Форматно-раскроечный станок своими руками: чертежи, видео, фото
При рассмотрении того, какое оборудование требуется для качественного самостоятельного изготовления мебели следует обратить внимание на форматно-раскроечный станок. Многие специалисты утверждают, что форматно-раскроечный станок при необходимости можно сделать самостоятельно. Рассмотрим все особенности самостоятельного создания станка для обработки дерева.


Предназначение форматно-раскроечного станка
Форматно-раскроечный станок используется для раскроя в поперечном или продольном направлении с возможностью выдерживания заданного угла, а также обрезки и раскроя щитовых заготовок.
К особенностям использования форматно-раскроечного станка можно отнести:
- При его использовании можно получить готовую продукцию высокого качества. Это связано с тем, что раскройка и другие технологически процессы проходят с высокой точностью.
- Предназначение станка кроется в задаче основных параметров оборудованию, после чего деталь будет более подготовленной к дальнейшей обработке.
- Некоторые модели могут проводить поштучную раскройку, другие предназначены для обработки целого пакета.
При рассмотрении функционала достаточно важно обратить внимание на то, с какими материалами может работать форматно-раскроечный станок. Самодельный и промышленный вариант исполнения рассматриваемого оборудования предназначен для работы с:
- ДСП, ДВП, МДФ;
- облицовочным пластиком и композитными листовыми материалами;
- порода массива дерева не определяет возможность использования оборудования;
- заготовки из шпона и меламина также могут обрабатывать на форматно-раскроечной станке;
- ламинированный и бумажные заготовки.
Существенным ограничением по области применения можно назвать то, что заготовка должна иметь точные геометрические размеры, то есть массив дерева или другой материл должен пройти первичную обработку.
Целесообразно использовать форматно-раскроечный станок на мелкосерийном производстве. Многие мелкие, средние и достаточно крупные фабрики по производству мебели устанавливают подобное оборудование с автоматизированной системой обработки. Для бытового применения в большей степени самодельный вариант исполнения, так как он будет обладать меньшей стоимостью, а процесс наладки и обслуживания можно провести самостоятельно. В домашней мастерской многие решают установить самодельный форматно-раскроечный станок по причине того, что он проводит раскройку заготовок с высокой точностью и качеством. При использовании обычной пилорамы есть вероятность нарушения правильности геометрии, а также торцевая поверхность может иметь другого рода дефекты.
Особенности конструкции
Для того чтобы сделать раскроечный станок своими руками следует разобраться с его конструктивными особенностями. Следует отметить, что стандартная конструкция представлена следующими узлами:
- Станина – элемент, служащий основанием для всей конструкции. Также станина предназначена для гашения части вибрации.
- Рабочего подвижного и неподвижного стола.
- Пильного узла, который состоит из 2-х пильных дисков, регулируемых фиксаторв.


Основные узлы оборудования
Подвижный стол имеет достаточно сложную конструкцию, которая состоит из тележки, опорной рамы, линейки, сепаратора, каретки. Практически все узлы изготавливаются из металла.
Пильный узел
Важным элементом конструкции можно назвать пильный узел. Самодельный вариант исполнения зачастую представлен сварной конструкцией, так как подобный метод соединения элементов позволяет эффективно бороться с вибрацией, возникающий при пилении. Главной проблемой рассматриваемого технологического процесса является образование на облицовке сколов, которые снижают качество получаемого материала. Именно поэтому пильный узел имеет два пильных диска, что и позволяет исключить вероятность появления проблемы.


Устройство пильного узла
К особенностям пильного агрегата можно отнести:
- Узел цельный, зачастую его отливают из чугуна.
- Некоторые модели могут иметь один электродвигатель, но зачастую устанавливают два – для каждой пилы.
- Ременная передача используется для того чтобы привести в движение подрезной диск. Отметим, что наличие ременной передачи – обязательное условие обеспечения длительной работы электродвигателя, так как подобный способ передачи усилия позволяет сгладить нагрузку, оказываемую на выходной вал электродвигателя.
- Диаметр пильных дисков может достигать 120 миллиметров. Изготавливают их из инструментальной стали, так как она более устойчива к истиранию.
- Электродвигатель через ременную передачу с различными шкивами должен обеспечивать до 8000 об/мин. Отметим, что чем выше показатель, тем более качественную поверхность можно получить. Однако повышение частоты приводит к уменьшению величины подачи и возникновению конструкционных проблем из-за оказания большой нагрузки на узел.
Важно отметить тот момент, что сделанный своими руками вертикальный форматно станок может иметь поворотный пильный узел. Сделать его достаточно сложно, необходим для проведения распила под углом.
Основная пила
Разрабатывая форматно раскроечный станок дома своими руками чертежи следует учитывать, что вращение основной пилы должно быть с частотой 4-6 тысяч оборотов в минуту. При снижении показателя есть вероятность повреждения кромки. Если при создании конструкции использовать современный электродвигатель, то есть возможность регулировать чистоту вращения согласно особенностям обрабатываемого материала. Мощность электродвигателя должна варьировать в пределе от 3 до 5 кВт. С увеличением показателя мощности существенно повышается производительность, но также и расходы из-за потребления большего количества электричества. Провести регулировку можно также путем подбора шкивов ременной передачи, однако подобная перенастройка форматно-раскроечного станка требует определенного времени и расчетов.
В большей части моделей высота пропила и положение пилы регулируется путем передвижения всего пильного агрегата. При этом обеспечить подобную регулировку можно двумя основными методами:
- по вертикальным направляющим;
- за счет качения вокруг горизонтальной оси.
Также важным параметром можно назвать то, на какую высоты подымается пила относительно стола, так как этот показатель определяет максимальную толщину пропила.
Для перемещения заготовки во многих случаях используется роликовая тележка. Тележка движется по стальным направляющим, для чего в конструкцию включены сепаратор с шариками или роликами. Компенсаторы и регуляторы могут выглядеть различным образом, все зависит от достигаемой точности и качества при обработке.
Особенности подвижного стала
Большие трудности возникают при создании подвижного стола. Эта поверхность выступает в качестве базирующей поверхности, поэтому она должна выдерживать оказываемое воздействие. Нагрузка оказывается на саму каретку и соединительный элемент.
- Габаритный 3D-чертеж
- Габаритный чертеж форматного станка и картеки
Из-за конструктивных особенностей на месте контакта шариков и роликов возникает довольно большая нагрузка. Именно поэтому создавая свой форматно-раскроечный станок следует использовать специальные направляющие, которые не создают люфт при работе. От этого напрямую зависит точность обработки.
В качестве направляющих могут использоваться:
- ролики;
- шарики;
- комбинация роликов и шариков.
Наиболее популярной схемой является сочетание алюминиевой каретки и стальных направляющих, на которые устанавливаются линейные подшипники.
При самостоятельном изготовлении направляющих следует учитывать нижеприведенные моменты:
- сами направляющие могут быть выполнены в виде стальных полос;
- встраивание направляющих проводится таким образом, чтобы можно было размещать шарики в два канала.
Рассматриваемая схема позволяет раскрыть возможности рассматриваемого оборудования, так как нагрузка может эффективно гаситься в любом направлении. Для того чтобы они работали на протяжении нескольких лет следует выбирать материал для их изготовления, который был подвержен термической обработке.
В последнее время направляющие стали изготавливать из пластика. Достигнуть необходимой точности передвижения можно только в случае использования алюминиевого профиля с большим количеством внутренних ребер.
В заключении при рассмотрении вопроса того, как сделать форматно раскроечный станок отметим то, что самодельные варианты исполнения по показателю точности и функциональности существенно уступает моделям промышленного производства. Это связано с тем, что из-за наличия большого количества подвижных элементов существенно понижается жесткость конструкции. Самостоятельно создать направляющие, которые будут обеспечивать точное базирование заготовки, достаточно сложно.
Если вы нашли ошибку, пожалуйста, выделите фрагмент текста и нажмите Ctrl+Enter.
Форматно-раскроечный станок своими руками: чертежи, фото, видео
Содержание статьи:
Во время изготовления корпусной мебели применяются различные типы инструментов. Для получения ровных заготовок необходимо форматно-раскроечное оборудование. В большинстве случаев небольшое производство не имеет возможности приобрести этот станок. Поэтому в качестве альтернативы можно рассмотреть вариант самостоятельного изготовления.
Назначение форматно раскроечного станка
Заводской форматно-раскроечный станок
Основные функции форматно-раскроечного станка заключаются в формировании ровного реза на поверхности ламинированного ДСП или ДВП. При этом предъявляются особые требования к качеству кромки.
Внешне конструкция напоминает простую пилораму. Разница заключается в жесткой фиксации заготовки относительно режущих компонентов. Для увеличения качества присутствуют два диска различных диаметров. Один из них больше другого и вращается в обратную сторону. Это дает возможность уменьшить вероятность появления сколов на торце деревянной поверхности.
- устойчивость оборудования во время работы;
- наличие измерительных инструментов для предварительной раскройки деревянного листа.
- размеры рабочего стола. Они напрямую зависят от габаритов заготовки;
- меры безопасности. Это относится к оборудованию и рабочему персоналу. Для удаления стружки обязательно должен присутствовать вытяжной механизм, режущие компоненты находятся под специальным чехлом.
Важным фактором является предварительный расчет всех элементов конструкции. Она должна выполнять свои функции в зависимости от степени нагрузки. Одним из недостатков форматно-раскроечного станка является невозможность формирования резов фигурной формы. Для этого необходимы другие типы оборудования.
Во время анализа заводских моделей следует учитывать толщину обрабатываемого материала и его удельную плотность. Это повлияет на выбор пильных дисков.
Конструкция самодельного форматно раскроечного станка
Блок реза станка
Следующим этапом проектирования является разработка оптимальной схемы изготовления. Лучшим вариантом будет детальный анализ заводских самодельных моделей для создания уникального оборудования для мебельной мастерской.
Основным рабочим компонентом является блок реза, который состоит из двух пильных дисков, электродвигателя и раструба для подключения к стружкопылесосу. Для комплектации станков рекомендуется приобретать заводскую модель этого блока, так как самостоятельное изготовление может повлечь за собой возникновение трудностей в работе оборудования.
Компоненты, которыми должен обладать форматно раскроечный станок своими руками:
- станина. Является основным корпусом оборудования, на который в дальнейшем будут монтироваться остальные элементы. Чаще всего это трубчатые конструкции с регулировочными ножками;
- рабочий стол. На него устанавливается заготовка. Основные требования к материалам: идеально ровная поверхность, отсутствие дефектов, способных повредить ламинированный лист;
- прижимы для заготовки. Они необходимы для фиксации деревянного листа для обрезания его части определенного размера;
- подвижная каретка. Это несущий элемент для пильного блока. Чаще всего изготавливается из двутавровой балки или двух труб круглого сечения;
- защитные кожухи.
Это самая простая конструкция форматно-раскроечного станка, которую можно сделать своими руками из подручных материалов. Одним из главных условий их выбора является надежность и возможность выдерживать механические нагрузки, постоянную вибрацию. Любой самодельный форматник должен отвечать этим требованиям.
В некоторых конструкциях пильные диски располагаются по разным сторонам относительно заготовки. Отрезной находится внизу, а основной вверху. Это значительно улучшает качество реза, но усложняет процесс изготовления.
Порядок изготовления форматно раскроечного станка
Самодельный форматно-раскроечный станок
После составления оптимальной схемы и выбора комплектующих можно приступать непосредственно к процессу производства оборудования. Для этого потребуется сварочный аппарат, болгарка с диском по металлу, электродрель, измерительный инструмент.
Сначала изготавливается станина. Для этого применяются трубы квадратного или круглого сечения. Они обрезаются согласно схеме изготовления и крепятся между собой с помощью струбцин. После проверки размеров и правильного расположения компонентов можно приступать к сварке. Для увеличения жесткости конструкции рекомендуется установить несколько профилей между ножками станины.
Последующие этапы самостоятельного изготовления форматно-раскроечного станка.
- Подвижная каретка. Сначала устанавливаются направляющие. Это может быть балка или две трубы круглого сечения соединенные между собой. В конструкции самой каретки должны присутствовать ролики для плавного передвижения.
- Рабочий стол. Помимо требований к его поверхности стол является компонентом устойчивости всей конструкции. Специалисты рекомендуют делать его из двух материалов. Основа изготавливается из стального листа толщиной не менее 3 мм, рабочая поверхность — из листа ДСП, на ней же крепятся измерительные линейки.
- Прижимы для листов. Это может быть рычажный механизм любой конфигурации. Определяющим условием является относительно большая площадь фиксирующих компонентов. Давление на поверхность заготовки не должно оказать разрушающего воздействия.
В качестве дополнительных компонентов можно сделать узел изменения высоты дисков относительно поверхности деревянного листа. Для этого необходимо предусмотреть механизм подъема и последующей фиксацией блока резки относительно заготовки. На практике подобные механизмы не делают. Это обусловлено значительным повышением трудоемкости работ, закупки дополнительных комплектующих или их самостоятельное изготовление.
По окончании изготовления режущий блок подключается к стружкоотсосу. Перед полноценной эксплуатацией следует провести ряд испытательных работ. Во время выполнения контролируется качество реза, плавный ход пилы, отсутствие ощутимых вибраций.
В видеоматериале показан самодельный станок в процессе работы:
Примеры чертежей и фото
Форматный станок для начинающих | Блог Андрея Лаппо
Форматно-раскроечные станки – это один из основных видов необходимого оборудования для изготовления мебели. Раскрой плит ДСП, ДВП и МДФ и других листовых материалов производится с помощью форматно-раскроечных станков.
Одно из основных свойств форматников – точность распила, так как этот параметр оказывает большое влияние на качество изготовляемой мебели.
Без форматно-раскроечного станка в мебельном производстве делать нечего, но не у всех есть возможность начать бизнес с покупки хорошего оборудования. И тут на помощь приходит бесценный опыт товарищей-мебельщиков, которые с удовольствием делятся своими наработками на форуме мебельщиков.
Рассмотрим изобретение пользователя DokaLe, это НЕ первый его форматник, потому в данном варианте учтен опыт предыдущей работы над станком. Станок обеспечивает достаточно высокую точность раскроя, 0.1 мм при прямолинейной обработке по длине 2750мм, что является отличным показателем для самодельного оборудования. Сам станок занимает места меньше чем «заводские» образцы, длина станка составляет 4,5 метра и умещается в гараже размерами от стены до стены 6м, в то время когда для размещения «заводского» станка необходимо порядка 7 м. что является причиной поиска помещений с более высокой арендной платой.
Пильный узел с коробом для сбора опилок. Обратите внимание, что диски крутятся «друг на друга».
Пульт управления.
Линейка, с ограничительным прижимом.
Прижимы.
Станина.
Посмотрите видео ролик о работе данного станка:
Перед тем как продолжить расссказ про данный станок, хочу показать, как выглядел предыдущий вариант. Он был очень прост в изготовлении и имеет низкую себестоимость. Проработал 10 лет.На станке стоят дешевые китайские диски АТАКА, но пилят они почти без сколов. Каретка перемещается с помощью 12 подшипниковых колес от болгарского накопителя на магнитных носителях. На каждый пильный диск был установлен отдельный двигатель.
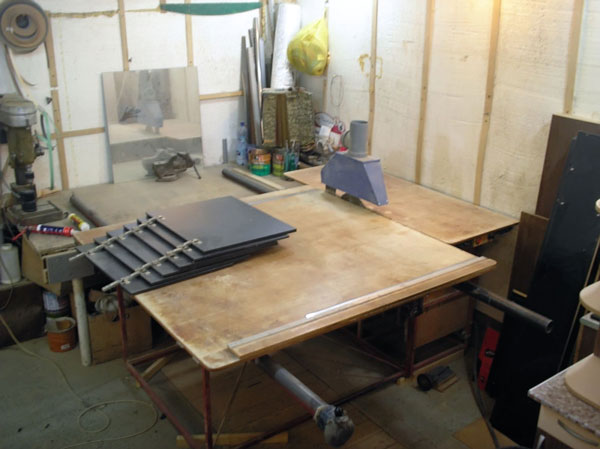
Станина.

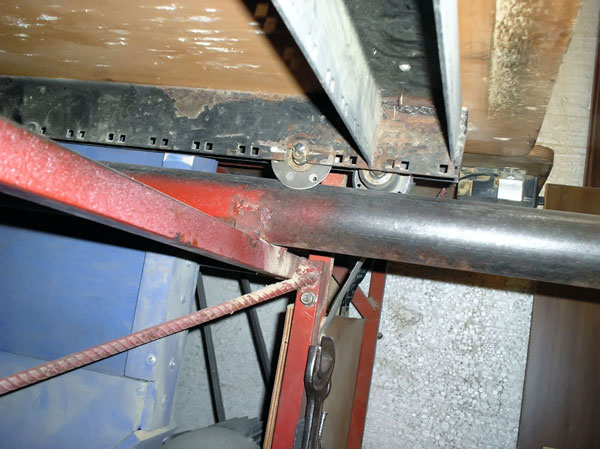
Перемещение каретки.


Вал с ременной передачей.
Итак, вернемся к новой модели. Станок позволяет обрабатывать детали с длиной пропила 2770мм, при длине стандартного листа 2750мм. Если необходимо распилить лист длиной 3500 мм. тогда потребуется его предварительно распилить на две части.
На станке предусмотрен расклинивающий нож, и это не случайно.
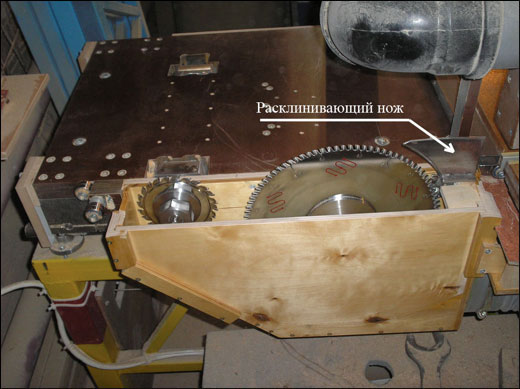
При обкатке нового станка отлетел обрезок (100х100мм) по ходу основной пилы. После экспериментов стало понятно, что обрезок подкидывает задним фронтом основной пилы и выкидывает вперед на подающего материал. (на видео есть момент без расклинивающего ножа и корпуса), после чего поставили нож. Это единственная его функция при данной конструкции станка.
Дело в том, что листы ЛДСП имеют внутреннее напряжение. Особенно это заметно на залежалых деталях или отсыревшем материале. Такой материал после пропила основным диском, начинает сжимать пропиленную щель. Если лист большой, то обратным ходом диска может поколоть лицевую сторону матераила. Если деталька маленькая, то ее может подбросить вверх. Поэтому расклинивающий нож необходим. Толщина ножа должна быть не меньше ширины диска, тоесть примерно 4 мм.
Рассмотрим более подробно из чего состоит станок и основные характеристики:
— двигатель основного вала – АИРЕ 80, 220В, 2800 об/мин, 2,2 кВт;
— двигатель подрезного узла – АИРЕ 71, 220В, 2800 об/мин, 1,1 кВт;
— ступенчатая скорость каретки обеспечивается двигателем постоянного напряжения 36В;
— редуктор червячный самый маленький из серии, 28-й, итальянского производства, оказался дешевле российского аналога почему-то.
На редукторе два шкива с двух сторон, каретка передвигается при помощи двух трехмиллиметровых тросиков в оплетке. На основном валу получаем скорость вращения 3500 об/мин, установлен клиновой ремень. Для подрезки получается более скоростной выход — 5800 об/мин, установлен поликлиновой ремень на 8 ручьев.
Основная пила имеет подъем 0-52мм, подрезная 0-4мм. Наклона пилы под углом нет. В качестве направляющих выступает калиброванный прут 25мм длиной 4,2 метра.
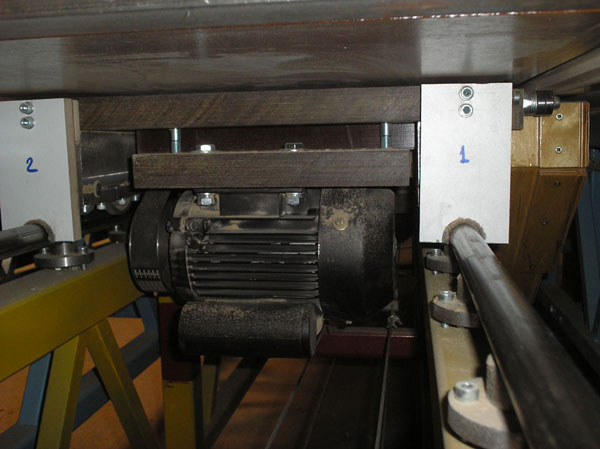
Каретка сделана из 30мм текстолита, размер 750х500мм. Все 8 роликов каретки каленые, по два подшипника в каждом. Стоят они парами под различными углами наклона, потому касание роликов с направляющей происходит в разных точках, это уменьшает износ направляющих, не дает накатывать канавку. С обеих сторон направляющей установлены конечные выключатели. На обратном ходу установлен дублирующий резервный конечник, на случай выхода из строя основного, а для индикации неисправности основного конечника установлена световая сигнализация.
Для цепи управления станком в силовой шкаф установили стабилизатор Ресанта 500Вт.
Столы изготовлены из МДФ толщиной 21мм и 32 (16+16)мм.
В качестве прижимов используются обычные мебельные газ-лифты на 5 килограмм.
Джойстик используется самодельный, трещетку взяли из автомобильного набора головок.
Везде использовались закрытые с обеих сторон малошумящие немецкие подшипники.
Габаритные размеры станка – 4500х2800мм.
Настройка станка производилась прибором (в быту называют цешкой) на замыкание с помощью двух натянутых струн. Настройка подрезки под основную пилу производилась с помощью прокладочных колец.
Процесс настройки происходит следующим образом.
[aslideshow]



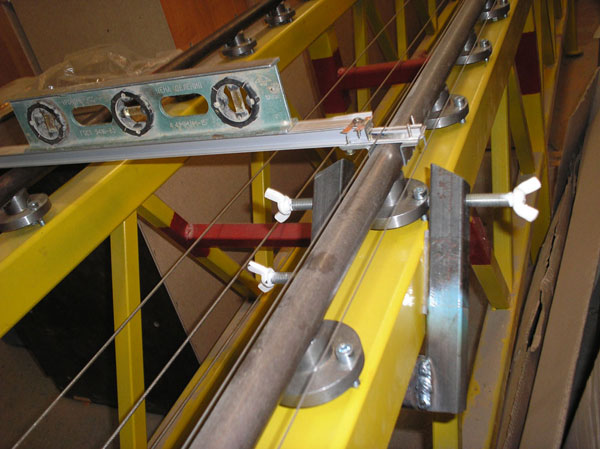
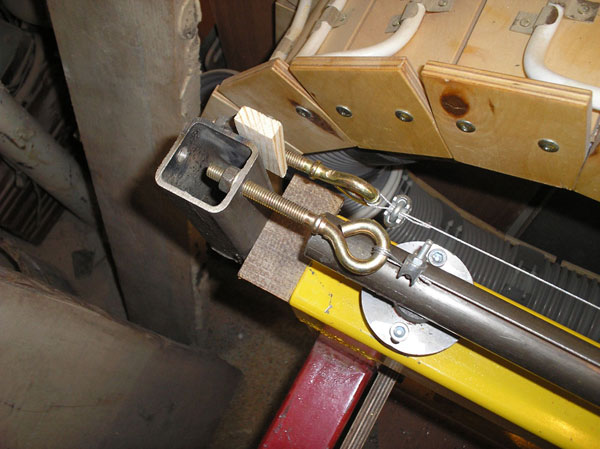
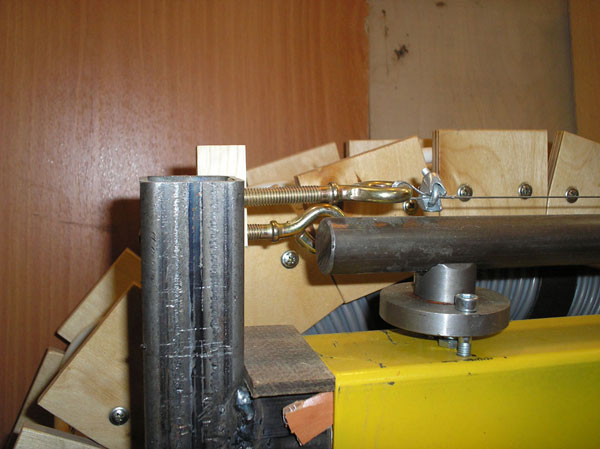
[/aslideshow]
Натягиваем два тросика 1мм сбоку и сверху. На направляющей устанавливается специальное приспособление с двумя пластинками, которые стоят в вертикальной и горизонтальной плоскости. Ее поверхности касаются с тросиком (на фото видно намеченные места касания). К тросикам подключен первый вывод «цешки», а к направляющей второй, установлен режим «ОМ». Направляющая и тросики изолированы (нет гальванической связки). Между верхним тросом и верхней пластинкой вставляем лист бумаги, внизу к профилю прикручивается струбцина (см. фото), у нее есть два болта. Настраиваем на касание с тросом (смотрим по прибору). После этого убираем бумагу и вставляем между боковым тросом и боковой пластиной (у автора штырь). С помощью болтов настраивается высота на замыкание (видно по прибору). Процедура повторяется отдельно с каждым узлом, в авторском варианте по 25 на каждой направляющей.
Ниже представлены рисунки каретки и валов, а также чертежи роликов и шарниров.
Также интерес представляет и оригинальная конструкция кабель-каналов из фанеры, за работой которых можно понаблюдать в видеоролике. Как видно, уложенные в них провода и шланги нигде не перегибаются и не придавливаются, что увеличивает износостойкость и продляет жизнь станку.
[aslideshow]
[/aslideshow]
Направляющие, сделанные из стали повышенной прочности 40Х, калибруются в специальных цехах методом волочения (разг. Протаскивания) через отверстие определенного диаметра, такие предприятия есть в любом среднем городе.
Регулировка плоскости стола относительно направляющей осуществляется следующим образом:
К столу под углом 90° клеится упор.
Выравниваем стол параллельно ходу каретки (на глаз). Стол прикручиваем одним саморезом к основанию станка. Берем прямоугольный кусок ЛДСП 600х600 мм. Поочередно срезаем с каждого края по 3мм (при этом деталь вращается строго по часовой стрелке 4 раза). После этого пятый раз поворачиваем деталь по часовой стрелке и делаем срез 15мм, берем этот отрезок, ставим на ребро и ломаем посередине. Полученные две части складываем вместе.
Если куски не совпали – начинаем двигать столешню в нужную сторону и повторяем процедуру с пилением ламината до получения идеального результата – точного совпадения высоты двух частей. Когда нужный результат достигнут – прикручиваем намертво столешню.
При работе со станком следует учесть следующие моменты:
Если не отвести каретку назад и положить деталь на стол – каретка будет возвращаться в автоматическом режиме не зависимо от того держит ли рабочий джойстик или нет. При этом она врежется в деталь рассекателем, если рабочий не успеет нажать красную кнопку аварийной остановки. Ничего страшного не произойдет, максимум испортится деталь, но в принципе при небольшой доработке эта проблема решаема.
Если нужно отпилить угол с детали немного неудобно целиться, но это легко решается установкой лазерной полосы там где движется пила.
Максимальная длина детали которую можно прогнать 2800мм, это следует учитывать.
А так получается очень надежный, удобный и компактный форматный станок для небольшого производства. Сейчас один из пользователей, dabasov, успешно повторяет опыт автора и собирает такой же аппарат для своего строящегося цеха.
Наблюдать за темой можно на форуме.
Не забудьте поблагадарить автора концепта, за предоставленную информацию. Отдельное спасибо пользователю DokaLe от «Блога интересных идей».
Форматно-раскроечный станок своими руками | Строительный портал
Многие хозяева задаются вопросом, какое оборудование требуется для качественного изготовления корпусной мебели. Специалисты утверждают, что это форматно-раскроечные станки, которые в народе называют станками круглопильными форматными или круглопильными с кареткой. Каждый хозяин может собрать такой аппарат собственноручно.
Содержание:
- Назначение форматно-раскроечного станка
- Конструкция форматно-раскроечного станка
- Изготовление форматно-раскроечного станка
Назначение форматно-раскроечного станка
Форматно-раскроечное оборудование предназначается для поперечного, продольного раскроя пиломатериалов и раскроя под определенным углом, форматной обрезки и раскроя щитовых заготовок, включая и удаление свесов после проведения их облицовывания, а также с целью раскроя на заготовки заданного размера полноформатных плит.
Форматно-раскроечное оборудование, что используется при производстве корпусной мебели, позволяет выпускать готовую продукцию высокого качества. Функция этих станков кроется в задаче базовых параметров деталям мебели для проведения последующей обработки. Подобные станки предназначены для поштучного и пакетного раскроя заготовок.
Фабричные и самодельные форматно-раскроечные станки работают с разными материалами: различными породами древесины, фанерой любой толщины, панелями МДФ, ДСП, ДВП, в том числе композиционными листовыми материалами, облицованными пластиком, ламинированными бумажными и пленочными материалами, шпоном и меламином. Данное оборудование, как правило, используется для раскроя материала, который имеет точные геометрические размеры.
Форматно-раскроечные станки используются на мелкосерийных производствах, средне- и крупно-масштабных мебельных фабриках, а также в небольших столярных мастерских. Возможность предварительной подрезки заготовок отдельной пилой непосредственно под зоной совершения пропила позволяет раскраивать облицованные натуральным или искусственным материалом заготовки без возникновения сколов облицовки.
Конструкция форматно-раскроечного станка
Конструктивно форматно-раскроечные станки состоят из таких элементов: станины, рабочего неподвижного рабочего стола и подвижного дополнительного стола (каретка, тележка, опорная рама, сепаратор, линейка), пильного узла, состоящего из 2 пильных дисков, направляющих,
Пильной узел
Сварная конструкция форматно-раскроечного станка гарантирует высокий уровень устойчивости и отсутствие при пилении вибрации. При раскрое облицованных плит главной проблемой является образование на облицовке сколов в той области, где зуб пильного диска выходит. Чтобы справиться с этой проблемой, в чертежах форматно-раскроечных станков предусмотрен пильный узел с двумя пильными дисками.
Пильный агрегат представляет из себя цельный узел, что отлит из чугуна. Установлены на его корпусе два электродвигателя, которые вращают при помощи ременной передачи подрезной и основной пильные диски. Подрезной диск находится ближе к заготовке, его размер доходит до 120 миллиметров, а в попутном направлении частота вращения достигает 8000 оборотов в минуту.
Этот диск и требуется для пропила слоя облицовки с той стороны, где выходят зубки основного диска, который вращается во встречном направлении к заготовкам и выполняет основной пропил в плите, как показано на видео о форматно-раскроечном станке. Подобная конструкция позволяет получить ровный и чистый пропил, который не испорчен задирами и сколами.
На некоторых видах станков устанавливают пильный узел при помощи специальных поворотных секторов, который может перестраиваться на распил под углом. При этом соотношение подрезного и основного пильных дисков не нарушается. Пильный агрегат может устанавливаться на рабочем столе или на станине.
Основанная пила
В форматно-раскроечных станках частота вращения главной пилы колеблется в пределах 4 — 6 тысяч оборотов в минуту. Плавная регулировка скорости позволяет быстрее производить настройку форматно-раскроечного станка и точно подбирать режимы работы для разных распиливаемых материалов. Как правило, мощность привода пилы составляет 3−5,5 киловатт. Помните, что не всегда уместна высокая потребляемая мощность, которая обычно характерна для технологического процесса, в котором проводиться пиление пакета листов или раскраиваются твердые сортов древесины.
Высоту пропила или положения основной пилы в форматно-раскроечных станках устанавливают посредством вертикального передвижения пильного агрегата. При этом применяются два метода: по вертикальным направляющим и за посредством качания вокруг горизонтальной оси.
Максимальная высота, на которую пила поднимается относительно стола, должна указываться в технических характеристиках агрегата.
Традиционно она достигает 80 — 130 миллиметров. При наклоне пилы этот показатель соответственно уменьшается. В некоторых моделях предусмотрен автоматический подъем и опускание пилы, работающий от электропривода, иногда с даже заданием высоты с помощью пульта управления.
Пилы форматно-раскроечного станка имеют, как правило, наклон до 45 градусов, как на фото форматно-раскроечных станков. При этом будет наклоняться весь пильный агрегат. Горизонтальная ось поворота станка благодаря наличию специальных цапф проходит по линии пересечения плоскости неподвижного стола и основной пилы, что исключает в прорези стола заклинивание пилы. Такая функция является необходимой при изготовлении элементов корпусной мебели.
Подвижный и неподвижный стол
Основной неподвижный стол, что отлит из чугуна, имеет верхнюю фрезерованную поверхность, размеры которой можно корректировать при помощи дополнительной установки на нем столов удлинения и расширения и параллельной упорной линейки, которая способна перемещаться.
Подвижный стол состоит конструктивно из каретки, которая изготовлена из многокамерного алюминиевого профиля, опорной рамы, угловой упорной линейки, что имеет откидывающиеся упоры и телескопическим удлинением, опорной рамы и её поддержки. Каретка благодаря собственной конструкции является устойчивой к нагрузкам на изгибание и скручивание.
Чаще всего в мебельном производстве используются форматно-раскроечные станки с длиной каретки приблизительно 3200 миллиметров. Это самое приемлемое решение для аппаратов с подвижной кареткой, потому что оно соответствует большинству габаритов плит, которые используются предприятиями.
Не стоит гнаться за высокими ценами форматно-раскроечных станков, полагая, что они работают качественнее. Помните, что всегда самая большая длина реза будет меньшей хода каретки, если имеется подрезная пила. Для полного прохождения зоны пиления заготовкой требуется дополнительно 200−300 миллиметров.
Для перемещения заготовки используется роликовая тележка, что передвигается по стальным направляющим, и сепаратор с шариками или роликами, которые перемещаются между V-образными стальными направляющими. Для регулировки подвижного относительно плоскости основного стола или пилы в конструкции форматно-раскроечных станков, как правило, предусматриваются соответствующие компенсаторы или регуляторы.
Направляющие и каретки
Подвижный стол форматно-раскроечных станков выполняет функцию базирующей поверхности, предназначенной для укладки раскраиваемых плит, он должен выдерживать вес материала. Нагрузку воспринимает сама каретка и ее направляющие. Если они недостаточно жесткие, на направляющие каретки будут воздействовать не только вертикальные нагрузки, но также крутящий момент.
Из-за существенной длины рычага приложения нагрузки в местах контакта роликов или шариков в линейных направляющих доходит до максимального значения. Поэтому используются в станках с кареткой специальные направляющие, которые обеспечивают легкость ее перемещения и исключают возникновение в них зазоров, что напрямую влияют на точность обработки раскраиваемой заготовки.
В различных станках разных изготовителей используются направляющие разной конструкции с применением роликов, шариков и их комбинаций. Наиболее распространенной конструкцией, не зависимо от стоимости форматно-раскроечного станка, является алюминиевая каретка, которая перемещается по стальным направляющим на линейных шарикоподшипниках.
Направляющие зачастую выполняются в виде стальных полос, которые встроены в алюминиевый корпус каретки таким способом, что образуются для размещения шариков два «канала». Подобная «призматическая» схема способна воспринимать нагрузки в любом направлении. Для возрастания срока службы накладки до установки конструкцию подвергают термическому упрочнению. И анодированию, что предотвращает возникновение на обрабатываемой заготовке полос от загрязнения алюминием.
Существуют и направляющие, в которых шарики являются не стальными, а пластиковыми, жесткость которых достигается с помощью использования алюминиевого профиля с большим количеством внутренних ребер. В некоторых направляющих имеются встроенные компенсаторы износа, но этот узел обычно ремонту в домашних условиях не подлежит.
Дополнительные опции
Многие форматно-раскроечные станки оснащаются цифровыми указателями положения упоров и линеек, которые установлены непосредственно на них. Имеются и станки, в которых текущее положение линейки или упора задается на экране монитора с помощью пульта управления, а затем подобные устройства перемещаются в заданное положение автоматически путем индивидуального электропривода.
На форматно-раскроечном оборудовании в качестве обычной или дополнительной комплектации могут применяться:
- система электроторможения основного пильного диска,
- регулировка скорости движения основного пильного диска,
- система автоматической смазки и регулировки угла пильного узла,
- электромеханические приводы,
- электрические двигатели с увеличенной мощностью,
- верхняя защита пильных дисков, что оснащена патрубком для отвода опилок,
- пневматические или эксцентриковые прижимы для удерживания заготовок,
- дополнительная опорная рама,
- поворотная линейка для раскроя заготовок и плит под непрямым углом,
- двойной угловой упор,
- датчик вибрации,
- система защиты от попадания стружки и пыли.
Изготовление форматно-раскроечного станка
Если вы планируете заняться изготовлением корпусной мебели, то вам стоит поинтересоваться, как сделать форматно-раскроечный станок. Проще простого его принцип работы, но цена форматно-раскроечного станка заводского изготовления достаточно приличная. Не каждый частный хозяин может себе позволить купить такое оборудование. А вот собрать станок своими руками по силам каждому человеку, который способен обращаться с инструментами и хоть немного знаком с техникой.
В процессе работы вам понадобятся: металлические трубы, швеллеры и металлические уголки, два электрических двигателя, основной пыльный и подрезной диск, валы от сельскохозяйственной техники, крепежные детали (гайки и болты), набор инструментов по металлу, сварочный аппарат.
Для начала вам необходимо изготовить прочную стальную станину для форматно-раскроечного станка, используя металлические швеллеры. Габариты заготовок для основания должны быть следующими: длина станка 6500-6700 миллиметров, ширина 2500 миллиметров, высота 800-1100 миллиметров. Затем сконструируйте основную и напольную направляющую станка и на станине укрепите их. Для изготовления направляющих принято использовать трубу, что имеет размеры 60 на 5 на 6500 миллиметров.
Подвижный рабочий стол нужно сделать перемещающимся по направляющей, потому что стол во время работы будет совершать подачу листа. Предусмотрите длину линии реза на уровне 3000-3200 миллиметров. При желании можно увеличить или уменьшить данный параметр, для этого нужно только изменить длину направляющих.
На станок навесьте две пилы – подрезную и основную. Пилы следует устанавливать на пильном блоке, они вращаются друг другу навстречу и в движение приводятся двумя асинхронными двигателями. В обязательном порядке предусмотрите возможность наклона для блока под острым углом до 45 градусов. Снабдите для этого пильный блок специальным поворотным механизмом.
К выбору двигателей отнеситесь внимательно, ведь они приводят в движение пилы. Мощность мотора должна составлять не меньше 2,9 кВт. Двигатели должны вращать основную пилу со скоростью порядка 5000 оборотов, а подрезную – 8000 оборотов в минуту. В конструкции станка используйте пильные диски диаметром 250 миллиметров, что позволяет совершать раскройку ламинированных древесно-стружечных плит и обрезку листов.
Для безопасного использования форматно-раскроечных станков своими руками в производственном помещении предусмотрите хорошую вытяжную вентиляцию, потому что частицы древесины способны воспламениться от самой маленькой искры, возникающей при работе двигателей. Учитывая большую скорость движения пильных дисков, рекомендуется соблюдать при работе на станке повышенную осторожность, так как диски, которые вращаются на большой скорости, могут нанести травмы работнику, вплоть до потери кисти руки и всей конечности.
После изготовления форматно-раскроечного станка в домашних условиях можно приступать к непосредственной обработке материала. Листы обычно имеют большие габариты, поэтому перед установкой листа в механизм стоит провести первоначальные разметки в местах, где будут проделаны разрезы. Размер заготовки при этом должен быть больше хотя бы на 7 – 8 миллиметров с каждой стороны. После создания небольшой стопки заготовок с разметками, можно заниматься раскройкой и обрезкой материала.
Как сделать форматно раскроечный станок своими руками
Форматно-раскроечный станок — оборудование, которое предназначено для распила мебельной плиты. Представляет собой конструкцию, состоящую из пильного узла и станины. Пильный узел представляет собой два пильных диска, с параллельными осями вращения, которые расположены на одной линии. Причем один из дисков большего один меньшего диаметра и вращаются в разные стороны — по направлению друг к другу.
Для того кто решил заняться изготовлением мебели наличие форматно-раскроечного, или как его еще называют круглопильного форматного станка — необходимое условие. Но стоят такие станки недешево, и если вы только начинаете заниматься производством мебели, то покупка такого сложного дорогостоящего станка не всегда возможна и оправданна. Но есть выход — собрать такой станок самостоятельно.
Для тех, кто умеет все делать своими руками, изготовление форматно раскроечного станка — выполнимая задача. Для этого только нужно, во-первых изучить конструкцию станка, во-вторых, собрать необходимые материалы, ну а инструменты у мастера на все руки всегда найдутся.
Изготовление можно начать со сборки прочной стальной станины из металлического швеллера и металлических уголков. При этом требуется выдержать такие габариты: длина станка — 6500-6700 мм, ширина 2500 мм, высота 800-1100 мм.
![]() |
Схема, применяемая обычно в промышленных станках |
Верхнюю часть стола нужно сделать подвижной, чтобы она передвигалась вместе с мебельным листом. При этом длину реза выбирают от 2500 до 3000 мм. Для того чтобы сделать столешницу подвижной используют направляющие, которые движутся по роликам.
После этого на станок нужно навесить две пилы. Первая по ходу движения листа пила, так назы-ваемая подрезная, должна быть меньшего диаметра до 120 мм и со скоростью вращения 8000 об/мин. Подрезная пила вращается в направлении от плиты. Основная пила вращается со скоростью 5000 об/мин и имеет диаметр 250 мм.
Для вращения пил применяют два разных асинхронных двигателя — для вращения основной пилы — мощностью 3-3,5квт, для подрезной мощность может быть немного меньше. Двигатели соединяются с валом с помощью клиноременной передачи. С помощью той же самой клиноременной передачи можно регулировать скорость вращения валов. Для удобства можно спроектировать приспособление для наклона стола. С помощью специального этого приспособления можно регулировать наклон стола до 45° относительно дисков.
Форматно-раскроечные станки – это один из основных видов необходимого оборудования для изготовления мебели. Раскрой плит ДСП, ДВП и МДФ и других листовых материалов производится с помощью форматно-раскроечных станков.
Одно из основных свойств форматников – точность распила, так как этот параметр оказывает большое влияние на качество изготовляемой мебели.
Без форматно-раскроечного станка в мебельном производстве делать нечего, но не у всех есть возможность начать бизнес с покупки хорошего оборудования. И тут на помощь приходит бесценный опыт товарищей-мебельщиков, которые с удовольствием делятся своими наработками на форуме мебельщиков.
Рассмотрим изобретение пользователя DokaLe, это НЕ первый его форматник, потому в данном варианте учтен опыт предыдущей работы над станком. Станок обеспечивает достаточно высокую точность раскроя, 0.1 мм при прямолинейной обработке по длине 2750мм, что является отличным показателем для самодельного оборудования. Сам станок занимает места меньше чем «заводские» образцы, длина станка составляет 4,5 метра и умещается в гараже размерами от стены до стены 6м, в то время когда для размещения «заводского» станка необходимо порядка 7 м. что является причиной поиска помещений с более высокой арендной платой.
Пильный узел с коробом для сбора опилок. Обратите внимание, что диски крутятся «друг на друга».
Линейка, с ограничительным прижимом.
Посмотрите видео ролик о работе данного станка:
Перед тем как продолжить расссказ про данный станок, хочу показать, как выглядел предыдущий вариант. Он был очень прост в изготовлении и имеет низкую себестоимость. Проработал 10 лет.На станке стоят дешевые китайские диски АТАКА, но пилят они почти без сколов. Каретка перемещается с помощью 12 подшипниковых колес от болгарского накопителя на магнитных носителях. На каждый пильный диск был установлен отдельный двигатель.
Вал с ременной передачей.
Итак, вернемся к новой модели. Станок позволяет обрабатывать детали с длиной пропила 2770мм, при длине стандартного листа 2750мм. Если необходимо распилить лист длиной 3500 мм. тогда потребуется его предварительно распилить на две части.
На станке предусмотрен расклинивающий нож, и это не случайно.
При обкатке нового станка отлетел обрезок (100х100мм) по ходу основной пилы. После экспериментов стало понятно, что обрезок подкидывает задним фронтом основной пилы и выкидывает вперед на подающего материал. (на видео есть момент без расклинивающего ножа и корпуса), после чего поставили нож. Это единственная его функция при данной конструкции станка.
Дело в том, что листы ЛДСП имеют внутреннее напряжение. Особенно это заметно на залежалых деталях или отсыревшем материале. Такой материал после пропила основным диском, начинает сжимать пропиленную щель. Если лист большой, то обратным ходом диска может поколоть лицевую сторону матераила. Если деталька маленькая, то ее может подбросить вверх. Поэтому расклинивающий нож необходим. Толщина ножа должна быть не меньше ширины диска, тоесть примерно 4 мм.
Рассмотрим более подробно из чего состоит станок и основные характеристики:
— двигатель основного вала – АИРЕ 80, 220В, 2800 об/мин, 2,2 кВт;
— двигатель подрезного узла – АИРЕ 71, 220В, 2800 об/мин, 1,1 кВт;
— ступенчатая скорость каретки обеспечивается двигателем постоянного напряжения 36В;
— редуктор червячный самый маленький из серии, 28-й, итальянского производства, оказался дешевле российского аналога почему-то.
На редукторе два шкива с двух сторон, каретка передвигается при помощи двух трехмиллиметровых тросиков в оплетке. На основном валу получаем скорость вращения 3500 об/мин, установлен клиновой ремень. Для подрезки получается более скоростной выход — 5800 об/мин, установлен поликлиновой ремень на 8 ручьев.
Основная пила имеет подъем 0-52мм, подрезная 0-4мм. Наклона пилы под углом нет. В качестве направляющих выступает калиброванный прут 25мм длиной 4,2 метра.
Каретка сделана из 30мм текстолита, размер 750х500мм. Все 8 роликов каретки каленые, по два подшипника в каждом. Стоят они парами под различными углами наклона, потому касание роликов с направляющей происходит в разных точках, это уменьшает износ направляющих, не дает накатывать канавку. С обеих сторон направляющей установлены конечные выключатели. На обратном ходу установлен дублирующий резервный конечник, на случай выхода из строя основного, а для индикации неисправности основного конечника установлена световая сигнализация.
Для цепи управления станком в силовой шкаф установили стабилизатор Ресанта 500Вт.
Столы изготовлены из МДФ толщиной 21мм и 32 (16+16)мм.
В качестве прижимов используются обычные мебельные газ-лифты на 5 килограмм.
Джойстик используется самодельный, трещетку взяли из автомобильного набора головок.
Везде использовались закрытые с обеих сторон малошумящие немецкие подшипники.
Габаритные размеры станка – 4500х2800мм.
Настройка станка производилась прибором (в быту называют цешкой) на замыкание с помощью двух натянутых струн. Настройка подрезки под основную пилу производилась с помощью прокладочных колец.
Процесс настройки происходит следующим образом.
Натягиваем два тросика 1мм сбоку и сверху. На направляющей устанавливается специальное приспособление с двумя пластинками, которые стоят в вертикальной и горизонтальной плоскости. Ее поверхности касаются с тросиком (на фото видно намеченные места касания). К тросикам подключен первый вывод «цешки», а к направляющей второй, установлен режим «ОМ». Направляющая и тросики изолированы (нет гальванической связки). Между верхним тросом и верхней пластинкой вставляем лист бумаги, внизу к профилю прикручивается струбцина (см. фото), у нее есть два болта. Настраиваем на касание с тросом (смотрим по прибору). После этого убираем бумагу и вставляем между боковым тросом и боковой пластиной (у автора штырь). С помощью болтов настраивается высота на замыкание (видно по прибору). Процедура повторяется отдельно с каждым узлом, в авторском варианте по 25 на каждой направляющей.
Ниже представлены рисунки каретки и валов, а также чертежи роликов и шарниров.
Также интерес представляет и оригинальная конструкция кабель-каналов из фанеры, за работой которых можно понаблюдать в видеоролике. Как видно, уложенные в них провода и шланги нигде не перегибаются и не придавливаются, что увеличивает износостойкость и продляет жизнь станку.
Направляющие, сделанные из стали повышенной прочности 40Х, калибруются в специальных цехах методом волочения (разг. Протаскивания) через отверстие определенного диаметра, такие предприятия есть в любом среднем городе.
Регулировка плоскости стола относительно направляющей осуществляется следующим образом:
К столу под углом 90° клеится упор.
Выравниваем стол параллельно ходу каретки (на глаз). Стол прикручиваем одним саморезом к основанию станка. Берем прямоугольный кусок ЛДСП 600х600 мм. Поочередно срезаем с каждого края по 3мм (при этом деталь вращается строго по часовой стрелке 4 раза). После этого пятый раз поворачиваем деталь по часовой стрелке и делаем срез 15мм, берем этот отрезок, ставим на ребро и ломаем посередине. Полученные две части складываем вместе.
Если куски не совпали – начинаем двигать столешню в нужную сторону и повторяем процедуру с пилением ламината до получения идеального результата – точного совпадения высоты двух частей. Когда нужный результат достигнут – прикручиваем намертво столешню.
При работе со станком следует учесть следующие моменты:
Если не отвести каретку назад и положить деталь на стол – каретка будет возвращаться в автоматическом режиме не зависимо от того держит ли рабочий джойстик или нет. При этом она врежется в деталь рассекателем, если рабочий не успеет нажать красную кнопку аварийной остановки. Ничего страшного не произойдет, максимум испортится деталь, но в принципе при небольшой доработке эта проблема решаема.
Если нужно отпилить угол с детали немного неудобно целиться, но это легко решается установкой лазерной полосы там где движется пила.
Максимальная длина детали которую можно прогнать 2800мм, это следует учитывать.
А так получается очень надежный, удобный и компактный форматный станок для небольшого производства. Сейчас один из пользователей, dabasov, успешно повторяет опыт автора и собирает такой же аппарат для своего строящегося цеха.
Наблюдать за темой можно на форуме.
Не забудьте поблагадарить автора концепта, за предоставленную информацию. Отдельное спасибо пользователю DokaLe от «Блога интересных идей».
» > Хочу поделиться конструкцией самодельного форматника.
После упорных трудов наконец сделал!Станком доволен.
Кому интересно могу скинуть более подробные фото узлов.
Общий вид размещу чуть позже.
Это чудовище не окупится. Точность и удобство работы никакие, а для дома-для сеньи совсем не нужно. Из разряда сделано Кулибиным.
Вы не правы.Это не для дома а для работы.А окупился он с лихвой за 3 месяца!Просто хотел поделиться некоторыми решениями в изготовлении отдельных узлов.Может кому понадобится.
Bhead написал :
Точность и удобство работы никакие
А судя по конструкции и отсутствию какой либо защиты, ещё и опасен.
Для работы разумней купить малую форматку и не изобретать велосипед. Если, конечно, не ради собственного удовольствия.
Ну покалить тут все мастера.
2 kation — молодец, респект!
А что молодец. пишет, что уже давно работает, а вид у станка гадкий. Не только что не покрашен, даже окалина и заусенцы от болгарки не сняты. Он просто опасен, даже если его просто задеть, про работу уже не упоминаю. Точно также можно ездить на раме от авто, поставленой на колёса. Что за кайф, не понимаю. Респект, когда конструктор доводит детище до ума, и это не только нормально и безопасно работает, но ещё и удобно и хоть немного красиво. А это так. прототип или действующая модель станка. рано радоваться. А Кулибиных у нас пруд пруди.
*******
на переферии и так сойдет, сам денюжку заработает и другим работу даст.
Автор станка молодец!
Покалечится может, вот и вся история.
2(777) Ну вот Вы, с периферии, объясните мне, что за кайф работать на таком чудовище? Неужели здоровья не жалко?
И ведь про «молодца» поёте даже не видев, какое качество станок даёт, и каково на нём работать. Сам автор про это даже слова не написал. Нет просчёта конструкции, не видно каретки, нет линеек, много чего не видно. Раму по чертежу сварить любой сварщик может, а здесь надо ещё доказать что конструкция работоспособна. Я не верю просто в слова: «После упорных трудов наконец сделал! Станком доволен.»
А вот и его вид
Bhead написал :
поёте даже не видев, какое качество станок даёт
В том то и дело, что вы же сами не видели как он пилит, а ****** любой может.
******* человек сделал, а вам завидно вот отсюда вся и грязь.
Вы покажите что своими руками сделали.
**********
kation давай еще фото, выкладывай ПРАКТИКИ РУЛЮТ!
********
Мне лично станок понравился. Как фотография, как вложенный труд и применённые мозги. Но работать на нём в том состоянии, что показано на фотографиях — действительно опасно.
Будут вопросы по узлам с удовольствием поделюсь с заинтересованными.
Позже выложу фотки приспособления для установки без напряга полноформатного листа на станок одним человеком а также небольшой микрофильм что можно изготовить имея разные приспособления и желание работать всего за 10-15мин.(и заодно покажу качество распила)
Обидеть художника может каждый
***********
Что Необхдимо доделать и и как.
1) Необходим защитный кожух на пилу.Скажем половинка от чугунной сковороды с приваренной на один из краев дуги осью сойдет. А еще лучше заводской от любой сломанной дисковой пилы.
Иначе хозяину может быть очень бо-бо.
2) Необходим съемный боковой кожух. Хотя бы листы фанеры на винтах (вкручиваемых в приваненные к раме гайки.
По той же причине.
3) И необходим нормальный вылючатель.
2(777) Давайте лучше по теме. чем нравится станок, чем нет, «ура» все уже слышали, какой я хороший, тоже. Плз к станку поближе*******.
Автору:
ТТХ в студию, общие фото погоды не делают, как работают узлы непонятно, какая точность, непонятно
******* человек хороший и художник. В этом я не сомневаюсь ни сколько, но мы же не о Вас говорим, а о Вашем станке. в его ценности я как раз и сомневаюсь, мелочей не хватает, а на слово я не верю.********
Можно обсудить метод регулировки подрезной пилы.
Предлагайте варианты удобной защиты сверху от пильных дисков и сборке пыли выбрасываемой основной пилой вверх-оригинальные.чтобы не мешали работе,легко сьемные и устанавливаемые.(извиняюсь за не кач.надписи на рис. но принцип должен быть понятен)
DSP007 написал :
.
3) И необходим нормальный вылючатель.
4) Пылесборника совсем нет
5) Линеек не видно
.
сырой станок, у меня такое чувство, что работать на нём приходится как на самодельном пильном станке, долго настраивать размеры, параллельность распила, смотреть в оба ,чтоб не попасть под диск и задыхаться от пыли во время реза. Не видно аварийного выключателя. По моему, долго, тяжело работать и не удобно.
Интересно ещё, какова точность установки распила и скорость подачи.
ИМХО, для работы малого предприятия гораздо разумней было взять кредит и купить нормальную форматку. Будет прибыль — расширить производство, там кроме форматки станков много нужно. А на таком самопале, продукция неконкурентноспособна, слишком узок диапазон и ассортимент изделий. И, кстати, разрешения работать на таком опасном станке никто не даст, а подполье, оно до поры, до времени.
Но подкупает, что такой агрегат с нуля создан, за это респект. Если совершенствовать, может что путное выйдет. Конструкцию основных узлов и принцип работы отдельных блоков можно подсмотреть серийной фориатке, кое что упростить и не изобретать заново велосипед.
(777) написал :
Покажите что вы сделали, ну хотя бы ремонт дома
какого из. по счёту? Хотя повторюсь, давно всё показано и обговорено, на «бис» не буду.
(777) написал :
Что не могли профи позвать.
до сих пор было наоборот.
(777) написал :
на что я отвечу: не ахти.
говори. никто за язык не тянет и рта не затыкает. другое дело, самому, похоже, похвастать нечем, а болтунов здесь хватало всегда. Если будет показано что-то стоящее, то отчего ж не похвалить.
Для Вас специально разжую свою позицию:
за идею и упорство в достижении своей цели автора можно только похвалить, за исполнение, не за что.
У кулибиных часто так получается: идея воплощается в черновом варианте, работает как действующая модель, и запал на этом затухает. Идея воплощена в жизнь, работает, мечта ощюществилась, а чего ещё надо? Идея интересна, пока не получен ответ на вопрос, себе же заданный, потом становится не интересно. Тот же Высоцкий, запоем играл в «Место встречи. » все погони, перестрелки. (как сейчас говорят «экшен»), а студийные съёмки его только раздражали и были не интересны.
Во первых не надо фразы из контекста выдирать, это мы могем тоже,
Изначально вы настроенны агрессивно, ремонт привел как пример, ну да ладно, покажите станок который собрали сами, чужое проще охаять.
Купить жаба душит, а сделать и сэкономить кучу бабла не можете, вот отсюда весь и негатив, как так, я купил за (пример 10000), автор же сделал при минимальных вложениях, по функциональности тот же (пусть не такой красивый) за 1000.
То что касается ваших оценок, то цена им ноль*******
Станок нравится и все тут *********
с точностью до наоборот, куплю, возьму в аренду, но делать не буду, это тупиковый путь.
(777) написал :
. сделал при минимальных вложениях, по функциональности тот же
вложения меньше, да, но функциональность далеко не та, точность +- километр, только для дома, не для продажи. Сами же такое и не купите, если придётся. Ура кричать многие горазды, а коснись конкретно, будет лепет, что станок конечно хорош, но то, что им делают, мне не подходит. Смотреть надо по результату.
(777) написал :
То что касается ваших оценок, то цена им ноль *****
это не более чем ИМХО отдельно взятого индивидуума ******* Я хоть и на чужой форматке, но работал, и знаю, о чём говорю, ********.
ЗЫ всё познаётся в сравнении.
kation написал :
Хочу поделиться конструкцией самодельного форматника.
После упорных трудов наконец сделал!Станком доволен.
Кому интересно могу скинуть более подробные фото узлов.
Общий вид размещу чуть позже.
Автору РЕСПЕКТ! Живу от ближайшего форматника в 60км..Заказов немного, покупать станок нет смысла , не окупиться. Для меня выход собрать самодельный форматник, так что я, проявляю к станку повышенный интерес. И не всё золото что блестит. С уважением.
Фотки поглядел, не порадовали. Заусенцы от болгарки (о такие пол пальца обрежешь и не заметишь, я их даже под сварку снимаю, хотя и не критично, но привычка), сварные швы ну полное гуано и даже не зачищены. То, что не покрашен на работоспособность не влияет, конечно, но все в целом создает впечатление, что сделано не для себя, без любви. Но критиковать не стану, работа сделана и приличная, характеристик станка я не знаю, может он точность до десятки дает без напряга. У меня больше вопросов к критикам появилсь.
Bhead написал :
с точностью до наоборот, куплю, возьму в аренду, но делать не буду, это тупиковый путь.
Bhead написал :
вложения меньше, да, но функциональность далеко не та, точность +- километр, только для дома, не для продажи.
Автор про продажу вроде и не говорил ни где, а про точность — как вы её оценили?
потому, что нельзя нормальный станок на коленке сделать. Это не пилорама из швеллера, а точный станок.
Викторыч написал :
Автор про продажу вроде и не говорил нигде
kation написал :
Это не для дома а для работы
продажа мебели из-под этой форматки.
Викторыч написал :
про точность — как вы её оценили?
по внешнему виду, других фото автор не дал. Ни линеек, ни конструкции направляющих, и автор своё детище не любит, сами это заметили. Не может станок такого вида давать достаточную точность.
Викторыч написал :
характеристик станка я не знаю
никто не знает, а автор не торопится озвучить.
yustas62 написал :
Для меня выход собрать самодельный форматник
ИМХО, лучше погружную циркулярку с шиной. Быстрей, дешевле и безопасней. У Вас заказов мало.
Начинайте его «облагораживать».
Задумайтесь о сплошном столе сверху. Так и безопастность «поднимите», и внешний вид улутшите.
Вспоминаю слова одного нашего клиента:»Станок выглядит красиво, значит работать должен хорошо!».(есть такое народное мнение!Причём встречаю его не первый раз!)
yustas62 написал :
Для меня выход собрать самодельный форматник
Подвижный стол перемещается по трем направляющим (две крайние-горизонтальные,средняя-осевая).Горизонтальные направляющие крепятся к основанию(раме станины) с помощью болтов М6 с возможностью регулировки их по высоте с помощью установки под нее регулировочных пластин.Осевая крепится к основанию в нескольких местах (примерно через примерно 50 см
-это достаточно) с возможностью регулировки ее осевого смещения с помощью винтов с эксцентриками.Для предварительной установки станины каретки горизонтально по уровню сама станина имеет внизу тоже регулировочные ноги!
Блоки подшипников установленные на самой каретке все имеют возможность смещения и точной установки по направляющим(достаточно простая конструкция для регулировки и изготовления).
Если оценивать стоимостные характеристики замены подшипников и направляющих то это обойдется примерно в 800руб! и один рабочий день.
Хотя на первой конструкции попроще направляющие служили почти 3 года.
Всем спасибо за критику и поддержку.Фото были процесса изготовления станка. С уважением «Катион»
Форматно-раскроечный станок своими руками: чертежи
Если вы задались вопросом о том, какое устройство лучше остальных подойдет для изготовления корпусной мебели, то следует рассмотреть форматно-раскроечный станок. Своими руками его вполне можно выполнить.
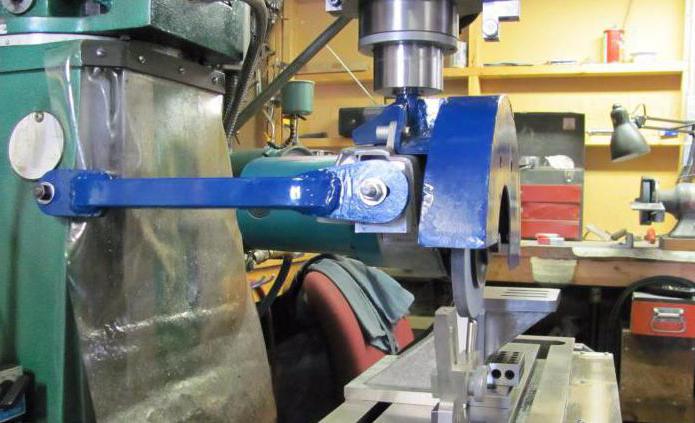
Назначение станка
Такое оборудование предназначается для продольного и поперечного раскроя материалов, а также для резки изделий под определённым углом. С помощью подобной техники можно выполнять щитовые заготовки и форматные обрезки. С помощью форматно-раскроечных станков можно выпускать продукцию высокого качества. Роль этого оборудования выражена в том, чтобы задавать определённые параметры деталям мебели для последующей их обработки.
Особенности пильного узла
Сварная конструкция описываемого агрегата обеспечивает хорошую устойчивость и отсутствие вибрации. Когда мастер раскраивает облицованные плиты, то в качестве основной проблемы выступает образование сколов, где зуб пильного диска выносится за пределы. Для того чтобы избежать этой проблемы, в конструкции описываемого оборудования присутствует пильный узел форматно-раскроечного станка. Своими руками его можно выполнить без проблем, он будет иметь вид цельной системы. В заводских аналогах эта часть отливается из чугуна.
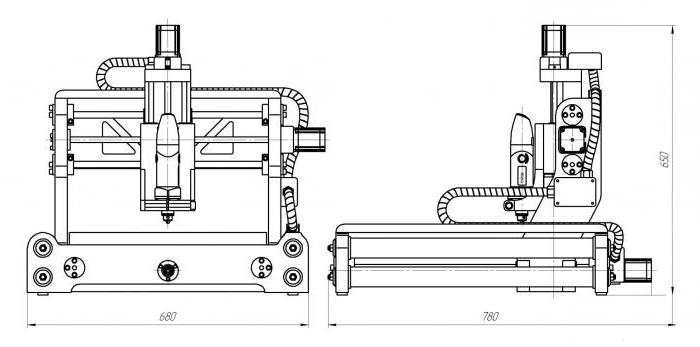
На корпусе устанавливаются два электрических мотора, которые вращаются ременной передачей. Подрезной диск располагается ближе к заготовке, а его размеры могут достигать 120 мм. В попутном направлении вращение может достигать 8000 оборотов в минуту. Диск необходим для пропила облицовки, где выходят зубки главного диска, вращающегося во встречном направлении по отношению к заготовкам.
Такая конструкция позволяет добиться чистого и ровного пропила, который не будет испорчен сколами и задирами. На некоторых станках пильный узел устанавливается с помощью поворотных секторов, при этом он перестраивается на распил под определённым углом. Соотношение основного и подвесного пильных дисков при этом не нарушается. Пильный агрегат иногда располагается на станине, иногда – на рабочем столе.
Подготовка к проведению работ
Если вы намерены выполнить форматно-раскроечный станок своими руками, то необходимо ближе ознакомиться с его конструктивными особенностями. Главным рабочим узлом является блок реза, состоящий из:
- пильных дисков;
- раструба для подключения к стружкопылесосу;
- электродвигателя.
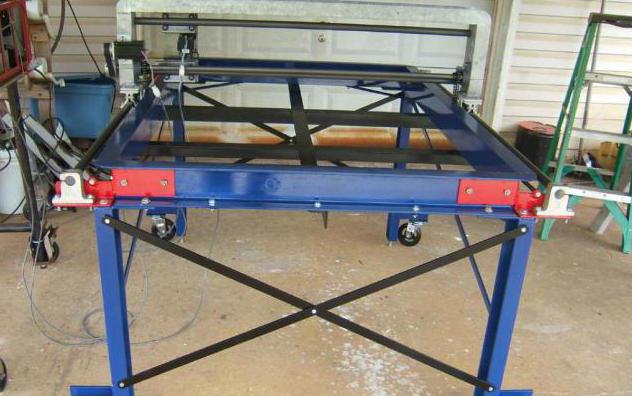
Мастеру необходимо будет подготовить определённые узлы, в качестве которых выступит не только станина, но и рабочий стол, прижимы для заготовки, подвижная каретка и защитные кожухи. Основным корпусом является станина, на нее в дальнейшем устанавливаются остальные элементы. На рабочем столе будет располагаться заготовка. Для ее изготовления нужно подготовить ровную поверхность, которая будет лишена дефектов, ведь они могут повредить ламинированный лист. Для фиксации деревянного полотна нужны будут прижимы.
Подвижная каретка представляет собой несущий элемент, который выполняется из труб круглого сечения или двутавровой балки. Если форматно-раскроечный станок своими руками изготовить с учётом вышеописанной конструкции, он станет наиболее простым вариантом, а собрать его можно будет из подручных материалов. При их выборе следует учитывать их способность претерпевать механические нагрузки, ведь функционирование станка сопровождается вибрацией. Иногда пильные диски располагаются в разных углах по отношению к заготовке. Основной при этом находится сверху, тогда как отрезной – снизу. Это повышает качество раскроя, однако усложняет процесс изготовления.
Рекомендации по сборке станка
Как только удастся выбрать комплектующие, можно начинать сборку станка. Для этого понадобятся:
- УШМ с диском по металлу;
- измерительный инструмент;
- сварочный аппарат;
- электрическая дрель.
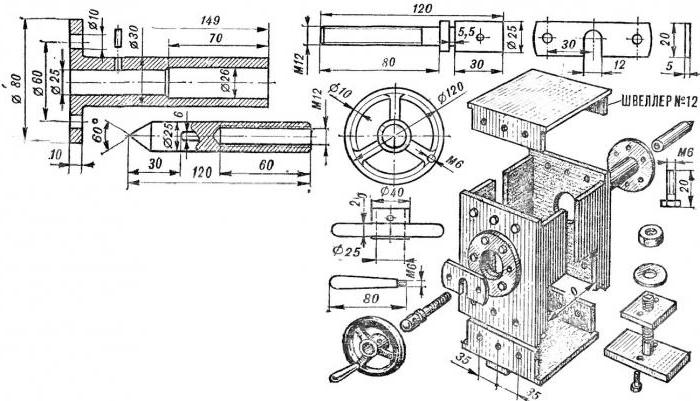
Когда выполняется форматно-раскроечный станок своими руками, на первом этапе необходимо сделать станину, для чего используются трубы круглого или квадратного сечения. Их необходимо обрезать, учитывая схему, и укрепить между собой струбцинами. Как только удастся выверить размеры и правильно расположить элементы, можно начинать сваривать их. Для повышения жесткости необходимо расположить профили между ножками станины.
Методика проведения работ
Начиная манипуляции над подвижной кареткой, необходимо установить направляющие, в качестве которых может выступить труба или балка. Заготовки соединяются между собой. Конструкция каретки должна иметь ролики для передвижения. Что касается рабочего стола, то он должен быть максимально устойчивым. Его можно выполнить из двух материалов. Таким образом, основа выполняется из 3-миллиметрового листа, тогда как поверхность – из ДСП, на которую следует укрепить измерительную линейку.
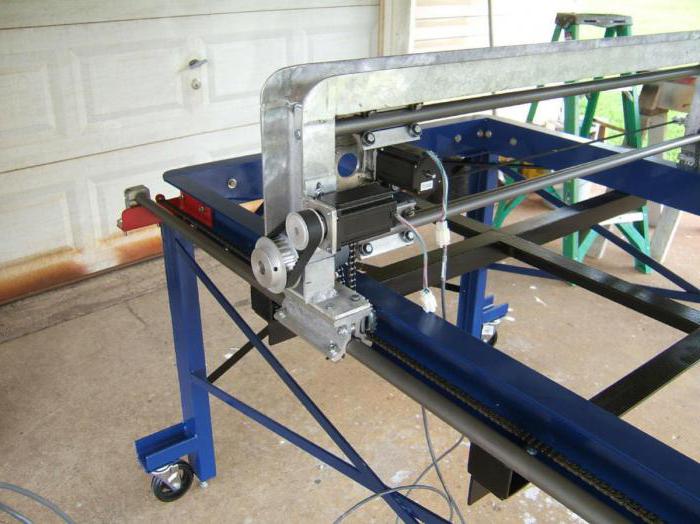
Если вы решили выполнить вертикальный форматно-раскроечный станок своими руками, то необходимо будет изготовить еще и прижимы для листов. Они будут представлять собой рычажный механизм, а конфигурация при этом может быть любой. Важным условием является большая площадь фиксирующих компонентов. В роли дополнительного узла может выступить компонент для изменения высоты дисков по отношению к поверхности листа. Для этого устанавливается механизм подъема, блок резки укрепляется относительно заготовки. Трудоемкость работ при этом будет повышена, придется приобретать дополнительные комплектующие или самостоятельно их изготавливать.
Описание станка «Силкин»
Вас может заинтересовать форматно-раскроечный станок «Силкин». Своими руками подобное оборудование вы можете изготовить по вышеописанной технологии. Если же речь идет об упомянутой модели, то она известна потребителю уже в течение 10 лет. По габаритам обработки, а точнее по длине пропила, в продаже можно встретить 3 модификации:
- 1830 мм;
- 2800 мм;
- 3660 мм.
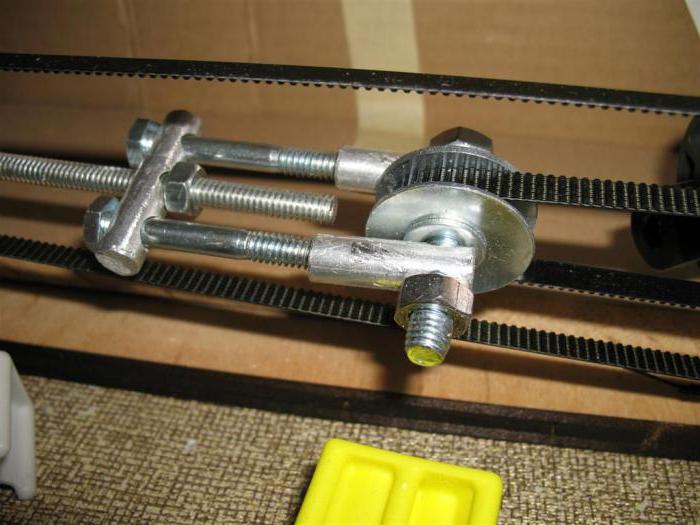
По специальному заказу может быть изготовлено оборудование, длина пропила которого составляет 5000 мм. Перед тем как сделать форматно-раскроечный станок своими руками, вы должны помнить, что заводские модели и варианты, выполненные в собственном гараже, будут предполагать в процессе эксплуатации необходимость проведения ремонта. Обычно он заключается в замене подшипников. Описываемые агрегаты, как показывает практика, работают без нареканий в течение 5 лет. А вот ремонтировать или менять направляющие не потребуется вовсе, ведь конструкция выбирает люфты при работе.
Заключение
Для проведения работ по изготовлению описываемого оборудования необходимо подготовить подрезной диск, валы, позаимствованные у сельскохозяйственной техники, набор инструментов по металлу, а также сварочный аппарат. Когда выполняется форматно-раскроечный станок своими руками, чертежи рассматриваются или подготавливаются заранее. Ознакомившись с ними, вы сможете понять, что конструкция предполагает необходимость выполнения прочной станины, для которой можно использовать металлические швеллеры.