Самодельные направляющие для станков своими руками
Направляющие для самодельного станка, естественно, нужно делать своими руками, иначе зачем надо было начинать его изготовление.
Статья от нашего читателя
Я живу в довольно маленьком городе, и выбор на строительном рынке у нас не слишком большой. А цены дерут зверские. Я долго мучился, заказывал из интернета, но однажды не выдержал. Почта, которая никогда не привозит ничего вовремя. транспортные компании, которые дерут за каждый лишний грамм огромные деньги.
В общем, вопрос встал – мне нужны направляющие для станков, и нужны прямо сейчас. Так как взять их неоткуда, пришлось делать самому. На выходе получилось очень симпатично, да и вполне функционально. Описывать сам процесс изготовления станины смысла нет, все и так понятно. Все запчасти, которые вам понадобятся, изображены на этом фото :
В умелых руках – 5 минут и готово.
Но, так как этот вариант не универсален, я начал копать дальше. Захотелось сделать рельс
Делал из дерева, крепил на металлическую основу. У станка рабочее поле вышло 1050 мм на 1050 мм – универсально и удобно. Первый вариант не устроил из-за тяжелого движения – почему-то была очень большая сила трения. Переделывал пару раз. Остановился на таком варианте – работают как часы!
Если не очень поняли по фото – вот схематичное изображение. Ничего сложного.
Дальше ушел в рельсы с головой, немного поколдовал и вышло как-то так:
Этот вариант местные мастера попросили у меня купить. Можно бизнес открывать.
В общем, я могу с уверенностью человека, который покопался в этой теме и попробовал все своими руками, сказать, что сделать своими руками направляющие для станков несложно, если вы дружите с руками, головой и инструментами. Главное – начните. Любые возникающие вопросы можно погуглить, но делать это лучше по ходу дела. Если начнете откладывать дело, пытаясь изучить все заранее, можете не приступить вообще.
Видео: ЧПУ своими руками (мебельные направляющие)
metmastanki.ru
Направляющие для ЧПУ своими руками
Направляющие – важная деталь в устройстве фрезерного станка. Направляющие для ЧПУ своими руками могут выполнить многие мастера, опыт работ в домашних условиях имеется у большинства практикующих специалистов.
Задумав домашнее производство мебели, необходимо соблюдать точность в конструкции. Поэтому многие мастера, осваивающее его нуждаются в качественном оборудовании. Специальный деревообрабатывающий механизм облегчит труд, позволит создавать качественную, продукцию в короткий срок.
Чтобы изделия отличались высокой точностью, но соответствовали современным характеристикам, применяются модели ЧПУ.

Числовое программное управление
Числовое программное управление дает такую возможность, но покупать его под силу не каждому предпринимателю. Именно по этой причине появляется потребность изготовить самодельный агрегат, для устройства которого применяются детали собственного производства.
Основными частями фрезерных станков, предназначенных для обработки того или иного материала, являются направляющие. Они представляют собой шариковые или роликовые подшипники качения, назначением которых является перемещение каретки. Их цель – ускорение, упрощение и придание точности производству.
Виды направляющих
Точность станка – это задача направляющих стержней. Они делятся на два вида:
- скольжения;
- качения – предполагают использование подшипников.
Первый вид используется на станках небольшой мощности и не нуждающихся в большой продуктивности. К ним относятся деревообрабатывающие, токарные, сверлильные и настольные аппараты.
Самодельные направляющие для ЧПУ станка изготавливаются линейного тапа, они могут быть роликовыми или шариковыми. Независимо от вида должны обладать следующими характеристиками:
- сохранением заданных параметров;
- плавным перемещением;
- эффективностью;
- низким трением.
В качестве деталей для скольжения втулок в большинстве случаев используются стержни цилиндрической формы, их необходимо отшлифовать. Некоторые мастера советуют изготовить механизм и без втулок, но из-за этой манипуляции будет снижена аккуратность изделий, а стержни будут иметь меньший срок эксплуатации.
Варианты самодельных направляющих
Направляющий механизм для ЧПУ часто бывает основан на использовании хромированной металлической трубы.

Направляющий механизм возможно сделать из хромированной металлической трубы
Она имеет небольшую стоимость, ее легко обрабатывать, меняя форму. Кроме того, есть и ряд недостатков:
- Защитный верхний слой стирается очень быстро, затем металл изнашивается быстрее.
- При высокой нагрузке на трубу, она не дает необходимой прочности.
Такое решение является дешевым для специалиста, но хватит работы такого станка лишь на несколько десятков часов. Это связано с минусами оцинкованных или хромированных труб, которые сами сделаны из мягкого металла, подверженного быстрому износу при нагрузке. Фрезер в совместном использовании с такими направляющими значительно сократит их срок службы.
Кроме этих способов, следует применять в качестве движущих частей устройства фрезера с небольшой мощностью. Они придают изготавливаемым деталям точную тщательную обработку, чаще их используют на станках для обработки дерева. Они имеют низкую цену и маленький срок выработки.
Самодельные направляющие: инструкция
Самодельные направляющие для деревообрабатывающего станка в ЧПУ собственного изготовления могут быть нескольких вариантов.
Первый вариант выполнения – простой, вовремя выполнения агрегата по такому алгоритму необходимо собрать конструкцию, состоящую из таких деталей:
- Подшипников – принимают силу мотора, оказываемую противодействию.
- Металлического уголка – выступает в роли каретки.
- Болтов и гаек – размер должен соответствовать внутреннему диаметру подшипника.
Инструкция по изготовлению:
- для начала измеряем необходимую длину металлического уголка, убрать лишнее;
- просверлить симметрично с двух сторон, отверстия необходимого диаметра;
- при помощи гаек и болтов закрепить подшипники.
Конструкция направляющих готова, она не требует массы усилий и довольно понятна для неопытного мастера.
Направляющие из мебельных стержней используются при изготовлении мебели на заказ, чтобы добиться точности, подойдет готовая фрезерная база из мебельных деталей. С применением в конструкции отшлифованных цилиндрических стержней.
В этом случае необходимо сделать отверстия, равные по диаметру их ширине, прямо в суппорте, они обязательно обязаны быть параллельны друг другу.
Специалисты рекомендуют дополнительно использовать бронзовые втулки, тогда их размер обязан ровняться диаметру направляющих.
Используя старые печатные машинки «Янтарь», легко изготовить направляющие для ЧПУ своими руками. Их особенность в том, что движущие части там выполнены в форме уголка. Понадобятся такие детали:
- подвижная часть;
- сепаратор – пластина, в которую вмонтированы шарики;
- рельсы;
- металлическая пластина;
- уголки, длина которых равна рельсу.
Соединяем все части необходимым образом и получаем готовый результат.
Рекомендации умельцев
Для маленького домашнего станка ЧПУ в качестве направляющих следует взять автомобильные стойки.

Автомобильные стойки подойдут для маленького станка ЧПУ
Их используют в отечественных автомобилях, поэтому достать их не составит труда. Используются штоки от стоек, они обладают прочностью и сделаны из качественного металла.
Поэтому проявив смекалку и фантазию, у мастера возможности становятся безграничны. Немного подумав, несложно собрать станок ЧПУ своими руками из подручных деталей, находящихся в доступе и не используемых по назначению. Это сократит затраты на домашнее производство и повысит его продуктивность и качественность.
Видео по теме: Самодельный линейный подшипник
promzn.ru
Направляющие для ЧПУ станков своими руками
Содержание статьи:
В конструкции станка с ЧПУ используется несколько типов направляющих. Самодельные устройства нередко комплектуются рельсами из каретки печатной машинки, принтера или покупными. Качество и характеристики направляющих влияют на возможности станка с ЧПУ и точность обработки, поэтому экономить на их покупке не стоит.
Валы круглого сечения
круглые полированные валы
Наиболее широко применяемый и недорогой тип направляющих это полированные валы. Они просто монтируются, обрабатываются, купить такие детали не проблема. Валы производят из высокопрочной стали, в основном, шарикоподшипниковой, марок ШХ15 СГ, ШХ15, 95Х18-Ш. Они дополнительно подвергаются индукционному закаливанию верхних слоев, после чего полируются. Закалка индукционным методом повышает срок эксплуатации и снижает степень износа. Полированная поверхность позволяет двигаться каретке с минимальным трением за счет идеальной гладкости. Фиксируются валы своими руками, с двух концов, очень просто и быстро.
В продаже множество подделок, выполненных из металла низкого качества. Ведь проверить твердость стали на месте не представляется возможным.
Эта модель направляющих обладает рядом недостатков:
- нет фиксации на основании. Вал удерживается лишь за счет двух концевых крепежей, что значительно облегчает установку своими руками, но делает направляющие независимыми от столешницы. Это увеличивает вероятность неточностей при обработке, направляющие может повести, со временем они искривляются.
- провисают на длинных отрезках. В связи с провисанием валы длиннее 100 см в станкостроении не применяют. Следует также учитывать соотношение толщины и длины вала. Оптимальным считается соотношение 0,05, а лучше от 0,06 до 0,1.
Линейные подшипники на круглый вал
Используется два типа линейных подшипников для направляющих:
- шариковые втулки;
- подшипники скольжения.
Шариковые втулки или подшипники качения по сравнению с каретками рельс обладают двумя большими недостатками: малая грузоподъемность, большой люфт. Чтобы каретка не разворачивалась, нужно на каждую ось ставить по паре валов. Минусы шариковых подшипников качения:
- невысокий ресурс работы — шарик прилегает к валу лишь в единой точке, поэтому здесь образуется высокое давление. Постепенно в месте соприкосновения пробивается канавка и вал необходимо своими руками менять;
- большой люфт — дешевые подшипники (а их большинство) производятся со значительным люфтом;
- легко забиваются опилкой и пылью.
Подшипники скольжения. Подшипники этого типа изготавливают из мягких металлов, капролона, они работают по принципу трения скольжения. Если при эксплуатации выдерживаются все допуски, грузоподъемность и точность такого подшипника не меньше, чем качения. Вместе с тем, ему не страшны опилки и пыль. Но это касается лишь бронзовых деталей, грамотно обработанных.
Постепенно изделие изнашивается и его необходимо периодически подгонять, чтобы убрать зазоры. Чаще всего при изготовлении направляющих своими руками, используются более доступные шариковые подшипники.
Шлицевые валы
шлицевые валы
Вал круглого сечения имеет продольные пазы, по которым двигаются шарики втулки. Конструкция обладает повышенной жесткостью по сравнению простыми шлифованными валами, более длительным сроком эксплуатации, способна воспринимать с втулки усилия кручения.
При этом они также просто устанавливаются на два крепления по концам. Благодаря конструкции можно обеспечивать натяжение вала, поэтому их используют при необходимости крепежа направляющих по концам.
Один из основных минусов шлицевых направляющих — их высокая цена, поэтому в обычных станках с ЧПУ они используются редко.
Цилиндрические валы
цилиндрический вал на основании
Конструкция цилиндрических валов позволяет удерживать уровень по всей длине, полностью исключая провисание под весом каретки или своим собственным. Такие направляющие называются еще линейными опорными валами, фиксируются они прямо к корпусу станка с ЧПУ через предусмотренные в опорах резьбовые отверстия. По таким направляющим могут двигаться каретки большого веса без провисания.
Минусы цилиндрических валов:
- малый срок эксплуатации;
- заметный люфт втулок.
Если подшипники линейного типа одинаково работают с нагрузками разного направления, то на цилиндрических валах каретки показывают меньшую стабильность. Это объясняется замкнутой поверхностью втулок, которой не обладают каретки. Поэтому следует быть готовым к тому, что аппарат с ЧПУ малого размера с увесистой кареткой на опорных валах будет работать с большей погрешностью, нежели такой же станок с ЧПУ на обычных круглых рельсах.
Технология изготовления цилиндрических рельс очень проста, поэтому их производят и известные фирмы, и кустарные мастерские. Этим объясняется разброс технических характеристик и цен. Зачастую каретки и рельсы одного изготовителя «ноу нэйм» не совпадают.
Профильные рельсовые направляющие
линейные направляющие
Такие направляющие устанавливаются в станках ЧПУ особой точности, фиксируются прямо к станине, они могут быть шариковыми и роликовыми.
Шариковые профильные направляющие
На профильных направляющих есть дорожки, по которым перемещается каретка. Поэтому нагрузка распределяется равномерно по длине дорожки: шарик каретки прилегает к рельсу по дуге. Рельсы-направляющие характеризуются геометрической точностью. При перемещении тяжелой каретки их прямолинейность не нарушается. Служат они долго и практически не дают люфт.
Минусы шариковых рельс:
- к местам крепления существуют высокие требования по прямолинейности и шероховатости;
- достаточно сложно монтируются на станок с ЧПУ.
В продаже можно найти модели кареток и направляющих с разными грузоподъемностью и преднатягом. Производство рельс дорого, технология сложна. Поэтому кустари не занимаются их изготовлением, а представленная на рынке продукция достаточно качественная. Достойные направляющие выпускают, например, под марками ТНК и Hiwin.
Роликовые профильные направляющие
Это одна из разновидностей профильных рельс с плоскими пазами качения. Опорные модули вместо шариков оснащаются роликами. Благодаря этой разнице направляющие получаются еще более жесткими, выдерживающими большие грузы и длительный срок эксплуатации. Такие рельсы устанавливают на интенсивно работающее оборудование для фрезеровки камня, прочных марок стали и чугуна.
Призматические рельсы и «ласточкин хвост»
Их устанавливают на металлообрабатывающих производствах, где требуется повышенная жесткость. Рельсы «ласточкин хвост» представляют собой два скользящих друг по другу, плоских элемента. Отличие конструкции в большой плоскости соприкосновения. Такие рельсы нельзя демонтировать, они являются частью станины. Их производство и ремонт довольно сложны, поменять их своими руками вообще невозможно. Поэтому конструкция используется только в профессиональных станках с ЧПУ.
Самодельные направляющие из того, что нашлось под рукой
направляющие из стального уголка
Простейшие направляющие можно собрать своими руками из металлического уголка, подшипников, гаек и болтов. Алюминиевые уголки для направляющих использовать не стоит — деталь придется менять очень часто. Ведь шарикоподшипники каретки будут выедать в ней дорожки. Предпочтительнее стальной уголок или кругляк. В зависимости от интенсивности использования его можно закалить или оставить, как есть. Но непременно следует отшлифовать, уменьшив трение. Наиболее простой и бюджетный вариант это направляющие из старого принтера.
Не следует подбирать слишком широкие подшипники, это бесполезно. Ширина «выедаемой» дорожки на направляющей не зависит от габаритов подшипника. Диаметр болтов должен совпадать с внутренним поперечником подшипника.
Чертежи, схемы и презентация самодельных направляющих в видеороликах:
stanokgid.ru
Направляющие и каретки для ЧПУ своими руками: типы, конструкции
Механика каждого станка, независимо от его предназначения и типа, содержит комплектующие, которые относятся к базовым. Поэтому игнорировать их параметры недопустимо. Общепризнанно, что такой важной составляющей для металлорежущих или деревообрабатывающих устройств считаются направляющие. Именно ними определятся безошибочная и цикличная работа.
Поэтому тот, кто решил создать станок, должен позаботиться, чтобы в его конструкции использовались качественные направляющие для ЧПУ, положительно влияющие на функционал устройства. На приобретении комплектующих не экономят.
Основные типы направляющих
В процессе конструирования и монтажа станков (заводского и самодельного изготовления) применяют разные типы направляющих устройства. Это связано с их предназначением – фрезерование, сверление или токарные работы. Они могут быть двух типов.
Направляющие скольжения
Их используют в оборудовании небольшой мощности, не требующем особой точности и высокой производительности. Такими деталями комплектуют сверлильные и токарные агрегаты настольного типа, деревообрабатывающие станки.
Полированный вал, как вид направляющей, относится к бюджетным. Он наиболее распространен.
ВАЖНО! Его изготавливают из высоколегированной стали, выполняют индукционную закалку и, впоследствии, шлифовку. Такая обработка служит для увеличения продолжительности работы, а вал изнашивается меньше.
Полированный вал имеет недостатки:
- крепление в концевых точках, со станиной нет крепления, из-за чего налицо отсутствие жесткой связи со столом и наличие погрешностей в обработке,
- провисание при увеличенной длине, поэтому допустим её максимум – 1 метр. Рекомендуют иметь оптимальное соотношение диаметра вала и его длины (0.06-0.1), чтобы достичь нормальных результатов.
Направляющие качения
Они сконструированы при участии подшипников качения.
У линейных подшипников – больший люфт, чем у каретки рельсовых направляющих, он меньше нагружен. Но у него есть ряд минусов:
- низкий уровень грузоподъемности,
- недолговечность,
- изготовление с солидным люфтом,
- чувствительный к воздействию пыли и стружек на вал.
Материал для производства втулок – бронза, латунь, капролон. Если имеет место соблюдение допусков, бронзовые подшипники скольжения не уступают подшипникам качения. Время от времени, если подшипник скольжения износился, его подгоняют, и чтобы устранить зазоры. Поэтому шариковая втулка более предпочтительна, благодаря тому, что она доступна и взаимозаменяема.
Вал и его виды
Стоит дать краткую характеристику и остальным видам.
- Шлицевому валу свойственно наличие специальной дорожки для шариков втулки. Отличаясь большей жесткостью и износостойкостью, сравнительно с валом обычного вида, применим в механизмах, в которых желателен монтаж направляющих на концах. В конструкции станков задействованы крайне редко из-за дороговизны.
- Вал на опоре в виде цилиндрических рельс линейного типа не допускает прогибания под нагрузкой и собственным весом. Его крепят на станине, надежно фиксируя. Несмотря на минусы, выражающиеся в наличии большого люфта втулок, их малом сроке эксплуатации, у цилиндрических рельс – большая грузоподъемность. Отличаясь от линейных подшипников, каретка по-разному реагирует на степень нагрузок. У небольшого станка ЧПУ, имеющего тяжелый шпиндель, есть вероятность того, что снизится точность.
- Предназначение профильных рельсовых направляющих – большая точность. Они также прикреплены к станине. Благодаря специальным дорожкам качения, нагрузки на каретку распределяются равномерно по поверхности, а профилем касания шарика к рельсе есть дуга. Среди плюсов – наличие хорошей грузоподъемности и износоустойчивости, а люфт сведен к минимуму. Сложности производства таких рельсов, отрицательно сказываются на ценообразовании, они дорогостоящие. Особенно это относится к направляющим, поставляемым известными брендами, у которых станки имеют числовое программное управление.
- У роликовых рельсов – плоские дорожки качения, а в опорном модуле, на месте шариков, установлены ролики, улучшающие все параметры направляющей. Их применяют в станках, фрезерующих черные металлы, сталь и камень.
- «Ласточкин хвост» выбирают для промышленного металлообрабатывающего оборудования, если нужна повышенная жесткость крепления. В направляющих этого типа – скольжение плоских поверхностей при максимальной площади контакта. Их выполняют в виде монолита со станиной. Вследствие сложности и трудоемкости процесса изготовления и ремонта, поэтому хоббийное станкостроение не приемлет эти направляющие.
Каким конструкциям отдать предпочтение
Не все могут позволить себе приобрести, скажем, обрабатывающий центр с ЧПУ для изготовления мелкосерийных деталей в домашних условиях, станок форматного типа или для токарных работ. Но самодельный агрегат с ЧПУ, сделанный собственноручно – реально. Собранное устройство в умелых руках продемонстрирует образцы правильной обработки деталей.
Собирая механику программируемых станков, обычно применяют самодельные линейные направляющие, так как в устройствах с круговым движением нет необходимости. Обратим внимание на некоторые конструкции, применяемые при этом.
Оцинкованные или хромированные трубы
Они идут с различным диаметром можно использовать как стержни при монтаже маломощных устройств – плоскошлифовальных наждаков, сверлильных или токарных станков. По шлифованному цилиндрическому стержню осуществляется движение бронзовой втулки. Иногда суппорт делают и без нее. У труб – невысокая цен, их легко обрабатывать. Хотя есть минус: небольшой ресурс (стирание защитного слоя наступает спустя 15-20 проходок, после чего сталь изнашивается более интенсивно), нет нужного уровня прочности при высоких нагрузках.
Фрезер
Эффективен фрезер, в котором направляющий механизм изготовлен на основе бывшего в употреблении матричного принтера или печатной машинки «Янтарь». При таком варианте прослужит долго. Не нужно искать очень широкие подшипники, их внутренний поперечник должен равняться диаметру болтов.
Мебельные стержни
Проблему механики для станков с ЧПУ можно правильно решить при помощи мебельных стержней. Тем более, что самоделки с их применением гарантируют тщательную обработку на деревообрабатывающем, ленточно-шлифовальном оборудовании, и даже фрезерном с невысокой мощностью. Мебельные комплектующие относятся к дешевым, хотя ресурс у них небольшой.
Полированный вал
Недорогой и часто применяющийся тип направляющей. Сущность обработки – индукционно закалить верхний слой, что способствует повышению длительности эксплуатации и снижению интенсивности процесса изнашивания. Затем вал полируется, и каретка движется при минимальном трении.
Самодельные
Часто практикуется установка самодельных направляющих, используя то, что есть в наличии. Например, можно воспользоваться стальным уголком, подшипниками, гайками и болтами.
ВАЖНО! Не берите алюминиевый, в таком случае надо быть готовым к частой замене детали. Дорожки в ней выедают шарикоподшипники каретки.
Предпочтение лучше отдать стальному уголку. Если использование механизма ожидается интенсивным, лучше его закалить и отшлифовать для снижения трения на подшипниках.
Штоки
Собирая маленький домашний станок, иногда пользуются, как направляющими, штоками автомобильных стоек из отечественного авто. Они прочны и изготовлены из металла высокого качества. Это ощутимо сократит затрату средств на стоимость комплектующих.
Шины
Есть и такой вариант: алюминиевые шины из распредустройства трансформаторной подстанции с впрессованными медно-графитными втулками от стартера МАЗа. А подвижные узлы делают из пневмоклапанов, которые применяются для управления пневмоцилиндрами.
При изготовлении направляющих и кареток для чпу своими руками (роликовых или шариковых), надо пользоваться такими ожидаемыми критериями:
- сохранение заданных параметров,
- плавное линейное перемещение кареток,
- эффективность работы,
- низкое трение.
ОБРАТИТЕ ВНИМАНИЕ! Некоторые умельцы советуют в механике на станке обойтись без втулок. Такой вариант возможен, но это чревато ухудшением производимых изделий, а сроки эксплуатации установленного устройства из стержней – снизятся.
Заключение
Если установленные комплектующие же умельцем подобраны или обработаны неточно, с таким устройством будут проблемы. Поэтому важно всегда учитывать эти рекомендации:
- в фрезеровке металлических или каменных заготовок, профильным рельсам нет замены,
- если строится станок с рабочим полем, превышающим 7 кв. м., лучше подобрать вариант профильных направляющих,
- в оборудовании по обработке мягких материалов с маленьким рабочим полем, меньшим формата А4, применим полированный вал с диаметром 16-25 мм.
Если направляющая соответствует всем критериям, и каретка по ней движется плавно и равномерно, то и работа такого узла будет правильная.

xn—-ntbhhmr6g.xn--p1ai
Большой портальный фрезерный станок с ЧПУ своими руками / Habr
Здравствуй дорогой читатель, в этой статье хочу поделиться своим опытом постройки фрезерного портального станка с числовым программным управлением.
Подобных историй в сети очень много, и я наверное мало кого удивлю, но может эта статья будет кому то полезна. Эта история началась в конце 2016 года, когда я со своим другом – партнером по разработке и производству испытательной техники аккумулировали некую денежную сумму. Дабы просто не прогулять деньги (дело то молодое), решили их вложить в дело, после чего пришла в голову идея изготовления станка с ЧПУ. У меня уже имелся опыт постройки и работы с подобного рода техникой, да и основной областью нашей деятельности является конструирование и металлообработка, что сопутствовало идее с постройкой станка ЧПУ.
Вот тогда то и началась движуха, которая длиться и по сей день…
Продолжилось все с изучения форумов посвященных ЧПУ тематике и выбора основной концепции конструкции станка. Предварительно определившись с обрабатываемыми материалами на будущем станке и его рабочим полем, появились первые бумажные эскизы, в последствии которые были перенесены в компьютер. В среде трех мерного моделирования КОМПАС 3D, станок визуализировался и стал обрастать более мелкими деталями и нюансами, которых оказалось больше чем хотелось бы, некоторые решаем и по сей день.
Одним из начальных решений было определение обрабатываемых на станке материалов и размеры рабочего поля станка. Что касается материалов, то решение было достаточно простым — это дерево, пластик, композитные материалы и цветные металлы (в основном дюраль). Так как у нас на производстве в основном металлообрабатывающие станки, то иногда требуется станок, который обрабатывал бы быстро по криволинейной траектории достаточно простые в обработке материалы, а это в последствии удешевило бы производство заказываемых деталей. Отталкиваясь от выбранных материалов, в основном поставляемых листовой фасовкой, со стандартными размерами 2,44х1,22 метра (ГОСТ 30427-96 для фанеры). Округлив эти размеры пришли к таким значениям: 2,5х1,5 метра, рабочее пространство определенно, за исключением высоты подъёма инструмента, это значение выбрали из соображения возможности установки тисков и предположили что заготовок толще 200мм у нас не будет. Так же учли тот момент, если потребуется обработать торец какой либо листовой детали длиной более 200мм, для этого инструмент выезжает за габариты основания станка, а сама деталь/заготовка крепится к торцевой стороне основания, тем самым может происходить обработка торца детали.
Конструкция станка представляет собой сборное рамное основание из 80-й профильной трубы со стенкой 4мм. По обе стороны длинны основания, закреплены профильные направляющие качения 25-го типоразмера, на которые установлен портал, выполненный в виде трех сваренных вместе профильных трубы того же типоразмера что и основание.
Станок четырех осевой и каждую ось приводит в движение шарико-винтовая передача. Две оси расположены параллельно по длинной стороне станка, спаренных программно и привязанных к Х координате. Соответственно оставшиеся две оси – это Y и Z координаты.
Почему именно остановились на сборной раме: изначально хотели делать чисто сварную конструкцию с закладными приваренными листами под фрезеровку, установку направляющих и опор ШВП, но для фрезеровки не нашли достаточно большого фрезерно-координатного станка. Пришлось рисовать сборную раму, чтобы была возможность обработать все детали своими силами с имеющимися на производстве металлообрабатывающими станками. Каждая деталь, которая подвергалась воздействию электродуговой сварки, была отожжена для снятия внутренних напряжений. Далее все сопрягаемые поверхности были выфрезерованны, и в последствии подгонки пришлось местами шабрить.
Залезая вперед, сразу хочу сказать, что сборка и изготовление рамы оказалась самым трудоемким и финансово затратным мероприятием в постройке станка. Первоначальная идея с цельно сваренной рамой по всем параметрам обходит сборную конструкцию, по нашему мнению. Хотя многие могут со мной и не согласиться.
Многие любители и не только, собирают такого рода и размера (и даже большего) станки у себя в мастерской или гараже, делая целиком сварную раму, но без последующего отжига и механической обработки за исключением сверления отверстий под крепление направляющих. Даже если повезло со сварщиком, и он сварил конструкцию с достаточно хорошей геометрией, то в последствии работы этого станка ввиду дребезга и вибраций, его геометрия будет уходить, меняться. Я конечно могу во многом ошибаться, но если кто то в курсе этого вопроса, то прошу поделиться знаниями в комментариях.
Сразу хочу оговориться, что станки из алюминиевого конструкционного профиля мы тут пока рассматривать не будем, это скорее вопрос другой статьи.
Продолжая сборку станка и обсуждая его на форумах, многие начали советовать сделать внутри рамы и снаружи диагональные стальные укосины для добавления еще большей жесткости. Мы этим советом пренебрегать не стали, но и добавлять укосины в конструкцию то же, так как рама получилась достаточно массивной (около 400 кг). А по завершению проекта, периметр обошъётся листовой сталью, что дополнительно свяжет конструкцию.
Давайте теперь перейдем к механическому вопросу этого проекта. Как было ранее сказано, движение осей станка осуществлялось через шарико–винтовую пару диаметром 25мм и шагом 10мм, вращение которой передается от шаговых двигателей с 86 и 57 фланцами. Изначально предполагали вращать непосредственно сам винт, дабы избавиться от лишних люфтов и дополнительных передач, но без них не обошлось в виду того, что при прямом соединении двигателя и винта, последний на больших скоростях начало бы разматывать, особенно когда портал находится в крайних положениях. Учитывая тот факт, что длина винтов по Х оси составила почти три метра, и для меньшего провисания был заложен винт диаметром 25мм, иначе хватило бы и 16 мм-го винта.
Этот нюанс обнаружился уже в процессе производства деталей, и пришлось быстрым темпом решать эту проблему путем изготовления вращающейся гайки, а не винта, что добавило в конструкцию дополнительный подшипниковый узел и ременную передачу. Такое решение так же позволило хорошо натянуть винт между опорами.
Конструкция вращающейся гайки довольно проста. Изначально подобрали два конических шарикоподшипника, которые зеркально одеваются на ШВП гайку, предварительно нарезав резьбу с ее конца, для фиксации обоймы подшипников на гайке. Подшипники вместе с гайкой вставали в корпус, в свою очередь вся конструкция крепится на торце стойки портала. Спереди ШВП гайки закрепили на винты переходную втулку, которую в последствии в собранном виде на оправке обточили для придания соостности. На неё одели шкив и поджали двумя контргайками.
Очевидно, что некоторые из вас, зададутся вопросом о том – «Почему бы не использовать в качестве механизма передающего движения зубчатую рейку?». Ответ достаточно прост: ШВП обеспечит точность позиционирования, большую двигающую силу, и соответственно меньший момент на валу двигателя (это то, что я с ходу вспомнил). Но есть и минусы – более низкая скорость перемещения и если брать винты нормального качества, то соответственно и цена.
Кстати, мы взяли ШВП винты и гайки фирмы TBI, достаточно бюджетный вариант, но и качество соответствующее, так как из взятых 9 метров винта, пришлось выкинуть 3 метра, ввиду несоответствия геометрических размеров, ни одна из гаек просто не накрутилась…
В качестве направляющих скольжения, были использованы профильные направляющие рельсового типоразмера 25мм, фирмы HIWIN. Под их установку были выфрезерованны установочные пазы для соблюдения параллельности между направляющими.
Опоры ШВП решили изготовить собственными силами, они получились двух видов: опоры под вращающиеся винты (Y и Z оси) и опоры под не вращающиеся винты (ось Х). Опоры под вращающиеся винты можно было купить, так как экономии ввиду собственного изготовления 4 деталей вышло мало. Другое дело с опорами под не вращающиеся винты – таких опор в продаже не найти.
Из сказанного ранее, ось Х приводится в движение вращающимися гайками и через ременную зубчатую передачу. Так же через ременную зубчатую передачу решили сделать и две другие оси Y и Z, это добавит большей мобильности в изменении передаваемого момента, добавит эстетики в виду установки двигателя не вдоль оси винта ШВП, а сбоку от него, не увеличивая габариты станка.
Теперь давайте плавно перейдем к электрической части, и начнем мы с приводов, в качестве них были выбраны шаговые двигатели, разумеется из соображений более низкой цены по сравнению с двигателями с обратной связью. На ось Х поставили два двигателя с 86-м фланцем, на оси Y и Z по двигателю с 56-м фланцем, только с разным максимальным моментом. Ниже постараюсь представить полный список покупных деталей…
Электрическая схема станка довольно проста, шаговые двигатели подключаются к драйверам, те в свою очередь подключается к интерфейсной плате, она же соединяется через параллельный порт LPT с персональным компьютером. Драйверов использовал 4 штуки, соответственно по одной штуке на каждый из двигателей. Все драйвера поставил одинаковые, для упрощения монтажа и подключения, с максимальным током 4А и напряжением 50В. В качестве интерфейсной платы для станков с ЧПУ использовал относительно бюджетный вариант, от отечественного производителя, как указанно на сайте лучший вариант. Но подтверждать или опровергать это не буду, плата проста в своем применении и самое главное, что она работает. В своих прошлых проектах применял платы от китайских производителей, они тоже работают, и по своей периферии мало отличаются, от использованной мной в этом проекте. Заметил во всех этих платах, один может и не существенный, но минус, на них можно всего лишь установить до 3-х концевых выключателя, но на каждую ось требуется как минимум по два таких выключателя. Или я просто не разобрался? Если у нас 3-х осевой станок, то соответственно нам надо установить концевые выключатели в нулевых координатах станка (это еще называется «домашнее положение») и в самых крайних координатах чтобы в случае сбоя или не хватки рабочего поля, та или иная ось просто не вышла из строя (попросту не сломалась). В моей схеме использовано: 3 концевых без контактных индуктивных датчика и аварийная кнопка «Е-СТОП» в виде грибка. Силовая часть запитана от двух импульсных источников питания на 48В. и 8А. Шпиндель с водяным охлаждением на 2,2кВт, соответственно включенный через частотный преобразователь. Обороты устанавливаются с персонального компьютера, так как частотный преобразователь подключен через интерфейсную плату. Обороты регулируются с изменения напряжения (0-10 вольт) на соответствующем выводе частотного преобразователя.
Все электрические компоненты, кроме двигателей, шпинделя и конечных выключателей были смонтированы в электрическом металлическом шкафу. Все управление станком производится от персонального компьютера, нашли старенький ПК на материнской плате форм фактора ATX. Лучше бы, чуть ужались и купили маленький mini-ITX со встроенным процессором и видеокартой. При не малых размерах электрического ящика, все компоненты с трудом разместились внутри, их пришлось располагать достаточно близко друг к другу. В низу ящика разместил три вентилятора принудительного охлаждения, так как воздух в нутрии ящика сильно нагревался. С фронтальной стороны прикрутили металлическую накладку, с отверстиями под кнопки включения питания и кнопки аварийного останова. Так же на этой накладке разместили панельку для включения ПК, ее я снял с корпуса старого мини компьютера, жаль, что он оказался не рабочим. С заднего торца ящика тоже закрепили накладку, в ней разместили отверстия под разъемы для подключения питания 220V, шаговых двигателей, шпинделя и VGA разъем.
Все провода от двигателей, шпинделя, а также водяные шланги его охлаждения проложили в гибкие кабель каналы гусеничного типа шириной 50мм.
Что касается программного обеспечение, то на ПК размещенного в электрическом ящике, установили Windows XP, а для управления станком применили одну из самых распространенных программ Mach4. Настройка программы осуществляется в соответствии с документацией на интерфейсную плату, там все описано достаточно понятно и в картинках. Почему именно Mach4, да все потому же, был опыт работы, про другие программы слышал, но их не рассматривал.
Технические характеристики:
Рабочее пространство, мм: 2700х1670х200;
Скорость перемещения осей, мм/мин: 3000;
Мощность шпинделя, кВт: 2,2;
Габариты, мм: 2800х2070х1570;
Вес, кг: 1430.
Список деталей:
Профильная труба 80х80 мм.
Полоса металлическая 10х80мм.
ШВП TBI 2510, 9 метров.
ШВП гайки TBI 2510, 4 шт.
Профильные направляющие HIWIN каретка HGh35-CA, 12 шт.
Рельс HGh35, 10 метров.
Шаговые двигатели:
NEMA34-8801: 3 шт.
NEMA 23_2430: 1шт.
Шкив BLA-25-5M-15-A-N14: 4 шт.
Шкив BLA-40-T5-20-A-N 19: 2 шт.
Шкив BLA-30-T5-20-A-N14: 2 шт.
Плата интерфейсная StepMaster v2.5: 1 шт.
Драйвер шагового двигателя DM542: 4шт. (Китай)
Импульсный источник питания 48В, 8А: 2шт. (Китай)
Частотный преобразователь на 2,2 кВт. (Китай)
Шпиндель на 2,2 кВт. (Китай)
Основные детали и компоненты вроде перечислил, если что-то не включил, то пишите в комментарии, добавлю.
Опыт работы на станке: В конечном итоге спустя почти полтора года, станок мы все же запустили. Сначала настроили точность позиционирования осей и их максимальную скорость. По словам более опытных коллег максимальная скорость в 3м/мин не высока и должна быть раза в три выше (для обработки дерева, фанеры и т.п.). При той скорости, которой мы достигли, портал и другие оси упершись в них руками (всем телом) почти не остановить — прёт как танк. Начали испытания с обработки фанеры, фреза идет как по маслу, вибрации станка нет, но и углублялись максимум на 10мм за один проход. Хотя после заглубляться стали на меньшую глубину.
По игравшись с деревом и пластиком, решили погрызть дюраль, тут я был в восторге, хоть и сломал сначала несколько фрез диаметром 2 мм, пока подбирал режимы резания. Дюраль режет очень уверенно, и получается достаточно чистый срез, по обработанной кромке.
Сталь пока обрабатывать не пробовали, но думаю, что как минимум гравировку станок потянет, а для фрезеровки шпиндель слабоват, жалко его убивать.
А в остальном станок отлично справляется с поставленными перед ним задачами.
Вывод, мнение о проделанной работе: Работа проделана не малая, мы в итоге изрядно приустали, так как ни кто не отменял основную работу. Да и денег вложено не мало, точную сумму не скажу, но это порядка 400т.р. Помимо затрат на комплектацию, основная часть расходов и большая часть сил, ушла на изготовление основания. Ух как мы с ним намаялись. А в остальном все делалось по мере поступления средств, времени и готовых деталей для продолжения сборки.
Станок получился вполне работоспособным, достаточно жестким, массивным и качественным. Поддерживающий хорошую точность позиционирования. При измерении квадрата из дюрали, размерами 40х40, точность получилась +- 0,05мм. Точность обработки более габаритных деталей не замеряли.
Что дальше…: По станку есть еще достаточно работы, в виде закрытия пыле — защитой направляющих и ШВП, обшивки станка по периметру и установки перекрытий в середине основания, которые будут образовывать 4 больших полки, под объем охлаждения шпинделя, хранения инструмента и оснастки. Одну из четвертей основания хотели оснастить четвертой осью. Также требуется на шпиндель установить циклон для отвода и сбора стружки о пыли, особенно если обрабатывать дерево или текстолит, от них пыль летит везде и осаждается повсюду.
Что касается дальнейшей судьбы станка то тут все не однозначно, так как у меня возник территориальный вопрос (я переехал в другой город), и станком заниматься сейчас почти некому. И вышеперечисленные планы не факт что сбудутся. Не кто этого два года назад и предположить не мог.
В случае продажи станка с его ценником все не понятно. Так как по себестоимости продавать откровенно жалко, а адекватная цена в голову пока не приходит.
На этом я пожалуй закончу свой рассказ. Если что-то я не осветил, то пишите мне, и я постараюсь дополнить текст. А в остальном многое показано в видео про изготовления станка на моем YouTube канале.
habr.com
Самодельный фрезерный ЧПУ станок из мебельных направляющих. Механика
Как вы уже знаете последнее время я собираю ЧПУ станки . Первый станок я собрал из всяких ненужных вещей и обошелся он мне всего 3000 руб. Лазерный гравировальный станок с ЧПУ я собрал вторым. Сейчас я приступил к сборке боле мене качественного фрезерного станка с ЧПУ. В данной статье пойдет речь как и из чего я его собирал.
Для сборки
станка я купил фанеру толщиной 16 мм. И
начел ее раскраивать на детали похожие,
как я делал для лазерного станка, только
пришлось учесть пару моментов. Это то
что ведущие валы всего 600 мм. И
станок
должен получиться так чтобы валы не
были маленькими. Чуть больше ни чего
страшного. Самое проблематичное было
рассчитать размеры заготовок для оси
Y так как это общий каркас станка и от
него зависит не только ось Y но и ось X.
В качестве направляющих выбрал мебельные направляющие длиной 600 мм. Установил на основания ЧПУ станка .
На направляющие установил лист фанеры . А поверх установил мебельного ламината. У вас наверное возник вопрос для чего мебельный ламинат. А дело в том, что в мебельном ламинате я планирую сделать фиксаторы для материала. И также при фрезеровании фреза будит портить основание стола. А тут поменял лист мебельного ламината и работаешь дальше.
Ответную часть для ведущего вала сделал следующим образом. Отфрезеровал отверстия для латунной гайки и стянул винтами М3 заготовки из фанеры. Вот такой бутерброд получился.
Установил мебельные направляющие на ось X примерно по тому же принципу что и на ось Y.
Чтобы закрепить горизонтальные направляющие пришлось сверху станка и в заранее подготовленный выступ установить два куска фанеры. А после закрепить мебельные направляющие. Ответную часть сделал аналогично оси Y.
Для того чтобы сделать ось Z установил на ось X небольшой кусок мебельного ламината. Перпендикулярно закрепил заготовки из фанеры для крепления мебельных направляющих.
На данной оси решил использовать всего 1 пару мебельных направляющих. Так как тут я их закрепил перпендикулярно оси X и плюс кусок фанеры установил достаточно плотно между направляющими. Поэтому хождений практически нет. Если возникнут проблемы с данной конструкцией ни когда не поздно ее переделать.
Все шаговые двигателя установил на самодельные крепления сделанные из корпуса видео магнитофона.
Сделал из фанеры крепления для гравера . В итоге у меня получилось вот такой самодельный фрезерный станок с ЧПУ.
В следующем видео буду устанавливать электронику на самодельный фрезерный ЧПУ станок. Не пропустите!
Подписывайтесь на мой канал на Youtube и вступайте в группы в Вконтакте и Facebook.
Спасибо за внимание!
Понравилась статья? Поделитесь ею с друзьями:
portal-pk.ru
Выбор направляющих для станка с ЧПУ
В данной статье будут рассмотрены виды направляющих для станка с ЧПУ, их основные особенности и преимущества.
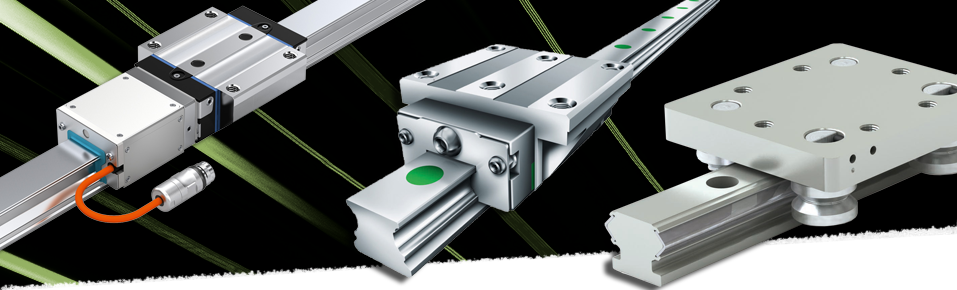
НАПРАВЛЯЮЩИЕ ПОЛИРОВАННЫЕ ВАЛЫ
Самый распространенный и бюджетный вид направляющих. Отличается низкой стоимостью, легкостью обработки и установки.
Полированные валы изготавливаются из высоколегированных сталей, как правило — конструкционных подшипниковых, и проходят индукционную закалку поверхности с последующей шлифовкой.
Это обеспечивает продолжительное время работы и сопутствует меньшему износу вала.
Шлифованные валы имеют идеальную поверхность и обеспечивают движение с очень маленьким трением.
Валы крепятся только в 2 точках на концах, и поэтому монтаж их не представляет особой сложности.
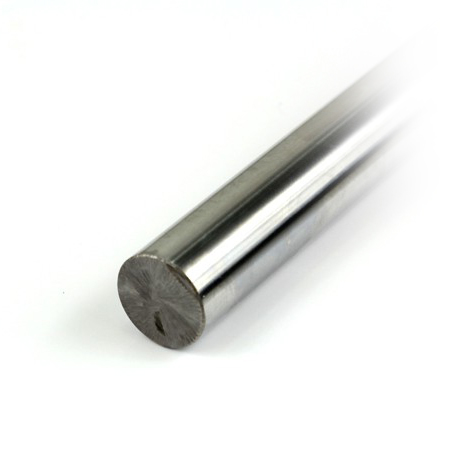
Полированные валы
Однако многие недобросовестные производители часто делают валы из дешевых и мягких сортов высокоуглеродистых сталей, пользуясь тем, что покупатель не всегда обладает средствами для проверки вида материала и его твердости.
К недостаткам полированных валов относятся:
1. Отсутствие крепления к станине.
Вал крепится в двух точках на концах — это облегчает монтаж направляющих, однако приводит к тому, что направляющие устанавливаются независимо от рабочей поверхности стола. В то же время в портальных станках крайне желательно ставить направляющие в жесткой связи со столом. Такая связь снижает погрешности обработки, если рабочий стол подвергался искривлению, «повело винтом» — направляющие, повторяя изгибы стола, нивелируют часть погрешности.
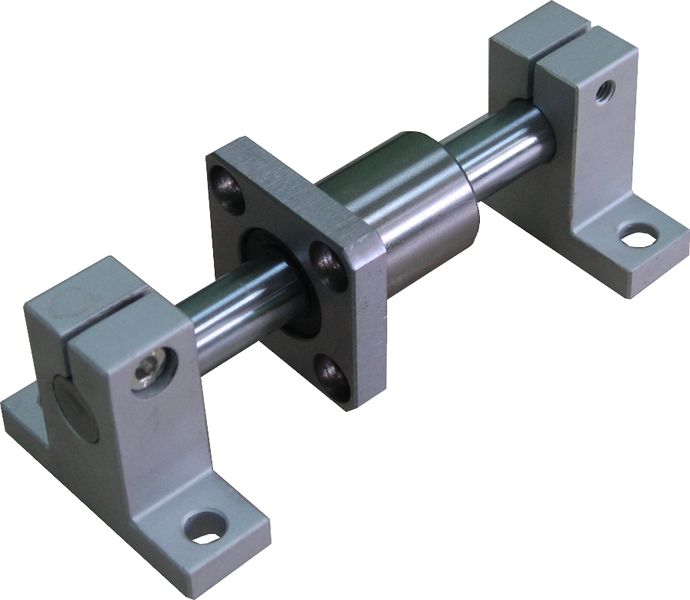
Крепление вала
2. Провисание на большой длине.
На практике из-за провисания валы используют длиной не более 1 метра. Кроме того, важно отношение диаметра вала к его длине — для получения приемлемых результатов его значение должно быть не менее 0.05, желательно в пределах 0.06—0.1. Более точные данные можно получить, произведя моделирование нагрузки на вал в пакетах САПР.
Виды линейных подшипников на вал:
1. Шариковые втулки
Линейные подшипники качения имеют большие люфты по сравнению с каретками рельсовых направляющих и меньшие нагрузочные характеристики.
Помимо этого для защиты от поворота каретки необходимо использовать как минимум два направляющих вала на одну ось. Недостатки линейных подшипников качения:
- Низкая грузоподъемность.
- Cледствие предыдущего пункта, а также конструктивного строения линейных подшипников.
- Недолговечность.
- Каждый шарик линейного подшипника касается вала в одной точке, что создает очень высокое давление. Со временем шарики могут прокатать канавку на валу, после чего вал подлежит замене.
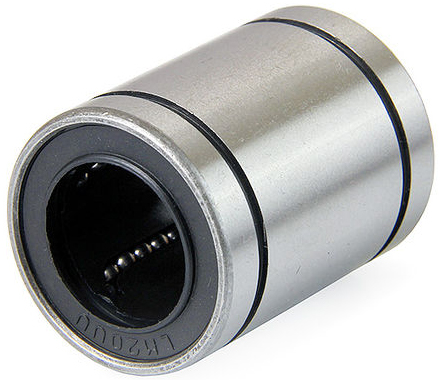
Шариковые втулки
- Люфт
- Бюджетные линейные подшипники многими производителями изготавливаются зачастую с весьма существенным люфтом.
- Достаточно чувствительны к пыли и стружке на валу
2. Линейные подшипники скольжения
Втулки скольжения используют трение скольжения и изготавливаются из бронзы, латуни, капролона и иных материалов.
При должном соблюдении допусков бронзовый подшипник скольжения не уступает подшипнику качения в точности и грузоподъемности, и при этом легче переносит пыль и стружку. Однако необходимо быть уверенным, что вы всегда сможете достать материал для подшипника и обработать его как нужно.
Кроме того, периодически, по мере износа подшипник скольжения приходится подгонять для устранения зазоров. В большинстве случаев шариковая втулка предпочтительней для начинающих, по причине их высокой доступности и взаимозаменяемости.
ШЛИЦЕВЫЕ ВАЛЫ (BALL SPLINE)
Шлицевые валы имеют специальные дорожки качения для шариков втулки. Они более износостойкие и жесткие, чем обычные валы, а также могут воспринимать крутильные усилия с втулки.
Сочетая в себе преимущества монтажа валов, износостойкость профильных рельсов с возможностью создания натяга, шлицевые валы находят применение там, где требуется монтаж направляющих исключительно на концах.
Однако, из-за их существенно более высокой стоимости (по сравнению с полированными валами) они редко применяются в строении обычных станков.
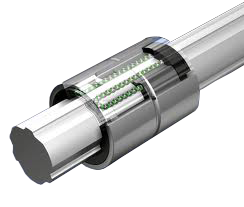
Шлицевый вал
ВАЛЫ НА ОПОРЕ
Линейные валы на опорах (цилиндрические рельсы) служат для поддержки направляющей по всей длине, что предотвращает её прогиб под воздействием нагрузки или собственного веса при большой длине и массе движущейся каретки.
Цилиндрические рельсы крепятся непосредственно на станок.
Отверстия с резьбой в опоре выполнены специально для удобного крепления и обеспечивают надежную фиксацию направляющей на станине.
Цилиндрические рельсы имеют общие недостатки с полированными валами — высокий люфт у втулок, недолговечность. Однако цилиндрические рельсы уже не провисают на длине, и имеют большую грузоподъемность.
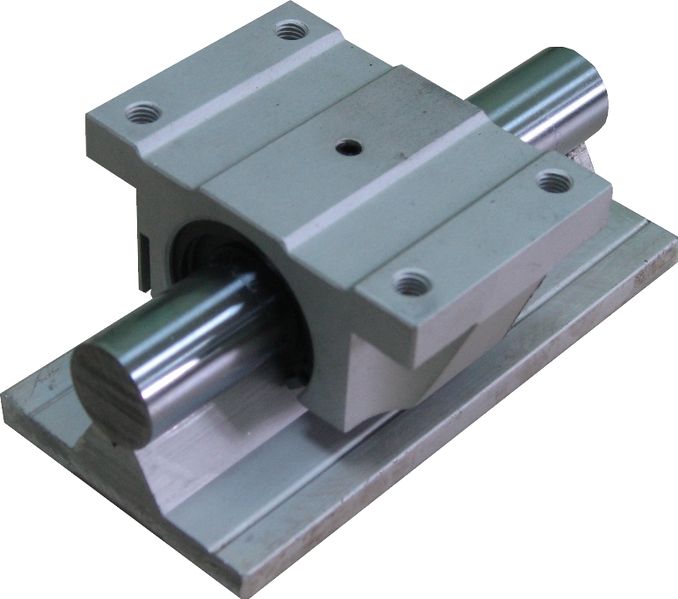
Вал на опоре
В отличие от линейных подшипников на валы, каретки на цилиндрические рельсы реагируют на разнонаправленные нагрузки по-разному.
Это происходит потому, что шариковые втулки на вал — замкнутые по контуру, а каретки на рельсы — нет. Этот эффект может привести, например, к тому, что небольшой станок с тяжелым шпинделем на цилиндрических рельсах может показать точность хуже, чем аналогичная конструкция на валах.
Валы и цилиндрические рельсы просты в производстве. По этой причине существует множество именитых и безымянных производителей данного продукта, и качество, и параметры разнятся соответственно в весьма широких пределах. Бывает так, что каретки одного и того же безымянного производителя не подходят к его же валам из другой партии.
ШАРИКОВЫЕ ПРОФИЛЬНЫЕ РЕЛЬСОВЫЕ НАПРАВЛЯЮЩИЕ
Профильные рельсовые направляющие используются там, где требуется высокая точность. Так же как и цилиндрические, профильные рельсы крепятся непосредственно на станину станка.
В профильных рельсах сделаны специальные дорожки качения. В результате нагрузка на каретку распределяется по рабочей поверхности дорожек качения равномерно — профиль касания шарик-рельс уже не точка, а дуга.
Профильные рельсы отличаются высокой точностью и прямолинейностью, отменной грузоподъемностью, высокой износоустойчивостью, низким люфтом или полным его отсутствием.
Недостатком профильных направляющих является высокие требования к шероховатости и прямолинейности места крепления, а также сложность установки.
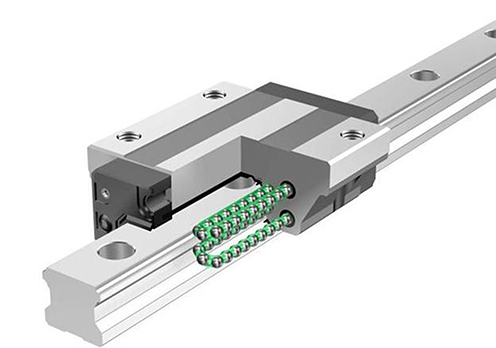
Шариковая направляющая
Как правило, рельсы и каретки выпускаются в нескольких вариантах — с преднатягом и грузоподъемностью разной степени.
Классическим примером могут служить рельсовые направляющие Hiwin и THK.
Профильные рельсы сложны и дороги в производстве, поэтому производителей рельсов меньше, чем производителей валов. Они, как правило, дорожат своей репутацией, потому качество профильных рельсов гораздо стабильней.
Мы рекомендуем всегда, когда это возможно, использовать именно профильные рельсовые направляющие известных брендов для построения станков с ЧПУ.
РОЛИКОВЫЕ ПРОФИЛЬНЫЕ РЕЛЬСОВЫЕ НАПРАВЛЯЮЩИЕ
Роликовые рельсы являются подвидом профильных направляющих, у которых дорожки качения — плоские, а вместо шариков в опорных модулях использованы ролики.
Это позволило увеличить жесткость направляющей, грузоподъемность и долговечность.
Роликовые направляющие используются в высоконагруженных металлообрабатывающих станках с ЧПУ, предназначенных для фрезеровки черных металлов, стали, камня.
Вряд ли Вы ищете именно такие направляющие, иначе Вы бы не читали данную статью.
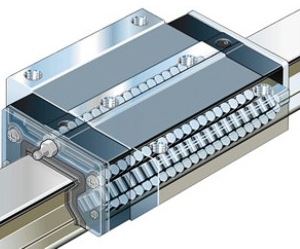
Роликовая направляющая
НАПРАВЛЯЮЩИЕ «ЛАСТОЧКИН ХВОСТ»
И ПРИЗМАТИЧЕСКИЕ НАПРАВЛЯЮЩИЕ
Этот вид направляющих применяется там, где нужна очень высокая жесткость, например, в промышленных металлообрабатывающих станках.
В направляющих типа «ласточкин хвост» контактирующие поверхности плоской формы скользят друг по другу, чем достигается большая площадь контакта.
«Ласточкин хвост» не является съемным, а выполняется в виде единого целого со станиной.
Изготовление, так же как и ремонт «ласточкина хвоста» — весьма сложная и трудемкая операция, а замене ЛХ не подлежит.
«Ласточкин хвост» практически не используется в хоббийном станкостроении по упомянутой совокупности причин.
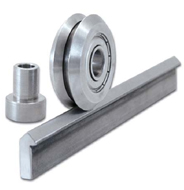
V-образная направляющая
ПОДВОДЯ ИТОГИ
При выборе направляющих обращайте внимания на следующие моменты:
- вал вал и бронзовая втулка — низкая жесткость и грузоподъемность, ограниченная точность, необходимость в периодической подгонке, низкая цена, малая доступность готовых изделий на рынке. Вал провисает при большой длине.
- вал и пластмассовая втулка — низкая жесткость и грузоподъемность, низкая точность, необходимость в периодической подгонке, низкая цена, высокий износ, малая доступность готовых изделий на рынке. Вал провисает при большой длине.
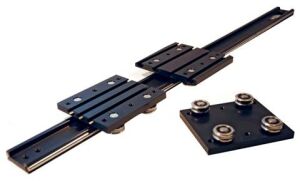
Роликовая профильная направляющая
- Вал и шариковая втулка — низкая жесткость и грузоподъемность, ограниченная точность, средняя стоимость. Вал провисает при большой длине. Используются в хоббийных станках и станках среднего класса.
- Вал на опоре и шариковая втулка — средняя жесткость и грузоподъемность, ограниченная точность, средняя стоимость. Рельс повторяет деформации станины, нивелируя погрешность. Используются в хоббийных станках и станках среднего класса.
- Профильные направляющие — высокая жесткость, точность, износостойкость, высокая грузоподъемность, не требуется регулировка, высокая стоимость. Немаловажный фактор — сложность монтажа профильных направляющих и необходимость соответствующей подготовки монтажных поверхностей. Используются в станках среднего и промышленного класса.
Если Вы все прочитали, но ситуация не стала яснее, в заключение несколько конкретных рекомендаций:
- Если на станке планируется фрезеровать металлы или камень — альтернативы профильным рельсам нет.
- Если ваш станок будет иметь рабочее поле больше, чем 0,7 кв. м, лучше всего также применить профильные направляющие.
- Если ваш станок имеет рабочее поле меньше, чем формат А4, планируется обрабатывать мягкие материалы — подойдут валы диаметром 16–25 мм.
- Если Вы все еще затрудняетесь с выбором, обратитесь за консультацией к нашим специалистам.
purelogic.ru