Роторный шлифовальный станок (из дрели и фанеры)

Наверняка, если вы увлекаетесь шлифовальными и другими подобными работами, уже слышали про такие полезные вещи, как ленточная шлифовальная машина, орбитальная, шлифовальная вибромашина и так далее. Но вполне возможно, что вам не встречалась такое приспособление, как роторная шлифовальная машина. Ее отличием считается то, что тут шлифовальным элементом являет не ремень и не диск, это вал! Такая машина отличается простотой, а ее эффективность можно вполне сопоставить с ленточным шлифовальным станком, если вам, конечно, не нужна в совершенстве идеальная плоскость. Впрочем, точность тут не проблема, все зависит от качества сборки.
При желании вы удобно можете обрабатывать любые по ширине плоскости (учитывая максимальную ширину станка), вы запросто можете обрабатывать торцы материала. Рассмотрим подробнее, как же сделать это чудо техники.
Материалы и инструменты, которые использовал автор:
Список материалов:
— наждачная бумага;
— фанера;
— дрель;
— длинный резьбовой стержень;
— два подшипника;
— гайки, барашки, шайбы и другие мелочи;
— два длинных винта с гайками и шайбами;
— саморезы;
— дверные петли;
— клей по дереву, эпоксидный клей, суперклей.
Список инструментов:
— сверлильный станок;
— дрель;
— шуруповерт;
— электролобзик;
— гаечные ключи;
— зажимы.
Процесс изготовления станка:
Шаг первый. Изготовление рабочей плоскости
Основным элементом станка можно считать рабочую плоскость, именно благодаря ней можно регулировать расстояние до шлифовального вала. Рабочая плоскость должна иметь возможность подниматься и опускаться. Сделать ее очень просто. Берем лист фанеры и вырезаем из него основание, к основанию крепим два прямоугольника из фанеры. Садим их на клей по дереву, а с другой стороны дополнительно заворачиваем саморезы.
Теперь будет нужен еще один кусок фанеры, это будет непосредственно рабочая плоскость. Берем дверные петли и прикручиваем ее на них. В итоге плоскость сможет подниматься и опускаться.
Шаг второй. Установка крепежных винтов
По бокам рабочей плоскости установлены два винта, они предназначены для фиксирования стола на нужной высоте. Под них нужно просверлить отверстия между двумя половинками фанеры, более подробно о чем я, смотрите на фото. Потом открутите планку фанеры, между которой сверлились отверстия и положите в канавку болт. Легкими ударами молотка утопите шляпку до половины диаметра в фанеру, аналогично нужно сделать и на другой стороне. В итоге у вас получатся отличные пазы для шляпок винтов.
Шаг третий. Установка боковых стенок
Боковые стенки автор также делает из фанеры. Они двойные, самая широкая стенка предназначена для поддерживания рабочей плоскости, а узкая нужна для надежного крепления шлифовального ротора.
В широкую боковую стенку должны заходить стержни винтов, которые устанавливаются в рабочем столе. Берем карандаш и рисуем линию, по которой эти винты будут двигаться при поднятии и опускании столика. Сверлим в начале и конце линий отверстия, а затем вырезаем пазы при помощи электролобзика.
Установите винты на свои места в рабочем столе, желательно фанеру склеить и потом скрутить саморезами. Теперь установите боковые стенки, а с другой стороны на винты установите шайбы и гайки барашки. С помощью этих гаек вы сможете быстро фиксировать рабочую плоскость в нужном положении.
Шаг четвертый. Прикручиваем основу
Чтобы скрепить всю конструкцию, вам понадобится лист фанеры, из которого изготавливается основа. Первым делом приклейте к боковым стенкам короткие стенки, предназначенные для установки подшипников.
Переворачиваем конструкцию и прикручиваем с другой стороны основу. Основная рама собрана!
Шаг пятый. Устанавливаем подшипники для оси ротора
Настало время установить подшипники. Для них нужно рассверлить посадочные места, в этом деле вам поможет дрель с соответствующей битой. Потом просверлите отверстия для оси ротора, которой выступает длинный болт или резьбовой стержень.
Шаг шестой. Изготовление и установка шлифовального ротора
Установите подшипники на свои места, не забыв хорошо смазать, а также подготовьте гайки с шайбами. Ротор изготавливается из кругляков фанеры, которые вырезаются на сверлильном станке. Разводим эпоксидную смолу и поочередно надеваем кругляки на ось, между каждой деталью наносим эпоксидный клей! Когда соберете всю эту гирлянду, хорошенько ее сожмите и дайте клею полностью высохнуть.
Когда клей высохнет, зафиксируйте и отрегулируйте шлифовальный ротор. Это делается с помощью гаек. Закрутите их так, чтобы люфт вала был минимальным, но подшипники не должны быть перетянутыми! Зафиксируйте гайки с помощью суперклея, или просто ставьте по две гайки.
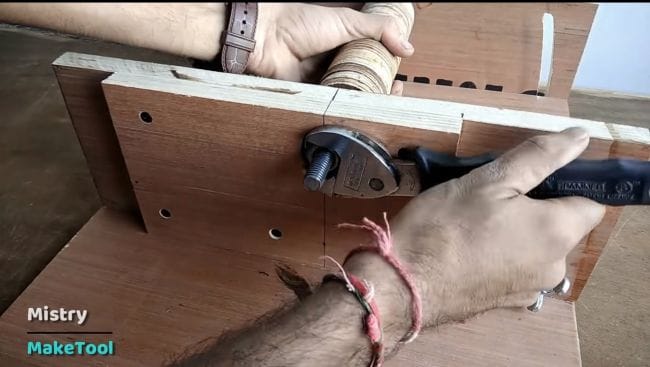
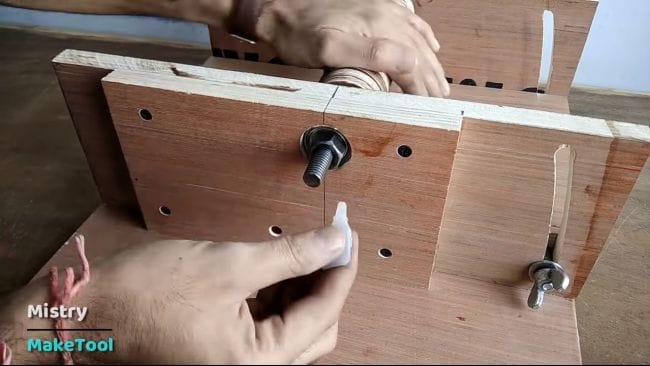
Шаг седьмой. Устанавливаем дрель
Для установки дрели понадобится изготовить небольшой «столик» с кронштейном. Этот столик делается из фанеры. Закрепите патрон дрели на валу и вырежьте детали по высоте. Скрутите «столик», используя саморезы.
Теперь можно изготовить крепежный кронштейн, для этого понадобится фанера или деревянный брус. Делаем необходимые замеры и распиливаем фанеру вдоль на две части. Далее между двумя половинками положите не толстую планку и просверлите на сверлильном станке отверстие такого диаметра, чтобы в него могла потом зайти носовая часть дрели.
Вот и все, кронштейн почти готов. Осталось установить винты, с помощью которых дрель можно будет зажать в кронштейне. Сверлим под винты отверстия и устанавливаем винты. Вам нужно рассверлить посадочные места под шляпки винтов, чтобы они не выступали. Установите винты и залейте шляпки суперклеем или эпоксидкой. Кронштейн можно устанавливать! Наносим клей для дерева, устанавливаем, а с другой стороны притягиваем саморезами.
Закрепите дрель и включите. Она должна отцентрироваться. Потом закрепите «столик» для дрели саморезами. Станок почти готов, осталось доделать ротор!
Шаг восьмой. Шлифовальный ротор
Шлифовальный ротор не будет ровным, его нужно отшлифовать. Для этого включаем станок и проходимся по валу наждачной бумагой или напильниками. Нужно сделать его ровным и гладким, иначе станок будет работать не качественно.
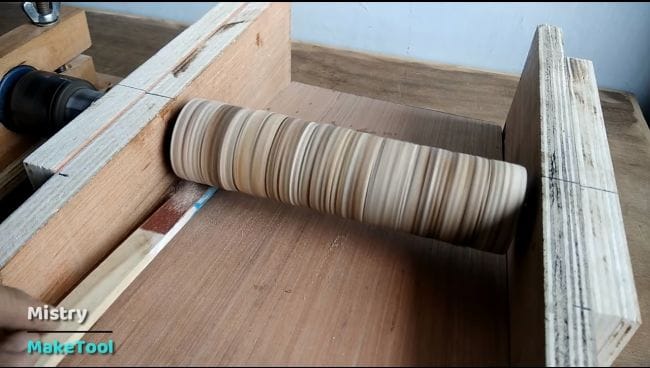
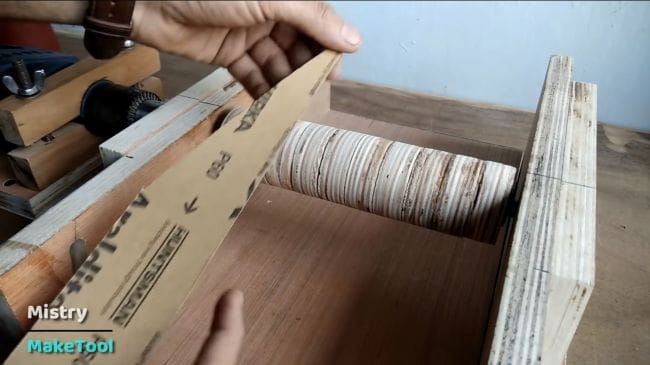
Теперь можно крепить наждачную бумагу. У автора, она, почему-то состоит из двух половинок. Крепим носовую часть ленты к валу суперклеем и потихоньку наматываем. Постоянно наносим суперклей на бумагу или вал при наматывании. Аналогичным образом наматывается вторая половинка, потом концы бумаги окончательно приклеиваются клеем для дерева. Пройдитесь суперклеем по швам, чтобы надежно приклеить наждачную бумагу.
Когда клей высохнет, станок можно испытать! Как можно отметить, собирается он довольно просто, но, как по мне, нужно придумать более простой способ для установки на вал наждачной бумаги. Как пример, ленту можно сделать цельной и использовать горячий клей, как пример. Ну или крепить ее по краям винтами.
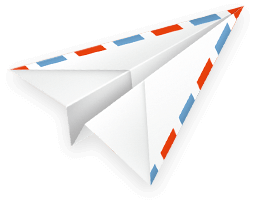
Получайте на почту подборку новых самоделок. Никакого спама, только полезные идеи!
*Заполняя форму вы соглашаетесь на обработку персональных данных
Становитесь автором сайта, публикуйте собственные статьи, описания самоделок с оплатой за текст. Подробнее здесь.Шлифовальный станок из дрели с быстрым креплением
Здравствуйте, уважаемые читатели!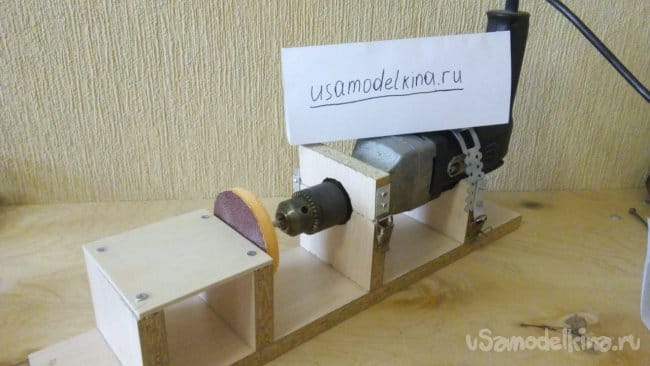
Материалы и инструменты:
- Ножовка по дереву.
- Ножовка по металлу.
- Ручной лобзик.
- Наждачная бумага (зернистость 40).
- Дрель и сверло 3 мм.
- Кернер или шило.
- Молоток.
- Пластина металла для изготовления некоторых деталей (в моём случае это алюминий).
- Набор надфилей.
- ДСП.
- Плоскогубцы.
- Тиски.
- Небольшая мебельная петля.
- Саморезы.
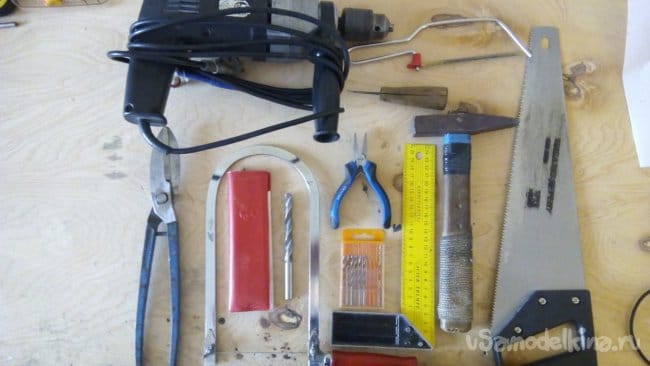
Процесс изготовления.
Шаг 1: разметка материала и распил.
Для начала на материал наносим схемы деталей для распила с учетом толщины реза пилы.
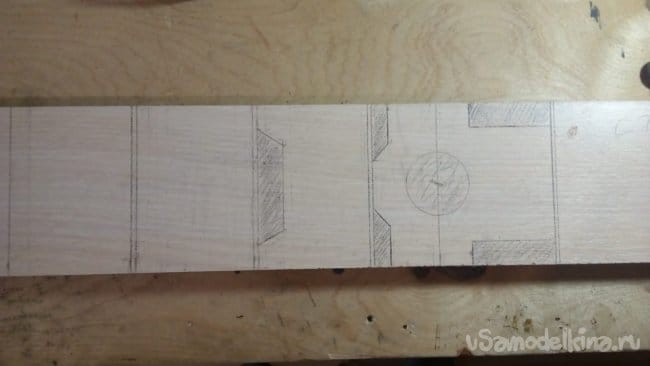
Теперь начнём распил. Для того чтобы всё отпилить ровно, устанавливаем в месте пиления направляющую (у меня это пластина алюминия) и производим распил. Когда деталь отпилена – сдвигаем направляющую к следующей детали.
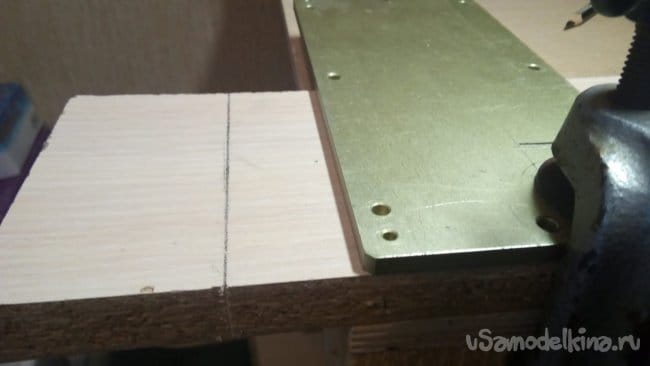
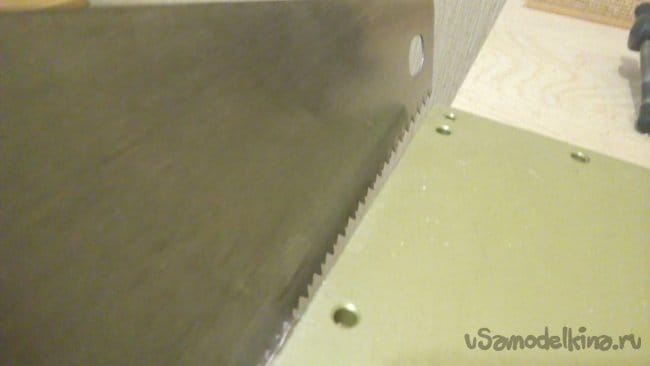
Размеры деталей.
Шаг 2: шлифовка и выравнивание деталей.
Так как вручную отпилить идеально ровно достаточно сложно, поэтому присутствуют небольшие неровности, которые нужно убрать. Для этого кладём грубую наждачную бумагу (у меня зернистость 40) на стол и прижимая к ней деталь шлифуем до выравнивания стороны (здесь важно вовремя остановиться, иначе можно не попасть в размер).
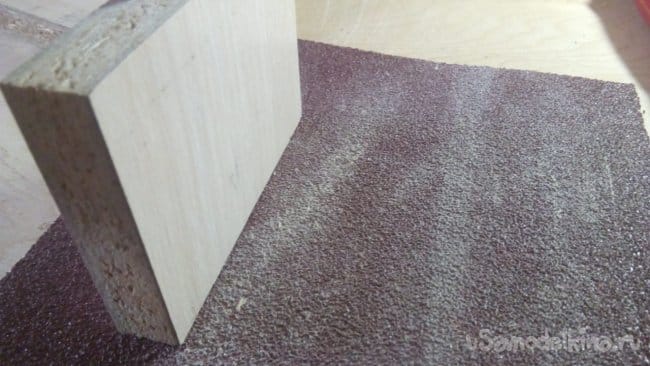
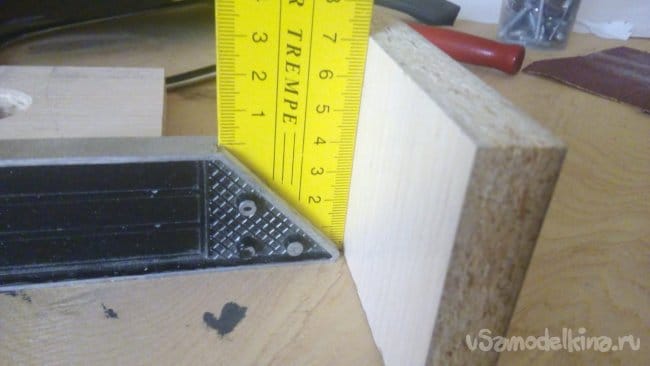
Шаг 3: доработка деталей.
В нашей конструкции присутствуют две детали, требующих дальнейшей работы с ними. Это держатели. На каждой из этих деталей есть заштрихованная часть (мне проще обозначать удаляемые части именно так), которую необходимо выпилить. Вооружившись ручным лобзиком, приступаем. Если дрель не устанавливается из-за небольшого несовпадения размеров – доводим наждачной бумагой (это поможет, если размер крепления меньше необходимого). Теперь, используя ножовку по металлу (из-за более аккуратного реза) распиливаем держатель пополам.
Теперь работаем со вторым держателем, выпиливаем заштрихованную часть и обрабатываем наждачной бумагой.
Шаг 4: изготовление фурнитуры.
Так как дрель в наш станок должна быстро устанавливаться и быстро сниматься, то необходимо использование мебельной фурнитуры: небольших петель и защёлок. Маленьких петель у меня не нашлось, поэтому я использовал самодельные, которые когда-то сделал. Так как у моих защелок ответная часть – зацеп не подходила к размеру детали, я изготовил её самостоятельно.
Вырезаем прямоугольник длинной 40-50 мм и шириной 15 мм.
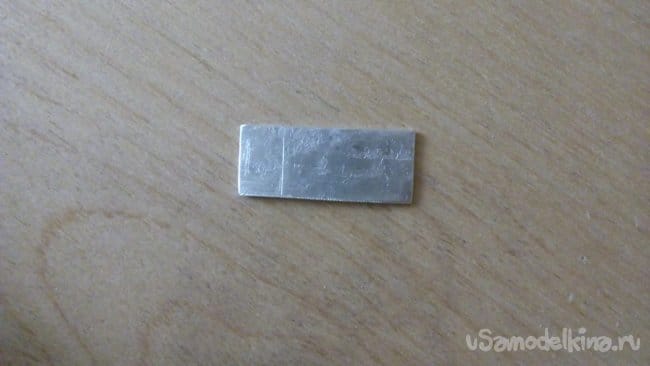
Отступив 5-6 мм от края загибаем чтобы получился крючок.
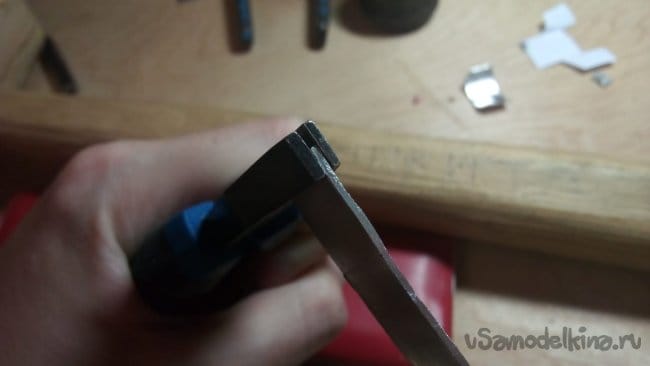
Обрабатываем деталь надфилем.
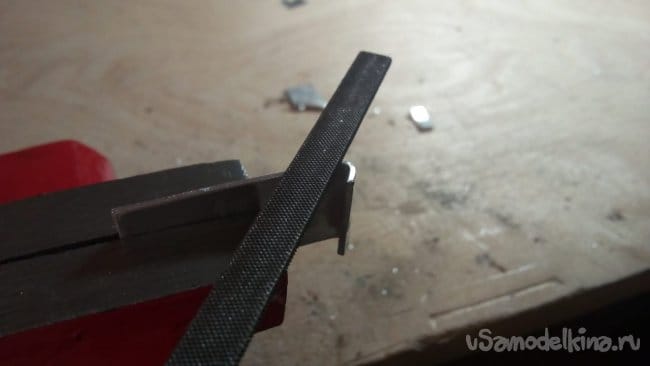
Намечаем шилом два отверстия.
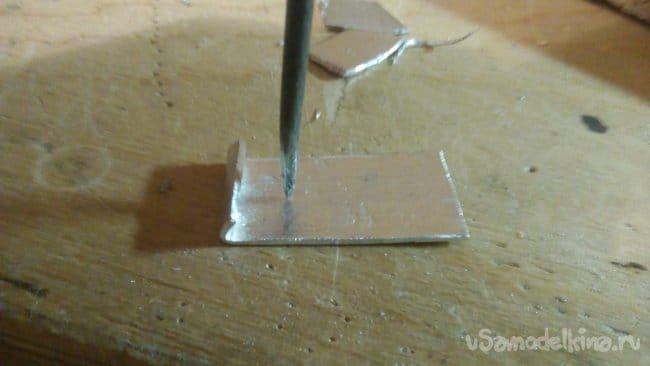
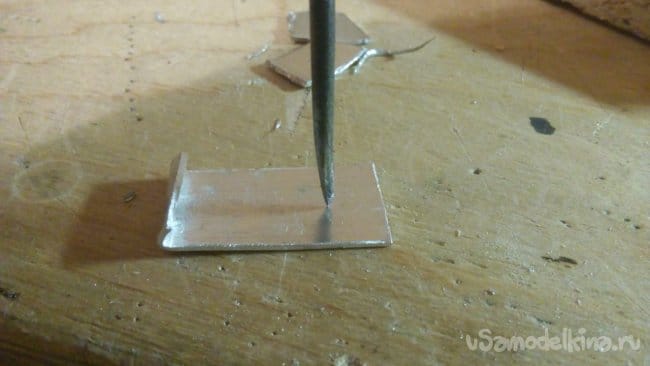
Сверлим.

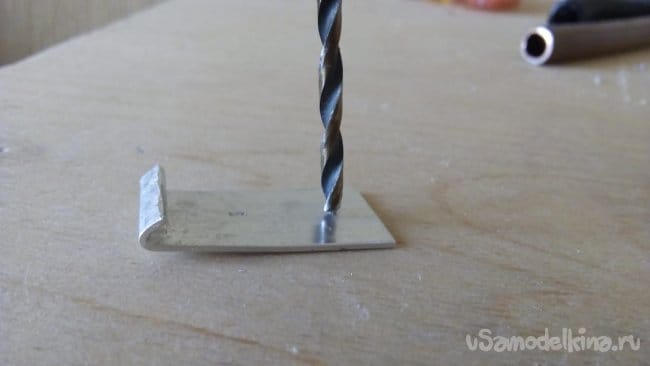
Обрабатываем отверстия.
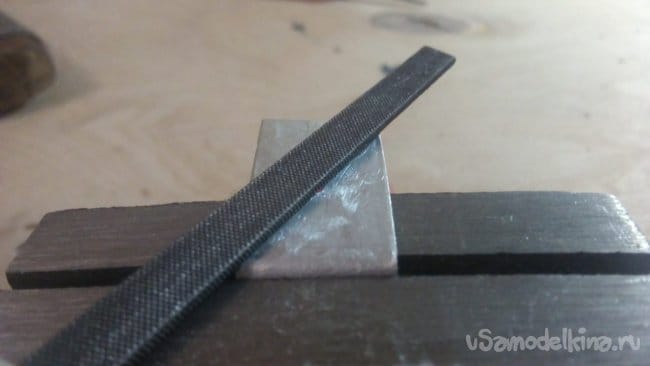
Готовая деталь.
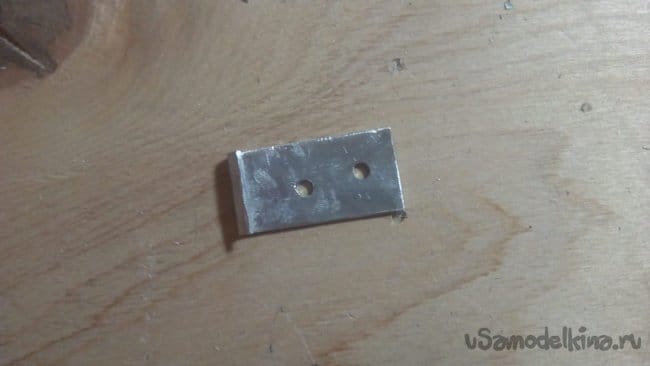
Теперь изготовим ещё одну ответную часть защёлки для крепления тела дрели. Так как в качестве фиксатора дрели я использую прямой подвес, то ответная часть защёлки будет изготовлена специально под него.
Данная деталь изготавливается аналогично предыдущей.
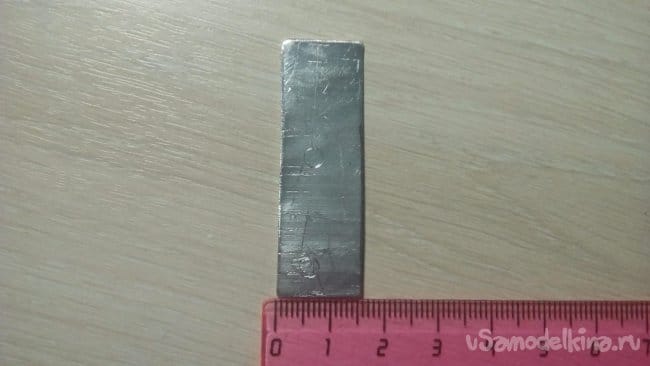
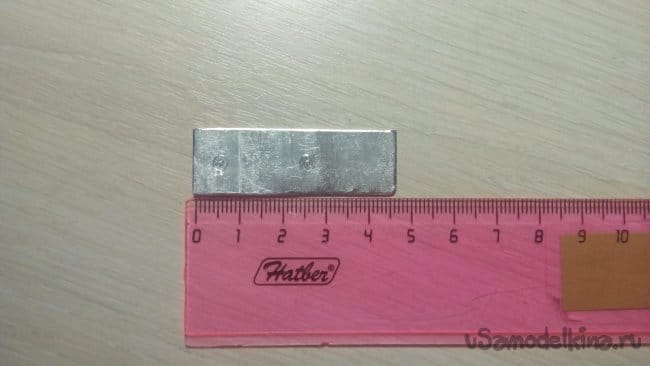
Загибаем край.
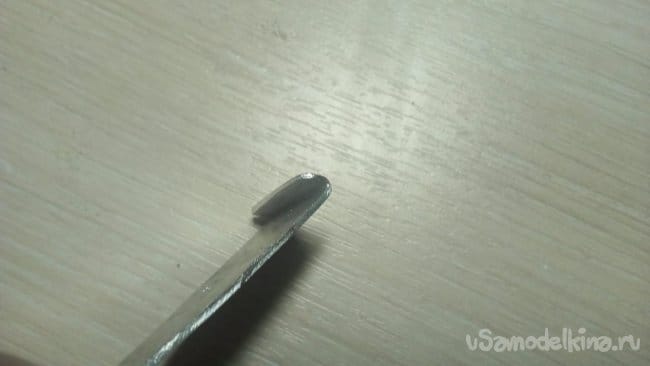
Обрабатываем деталь надфилем, намечаем отверстия по месту.
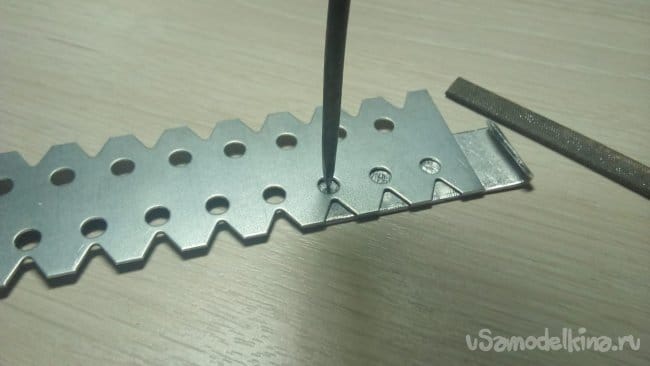
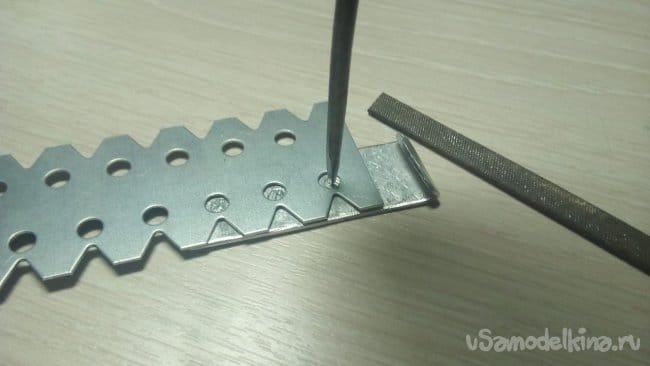
Сверлим.
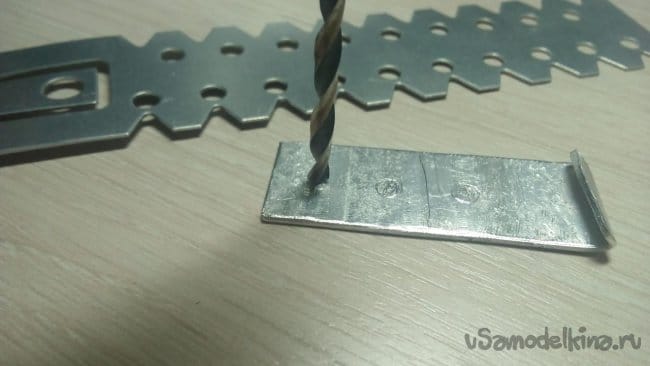
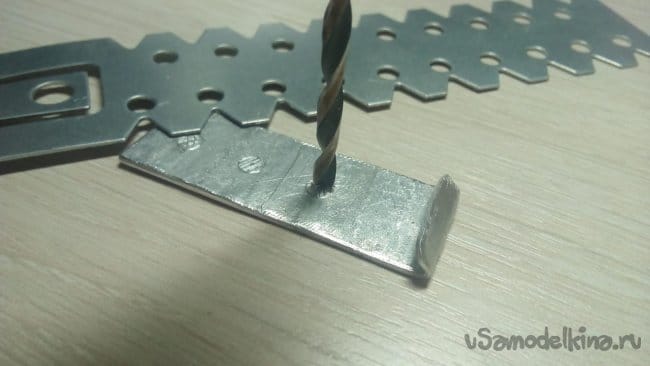
Шаг 5: частичная сборка.
Основные детали готовы, соберём каркас. Собирать конструкцию я буду на саморезы.
Держатели я установил на расстоянии 120 мм друг от друга и разметил места для отверстий под саморезы, просверлил их.
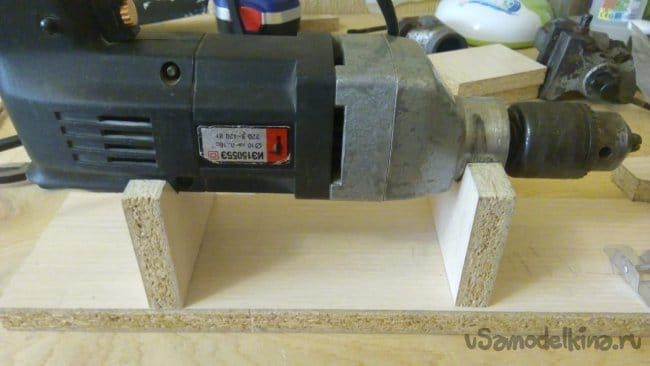
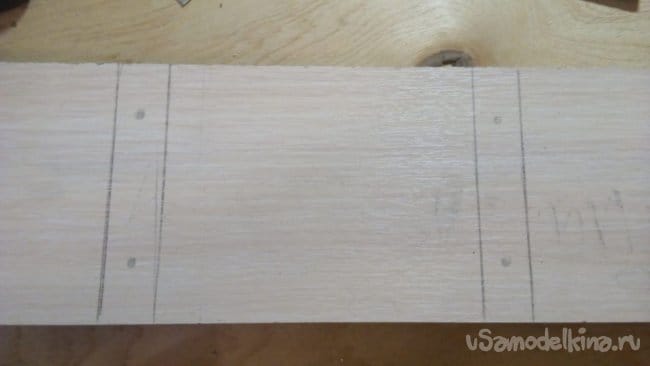
Зенкуем отверстия, что шляпка самореза не торчала.
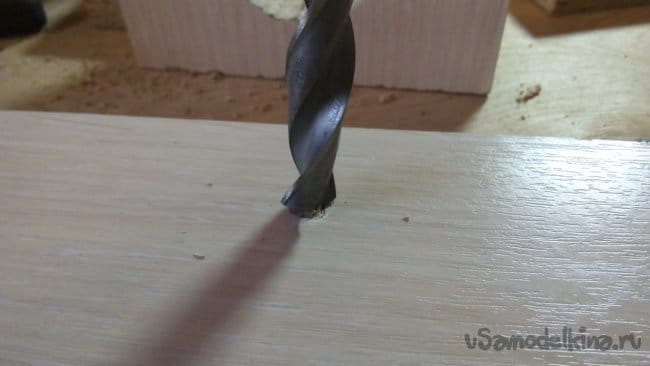
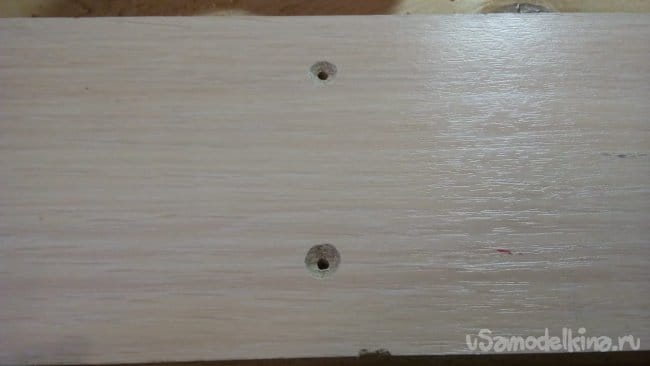
Столик был я установил на расстоянии 105 мм от переднего держателя, и поступил с ним также, как написано выше.
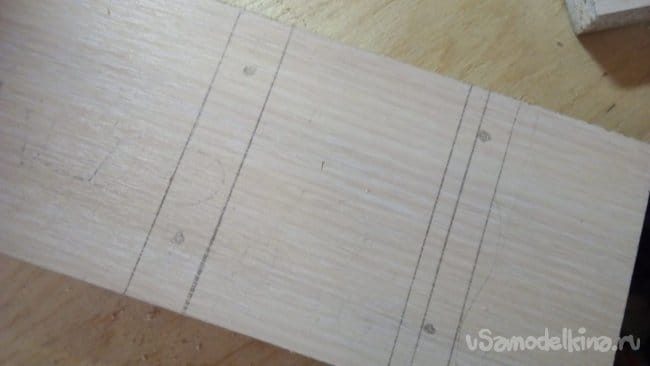
Собираем.
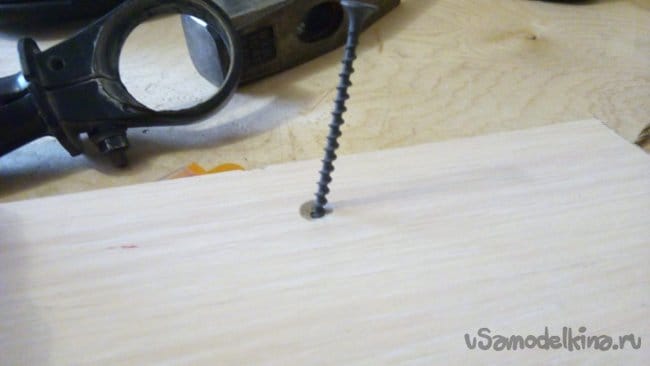
Результат.
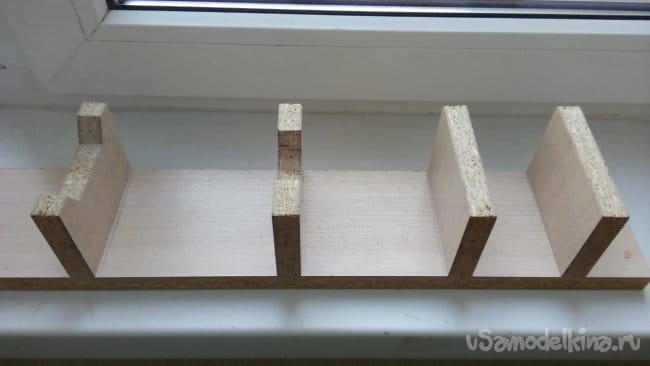
Шаг 6: крепление фурнитуры, полная сборка.
С одной стороны переднего держателя закрепляем петлю, с другой стороны крепим защёлку её ответную часть.
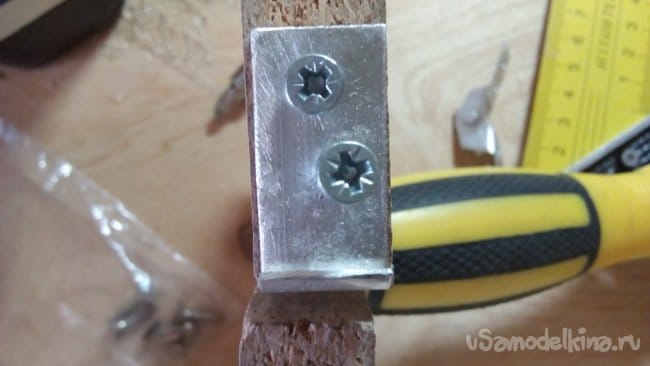
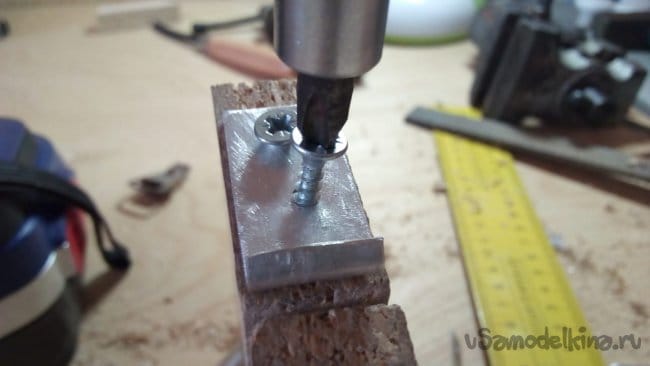
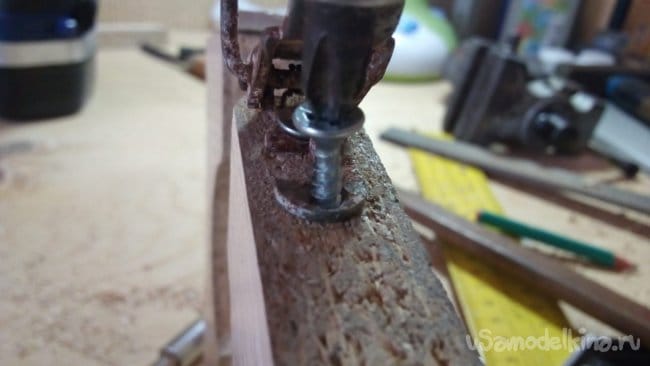
Результат.
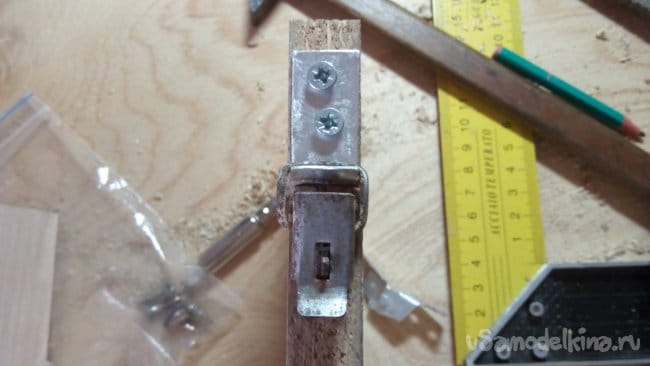
Теперь займёмся задним держателем.
Так как прямой подвес имеет достаточно большую длину нам необходимо его укоротить (мой подвес имел длину 300 мм, я обрезал по четыре секции с каждой его стороны).
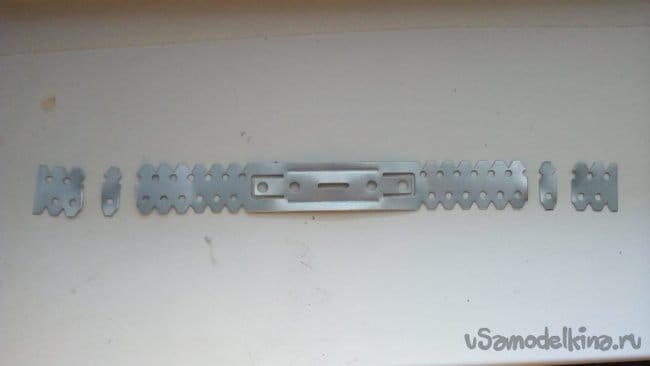
Закрепим подвес на держателе.
Просверлим отверстия для саморезов.
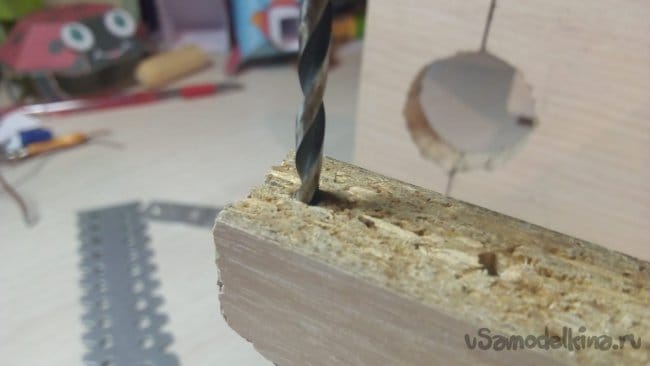
Прикрутим подвес.
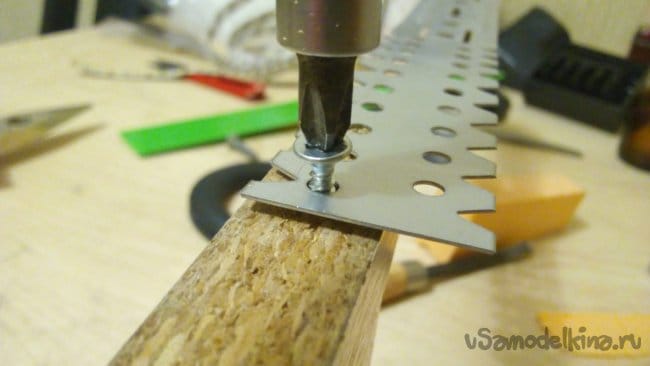
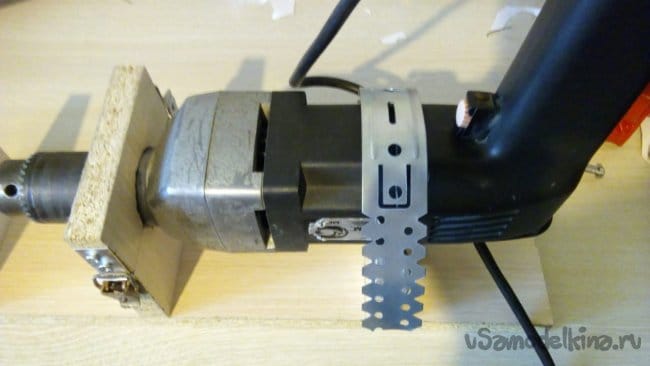
Теперь закрепим на подвесе ответную часть защёлки (использовались винты М3*10).


Теперь закрепим саму защёлку.
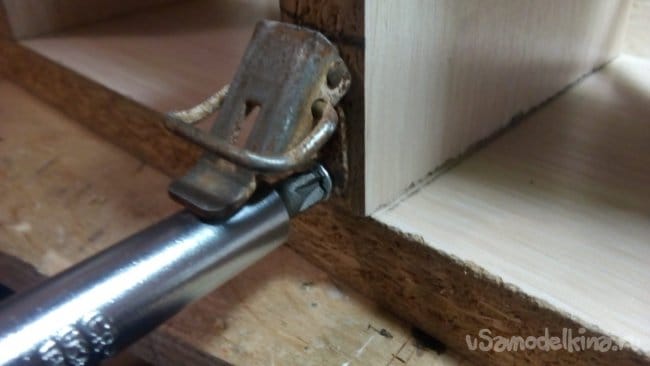
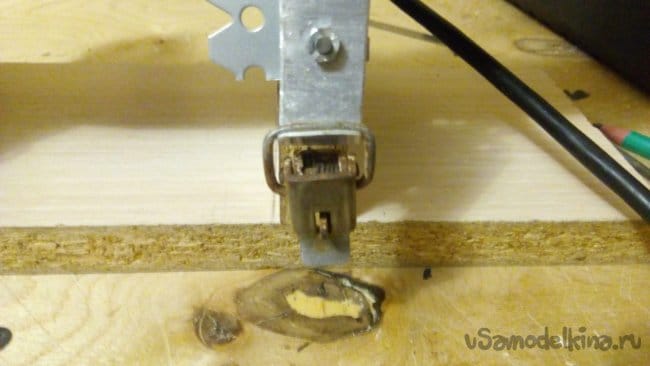
Фурнитура установлена, осталось сделать столик.
Вырезаем из фанеры прямоугольник подходящего вам размера (в моём случае это 100 мм * 97 мм). Обрабатываем края заготовки, сверлим и зенкуем отверстия (отверстия сверлим по месту) и прикручиваем столик.
Результат.
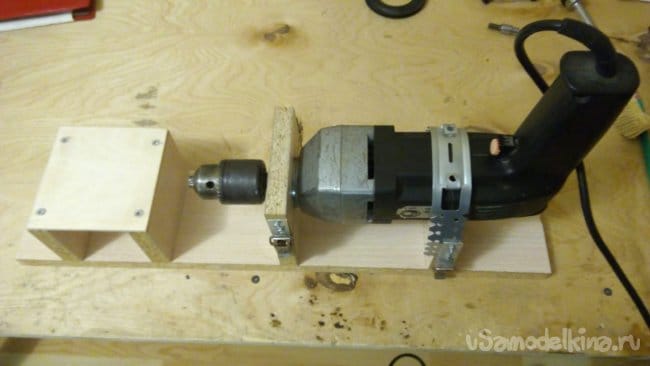
Также, если вы боитесь, что защёлки самопроизвольно откроются (хотя такое событие крайне маловероятно, так как защёлки достаточно надёжные) можно изготовить вот такие «ключики», которыми блокируются защёлки:
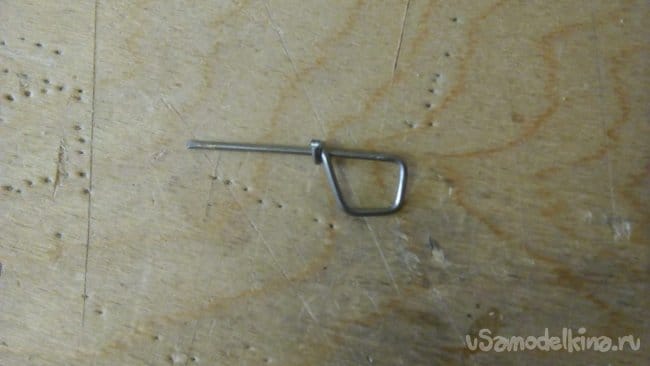
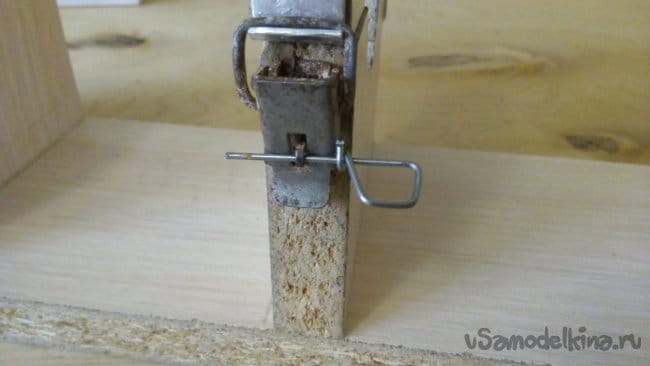
Самоделка в работе.
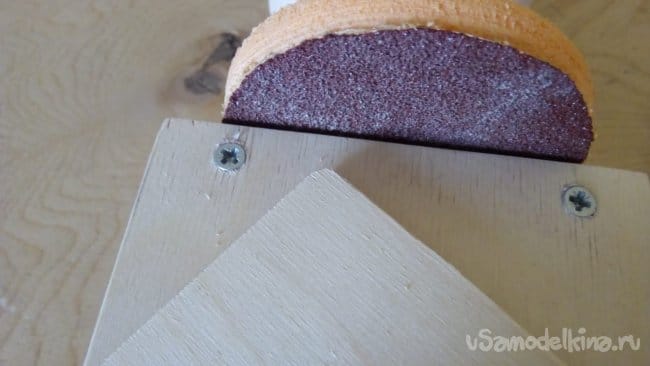
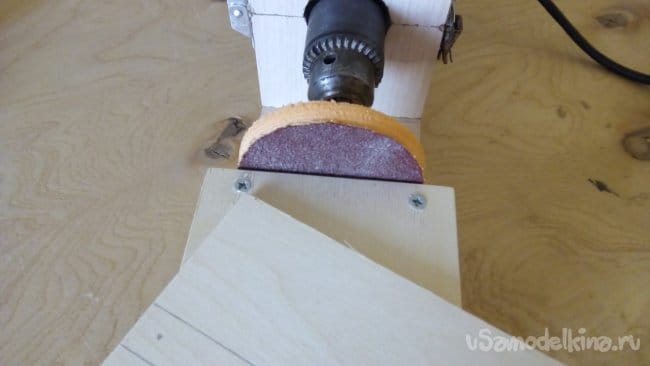
В заключение скажу, что при работе на этом станке не нужно забывать о ТБ, работайте аккуратно и и у вас всё получиться!
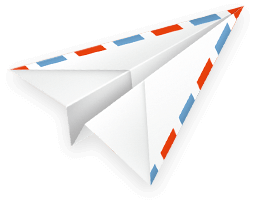
Получайте на почту подборку новых самоделок. Никакого спама, только полезные идеи!
*Заполняя форму вы соглашаетесь на обработку персональных данных
Становитесь автором сайта, публикуйте собственные статьи, описания самоделок с оплатой за текст. Подробнее здесь.чертежи по изготовлению своими руками сверлильного, токарного, фрезерного и шлифовального станков
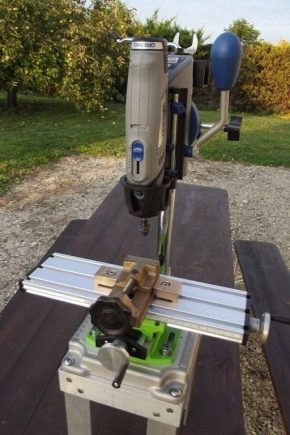
Электрическая дрель – это универсальный инструмент. Помимо использования по прямому назначению (сверлению отверстий), ее можно задействовать для множества видов работ. Ведь патрон дрели позволяет зажимать не только сверла, но и фрезы, шлифовальные элементы и даже деревянные заготовки для токарной обработки. Поэтому из этого инструмента можно сделать несколько видов полноценных домашних станков для обработки и изготовления различных материалов и деталей.
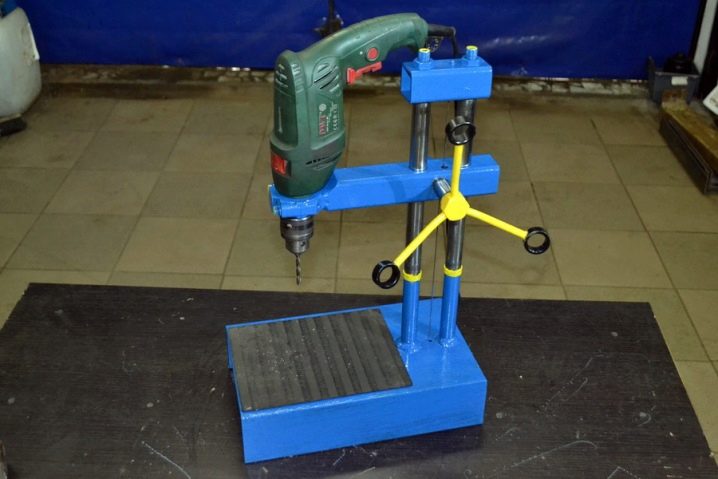
Особенности применения станков
Работа дрелью на весу при удержании инструмента только руками существенно ограничивает ее возможности. Вес инструмента и вибрация не позволяют жестко зафиксировать дрель в нужном положении. Но если продумать и сконструировать специальную станину, где она будет устойчиво крепиться, то обыкновенная ручная дрель превратится в профессиональное, почти промышленное оборудование.
Из дрели можно самостоятельно сделать такие виды станков:
- сверлильный;
- токарный;
- фрезерный;
- шлифовальный.
Причем после замены рабочего или режущего элемента станки становятся взаимозаменяемыми. Предусматривают функцию два в одном, например, сверлильный и фрезерный станок, токарный и шлифовальный. Все зависит от условий монтажа и потребностей владельца.
Мощность станков и их возможности будут зависеть от вида дрели (мощности ее электродвигателя), способу крепления, так как именно она в этом случае выступает главной рабочей частью оборудования.
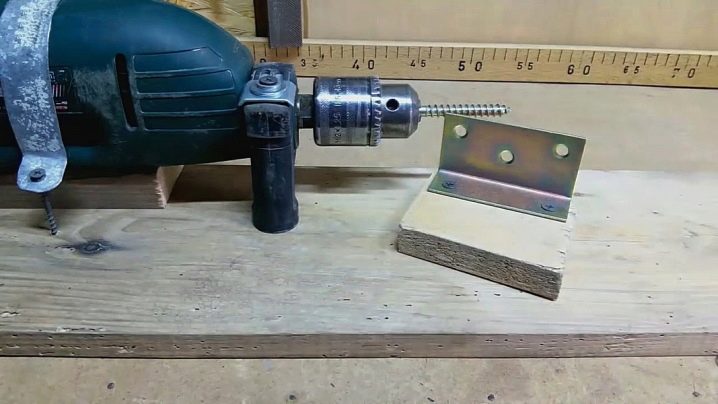
Виды станков
Несмотря на самодельную сборку, каждый станок позволяет изготавливать широкий спектр деталей различной сложности и конфигурации. При правильном монтаже агрегата, он практически не будет уступать профессиональным заводским аналогам по точности и скорости работы.
Если же задействовать и дрель высокой мощности, рассчитанную на длительную бесперебойную эксплуатацию, то на таком станке возможно наладить и серийное производство или обработку разнообразных элементов.
В домашних условиях такие станки способны полностью удовлетворить бытовые нужды по ремонту мебели, автомобиля, велосипеда и многих других вещей повседневного обихода. Они помогут реализовать множество дизайнерских решений без необходимости обращаться в профильные мастерские.
Каждый вид станка предусматривает выполнение разных работ и имеет свои особенности.
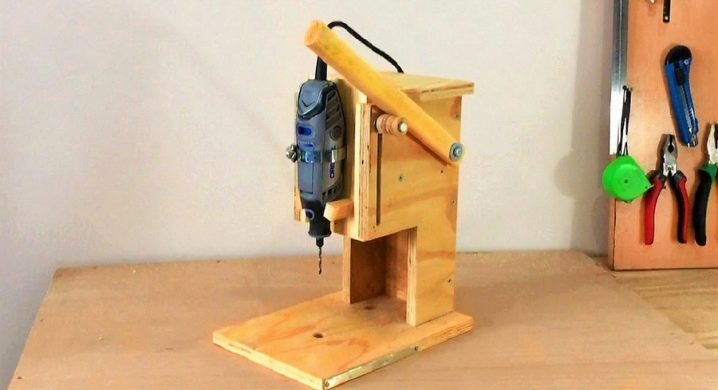
Сверлильный
Сверлильный станок необходим для формирования отверстий в различных поверхностях – как плоских, так и многогранных элементах из дерева, металла, пластика, стекла. Диаметр отверстия и материал детали определяется типом используемого режущего элемента – сверла.
Принцип работы агрегата основан на том, что механизм, обеспечивающий крутящий момент режущего элемента (в нашем случае – дрель) располагается прямо перпендикулярно относительно обрабатываемой поверхности на специальной станине – закрепленном на стойке шпинделе. При опускании шпинделя сверло входит в поверхность и проделывает в ней отверстие.
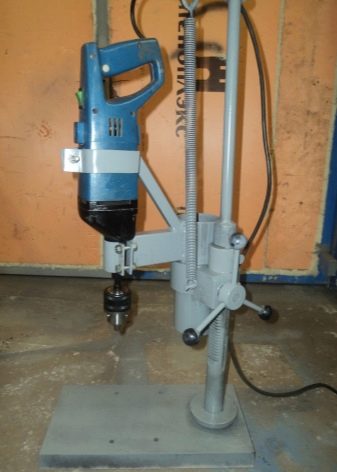
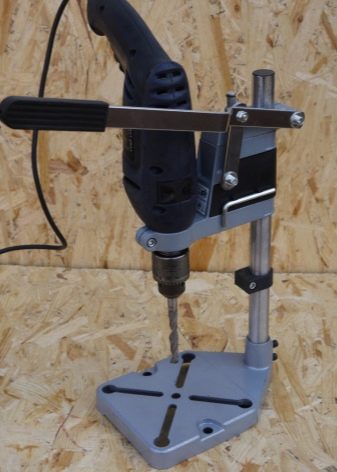
Главное преимущество работы на станке перед ручной обработкой – отверстие получается более точным. Закрепленную дрель можно четко сфокусировать и направить в нужное место.
Можно закрепить дрель на дополнительной продольной планке, размещенной перпендикулярно опускающему/поднимающему шпинделю на его корпусе – это позволит перемещать закрепленный инструмент не только в вертикальном, но и в горизонтальном направлении.
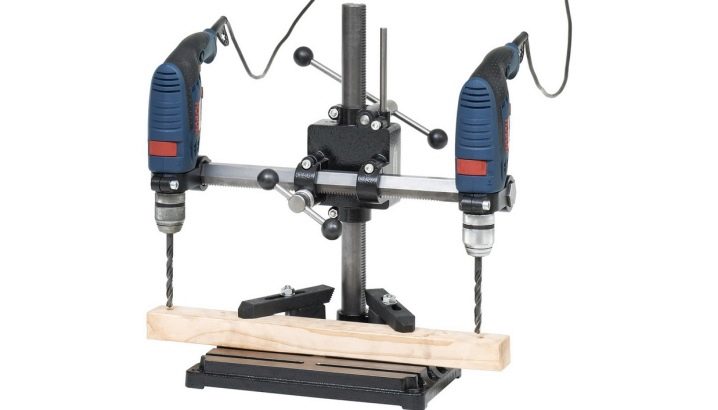
Токарный
Обработка деталей на токарном станке происходит за счет быстрых оборотов заготовки вокруг своей оси, которые обеспечиваются вращающимся от электродвигателя шпинделем, в данном случае – это патрон дрели. Режущий элемент подается вручную сбоку, перпендикулярно вращающейся заготовке, или же проникает внутрь, в зависимости от вида выполняемых работ.
Токарный станок используется для внутренней и наружной обработки металлических, деревянных или пластиковых деталей:
- нарезания резьбы;
- винторезных работ;
- подрезки и обработки торцов;
- зенкерования;
- развертывания;
- расточки.
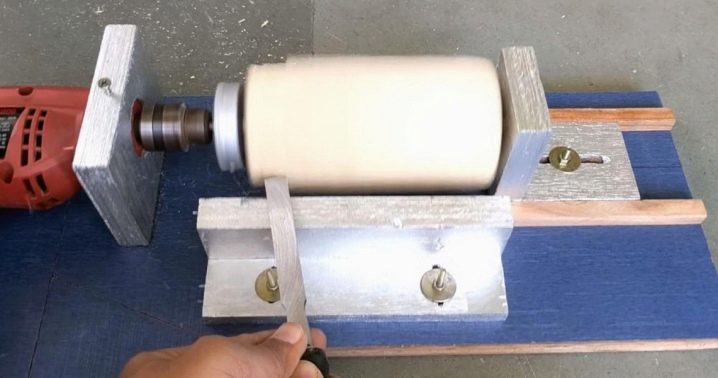
Заготовка зажимается в станке между обеспечивающим крутящий момент элементом (насадкой в патроне дрели) и прижимной направляющей втулкой. Прижимная втулка размещается на специальных полозьях, и фиксируется в нужном положении гайкой. От длины полозьев будет зависеть размер заготовки, которую можно установить в агрегат.
В данном случае, при самостоятельном изготовлении станка, длина полозьев определяется индивидуально по желаниям и потребностям владельца.
Дрель же фиксируется в станине «намертво».
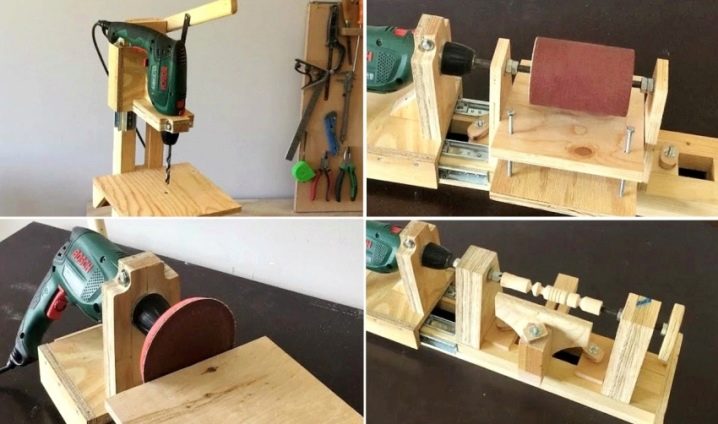
Фрезерный
Фрезерный станок используется для обработки металлических и деревянных заготовок с помощью фрезы – инструмента со специальными резцами, зубьями. Во время работы фреза, оборачиваясь вокруг своей оси, снимается с заготовки часть наружного слоя, придавая ей необходимую форму.
С помощью фрезы производят точильные и другие работы:
- резку;
- заточку;
- торцевание;
- зенкерование;
- развертку;
- нарезание резьбы;
- изготовление зубчатых колес.
В случае с самодельным мини-агрегатом, фрезеровочная насадка зажимается в патрон дрели, закрепленной на станине. Заготовка подается вручную или также фиксируется в специальном зажимном устройстве.
Шлифовальный
При помощи шлифовального станка производят зачистку различных поверхностей, делая их гладкими. Также шлифовка помогает менять форму заготовки, придавать ей нужный конструкционный вид, например, в деревообрабатывающей версии оборудования.
В качестве шлифующего элемента, как правило, используется наждачная бумага. В патрон дрели зажимается специальная насадка, которая имеет шероховатую поверхность – шлифблок.
Существуют насадки, предусматривающие замену шлифующего материала – лист наждачной бумаги фиксируется на их плоскую рабочую поверхность при помощи специальных «липучек», расположенных с тыльной стороны.
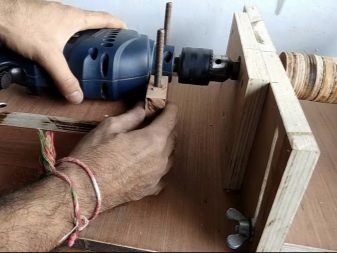
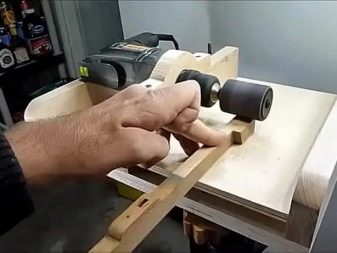
Процесс шлифовки производится за счет обработки заготовки вращающейся в патроне дрели насадкой со шлифующим покрытием. Благодаря абразивному напылению на наждачной бумаге она снимает с обрабатываемой заготовки часть ее поверхности.
При изготовлении станка дрель зажимается и фиксируется в станине в одном положении, а заготовка подается вручную.
В качестве упора для заготовки может использоваться дополнительная подставка – для удобства ее так же, как и в случае с токарным станком, можно разместить на полозьях.
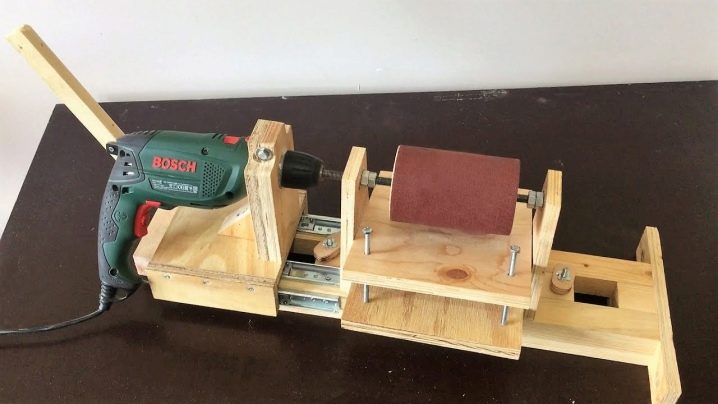
Необходимые материалы и инструменты
Создающим крутящий момент элементом, а соответственно главной рабочей частью в каждом виде станка является дрель. Тип обработки будет в большей степени зависеть от установленной в ее патрон насадки. Поэтому для их сборки понадобятся идентичные материалы.
Для сборки токарного, шлифовального станка:
- прямоугольное металлическое или деревянное основание, станина;
- прижимная втулка;
- прижимная бабка, которая будет крепиться на патрон дрели;
- полозья для прижимной втулки;
- посадочное место для фиксации дрели.
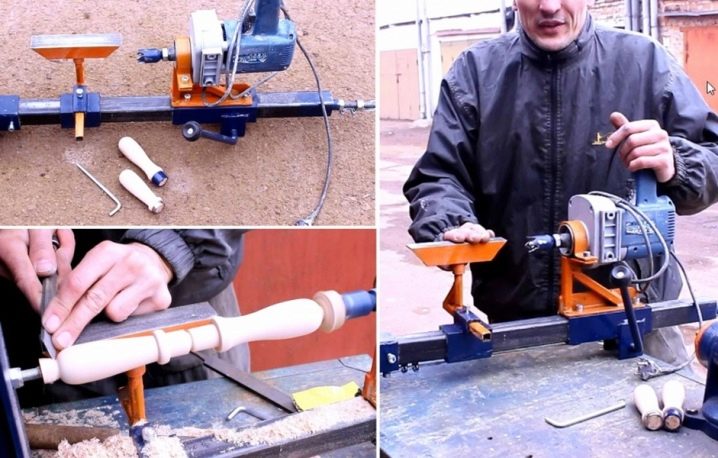
Материалы для сборки сверлильного, фрезерного станка:
- квадратная станина;
- металлическая стойка, на которой будет перемещаться шпиндель с закрепленной дрелью;
- пружина, соответствующая диметру стойки;
- столик для заготовки;
- штифт для крепления столика.
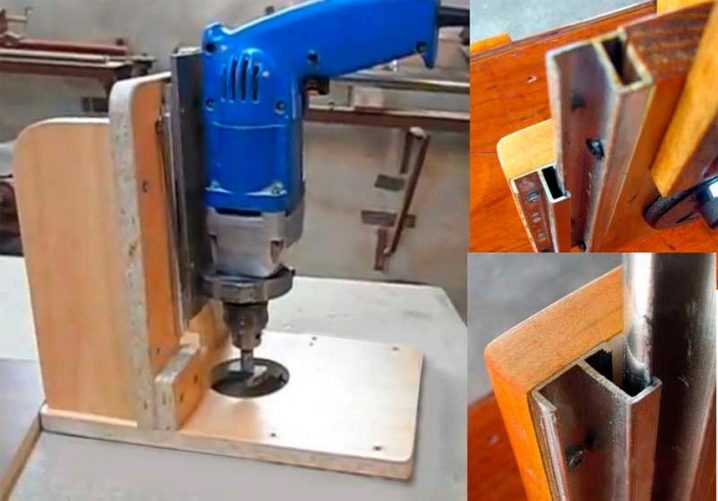
Из инструментов понадобятся:
- отвертка;
- плоскогубцы;
- ножовка по дереву или металлу;
- крепежные элементы – болты, саморезы, гайки;
- сварочный аппарат.
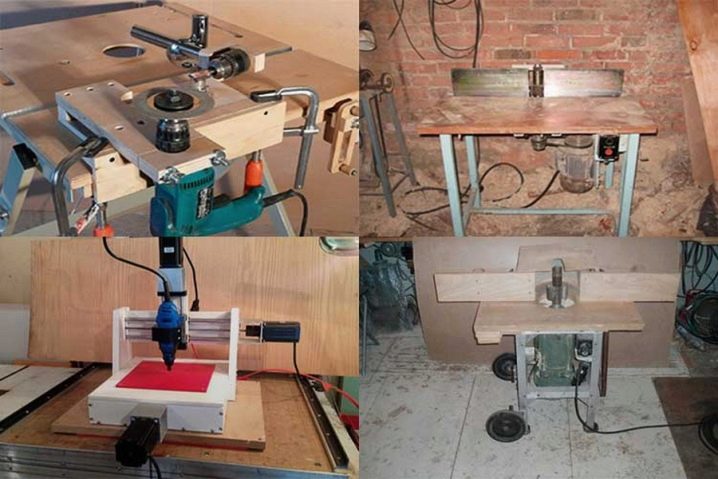
Если планируется изготавливать металлический станок, то необходимым условием будет наличие сварочного аппарата. Так как станок предназначается больше для домашнего использования, его чертежи и размеры составляющих элементов устанавливаются индивидуально.
Алгоритм изготовления
Учитывая, что по типу обработки домашние станки будут взаимозаменяемыми, а решающую роль будет играть установленная в дрель насадка, рассмотрим два основных варианта самодельных агрегатов – горизонтального и вертикального.
Порядок сборки вертикального станка таков.
- Вырезать из куска металла или дерева квадратную основу 50 на 50 см, толщиной от 10 до 20 мм.
- Точно по центру на расстоянии 1-2 см от края высверлить в ней отверстие для монтажа стойки. Диаметр стойки должен быть не менее 5 см.
- Установить стойку, отцентровать ее при помощи уровня и приварить сварочным электродом. Если изготавливается деревянный станок и стойка будет деревянной, то жестко зафиксировать ее саморезами.
- Дрель при помощи металлических хомутов закрепить на подвижном элементе, который будет надеваться на стойку, образуя опускающий/поднимающий шпиндель.
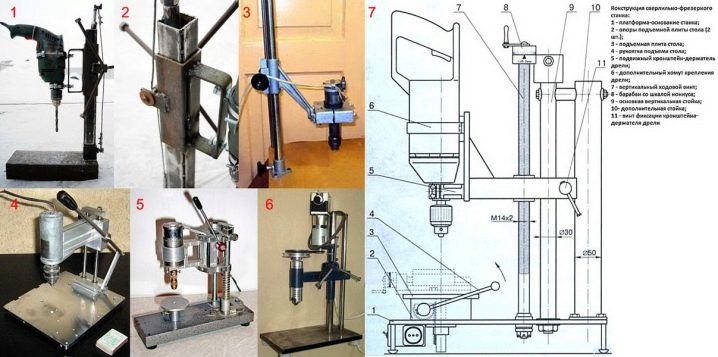
- Надеть пружину на стойку. Ее длина должна быть не менее 2/3 стойки.
- Насадив дрель на стойку, отметить место, куда будет попадать сверло при опускании шпинделя.
- Соответственно этому месту вырезать в станине крест-накрест две сквозные ложбины.
- В ложбину на штифте с резьбой устанавливается столик, на котором будет крепиться заготовка. С нижней стороны на штифт накручивается гайка, она будет фиксировать столик в нужном положении. С наружной стороны прикрепить столик к штифту можно также гайкой, утопив ее в поверхность столика, чтобы она не мешала укладке заготовок.
- Важно, чтобы после фиксации гайкой длина наружной части штифта была заподлицо с верхней поверхностью столика.
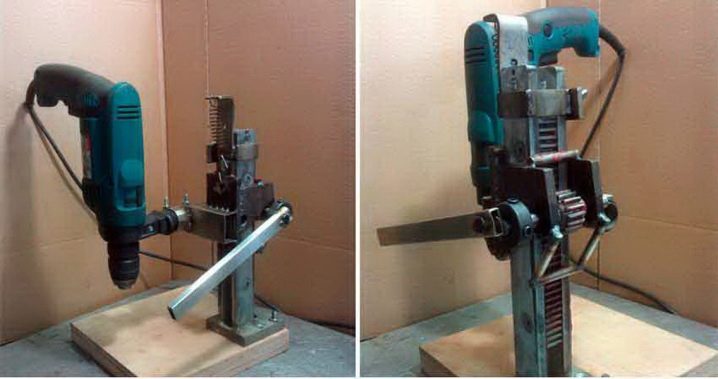
На столик укладывается заготовка (при необходимости фиксируется струбцинами) и по ложбинкам перемещается в нужном направлении. Дрель опускается вручную, обратно поднимается за счет пружины. Чтобы переоборудовать станок во фрезерный или шлифовальный, достаточно заменить сверло соответствующей насадкой – фрезой или шлифблоком.
Алгоритм сборки горизонтального станка выглядит так.
- Вырезать прямоугольную станину – размеры определяются индивидуально.
- На одном краю закрепить посадочное место для дрели с ложбиной в верхней части соответствующей размерам инструмента.
- Зафиксировать на нем дрель хомутом.
- Вдоль станины вырезать сквозную ложбину для штифта, а по краям установить два металлических уголка, по которым будет перемещаться прижимная втулка.
- Ширина прижимной втулки должна точно соответствовать расстоянию между направляющими уголками (полозьями). Снизу в нее вкручивается штифт с резьбой, который будет перемещаться в ложбине.
- Переместив втулку вплотную к патрону дрели, определить место, где будет установлена специальная бабка для фиксации заготовок.
- Прикрепить к втулке бабку с размещенным по центру металлическим конусообразным штырем.
- Втулка фиксируется в нужном положении (для зажима заготовки) гайкой, накручиваемой снизу на штифт.
Так же, как и предыдущий, этот станок может использоваться не только как токарный, но и как фрезерный или шлифовальный. Нужно лишь зажать в патроне дрели необходимый рабочий элемент – фрезу, шлифблок, сверло.
В обоих вариантах необходимо предусмотреть для станины специальные регулирующиеся ножки.
Если станина будет плашмя ложиться на верстак или стол, станет невозможным регулировка и фиксация прижимной втулки на горизонтальном станке или столика для заготовок на вертикальном.
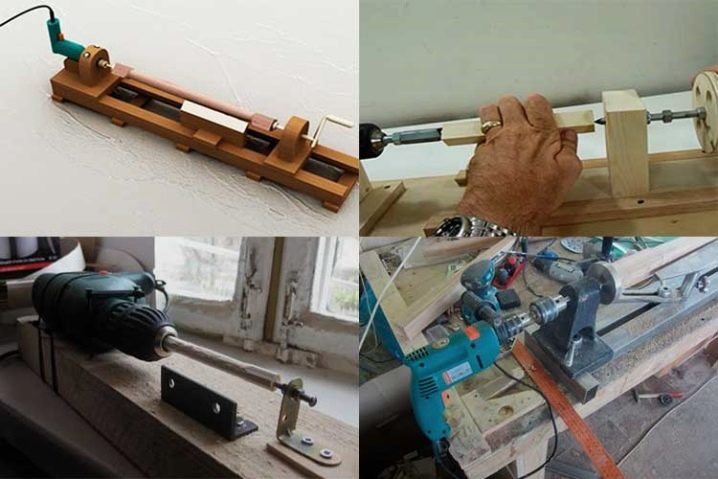
Советы мастеров по эксплуатации
Рекомендуется изготавливать такие станки только из металлических элементов – станина, прижимная втулка, стойка. Деревянная конструкция проще в сборке, но имеет меньший срок эксплуатации. Она может выйти из строя даже от несущественных механических повреждений – случайных ударов.
Кроме того, деревянная стойка выдерживает меньшее давление, на таком станке будет сложнее просверлить отверстие в твердом материале.
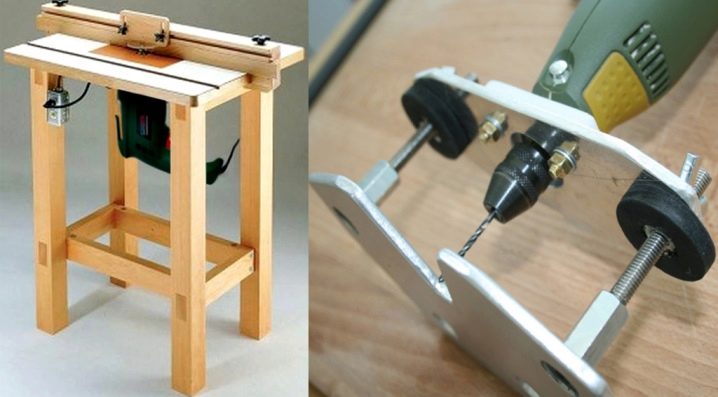
Выбирать модель дрели рекомендуется только из серии профессиональных инструментов, рассчитанных на долговременное и частое использование.
Следует заранее подумать о том, что, возможно, придется обрабатывать особо прочные материалы, поэтому лучше, чтобы дрель была с ударной функцией.
Важно понимать, что мощность ручной дрели и скорость ее оборотов значительно меньше, чем у электрических двигателей на станках промышленного назначения. Поэтому не следует перегружать инструмент, чтобы не сжечь его двигатель.
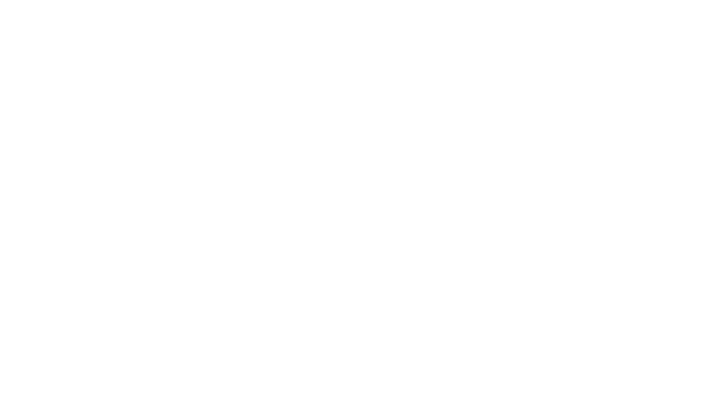
О том, как сделать из дрели станок своими руками, смотрите в следующем видео.
Шлифовальный станок из дрели и фанеры » Полезные самоделки
Третий станок для домашних работ — Шлифовальный из дрели.
В интернете посмотрел разные поделки на эту тему. И вот как я это делал:
Изготовление станка
1. Отрезал
- 4 деревянных бруска (30х30х600)мм,
- четыре рейки (10х20х600)мм,
- один брусок (30х20х200)мм,
- один куб (30х30х30)мм.
3. Из фанеры толщиной 10мм вырезал дощечки и саморезами собрал устройство крепления дрели. Установил его в левой части станины.
4. Из такой же фанеры и одного брусочка (30х30х200)мм изготовил опорную полку. Брусочек прикрепил снизу полки. В концах брусочка просверлил по одному отверстию для крепления полки к станине двумя специальным прижимными устройствами.
5. Изготовил специальные прижимные устройства крепления полки к станине.
6. Закрепил полу к станине этими устройствами с двух сторон.
7. Собрал станок и вот что получилось.
изготовления из дрели и винчестера
Для самодельной шлифмашинки в домашнем хозяйстве найдется множество вариантов применения. Речь идет не только о частном доме или приусадебном участке, но и о жилье в многоквартирном доме. С ее помощью можно обработать любую поверхность. Степень очистки зависит от типа и применяемых абразивных материалов. В отличие от промышленных моделей устройство, собранное своими руками, будет выгодно отличаться стоимостью, так как бюджет конструкции будет зависеть только от мастера. Обладая слесарными навыками и базовыми знаниями в электрическом деле, можно без особого труда собрать прибор самостоятельно.
Принципиальное устройство шлифовальной машинки
Без доскональных знаний конструкции шлифовальных машинок невозможно собрать качественное устройство своими руками. Прежде чем перейти к строению, познакомимся с самыми распространенными типами шлифмашин:
- Угловая. Проще говоря, болгарка. Расходными материалами являются диски. Зачистные круги предназначены для шлифования поверхности. Регулировка давления осуществляется вручную.
- Ленточная. Обработка поверхности выполняется шлифовальной лентой. Подходит для работ только с плоскими поверхностями.
- Дельташлифмашина. Для обработки изделий с криволинейной структурой.
- Вибрационная. Оптимально подходит для чистовой обработки ровных плоскостей.
Помимо вышеперечисленных существует еще несколько аппаратов, которые менее распространены:
- прямая;
- полировальная;
- эксцентриковая.
Независимо от того, является ли прибор заводским или собранным своими руками, основными элементами конструкции являются:
- Привод. От его мощности зависит производительность устройства. В аппаратах, собранных своими руками, используют привод электрического типа, однако встречаются пневматические самоделки, работающие от компрессора.
- Редуктор. Передает крутящий момент от привода на рабочий инструмент. Базовой частью редуктора является шпиндель.
Редуктор является неотъемлемой частью таких инструментов, как болгарка или дрель. Некоторые модели, особенно собранные своими руками, обходятся без него.
- Рабочая платформа. На нее крепят абразивный материал. Для этого можно использовать круги, ленты, диски.
- Корпус. Защищает конструкцию от механических повреждений и пыли, поэтому многие заводские модели оснащены системами пылеулавливания. Материалы, применяемые для изготовления прибора своими руками, как правило, не способны конкурировать с качественными полимерами, которые используют в производстве профессионального инструмента.
- Система управления. Включает в себя отключение питания, а также регулировку оборотов абразива.
Варианты самодельных конструкций
Сделать шлифовальную машинку своими руками несложно. Главное, чтобы она соответствовала видам работ, которые мастер планирует выполнять. С экономической точки зрения лучше взять комплектующие, находящиеся под рукой. Если составные части прибора придется покупать, то бюджет устройства, изготовленного своими руками, будет сопоставим с заводской моделью. При прочих равных условиях предпочтение лучше отдать промышленному инструменту, ведь его качество несоизмеримо выше.
Рассмотрим несколько приборов, сделанных своими руками. Возможно, какой-то из них подойдет именно вам.
Шлифмашинку из болгарки своими руками
Как следует из названия, болгарка предназначена для шлифования. Зачистные диски успешно справляются с грубой работой: снятием старой краски, удалением наплывов металла или следов коррозии. Для более тонкой очистки продаются специальные насадки из наждачного листа различной зернистости.
Модели для бытового использования работают в одном режиме, причем количество оборотов достигает 15 тыс. за минуту при среднем показателе в 11 тысяч. Такая скорость отлично подходит для распиливания материалов, однако для шлифовальных работ она велика.
Мотор болгарки обладает избыточной мощностью. Для полирования достаточно будет 300–400 Вт.
Шлифмашинка из болгарки будет обладать большим весом по сравнению с заводским инструментом, однако имеется возможность приспособить самоделку под себя, что повысит комфорт при шлифовке.
Для УШМ можно изготовить простую насадку, которая превратит аппарат в миниатюрную ленточно-шлифовальную машинку. В этом случае работы выполняются без защитного кожуха.
Если нет желания использовать приспособления, можно отрегулировать количество оборотов двигателя. Самостоятельная модернизация схемы потребует профильных знаний в электротехнике.
На профессиональных аппаратах можно выставить количество оборотов вручную, правда, их стоимость начинается от 200 долларов.
Делаем шлифмашинку из дрели
Из дрели своими руками можно собрать производительную ленточно-шлифовальную машину. В данном случае инструмент выступает в качестве привода. Сама конструкция проста и не требует значительных вложений. Для изготовления своими руками понадобятся следующие материалы:
- металлические пруты с резьбой и без нее;
- профильная труба;
- фанера;
- стальной лист;
- подшипники;
- метизы;
- столярный клей.
Следует позаботиться о наличии слесарного инструмента, инвертора и приспособлений для распиливания металла.
Этапы выполнения работ:
- Изготовление шкивов. Ведущий и ведомый шкивы предназначены для передачи крутящего момента от дрели к шлифмашине. Их изготавливают из фанеры.
- Изменением диаметра можно получить нужный крутящий момент. Один шкив состоит из нескольких кругляков, которые соединяются с помощью столярного клея. В центре необходимо просверлить отверстия под стальные пруты. После высыхания клея заготовки дорабатывают, делая паз, который должен соответствовать ширине приводного ремня.
- Изготовление ведущего и ведомого валов. Их также изготавливают из фанеры по аналогии со шкивами. Для них следует приготовить больше кругляков.
- Собираем нижнюю часть. Для этого понадобится профильная труба. В первую очередь необходимо сделать крепления подшипников и соединить их. Это основа под рабочий вал.
- Делаем верхнюю часть. К ней будет крепиться механизм натяжения.
- Изготавливаем упорную часть из стального листа.
- Установка привода. Обратите внимание: для нормальной работы лучше взять мощную дрель.
- Финишные работы. Остается только установить шкивы, натянуть приводной ремень и собрать защиту. После этого собранное своими руками приспособление нужно покрыть краской.
Для мелких и точных работ лучше приобрести компактные насадки барабанного или тарелочного типа в зависимости от типа работ.
Самодельная шлифмашинка из компьютерного винчестера
Из старого жесткого диска можно собрать небольшое шлифовальное приспособление, главным преимуществом которого будет полное отсутствие вложений за исключением затрат на абразивные круги. Процесс изготовления своими руками выглядит следующим образом:
- Раскрываем корпус и удаляем все элементы, расположенные рядом с магнитным диском.
- По размеру верхней части накопителя вырезаем круг из наждачной бумаги нужной зернистости.
- С помощью двухстороннего скотча закрепляем бумагу на поверхности диска.
- Изготавливаем кожух, защищающий от пыли или абразивного зерна.
- Для запуска конструкции винчестер необходимо подключить к блоку питания компьютера.
Такой прибор, сделанный своими руками, позволит выполнять мелкие работы, такие как шлифовка контактов, заточка пилочек или пинцетов. Скорость вращения зависит от заводских параметров. Среднее значение – 7200 оборотов в минуту.
Шлифмашинка, изготовленная своими руками, не будет обладать привлекательным внешним видом заводского инструмента, однако хорошая производительность и низкие затраты на сборку компенсируют этот недостаток.
А вы пробовали собирать шлифовальную машину своими руками? Что использовали в качестве привода? Поделитесь вашим опытом изобретения в комментариях.
Цилиндрический шлифовальный станок из дрели » Полезные самоделки
Четвертый мой самодельный станок для домашних работ — шлифовальный цилиндрической формы.Станина взята от третьего, изготовленного мною шлифовального станка на дрели. Откручиваем специальное прижимное устройство и снимаем полку. На это место закрепляем другой узел — узел для цилиндрической шлифовки.
Вот как он выглядит:
Изготовление станка
1. Корончатым сверлом вырезаем из 10 мм фанеры 8 кружков диаметром (8-10)см.
2. На резьбовой шпильке диаметром 8мм собираем эти кружки в цилиндр. Все кружки проклеиваем и гайками прижимаем в один цилиндр. Цилиндр обрабатываем наждачной бумагой.
3. На циркулярной пиле вырезаем вдоль цилиндра паз (5-6)мм глубиной. Этот паз нужен для крепления наждачной бумаги на цилиндр. Закрепляется наждачная бумага саморезами с двух сторон.
4. Далее вырезаем На циркулярной пиле две одинаковые дощечки в форме равнобокой трапеции. Перьевым сверлом просверливаем отверстия до половины толщины фанеры. В эти отверстия вставляем подшипники.
5. Вырезаем из той же фанеры два одинаковых прямоугольника и скрепляем их дверными петлями. Снизу по середине прикрепляем брусок (30х30х230)мм. В бруске с двух сторон делаем по одному отверстию, для крепления всего узла к станине специальным прижимным устройством. Далее весь узел собираем.
6. Узел устанавливаем на станину. Закрепляем специальным прижимным устройством. Закрепляем дрель. Станок готов к работе.
7. Доска на шарнире может применяться для прижима обрабатываемой детали к вращающемуся цилиндру с наждачной бумагой.
Сверлильный станок из дрели своими руками
Уважаемые посетители сайта «В гостях у Самоделкина» из представленного автором материала вы узнаете как можно самостоятельно сделать бюджетный сверлильный станок из обычной электрической дрели.Каждый мастеровой человек хотел бы иметь в своем хозяйстве подобный станочек, потому как в сравнении с заводскими аналогами обойдется в десятки раз дешевле, а если все запчасти и комплектующие есть в наличии, то и вообще бесплатно.
Автором данного станка является Игорь Стасюк, за что ему Большое Спасибо, поделился пошаговыми фотографиями сборки станка с народом. Конструкция довольно интересная и в тоже время простая. На основание из листа металла 3 мм наварены уголки и 4 ножки, на данную плиту наварен шток 500 мм из проф трубы квадратного сечения, ползун выполнен из 2 х сваренных в трубу уголков и надеты на подъемную колонну с зазором, чтоб ползун мог перемещаться по колонне вверх и вниз. Подъемный механизм приводится в действие за счет тросика натянутого вот верхней точки к нижней, а на ползуне тросик делает несколько витков.
И так, давайте внимательно рассмотрим, что конкретно понадобилось автору для сборки станка? А так же весь поэтапный процесс.
Материалы
1. листовой металл 3 мм
2. арматура
3. уголок
4. тросик
5. дрель
6. тиски для заготовок
7. болты, гайки, шайбы, граверы
8. зажим для дрели
9. краска
10.проф труба квадратного сечения
11. сверло
Инструменты
1. сварочный аппарат
2. болгарка (УШМ)
3. дрель
4. напильник
5. тиски
6. струбцина
7. штангенциркуль
8. линейка
9. уголок
10. уровень
11. наждачная бумага
12. кисть
13. ножовка по металлу
14. наждак
Процесс создания сверлильного станка из дрели.
И так, первым делом автор изготавливает основание станка из листового металла 3 мм, выпиливает заготовку при помощи болгарки (УШМ) А в нижнюю часть наваривает 2 уголка и 4 ножки из стального прута либо арматуры. Длина ножек должна быть одинакова, дабы не было перекоса станины.
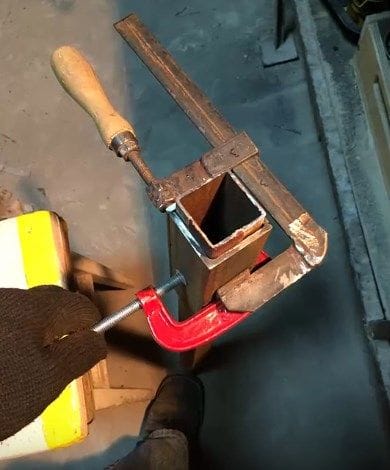

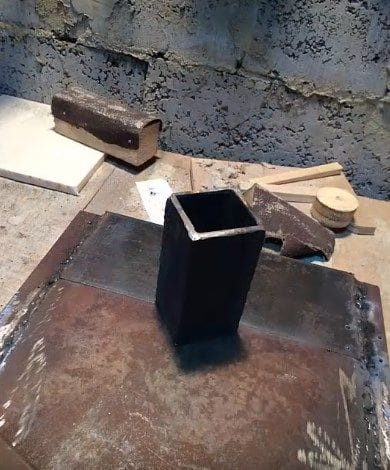
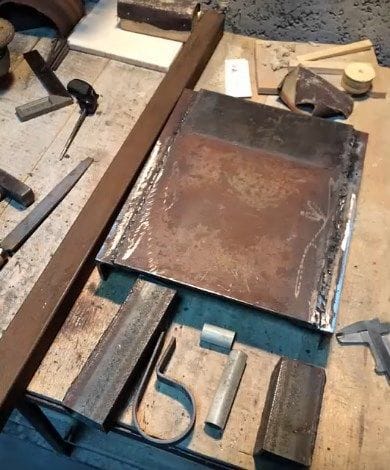

Занимайтесь больше творчеством, растите над собой, созидайте и успех обязательно придет к Вам.
На этом заканчиваю статью. Большое спасибо за внимание!
Заходите в гости почаще, не пропускайте новинки в мире самоделок!
Статья представлена в ознакомительных целях!
Источник
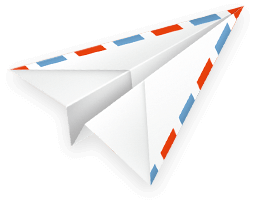
Получайте на почту подборку новых самоделок. Никакого спама, только полезные идеи!
*Заполняя форму вы соглашаетесь на обработку персональных данных
Становитесь автором сайта, публикуйте собственные статьи, описания самоделок с оплатой за текст. Подробнее здесь.