня:
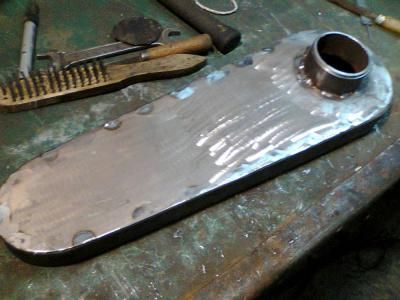
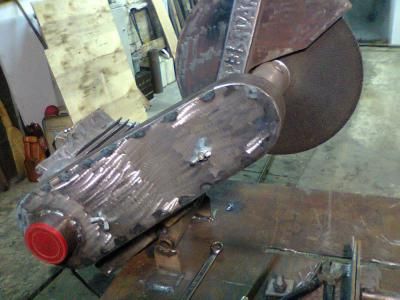
Далее монтируется электрическая часть станка, состоящая из автомата и концевика на выключение двигателя.
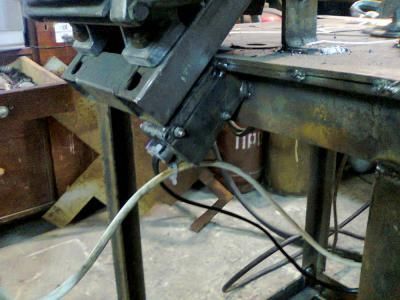
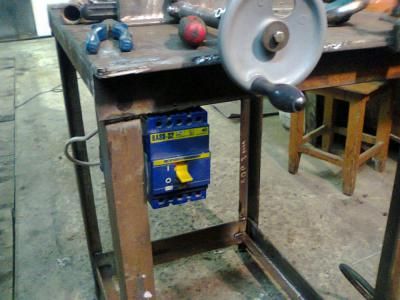
Приваривается пластинка для защиты от искр.
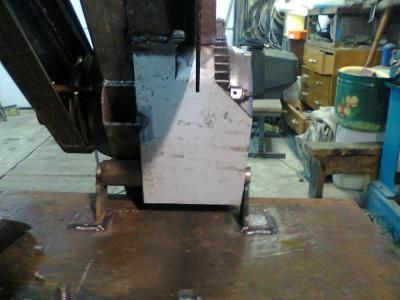
Дорабатывается столик, к нему добавляются деревянные полки.
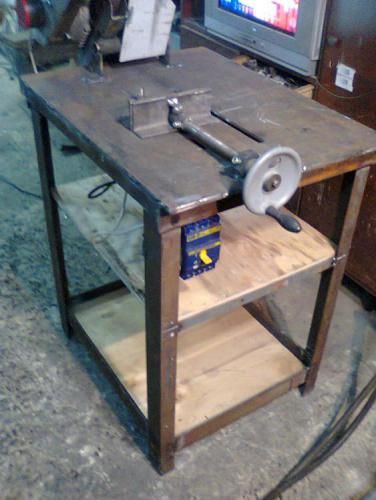
И вот как выглядит готовый станок после покраски:
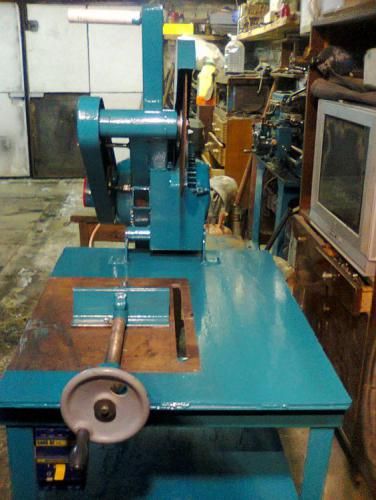
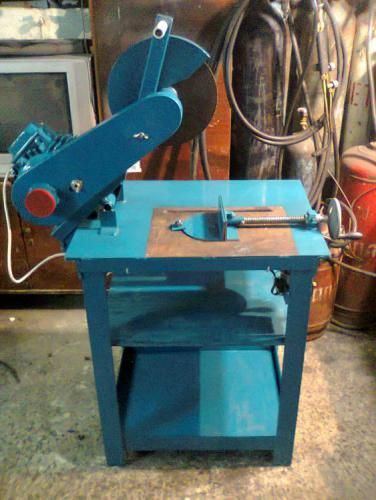
А вот результат его работы:
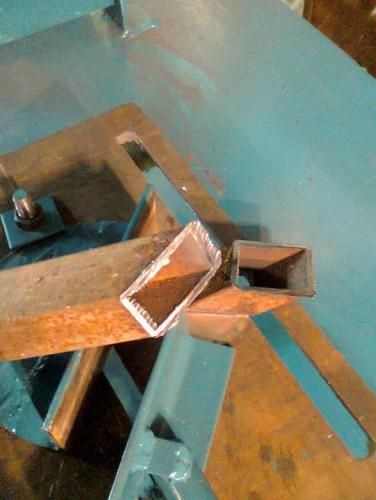
Источник
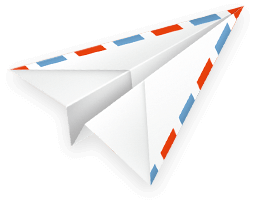
Получайте на почту подборку новых самоделок. Никакого спама, только полезные идеи!
*Заполняя форму вы соглашаетесь на обработку персональных данных
Становитесь автором сайта, публикуйте собственные статьи, описания самоделок с оплатой за текст. Подробнее здесь.usamodelkina.ru