Самодельный 3D-принтер со сварной рамой. Часть первая: начало проекта.
На самом деле все началось с другого проекта, который живет в моей голове и портит мне жизнь уже не один год…
О нем я, возможно, напишу в другой статье. Но суть такова, что для его реализации требовалось изготовить сварную раму из нержавеющего уголка, рассчитать и спроектировать цепную передачу. Ну и много чего еще. Все это требовало много работы на станках, особенно на фрезерном.
Стоит отметить, что для для нагрузок, с которыми связана работа проектируемого устройства, и сварная рама, и стальная цепь, и прочие ‘железяки’ очень избыточны.
В общем думал я как облегчить себе жизнь, думал… И тут мой руководитель покупает себе 3D-принтер! Конечно о технологии 3D печати я знал и раньше. Но после того как он принес напечатанные на своем принтере детальки, чтобы похвастаться, на меня снизошло озарение!:) Вот оно решение большинства проблем связанных с моим проектом!
Так начался проект 3D принтера.
Покупать китайские поделки как-то не хотелось, а отдавать кучу денег за что-то более-менее приличное стало жалко. Естественно решил делать принтер сам. Руки вроде из правильного места растут. С SolidWorks дружу. Кое что из железа уже было. Остальное буду заказывать.
Сразу решил делать капитально. На рельсовых направляющих и со сварной рамой.
Сварную раму решил делать по нескольким причинам:
- Стальные трубы дешевле и прочнее алюминиевого профиля.
- В гараже есть сварной стол и два сварочных аппарата. Один полуавтомат, другой TIG.
- Металлобаза в шаговой доступности от гаража.
- Варить, вроде как, получается неплохо, хоть я и не профессиональный сварщик.
- На квадратных трубах выходит неплохая компоновка узлов. Полости в трубах будут использованы.
Вот фотки того, что уже есть на данный момент:
1. Две каретки и две направляющие THK HSR20 длиной 580 мм. Рельсы и одна каретка Б/У, вторая новая. В принципе люфтов и закусываний вообще не чувствуется. Новая каретка ходит плавнее старой, но не могу сказать что разница колоссальная. Планирую поставить их на ость Z.
[IMG ID=143449 WIDTH=431 HEIGHT=322]
2. Два шаговых двигателя Nema23 Vexta C8940-9212K 2.8A
[IMG ID=143451 WIDTH=445 HEIGHT=333]
4. Два драйвера HY-DIV268N-5A (TB6600)
[IMG ID=143447 WIDTH=431 HEIGHT=322]
5. Три драйвера TB6600 ноунейм (типа улучшенные, есть деление шага на 32)
[IMG ID=143448 WIDTH=431 HEIGHT=322]
Вот набросок сварной рамы принтера.
[IMG ID=143450 WIDTH=544 HEIGHT=536]
Кинематику думаю делать либо H-Bot, либо CoreXY. Пока не решил. Скорее всего остановлюсь на CoreXY. Тогда часть ремней будет находиться внутри трубы на которой нет двигателей.
Двигатели мощные для 3d принтера но уж какие есть. Зато качественные 🙂
Мозгами пока что будет Arduino Mega + Ramps. Для попробовать и освоиться думаю в самый раз. Потом, если будет необходимо, перейду на 32 бита.
По направляющим для осей XY пока думаю. Скорее всего буду брать оригинальный Hiwin. Китай, конечно, дешевле в разы, но азартным человеком я не являюсь. Один раз потратиться на хорошие направляющие, которых, при должном уходе, хватит на много лет, по моему правильное решение.
Продолжение следует…
P/S
Это моя первая статья. Не стесняйтесь писать в комментариях конструктивную критику 😉 Возможно у кого-то будут идеи по конструкции рамы, или еще какие-то замечания и предложения. С радостью прочитаю!
3D принтер H-Bot на рельсах из стального профиля без печатных деталей своими руками.
‘Не бойся делать ,то чего не умеешь, соблюдая технику безопасности. Ведь Ковчег построил любитель, ‘Титаник’ — сделали профессионалы.’
Идея построить 3Д принтер возникла давно, так как занимаясь моделированием и радиолюбительством ,часто сталкивался с необходимостью изготовления корпусов или конструктивных элементов для поделок.
Поизучав вопрос, понял ,что покупать готовый набор неинтересно . Решено было изучить вопрос глубже и набить шишек побольше. Причём без использования готовых печатных деталей, а только из того что под рукой или в хозмаге.
Проект сделан полностью в Solidworks. Название поделке присвоил ‘Metall Bot’. Постройка заняла примерно 5 месяцев. Общий бюджет примерно 33 т.р. Ремень GT2 10мм. Рабочее поле 300х300х240. Стекло стола обычное 5мм ,заказано в стекольной мастерской. Нагрев стола — силиконовый нагреватель 220 вольт на 250 Китайских ватт 🙂 Управление нагревом стола через твердоельное реле однофазное CCP-25DA 3-32V DC до24-380V . Электроника MKS Robin. Драйверы на X-Y TMC2100, а на Z и экструдер DRV8825. Двигатели NEMA 17. Блок питания один на 12 вольт, второй на 24 вольта. Установлена плата управления электропитанием MKS PWC V2.0 для автоматического отключения. Индуктивный датчик уровня пока что не настроен. Катается пассажиром. С прошивкой пока не разобрался до конца с его настройкой.
Первый рабочий вариант.
Модификация оси X.
Видео работы.
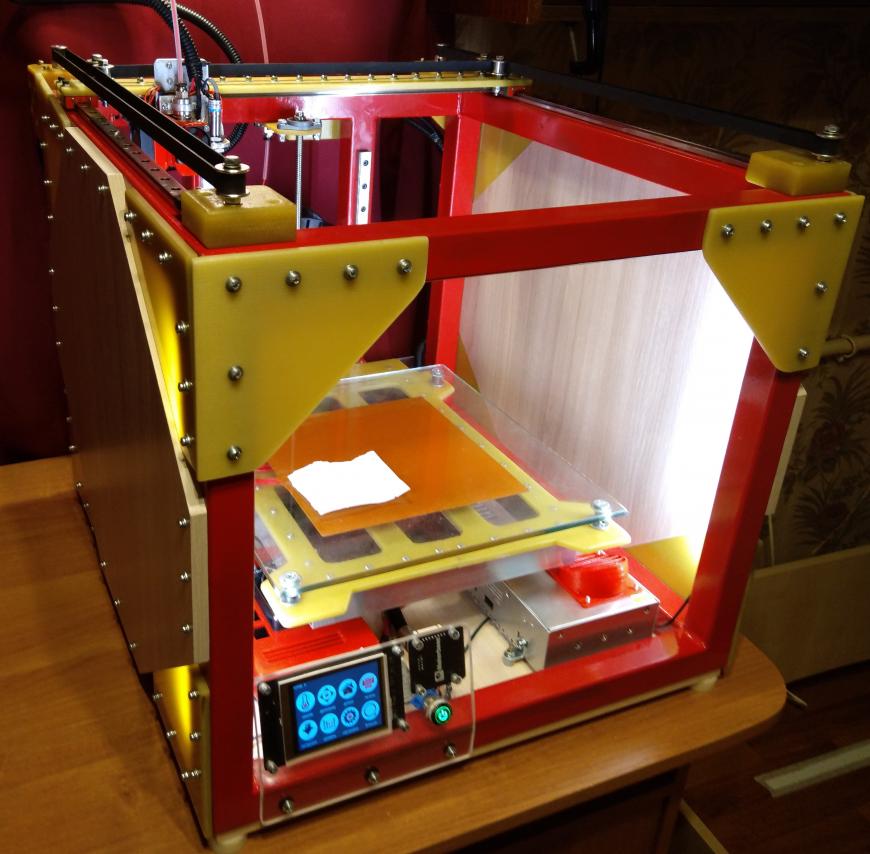
Для рамы использована стальная профильная труба 30х30х2 На всё хватило одной трубы 6 метров. Распиливалось и зачищалось в буквальном смысле на полу дома и над раковиной на кухне.
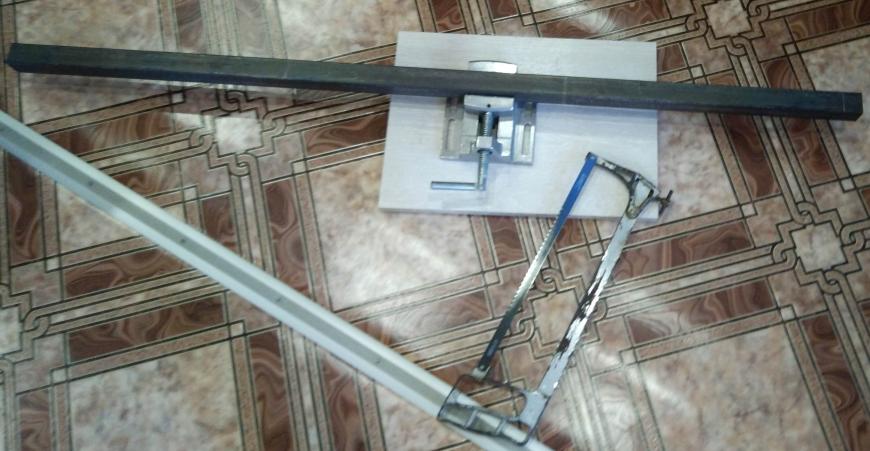
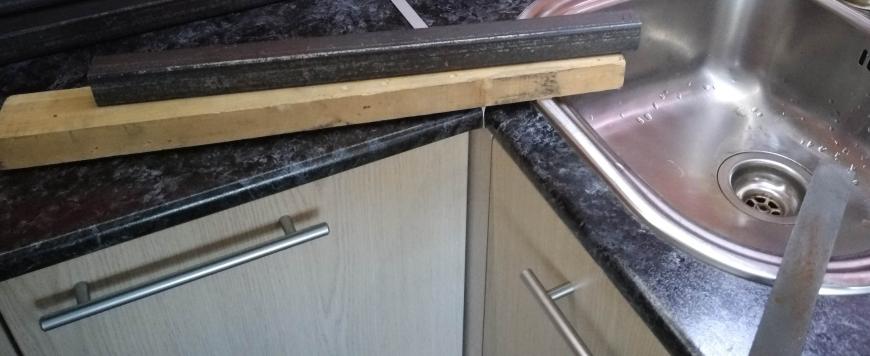
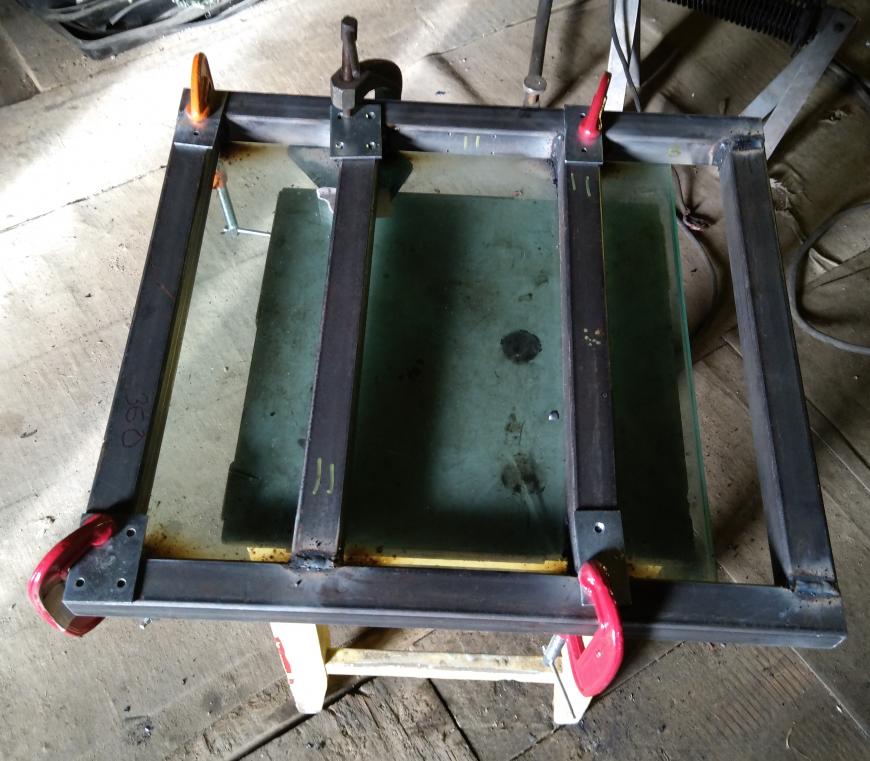
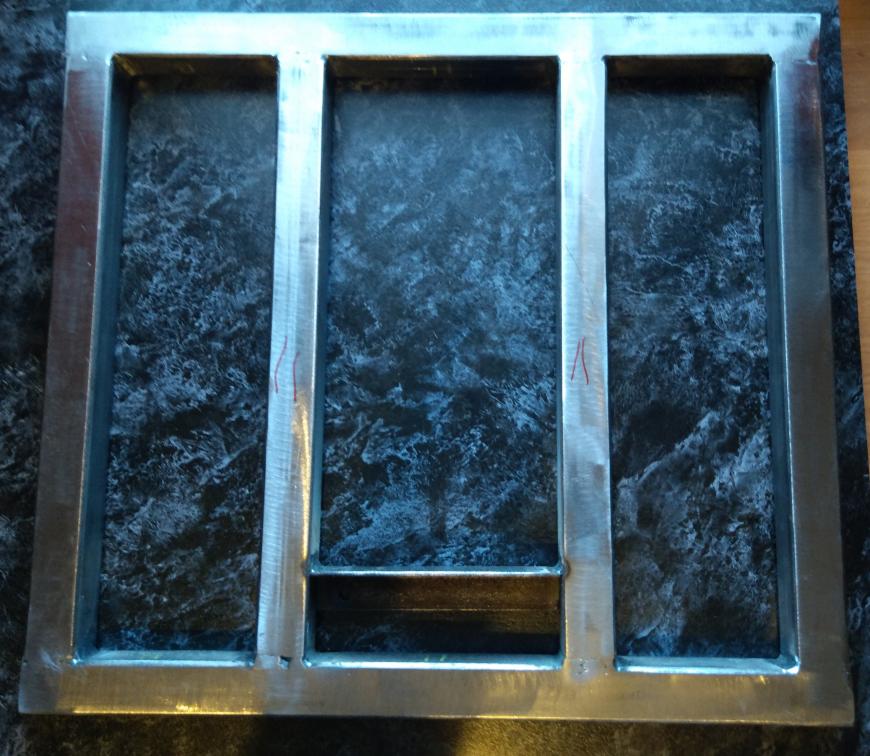
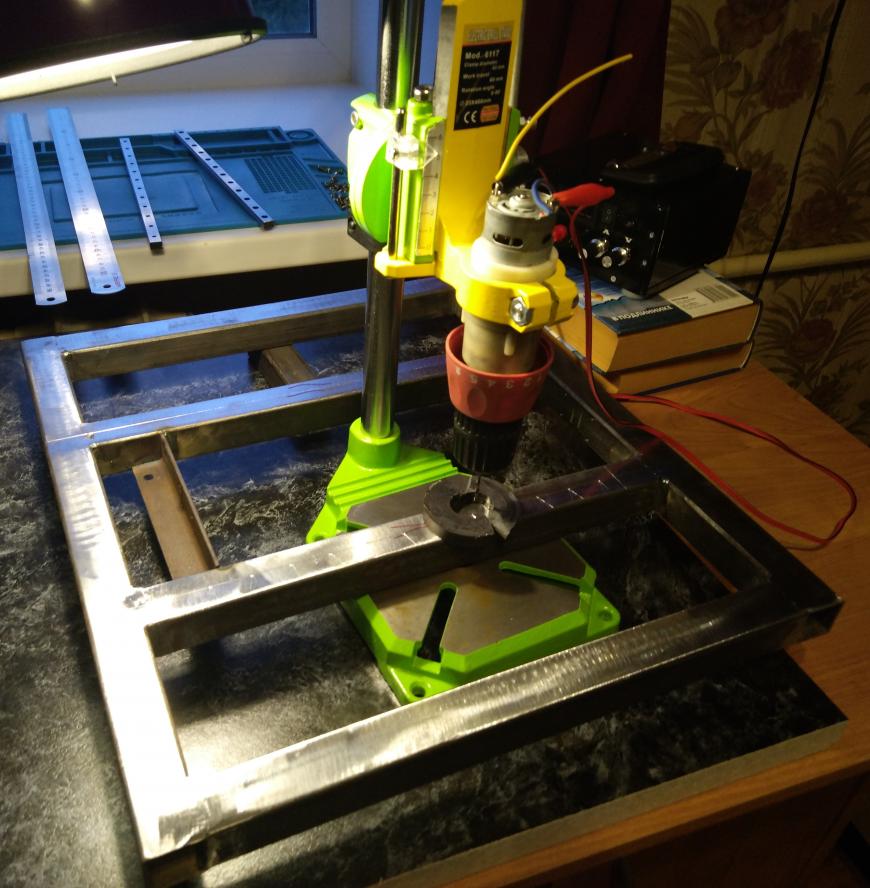
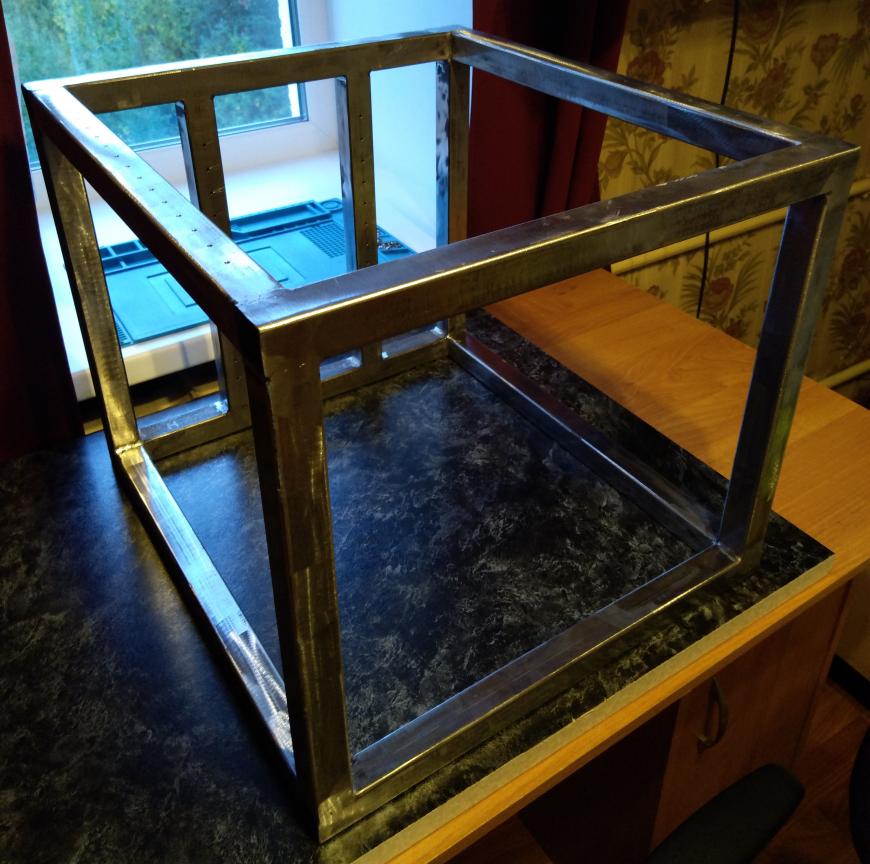
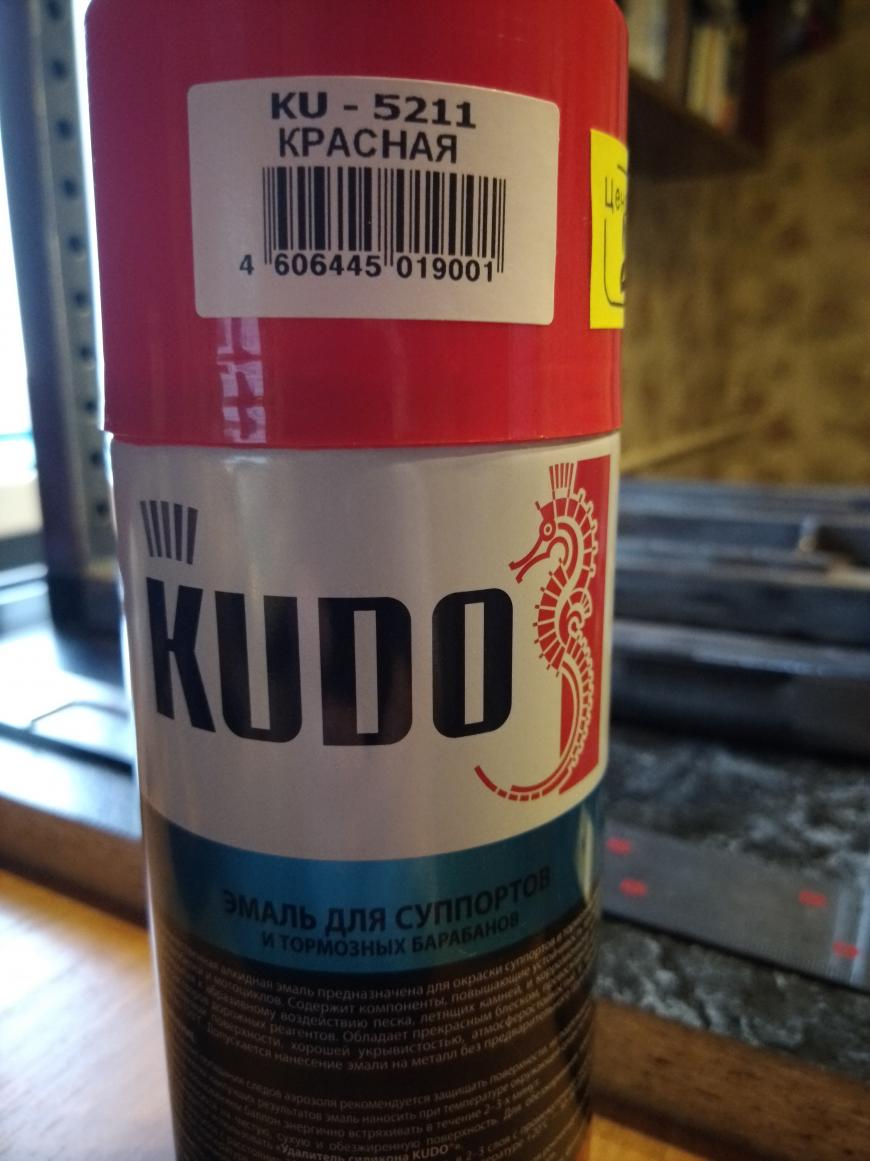
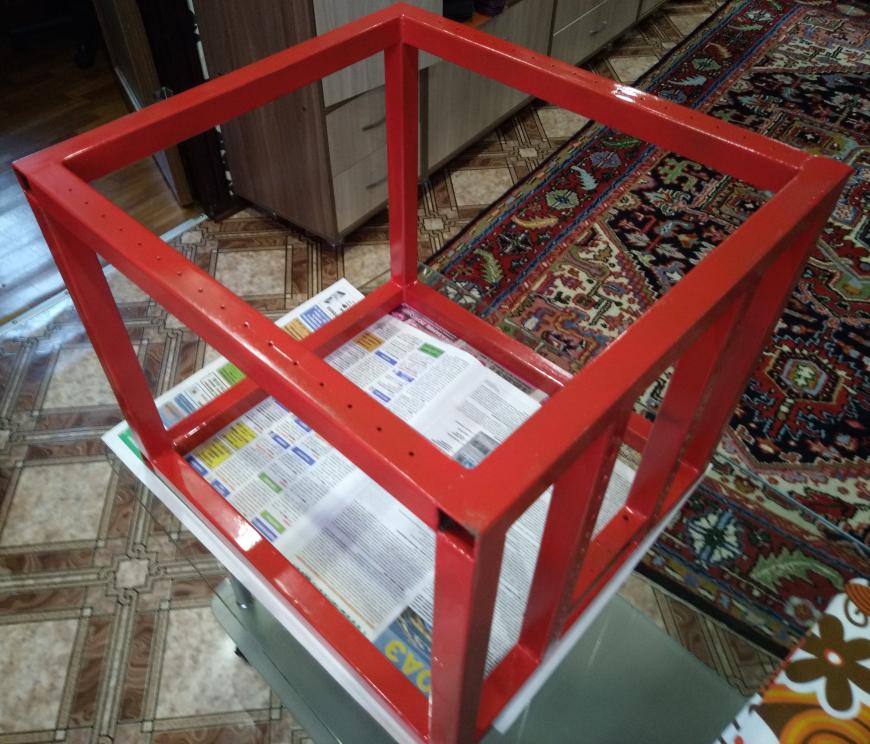
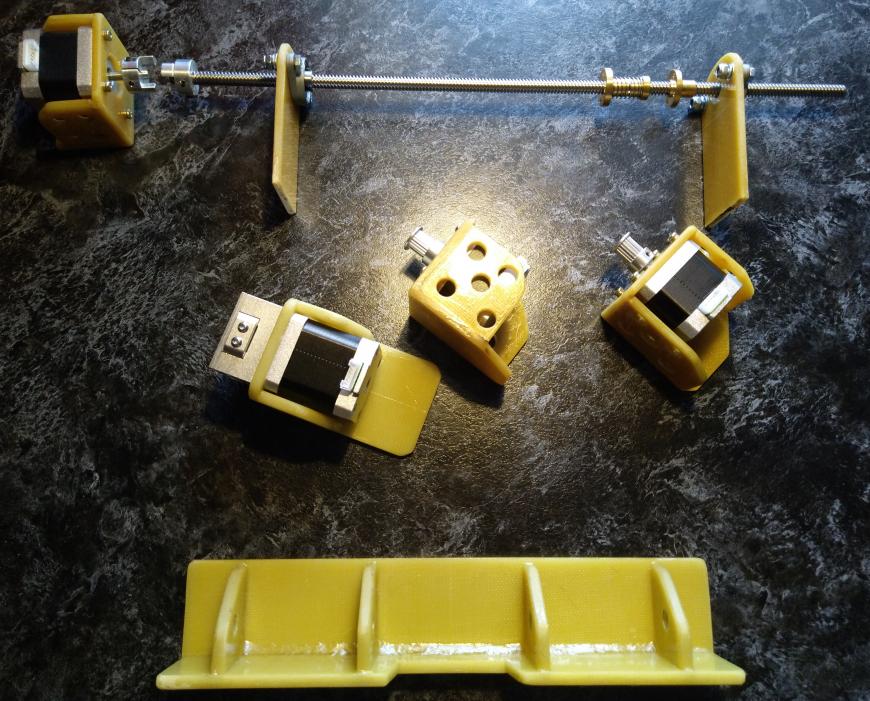
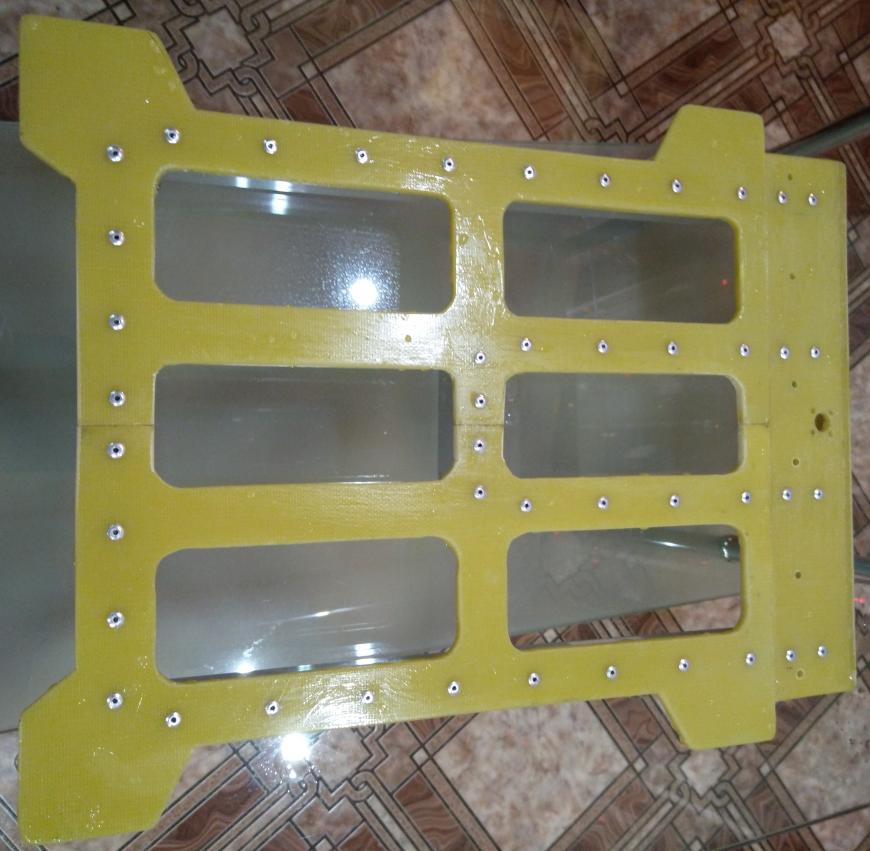
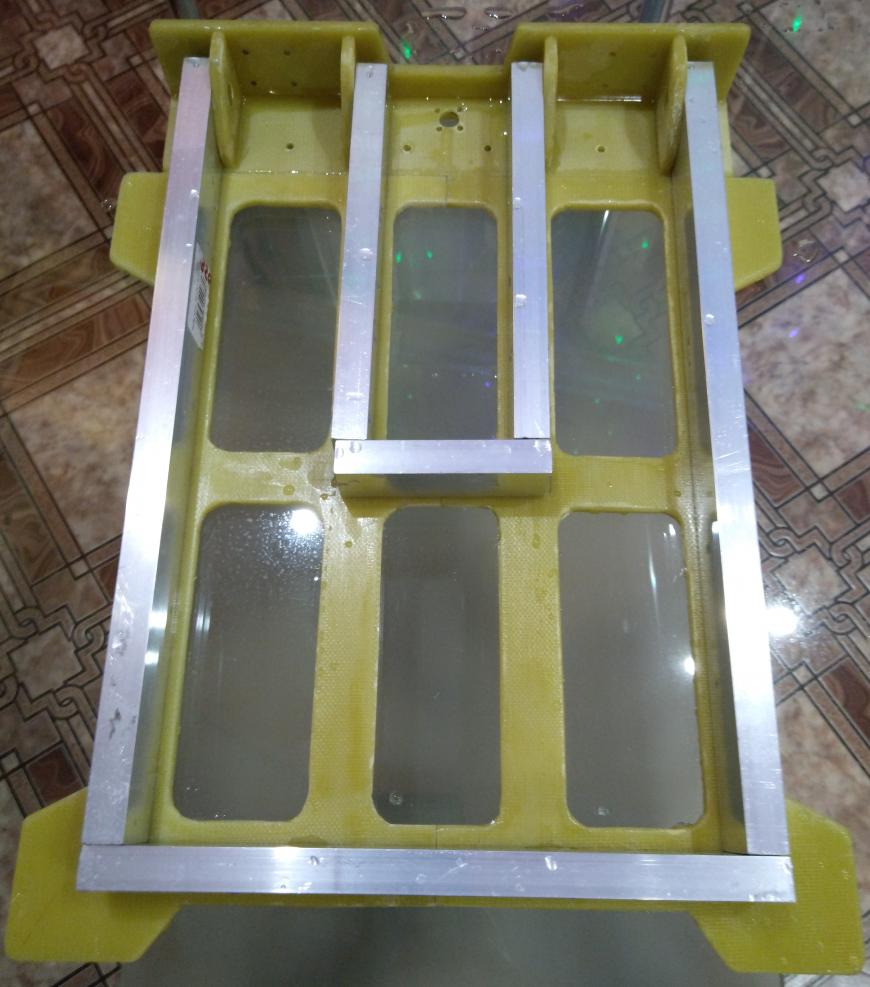
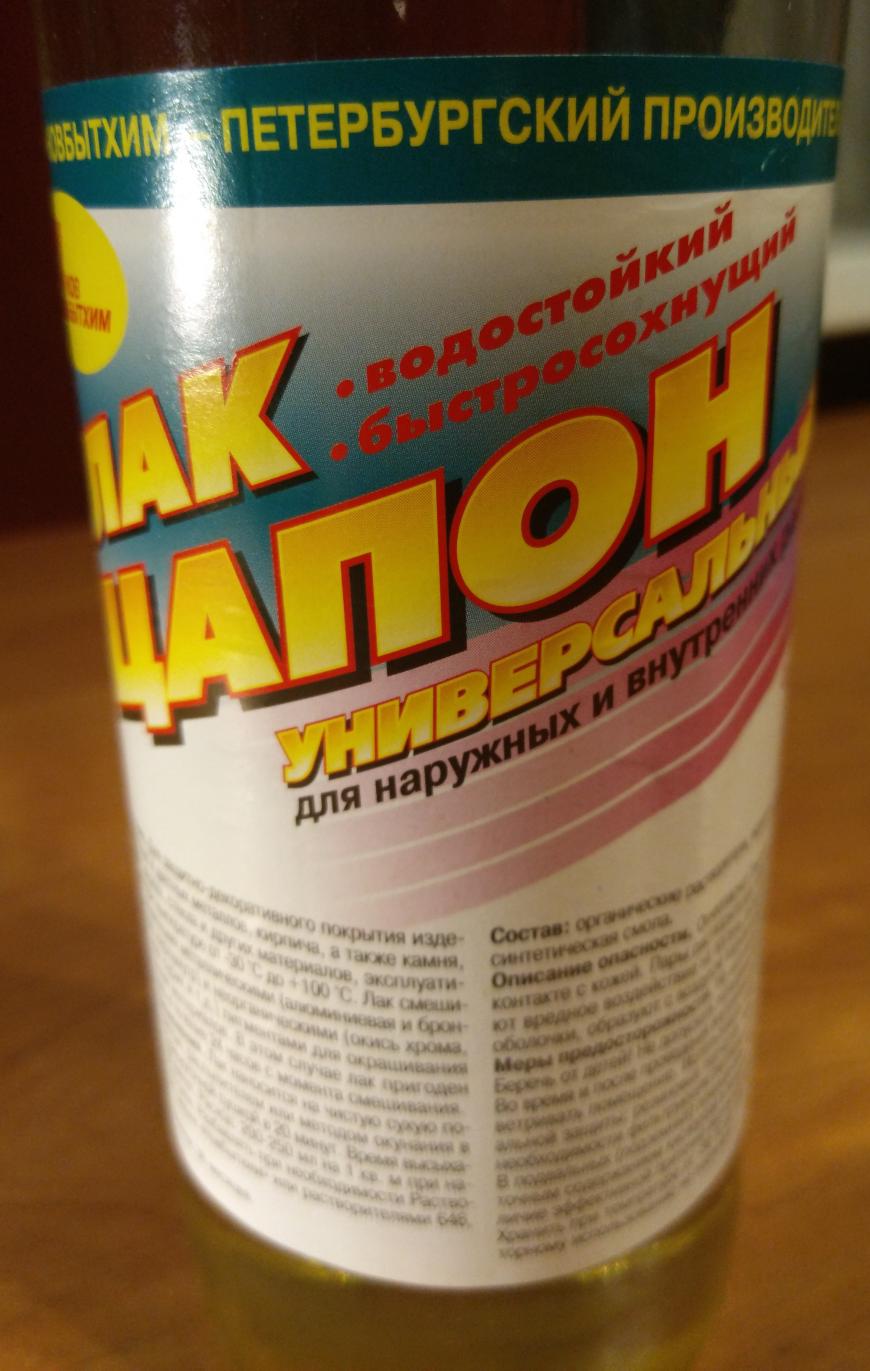
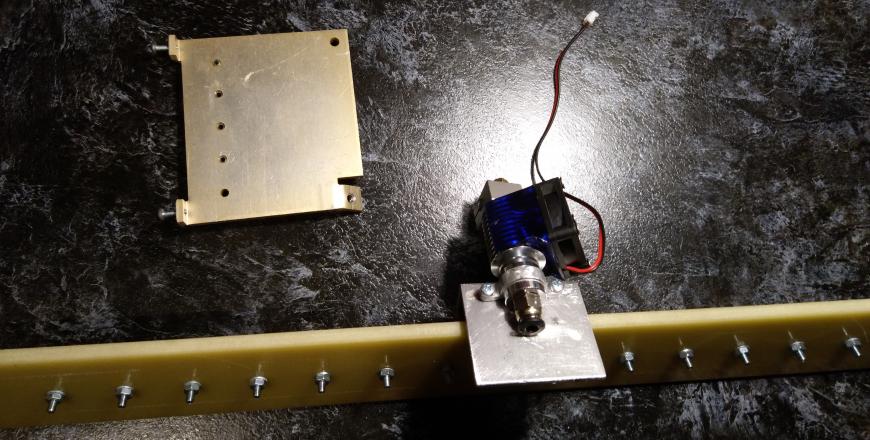
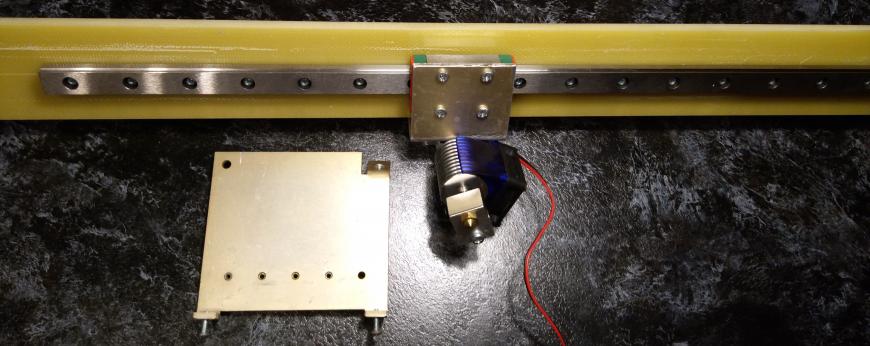
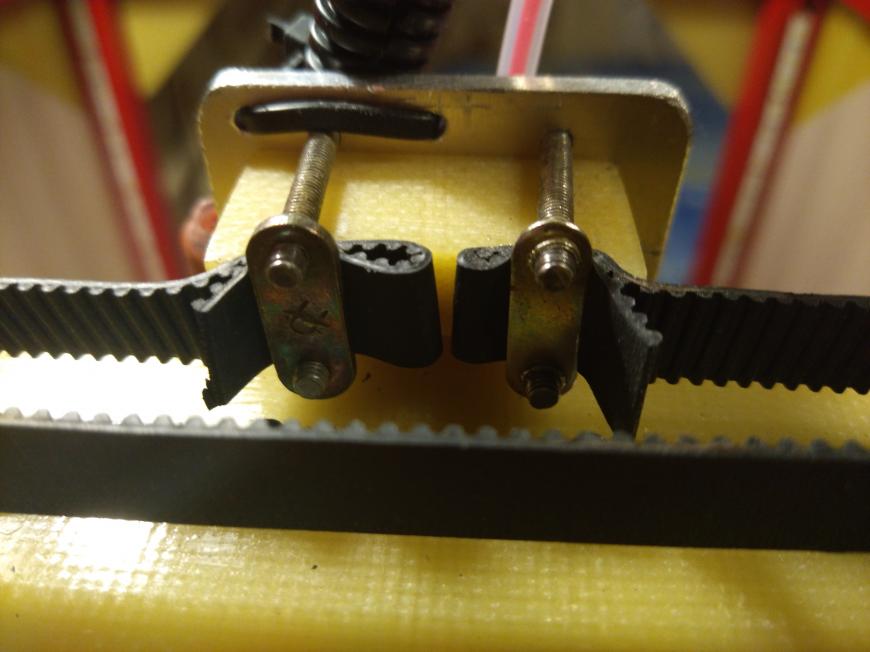
Вид стал вырисовываться.
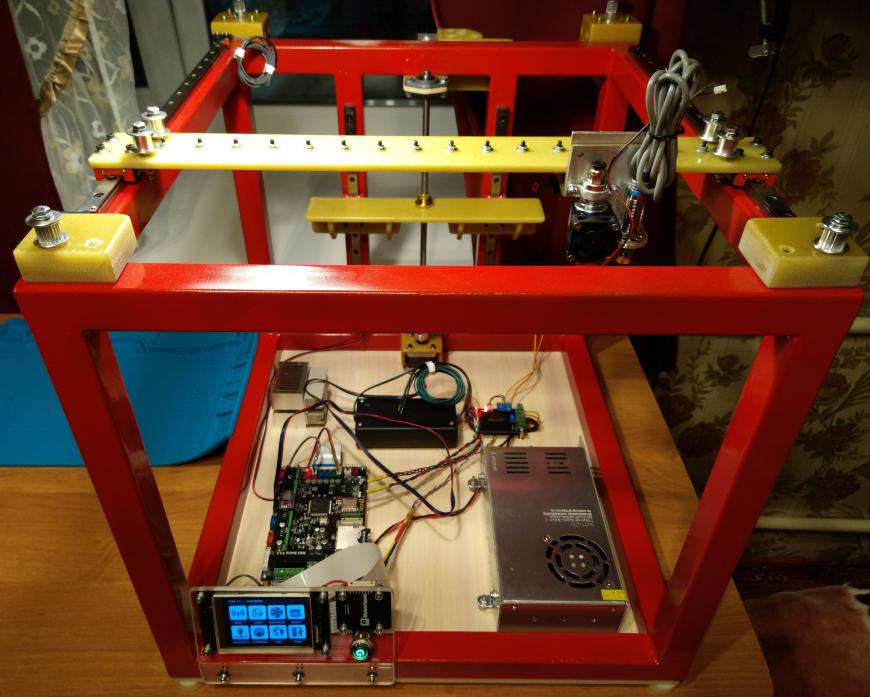
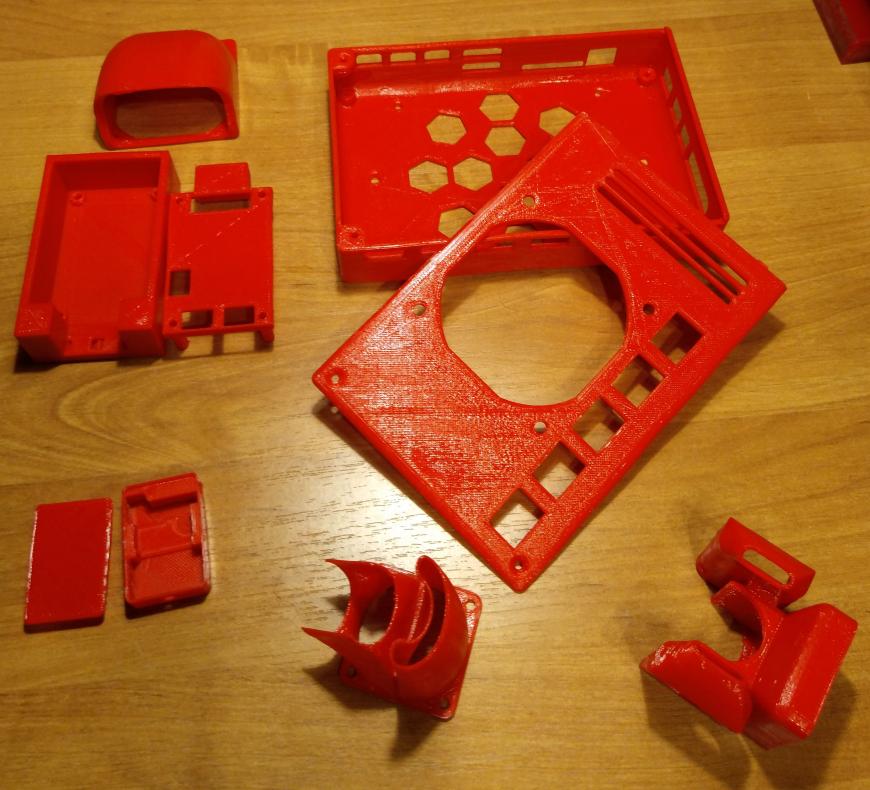
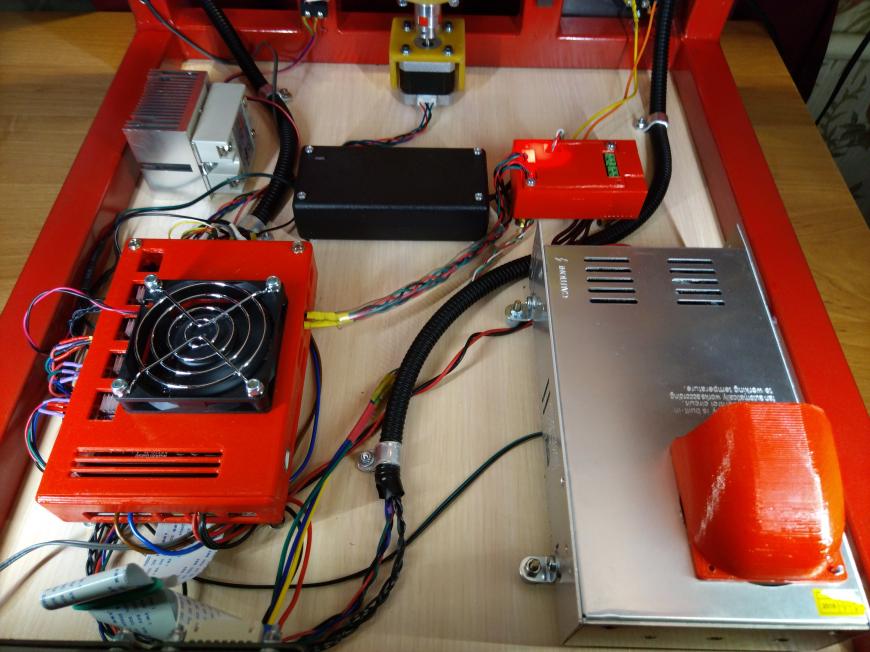
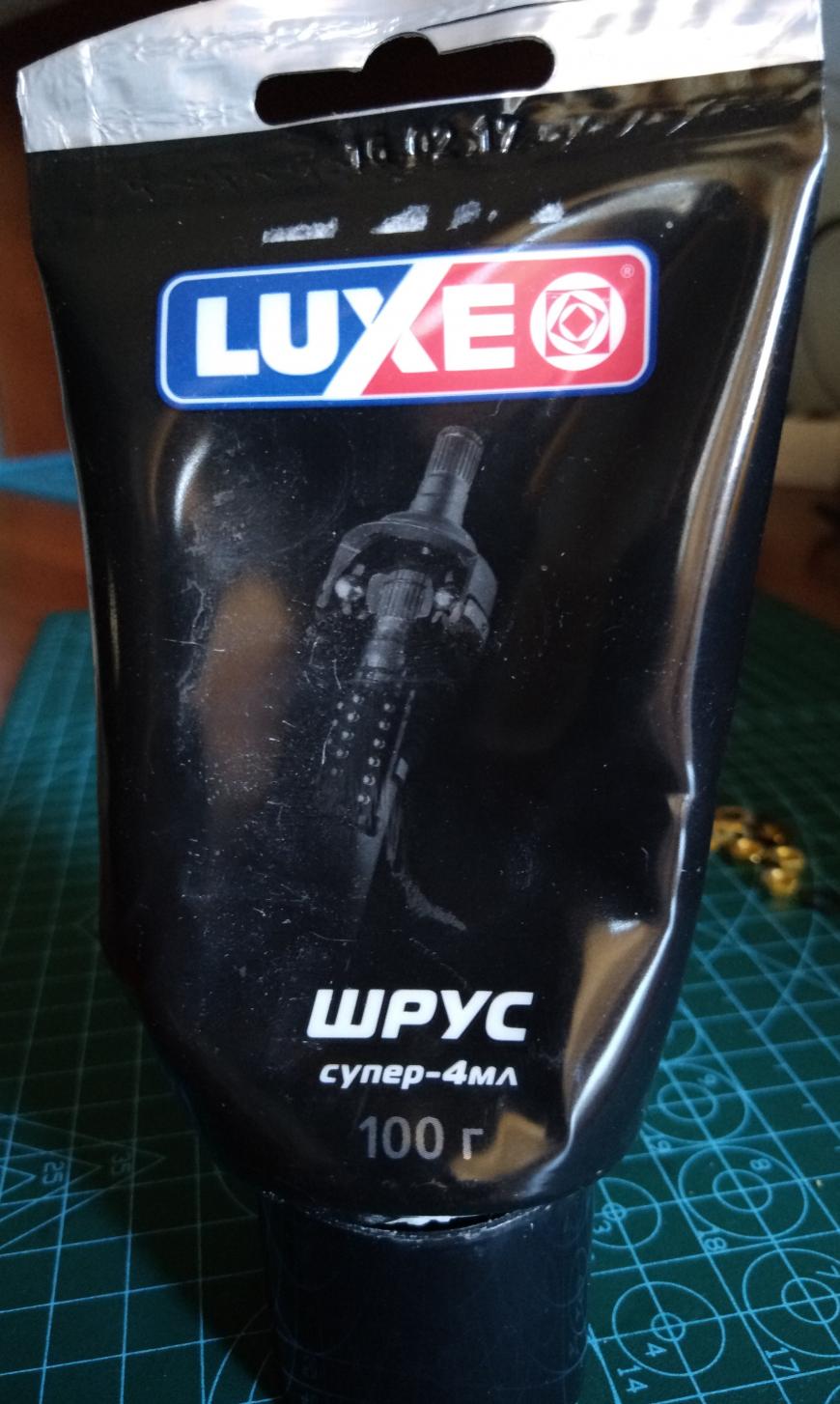
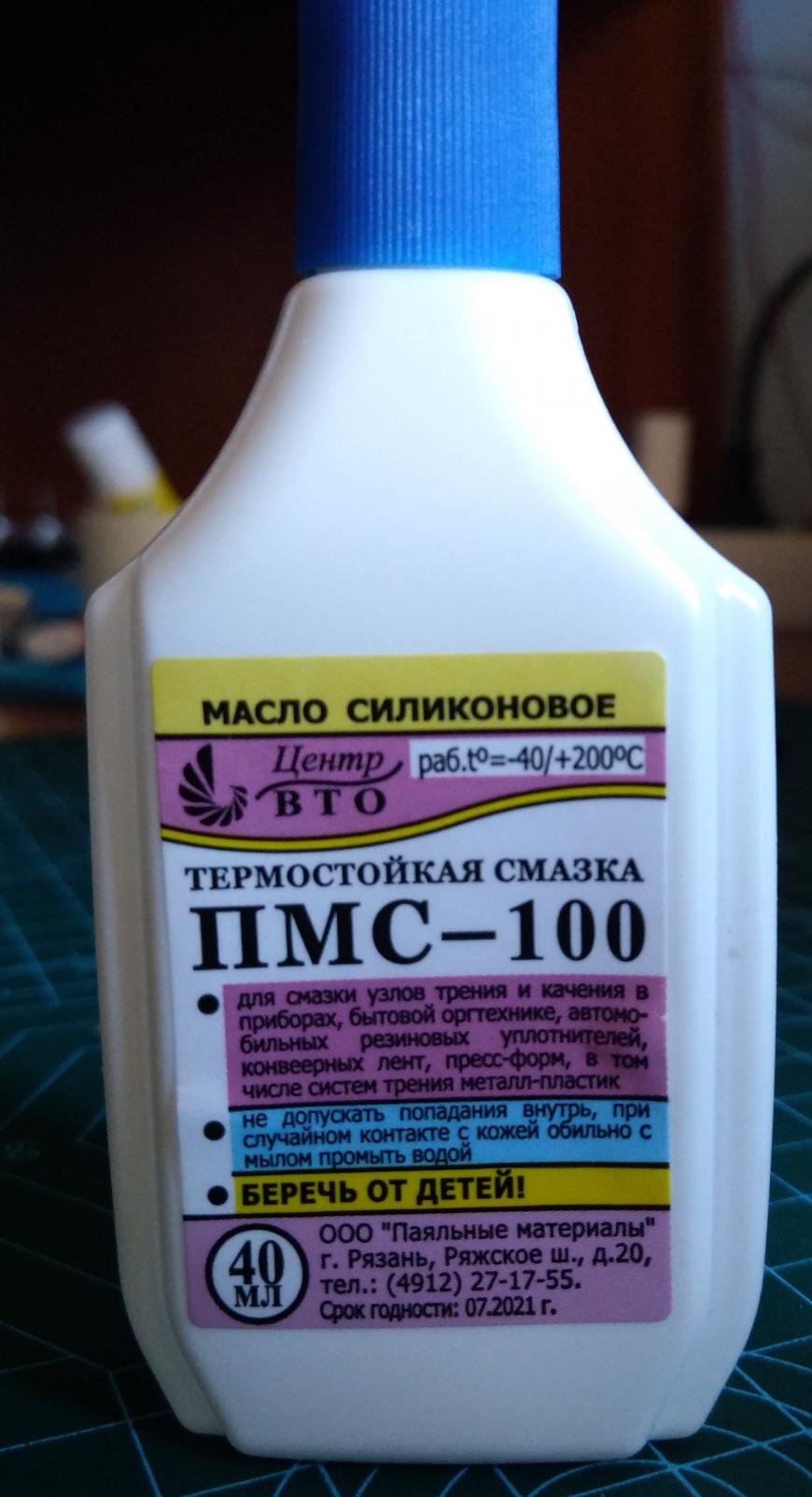
На оси XY поставил более мощные двигатели NEMA 1717HS8401.
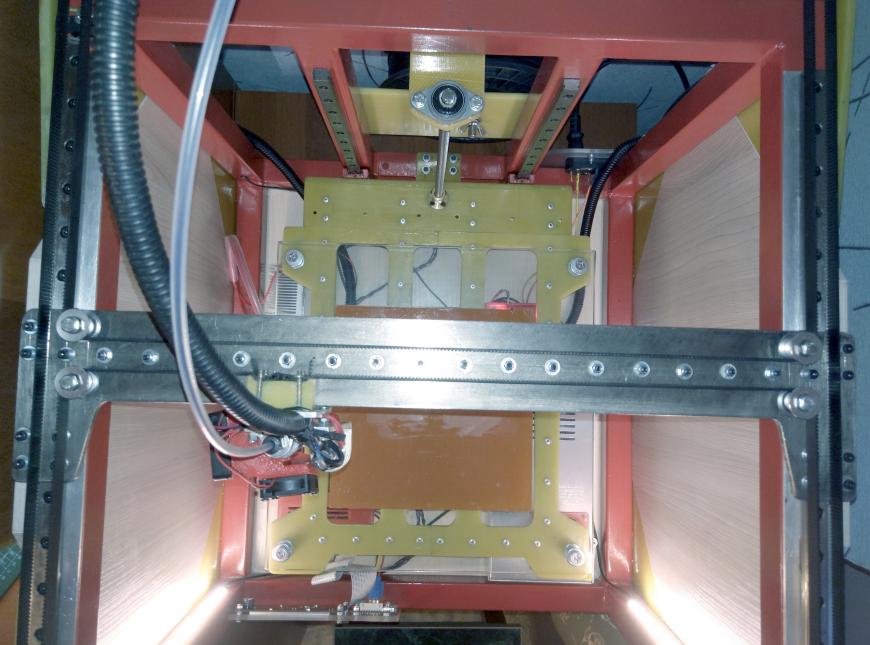
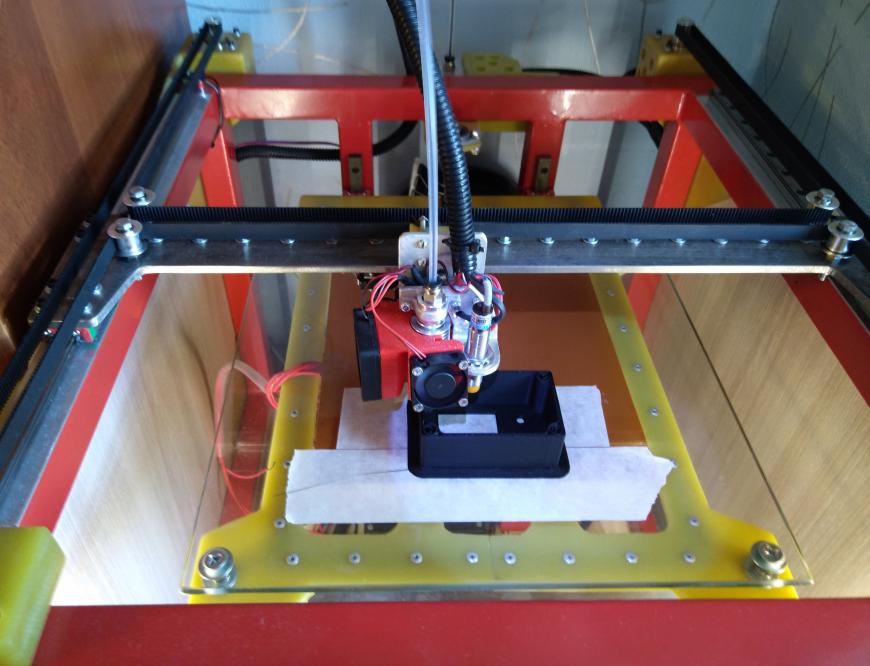
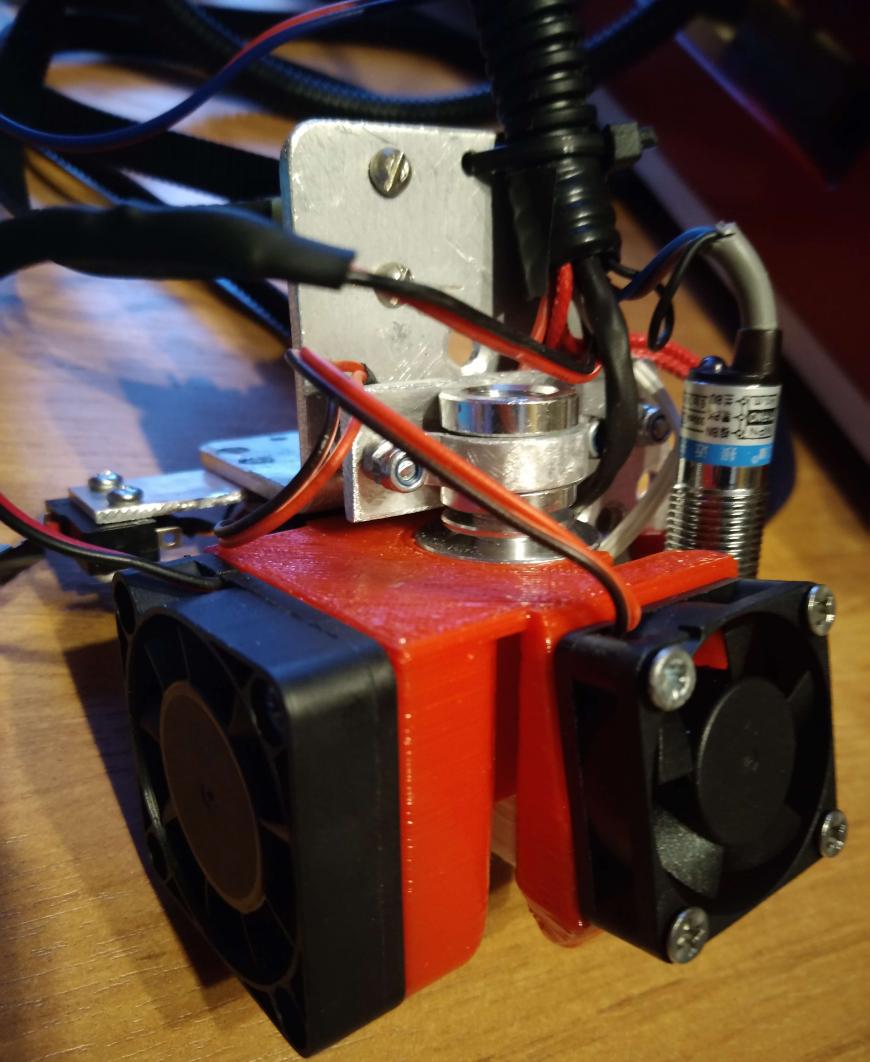
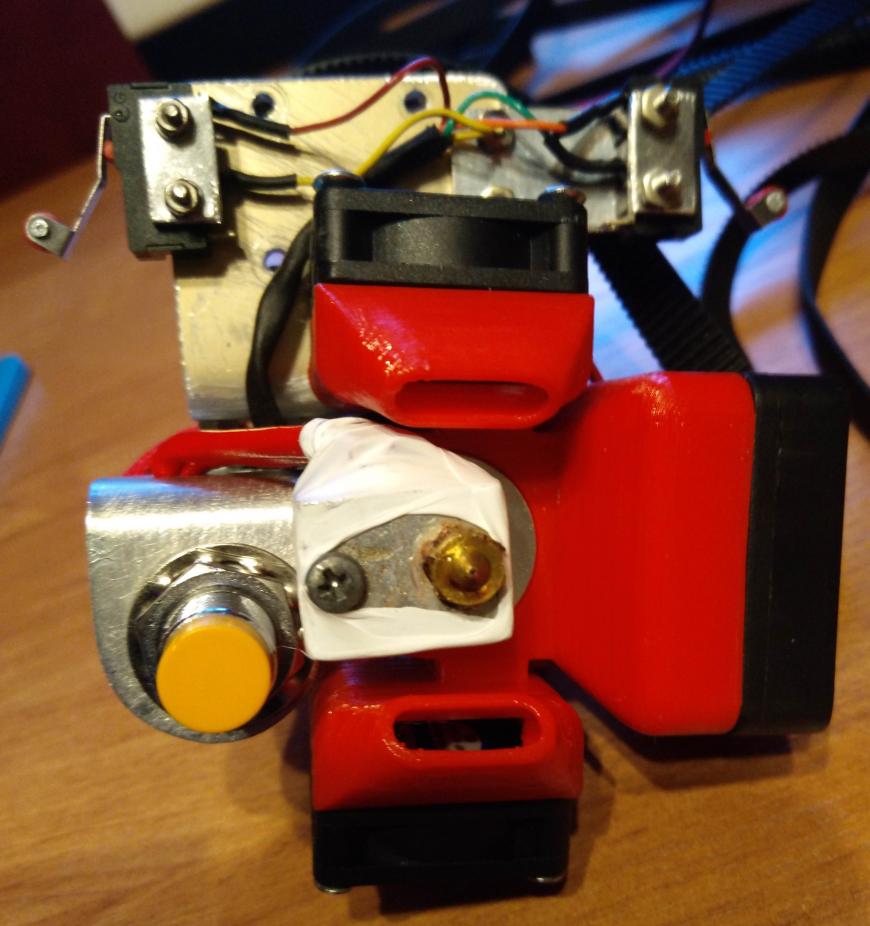
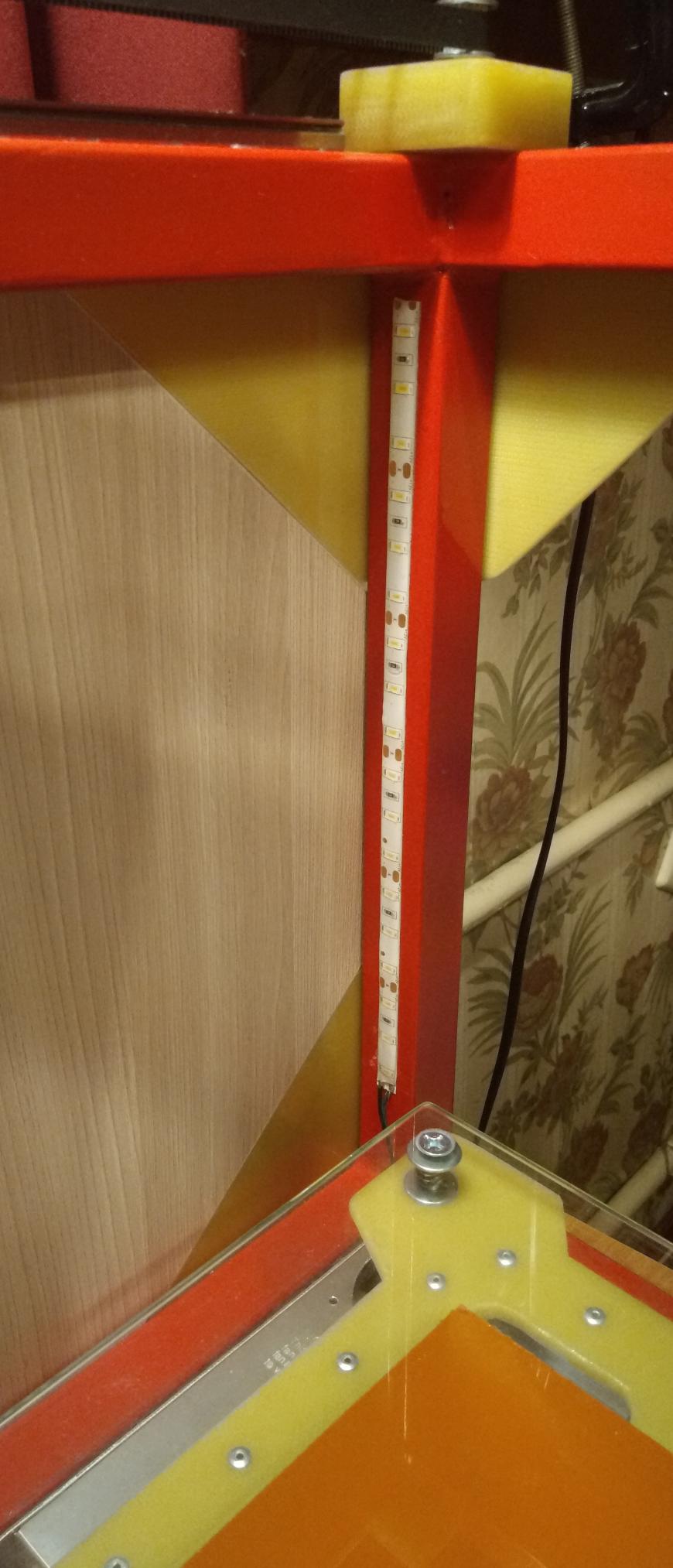
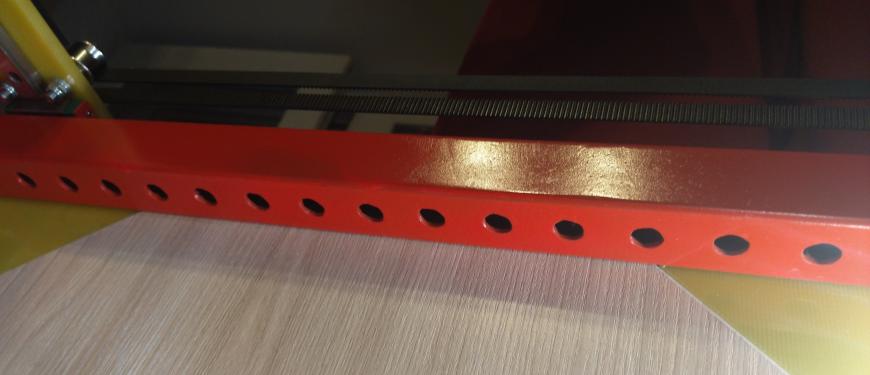
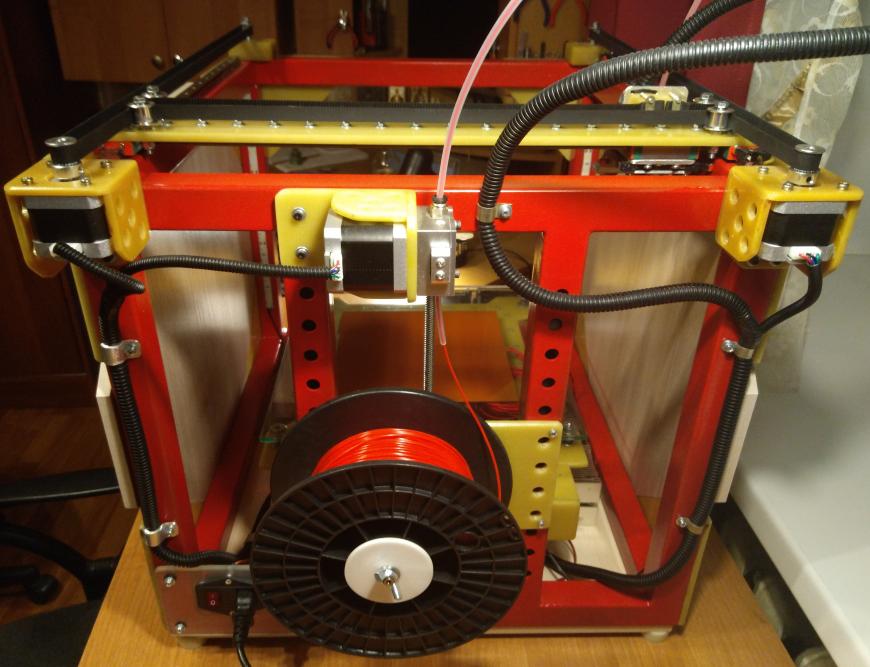
Спасибо. Всем удачи. 🙂
Самодельный 3D принтер из металлолома

Мечтаете купить 3D принтер? Не спешите — сделайте сами своими руками из того, что есть в мастерской.
Данный 3D принтер состоит из деталей старых пишущих машинок, матричных принтеров и другого металлолома. Каркас принтера выполнен из нержавеющей трубы.
Посмотрите ролик, в котором мастер рассказывает и показывает весь процесс создания и работы 3D принтера
Самодельный 3D принтер:
Усовершенствованная версия 3D принтера:
Изготовление экструдера:
Горячий стол:
Принтер почти готов:
Как разрабатывался 3D принтер:
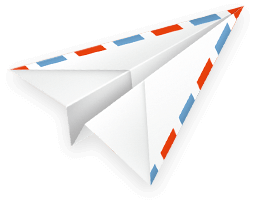
Получайте на почту подборку новых самоделок. Никакого спама, только полезные идеи!
*Заполняя форму вы соглашаетесь на обработку персональных данных
Становитесь автором сайта, публикуйте собственные статьи, описания самоделок с оплатой за текст. Подробнее здесь.3D принтер своими руками
Всем привет! Т.к. это мой первый опыт в написании статей, сборке 3D принтера и т.д., то прошу сильно не ругать в комментариях. Поехали!Немного о себе. Занимаюсь электроникой с 13 лет. В частности программированием микроконтроллеров. Учусь по этой же специальности. Иногда под вдохновлением делаю всякие интересные и не очень вещи.
Стояли очередные серые будни в общежитии моего университета, я, как обычно, зашел на ЮТУБ и мне в рекомендациях выскочило видео, где человек рассказывал про свой 3D принтер из какой-то доски, который занимал уйму места. И тут я подумал, а чем я хуже?
Начался поиск информации о самодельных 3D принтерах, так я узнал что такое RepRap и наткнулся на очень интересного человека: Еремин Сергей где он собрал 3D принтер из старых аппаратов и получил довольно-таки качественную печать. Я сидел на парах и просто читал. Вдохновившись его статьями, которые я перечитал по несколько раз, я решил взяться за дело.
Т.к. я бедный студент я решил поставить себе ограничение по бюджету в 50$ (позже было выяснено что этого очень мало и бюджет вырос до 60$). Нужно было экономить. И начать я решил с самого дорогого, на мой взгляд, с шаговых двигателей и направляющих. Пробежав по барахолкам, и местным аукционам я нашел одного человека, у которого были куплены 4 ШД. EM-34, 3 шт. EM-181, а так-же 4 направляющие от А3 сканеров, диаметром 12,3 мм и длиной 46 см. По цене 2,5$ за один шаговый двигатель и 2,5$ за пару направляющих (позже я купил еще одну направляющую, в итоге всех 5 шт.). Два ШД EM-34 пошли в запас, остальное в ход.
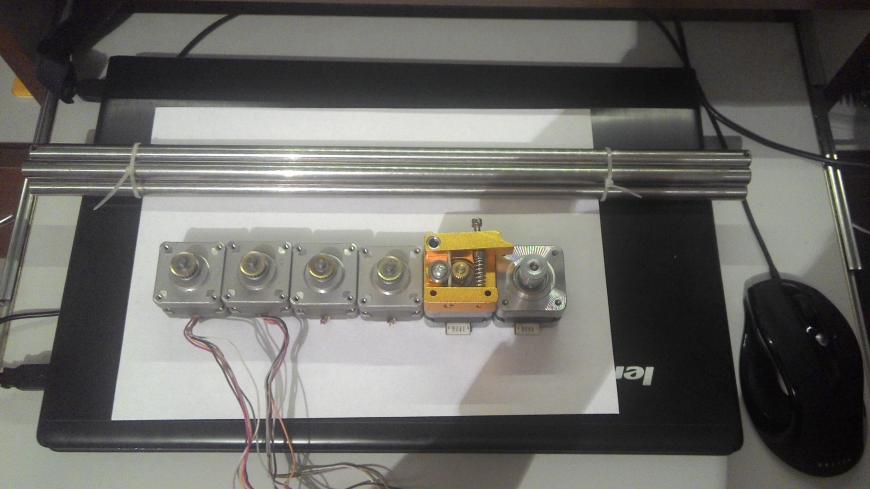
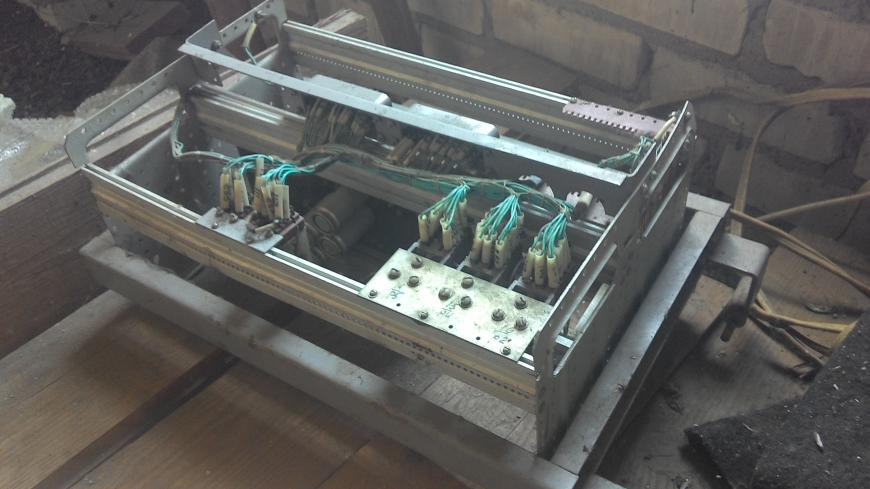
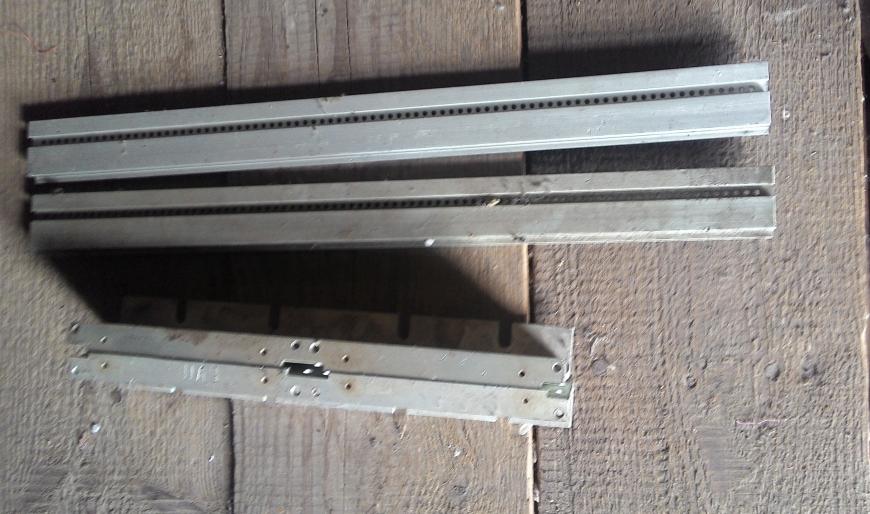
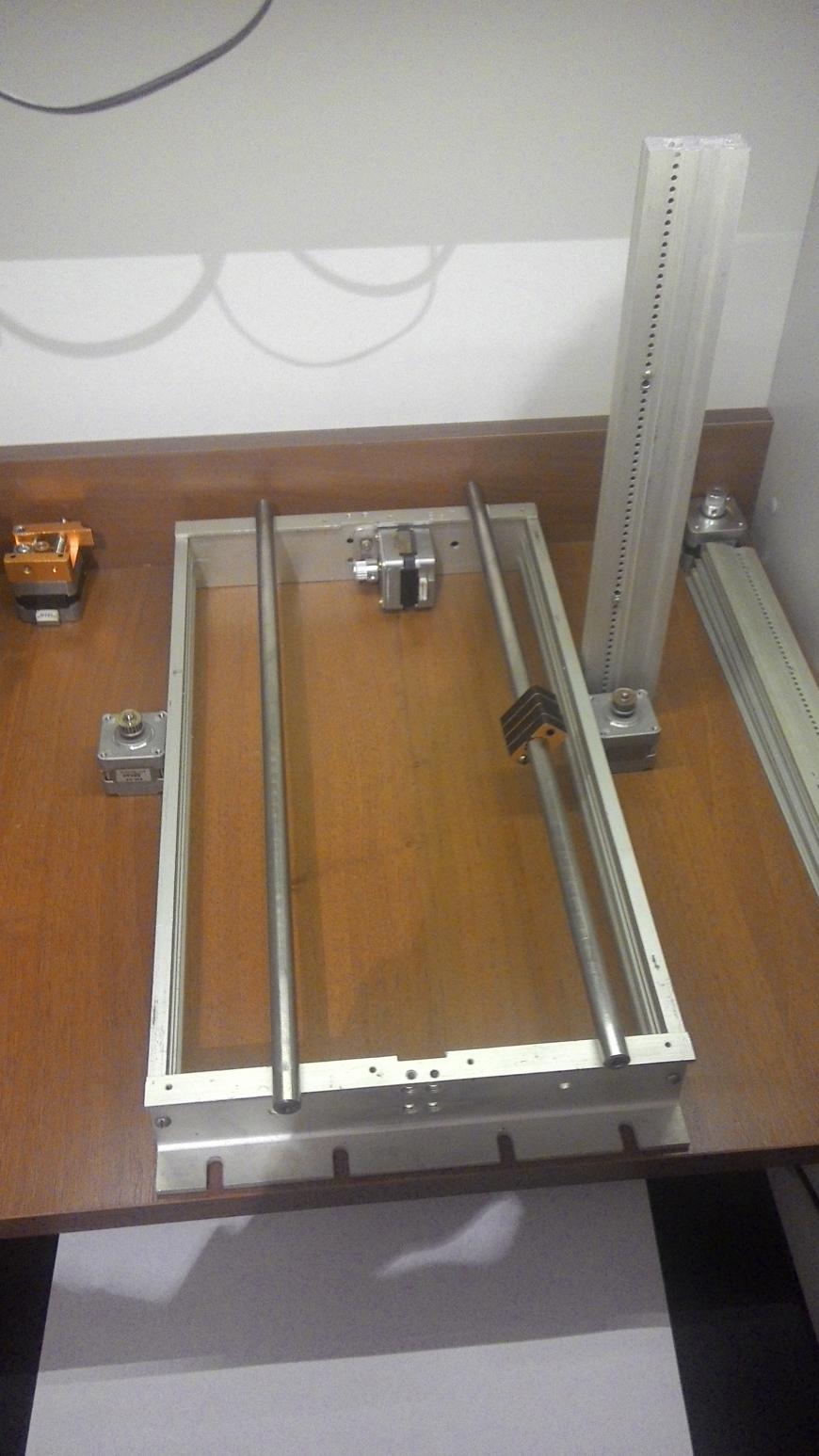
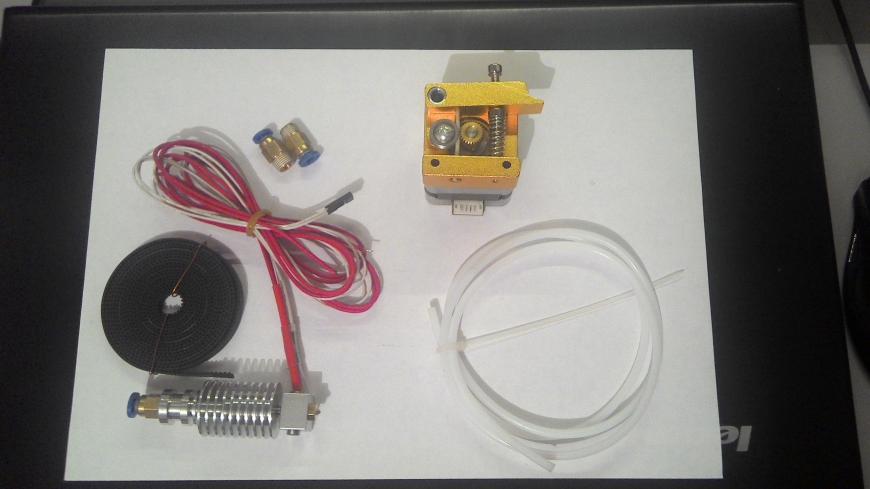
Дальше я вырезал из профиля горизонтальную поперечину, засверлил все, нарезал резьбу и прикрутил к раме. Вышло не плохо. Но во избежание заваливания оси Z нужно добавить косынки по бокам.
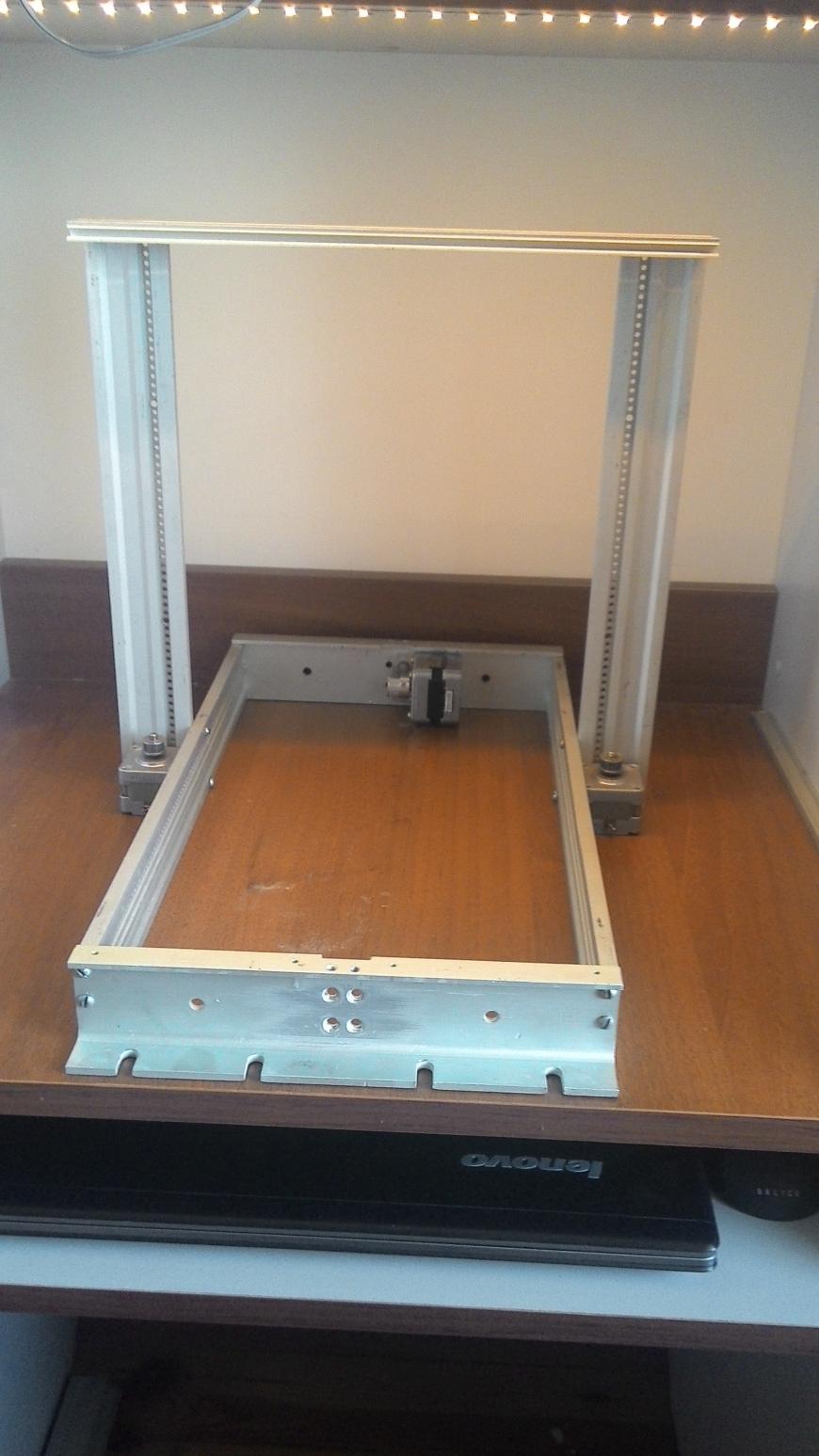
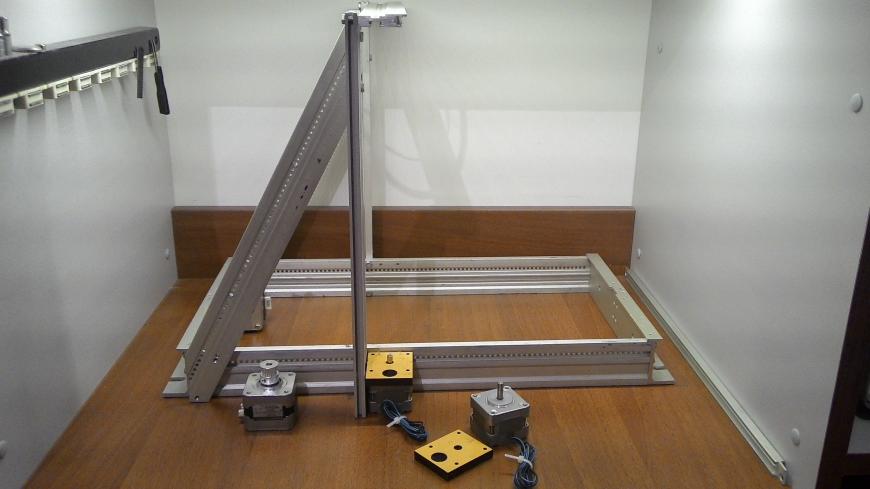
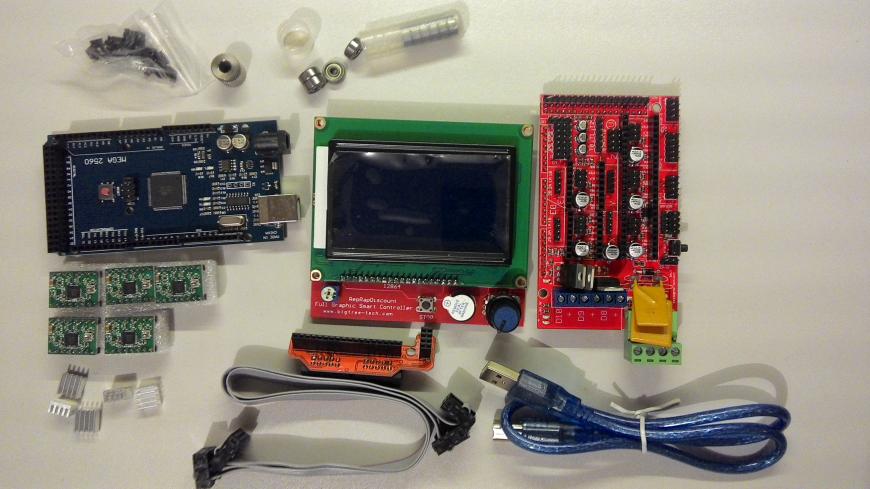
По качеству. Вот лучше бы китайцы продавали все это дело в виде набора для сборки, особенно RAMPS. Если SMD детали они и научились феном паять, то выводные — будто в школе на уроке труда паяли. Меня такое не устраивает, поэтому пришлось часок, другой поорудовать паяльником. Надоело выравнивать все разъемы!
Спустя несколько часов работы паяльником, этиловым спиртом, мылом и водой получается это. Осталось скачать Marlin поковырять настройки и в добрый путь!
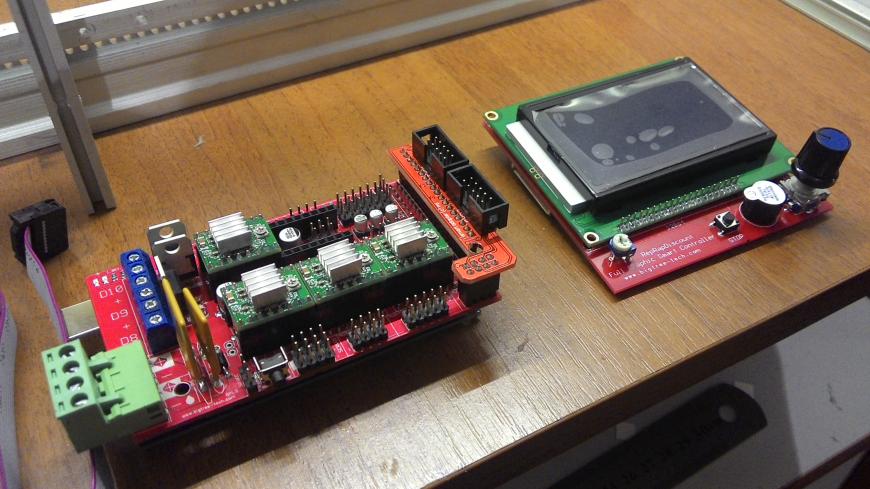
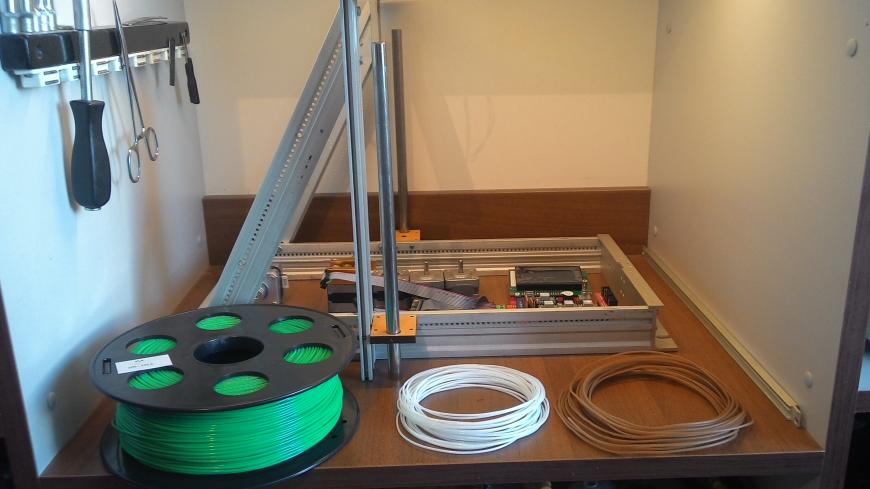
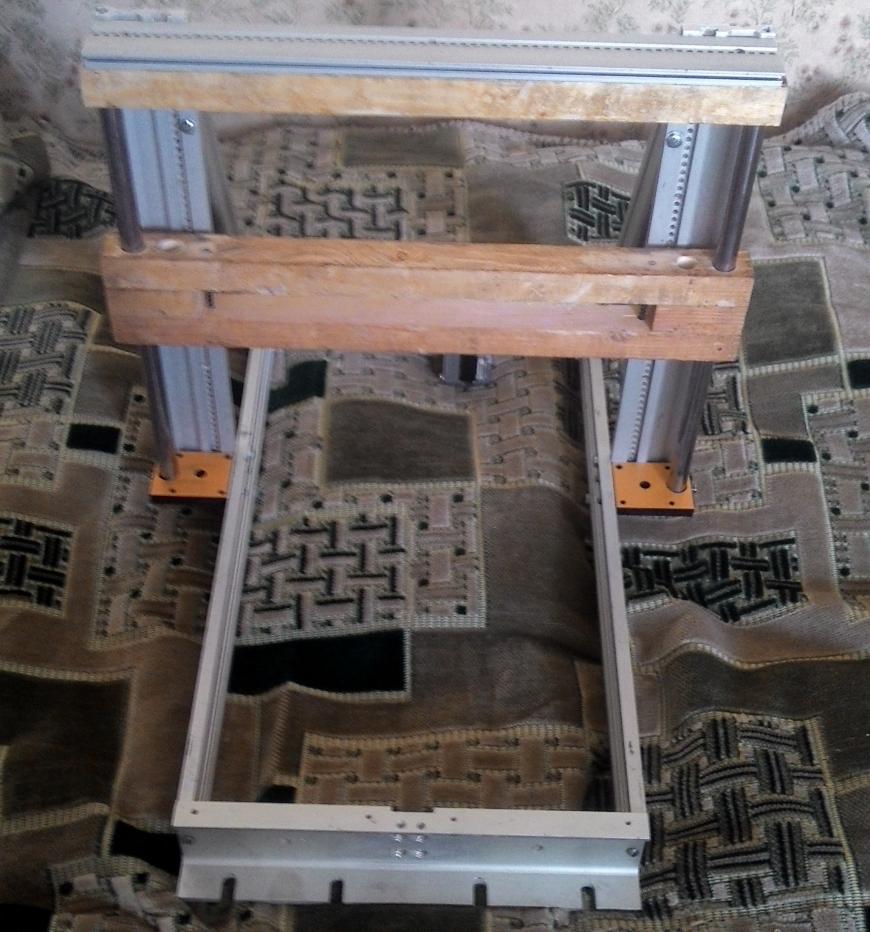
Из все тех же брусков от рамок я вырезал крепления для направляющих оси X и саму каретку на которую устанавливается хот-энд. Шаговый двигатель я закрепил к деревянной раме с помощью пластины из металла 3мм. На противоположный конец рамы был установлен ролик ремня из двух подшипников 623Z, сверху и снизу подложил шайбы М3 и добавил сверху широкую шайбу, дабы ремень не слетал и затянул все саморезом. Хот-энд закрепил на каретке с помощью хомута из медной проволоки — просто и со вкусом 🙂
Направляющие оси Y так же закрепил с помощью деревянных брусков от рамок. Линейные подшипники стола сделаны из них же.
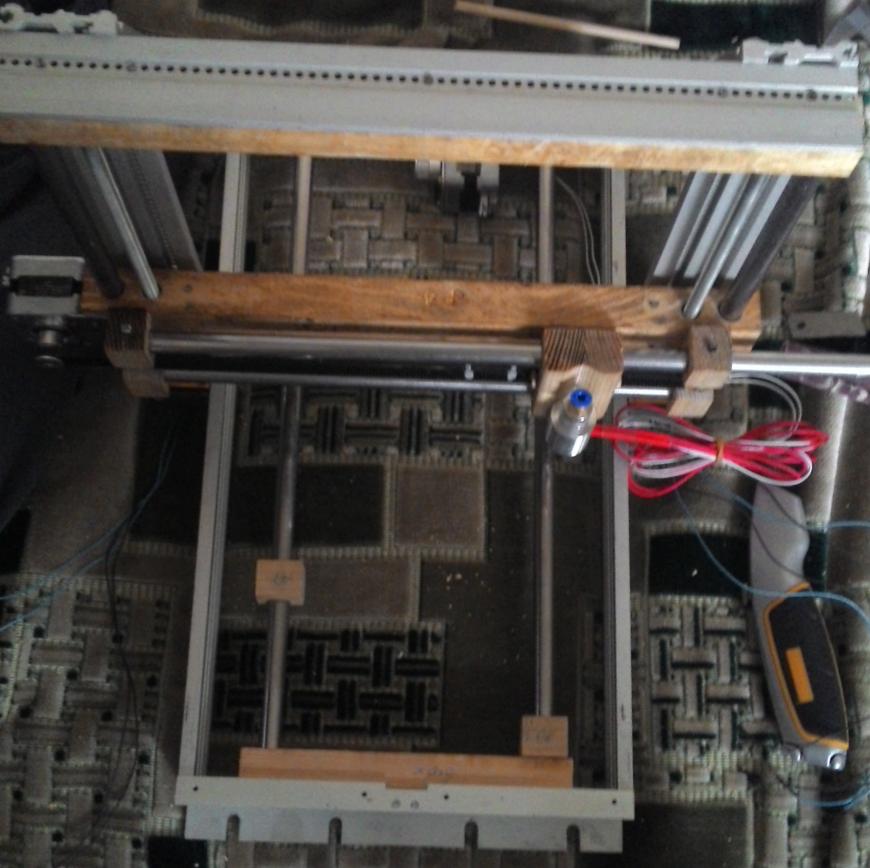
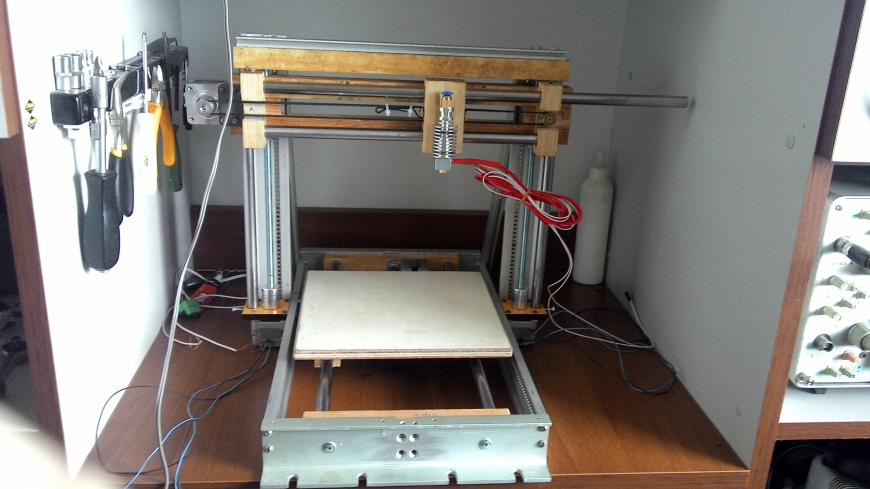
И так, сначала я, начитавшись про плохую адгезию, решил печатать на оргстекле. Скачав программу Cura я толком в ней ничего не настраивал (за что она мне и понравилась, для новичка самое оно). Выставил скорость печати, высоту слоя, заполнение и температуру. Ну и еще ретракт включил. Все. Скачал модель тестового кубика со стороной 20 мм, отслайсил, закинул на карту, вставил ее в принтер, перекрестился и нажал печать!.. Те ощущения, когда ты смотришь, как паркуется каретка, как греется хот-энд, не описать словами… И вот! Процесс пошел. Естественно сразу всплыли проблемы — я криво выставил высоту сопла. Сначала каретка елозила по стеклу, но через пару слоев я увидел КВАДРАТ! УРАААА! Заработало! Сколько же радости от того, что ты, вот, потратил свои законные 2 месяца каникул, вложил свои силы, деньги и не зря. И теперь эта конструкция работает. А ты смотришь и от радости распирает во все стороны… По окончанию печати я понял — брать оргстекло в качестве столика было плохой идеей. Либо это оргстекло такое, либо я идио… В общем мой кубик вплавился в столик 🙂
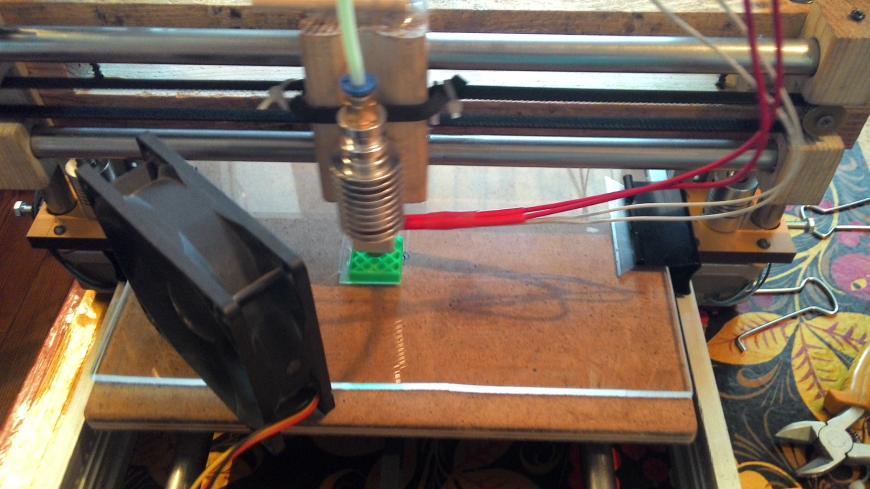
Отодрал я его только поломав у основания, ну и пусть. Качество печати меня очень сильно порадовало. Не смотря на то что я толком ничего не настраивал, не подбирал, а просто запустил печать абы как — все было прекрасно. Размеры кубика совпадали.
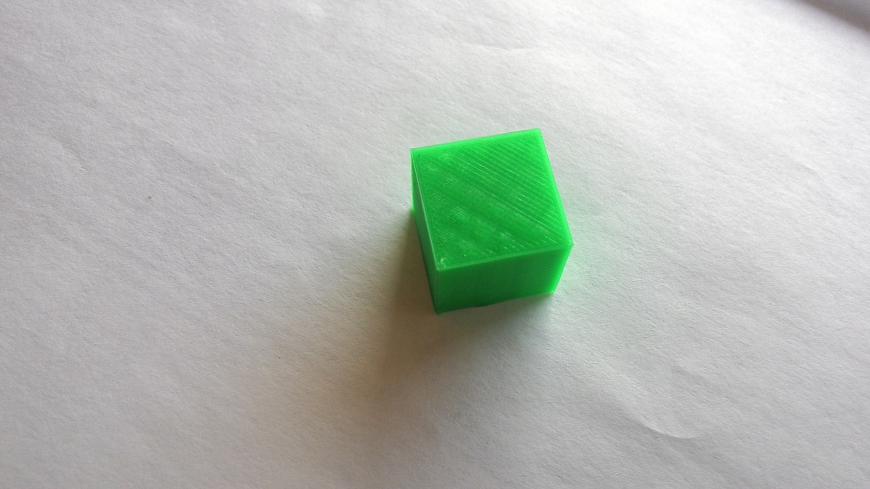
P.S. Сейчас я нахожусь в поисках направляющих. Ищу направляющую 12,3 мм от принтера/сканера А3 длиной от 35 мм, ну или две направляющие 10 или 8 мм той же длины. Если Вы из РБ и есть таковые — готов купить. Пишите в личку.
3D печать для самых новеньких. От А до Я. Кинематика.
В данной статье мы разберемся, что такое 3D печать и какая бывает кинематика 3D принтеров.1. 3D печать. Какая она на вкус?
Технологий печати существует большое множество, от FDM (FFF), по которой печатает больше 90% принтеров на данном портале, до SLA/DLP/LCD (с фотополимерами) и SLS/SLM (спекание порошка с помощью мощных лазеров)Нас на начальном этапе интересует FDM — послойное наплавление расплавленного прутка. На картинке ниже изображен хотенд (Hot end) — та часть экструдера 3D принтера, где происходит расплавление прутка.
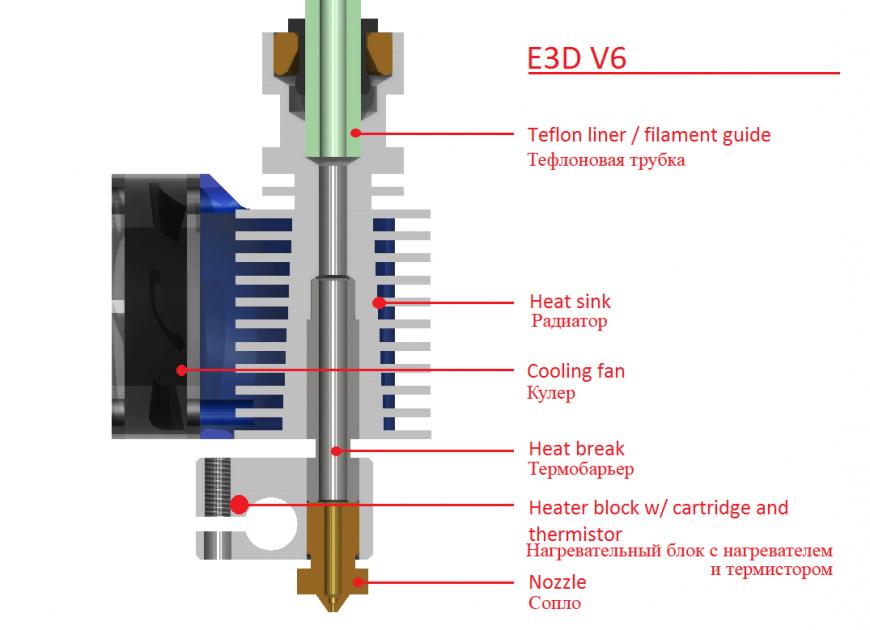
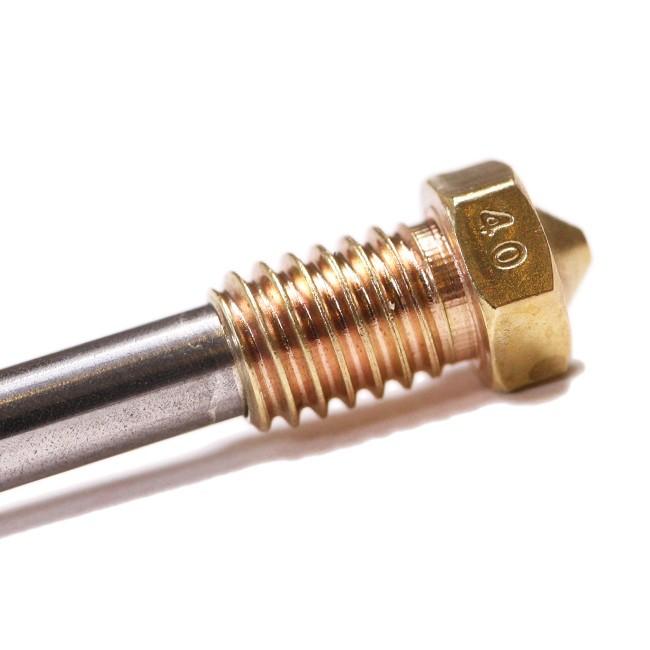
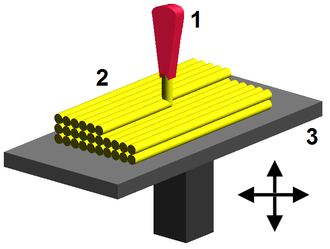
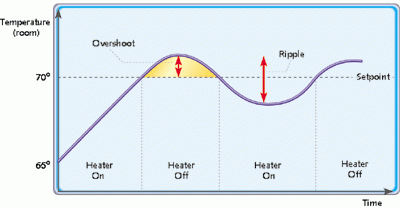
Термобарьер служит для того,что бы минимизировать нагрев пластика выше термоблока.
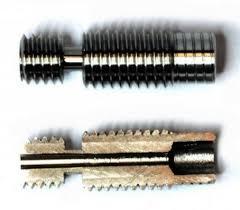
Наиболее часто выполняется из нержавеющей стали. У нее теплопроводность ниже, чем у обычной,нелегированной стали. Для предотвращения плавления прутка выше термоблока сверху на термобарьер накручивается радиатор и обдувается кулером. Все достаточно просто.
Очень часто возникает протечка расплавленного пластика через резьбу.
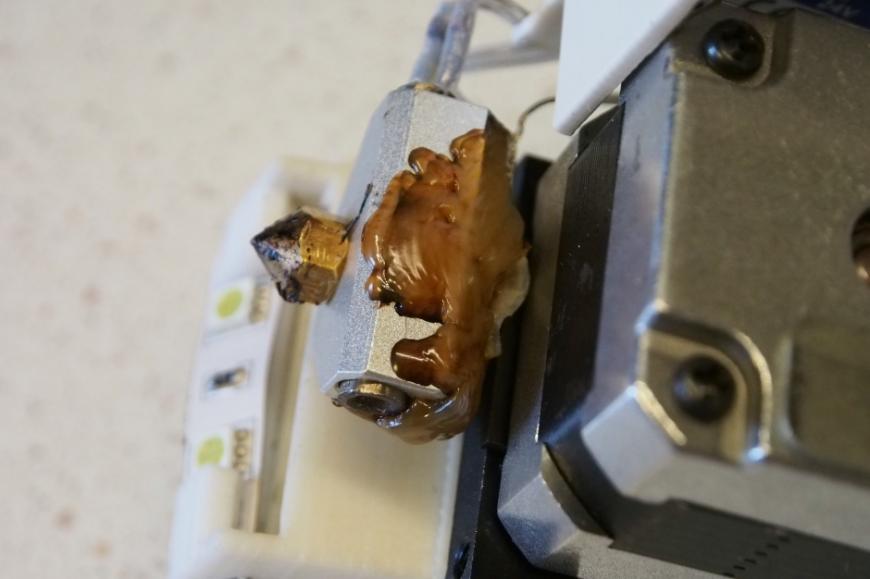
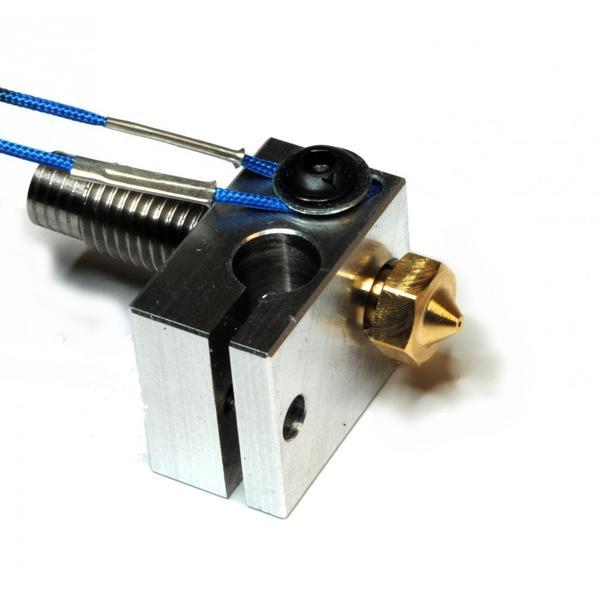
Иногда его выполняют совмещенным с хотэндом, и тогда такой тип экструдера (это все вместе хотэнд+фидер) называют директом (direct), то есть подача прямая, без трубок.
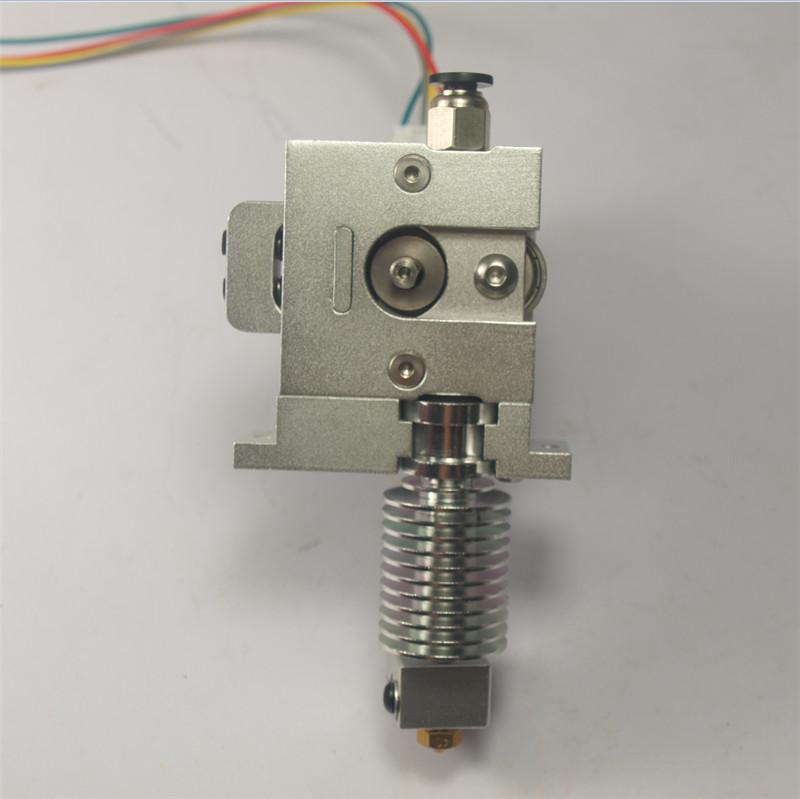
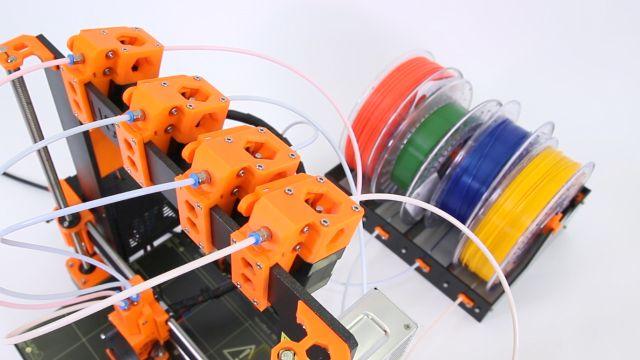
Директ экструдер:
1. Достоинства:
а) Более надежный за счет меньшего числа соединений для подачи пластика;
б) Менее придирчив к материалам, которыми печатает, в частности резиной на основе каучуков проблематично печатать на боуден экструдерах;
2. Недостатки:
а) Большой вес, за счет этого при ускорениях/замедлениях можно наблюдать небольшую рябь на поверхности детали;
б) Габариты. Они очень сильно влияют на область построения. Скажем, как на картинке выше, директ с 4 цветами был бы очень громадным. А для боудена это в самый раз.
Боуден экструдер:
1. Достоинства:
а) Вынесенный мотор снижает вес движущихся частей принтера, а их меньшая инерционность не влияет на поверхность модели;
б) Катушка не дергается вслед за моделью, а то при запутывании витков катушки с директом получим пропуск шагов, так как каретка будет тянуть за собой катушку.
2. Недостатки:
а) Настройки ретракта (вытягивание прутка обратно при холостых перемещениях, что бы расплавленный пластик, расширяясь не сочился из сопла) сложнее, так как пруток меньше внутреннего диаметра трубки, он имеет свойство тянуться;
б) Сложнее, чем на директе, выбрать все зазоры, чтобы печатать различными гибкими пластиками. Все, кто говорит,что на боудене печать невозможна гибкими пластиками — нагло врут. Я печатаю. И вполне успешно.
Теперь переходим непосредственно к механике и ее калибровке.
Часть 2. Механика. Что, как и чем дергает?
Существует весьма ограниченное число кинематических схем, под которые написана прошивка, и которые вполне сносно отрабатывают перемещения.Рассмотрим все, от самых распространенных:
1. Конструкция и кинематика от Джозефа Прюши ( не надо читать Прусся,Праша и прочее, это имя человека, в конце концов).
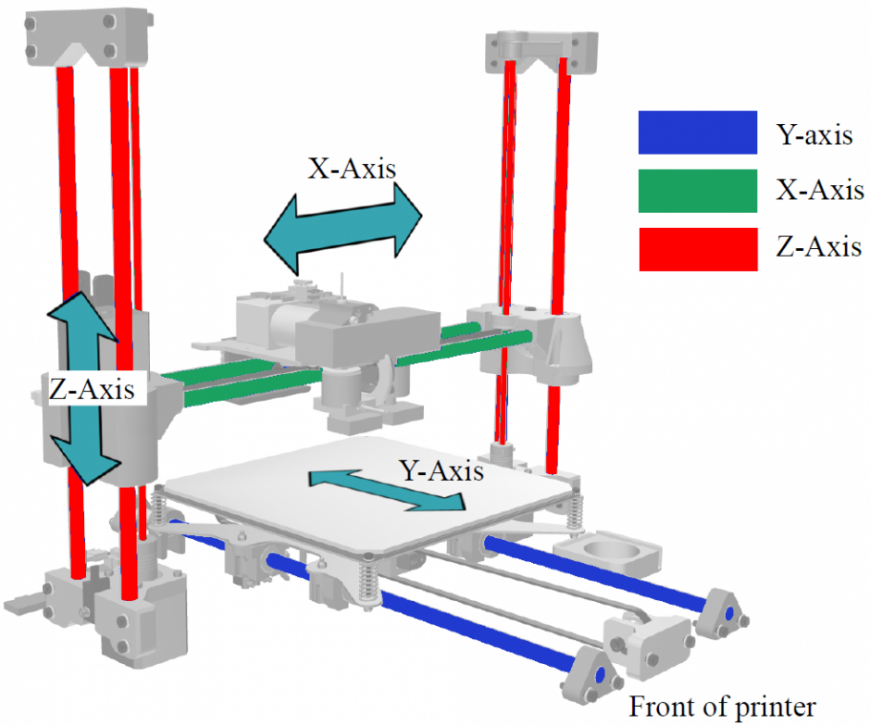
Вот винт с трапециеидальной резьбой. Как шпильки с метрической резьбой выглядят прикладывать не буду.
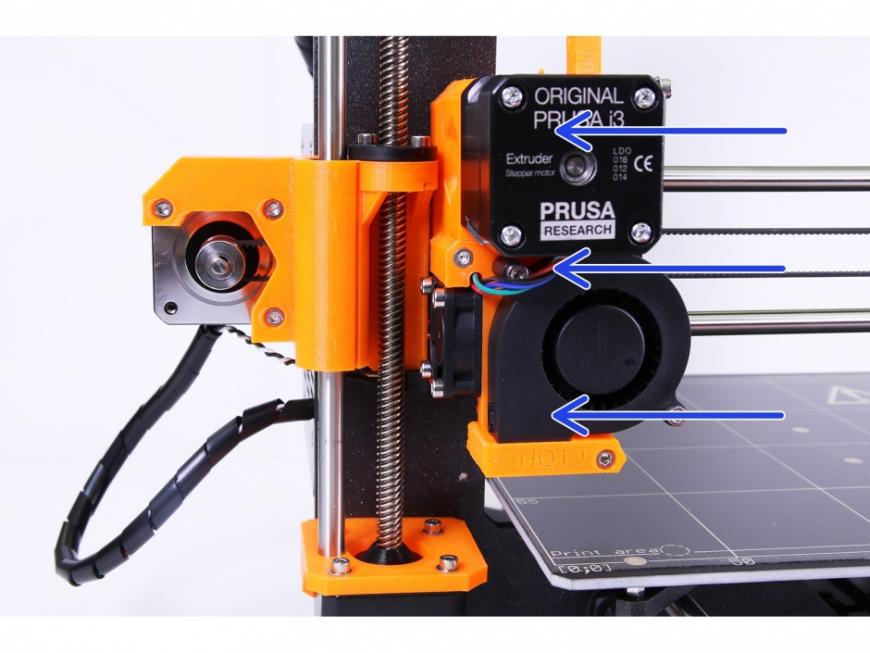
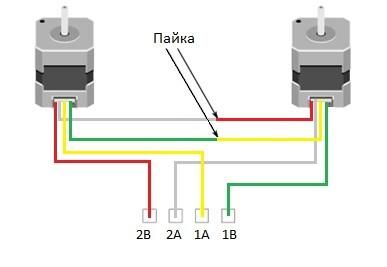
Плюсы данной кинематики:
1) Независимое перемещение каждой из осей. Легко поймать понять какая ось пропускает шаги. Кинематика перекочевала в принтеры от фрезерных ЧПУ, поэтому многие производители делают на ней настольные фрезерные станки, вместо экструдера предлагают установить лазер для гравировок или резки, шпиндель для фрезеровки плат, экструдер для шоколада или даже теста, что б печь блины.
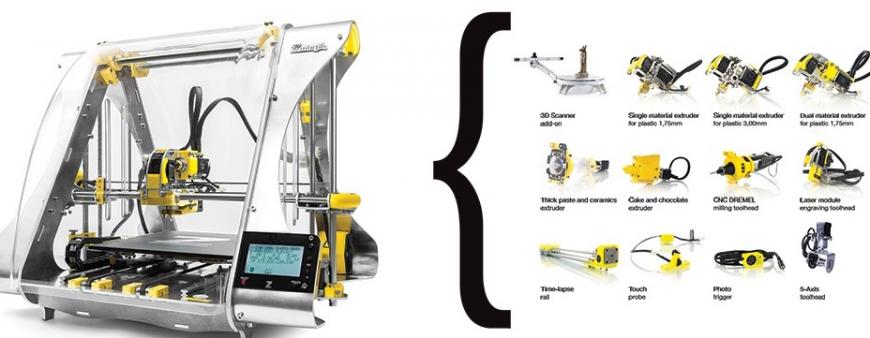
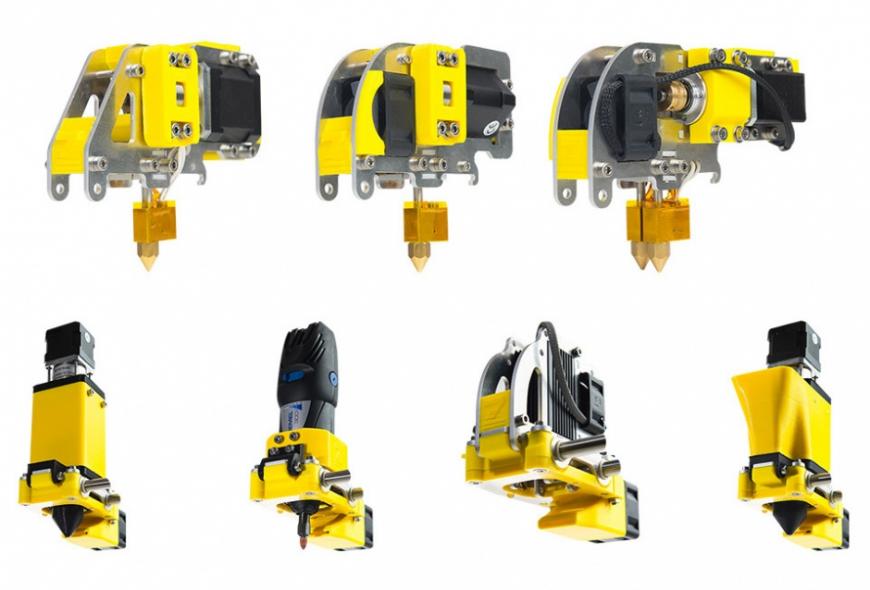
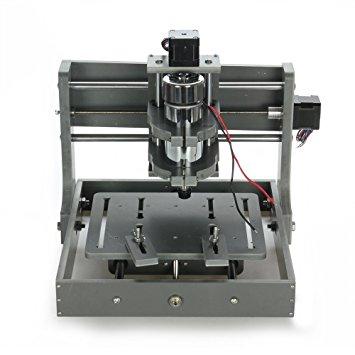
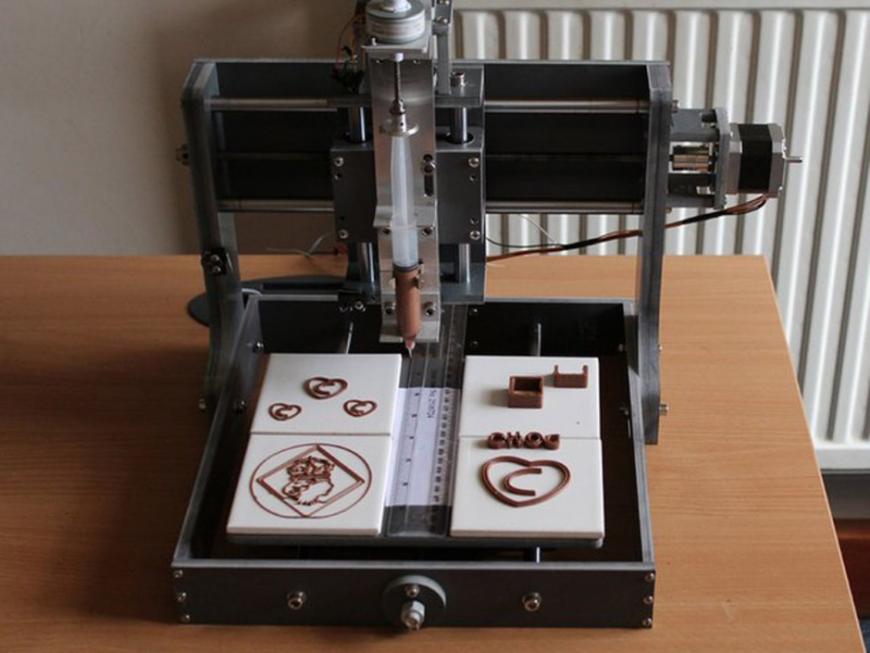
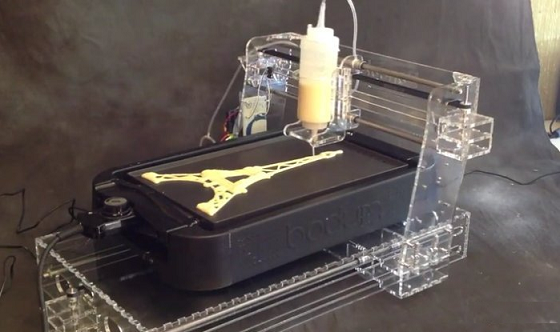
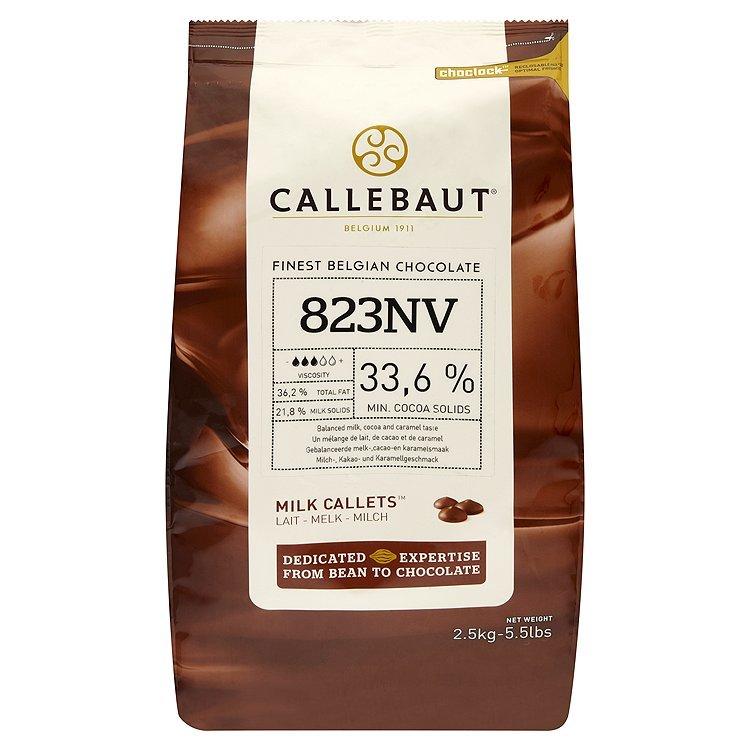
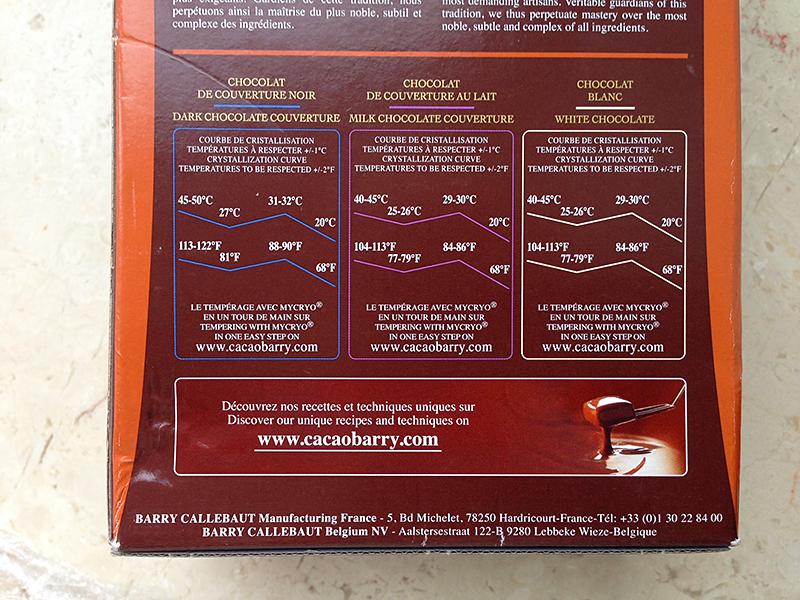
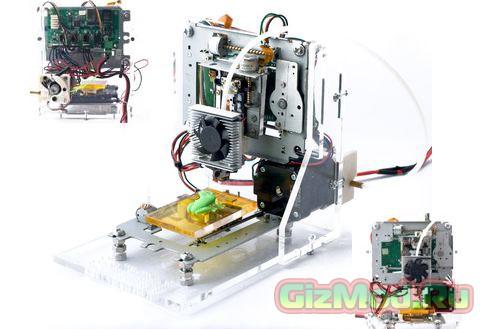
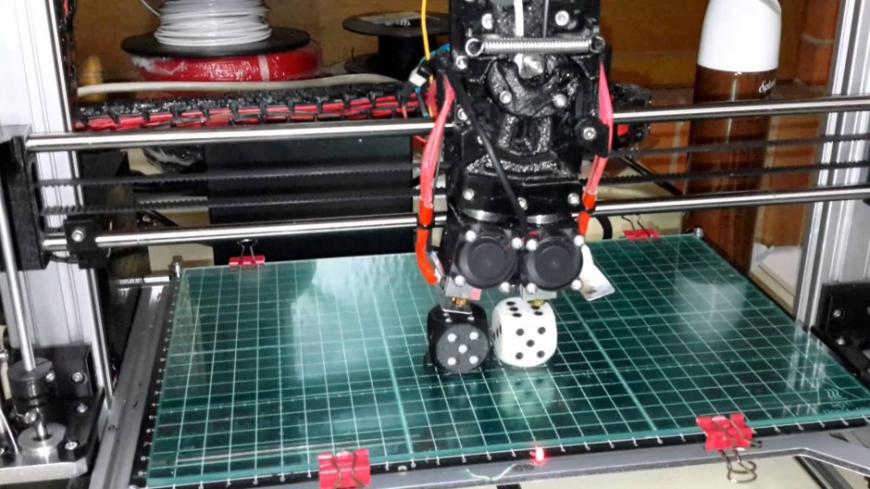
Недостатки данной кинематики:
1) Сложная калибровка. Да, поскольку стол ‘дрыгается’ печатать сложновато качественно, ибо деталь+стол при резкой смене направления перемещения по инерции стремяться ехать дальше. Получаются некрасивые артефакты печати. И для качественной печати нужна небольшая скорость. А вообще, все зависит от рамы. У меня первым принтером была китайская прюша. С акриловой рамой.
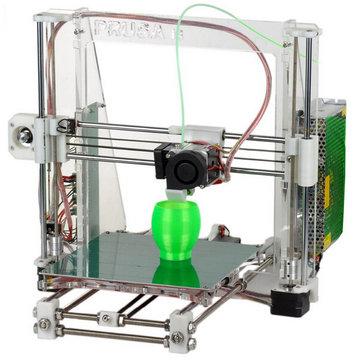
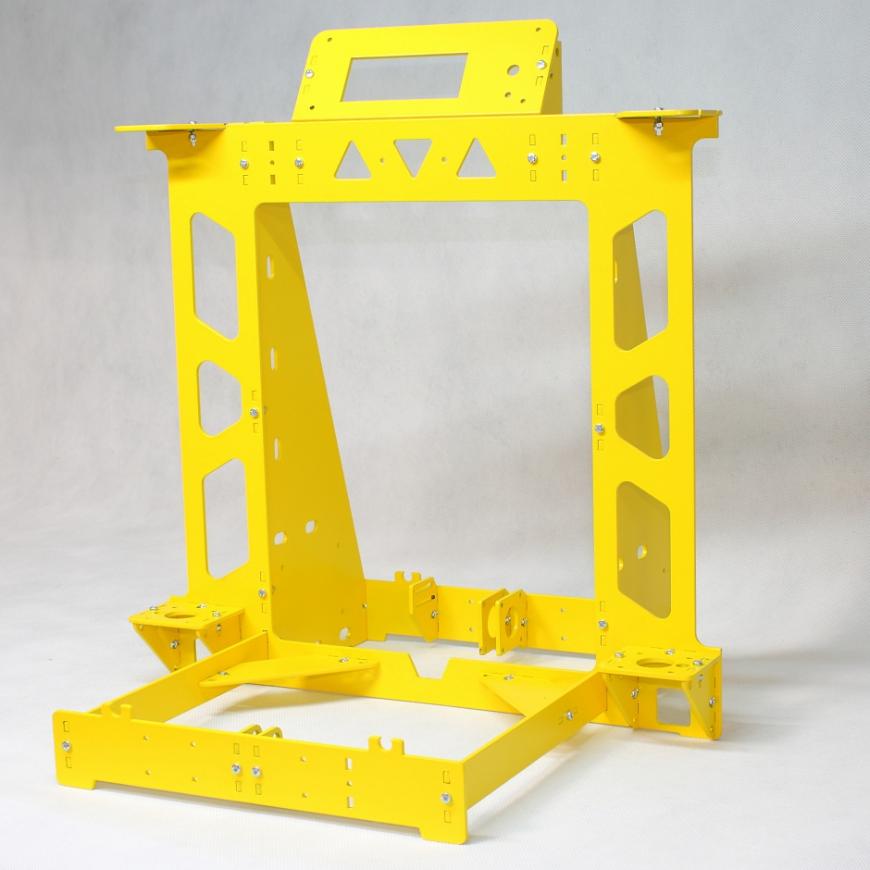
2) Деламинация. Из-за открытого корпуса и постоянно перемещающейся платформы горячий воздух, можно сказать, постоянно сдувается, а охлаждая излишне деталь сквозняками мы увеличиваем и без того большую усадку нейлонов,абс и прочих капризных пластиков. Кто-то шьет шубу для принтера из ткани, а кто-то довольствуется и коробками.
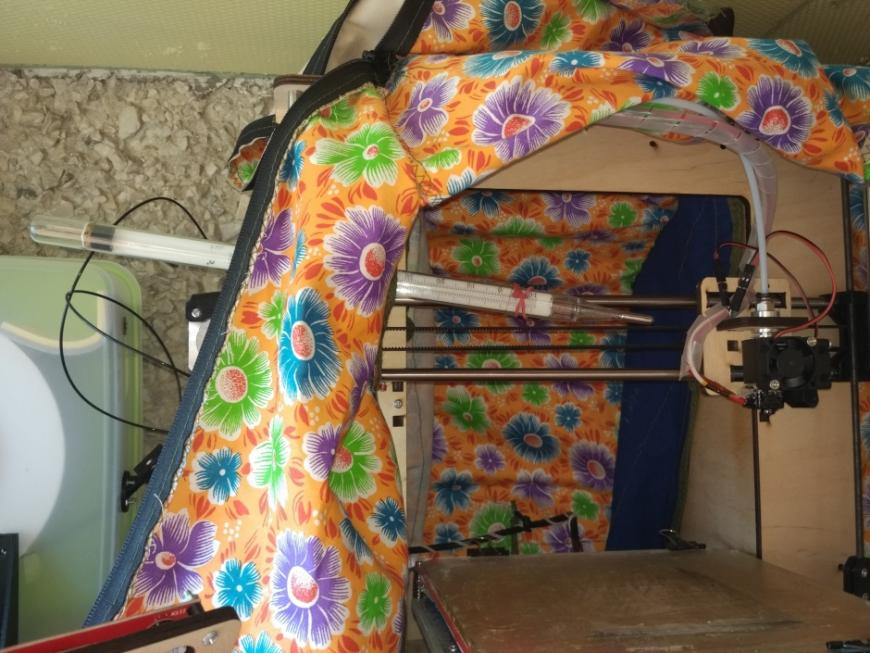
Основные моменты правильной калибровки принтеров с данной кинематикой:
1) Установить принтер на ровную поверхность. Желательно горизонтальную. Для этого необходим пузырьковый уровень. Далее устанавливаем по уровню положение оси X.
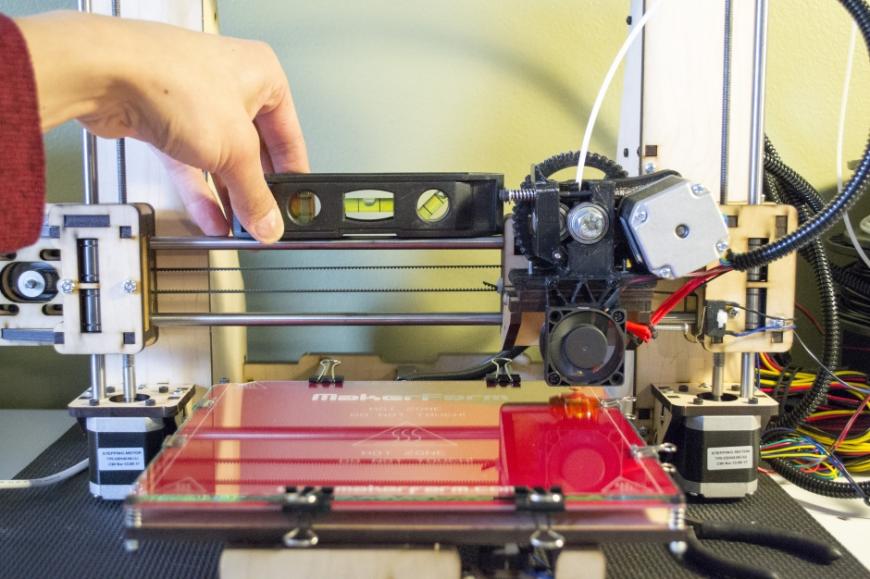
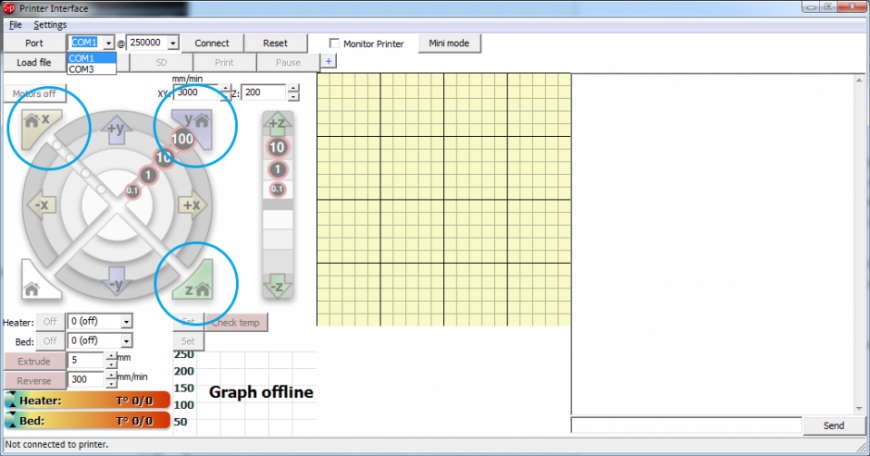
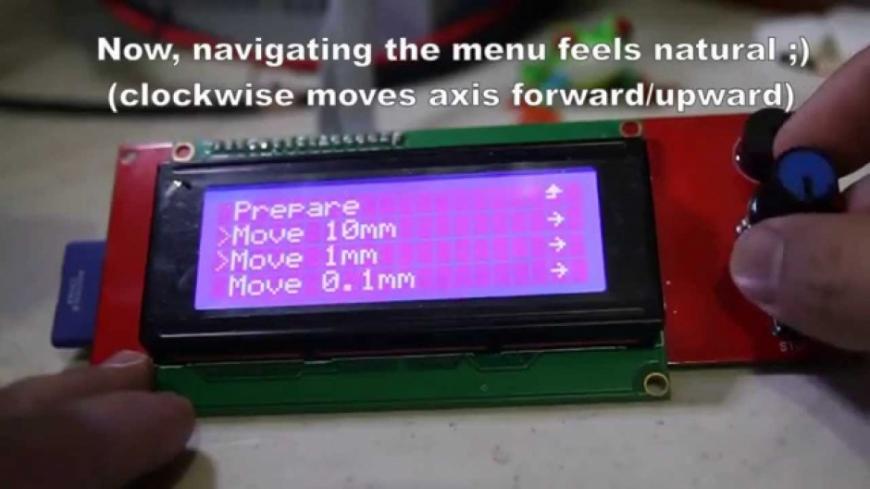
Постараюсь избавить вас от ошибок. На фото принтера выше стекло на столе крепится аж 8 зажимами. И вполне возможно, что по центру будет горб. Чтобы избежать подобных проблем стекло стоит закреплять 3 зажимами. Плоскость строится, как известно из начертательной геометрии, по 3 точкам. И калибровка будет проще в этом случае. Просто подкручиваем винт над концевиком по Z.
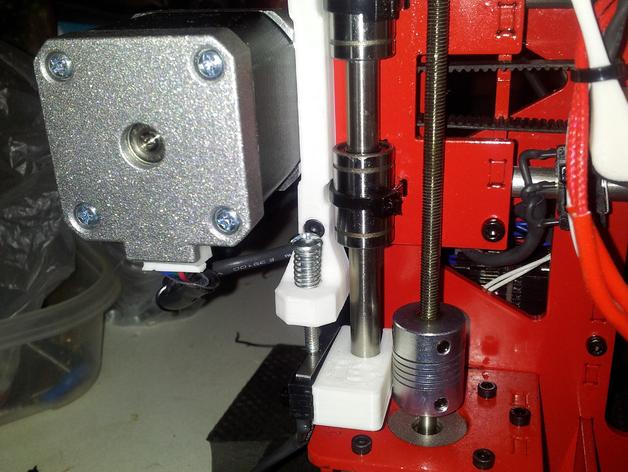
Касательно вобблинга.
Всякие антивобблинговые системы вроде установки продшипника в верхнюю опору не работают.
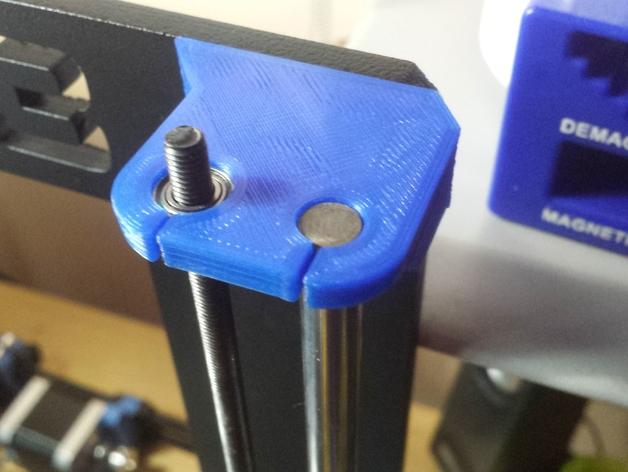
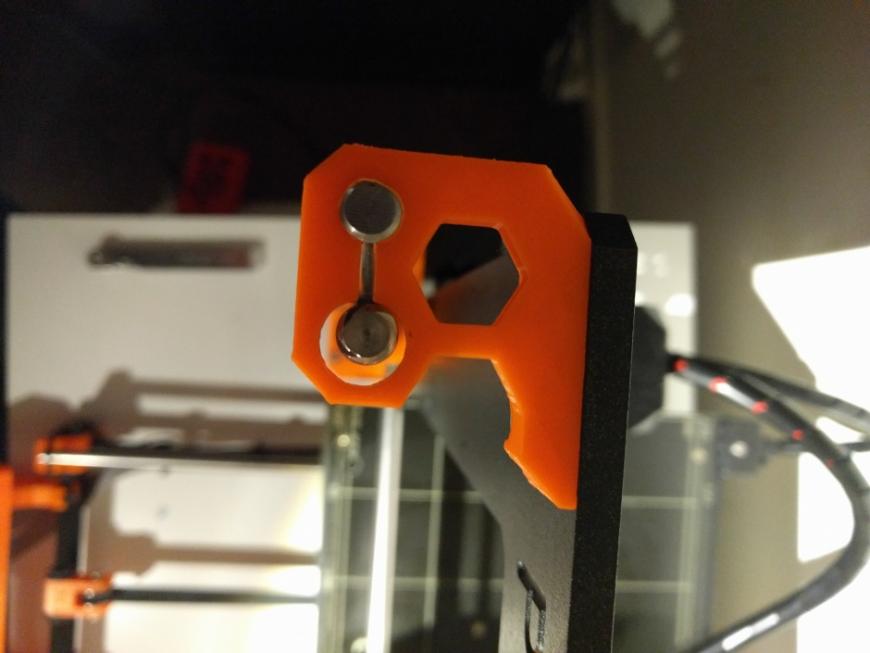
2. Конструкция по типу кинематики принтеров компании Felix printers.
Таких принтеров много, такие делает МЗТО (mz3d.ru), уже упомянутые Felix. По сути кинематика та же, что и у Prusa. Независимые друг от друга оси. Только теперь стол ездит не вдоль одной оси, а сразу вдоль целых двух. Вдоль оси Z, и по оси Y.
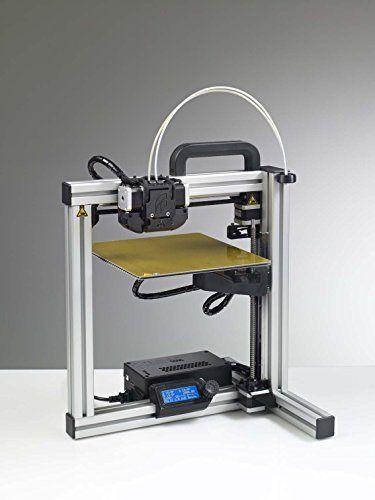
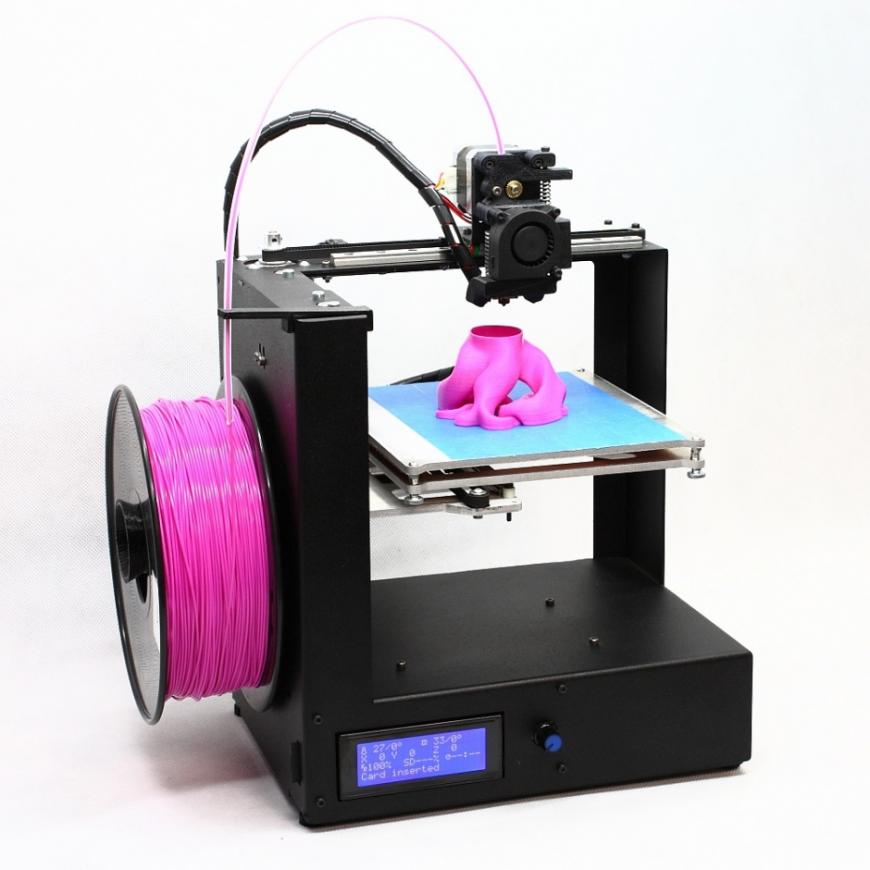
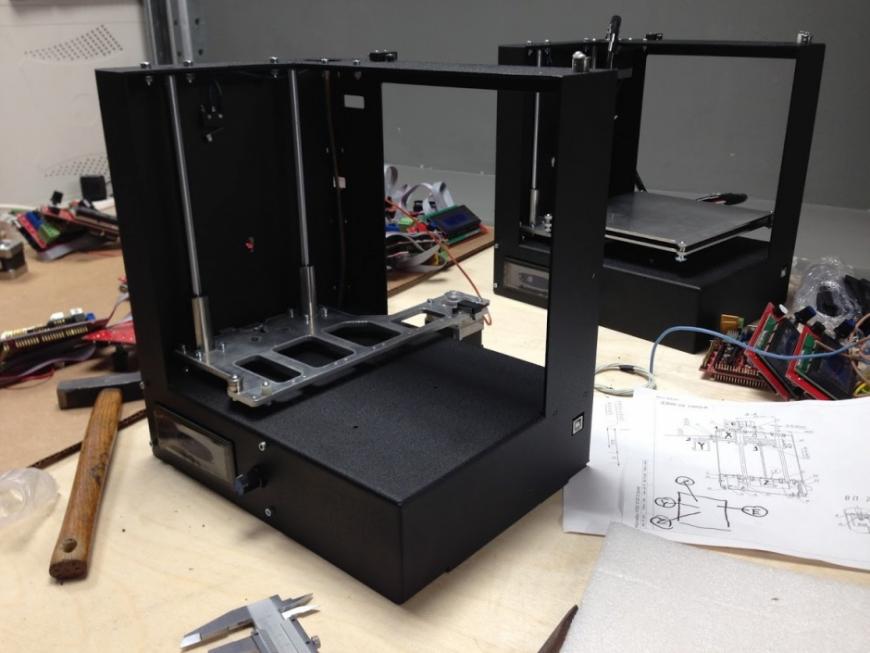
Плюсы данной кинематики:
1) Отсутствует второй мотор по оси Z. Пресловутого вобблинга нет просто потому, что есть 2 вала и 1 винт. Винт, так же не стоит закреплять сверху. Если это не ШВП.
ШВП это отдельная тема. Если брать качественную ШВП, скажем, от тех же Hiwin, то она изготавливается как минимум по 7 классу точности (если катанная, а если шлифованная, то класс еще выше) и устанавливаться должны в подшипниковых опорах. Со стороны привода — 2 радиально-упорных подшипника back-to-back,а с другого конца — радиальный со свободной посадкой для компенсаци теплового расширения.
Цель установки ШВП — обеспечение точности перемещения. Если же ее устанавливать неправильно — деньги на ветер, и точность будет не выше пары винт-гайка с трапециеидальной резьбой. Для FDM c лихвой хватит точности трапеций.2) Много места для установки директ-экструдера. Как и в предыдущей кинематике есть простор для творчества, подбирать тот самый, единственный и неповторимый экструдер, который вам по душе.
3) Жесткая рама. Есть возможность сделать нормальную раму. Жесткую,прочную. Да хоть чугуниевую. Ребята из Феликса решили не забивать голову и лепят из алюминиевого профиля. МЗТО пошли дальше, погнули стальной лист. А полку под установку стола отфрезеровали из листа алюминия.
4) Если брать конструкцию Феликса на профиле, то с помощью замены пары кусков профиля и винта по Z можно увеличить область печати.
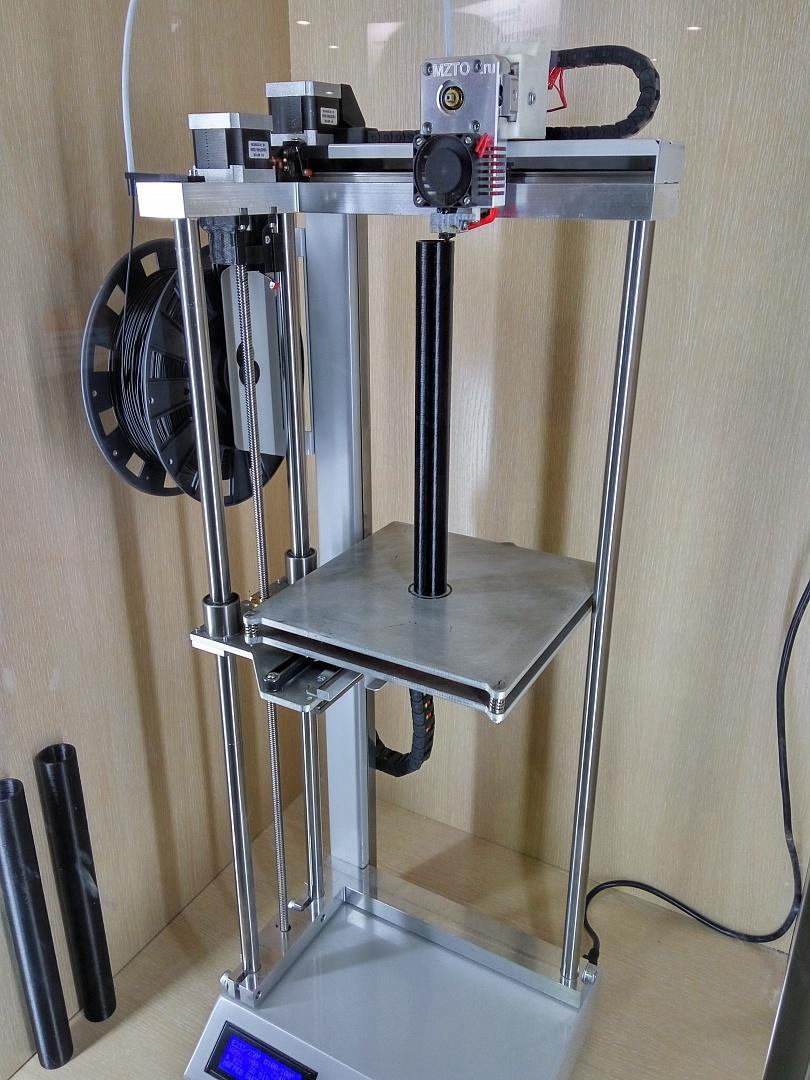
Недостатки кинематики:
1) Несомненно, большие дергающиеся массы. Стол вперед-назад,а если включить движение по Z при холостых перемещениях (Z-hope), то будет дискотека.
2) Нет возможности сделать ему нормальную термокамеру. Стол двигается вперед-назад и градиент температуры просто сдувается. Отсюда проблемы при печати нейлонами или ABS. Небольшие сквознячки в комнате с легкостью покажут вам где раки зимуют как усаживается материал.
Калибровка стола данного принтера аналогична калибровке стола у Prusa, только несколько проще. Проще за счет того, что ось X вам выставлять по уровню не надо, она автоматически выставлена при сборке рамы. Подводим сопло к столу и крутим барашки.
3. Кинематика Ultimaker.
Одна из наиболее распространенных вариаций Cartesian кинематики.
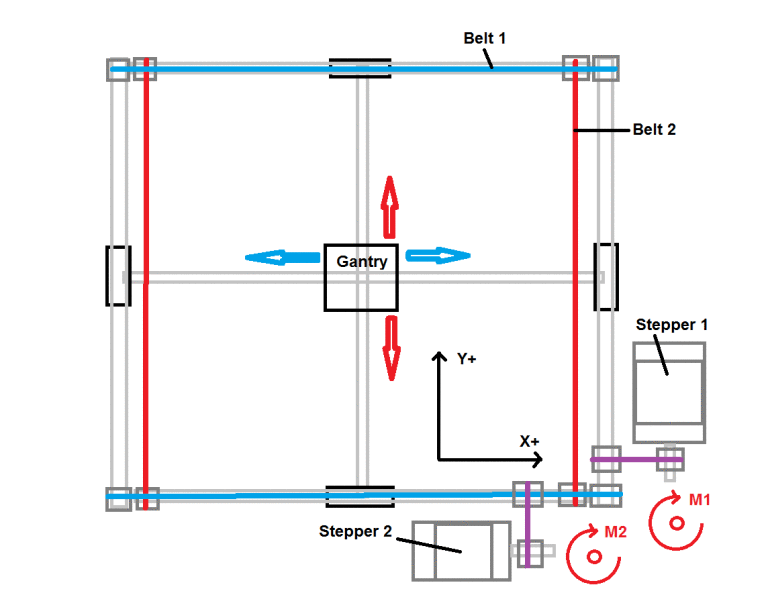
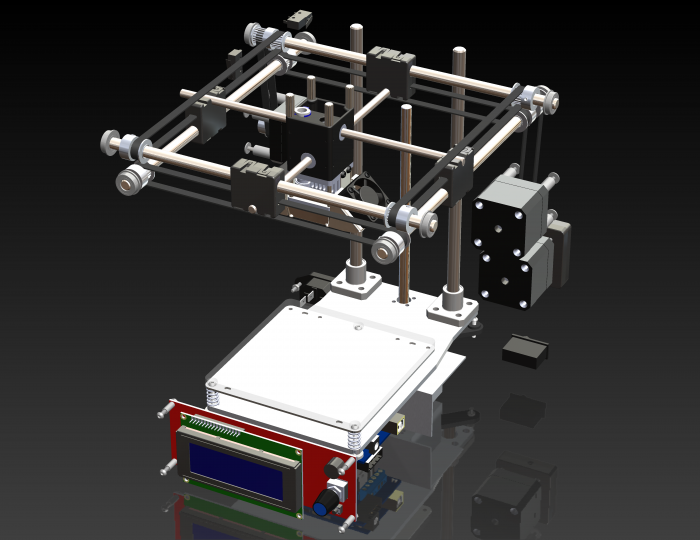
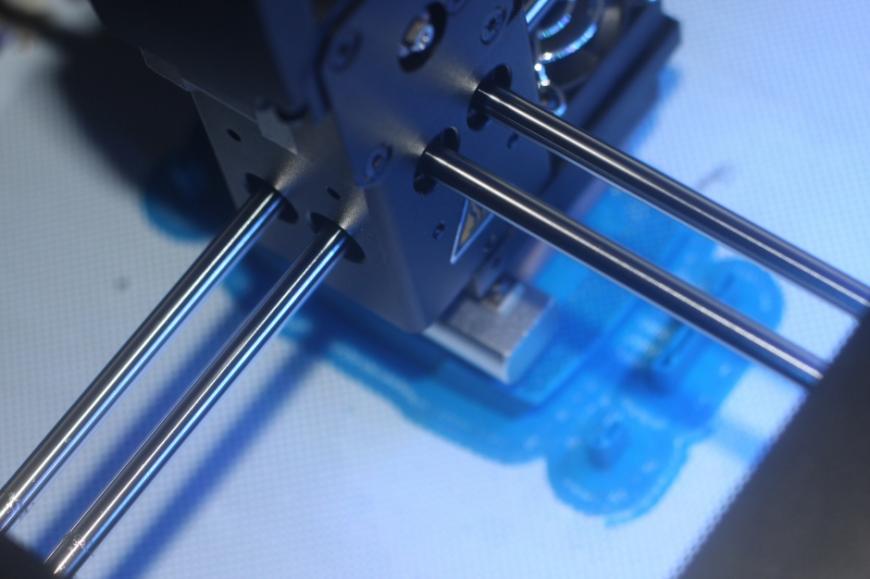
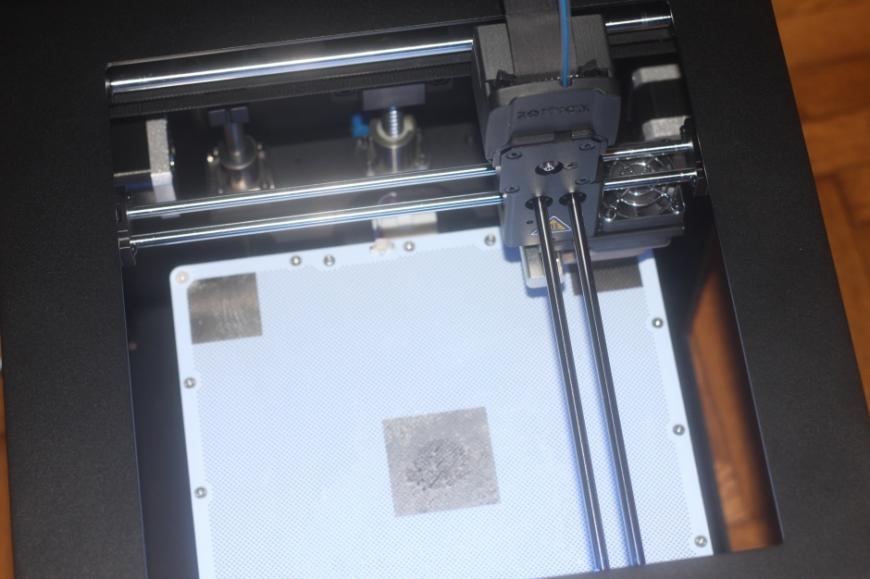
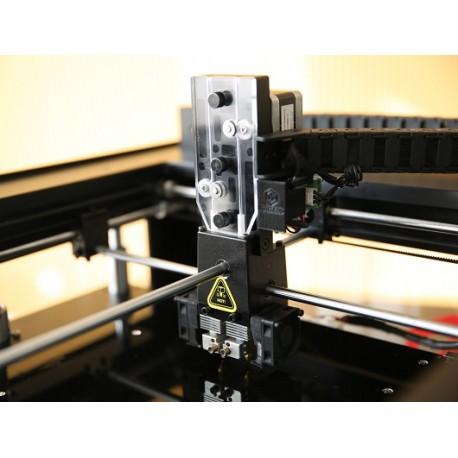
Плюсы данной кинематики:
1) Стол движется только вдоль одной оси. Вертикальной. И градиент температур никоим образом от этого не страдает. Стол консольный, поэтому желательно предусмотреть ребра жесткости или учесть это толщиной стола.
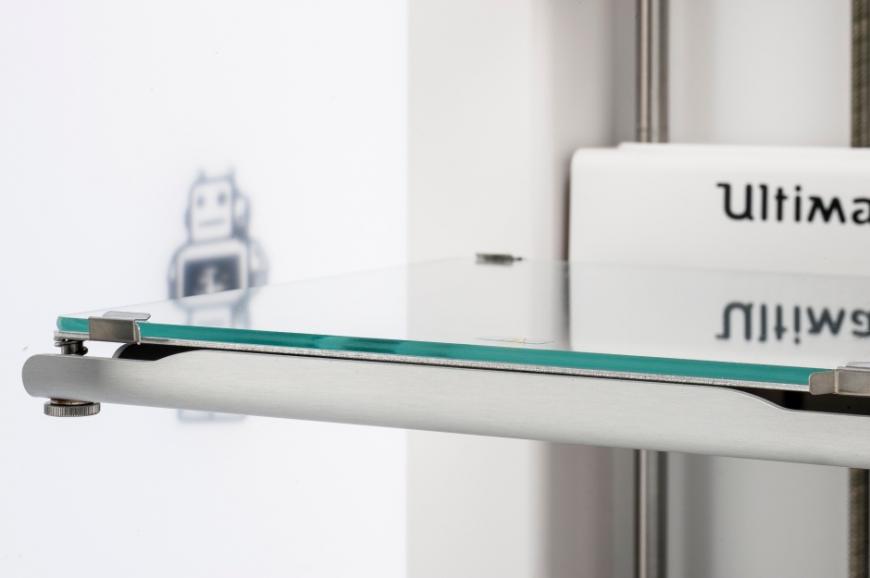
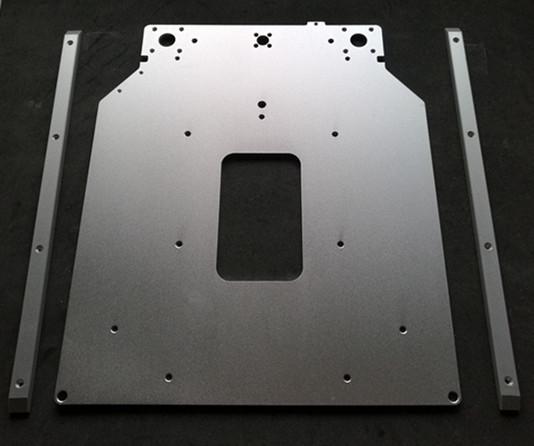
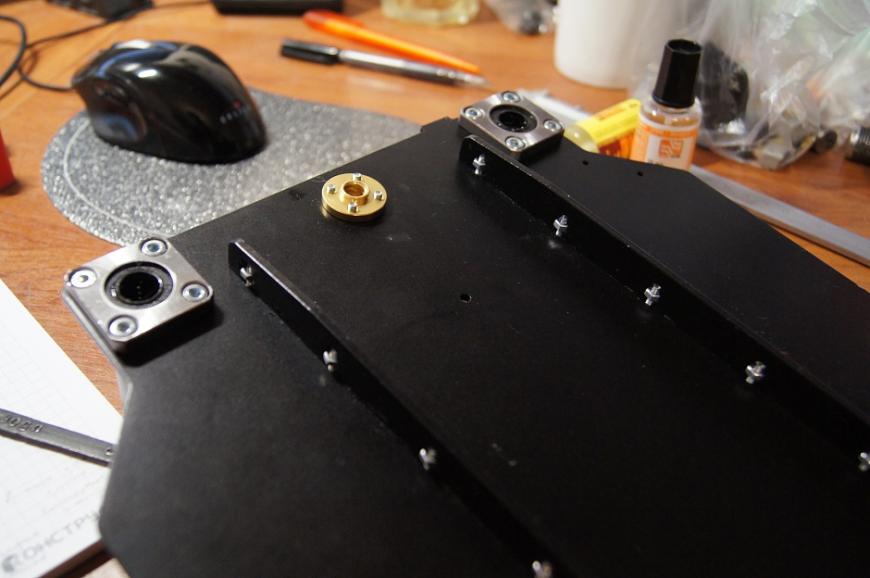
3) Корпус закрытый, что защищает от сквозняков, и следовательно деламинации. Некоторые для пущего эффекта ставят акриловую дверцу.
Минусы кинематики:
1) Для хорошей печати мало купить пачку ровных валов. Собрать все эти валы правильно воедино та еще задачка. Заодно и купить хорошие подшипники. Не то, китайское барахло, что чаще втюхивают на али, а нормальные подшипники. Если подшипники, что ставят в корпус будут плохо вращаться — печать будет рывками и со сдвигом слоев. Последствия можно спросить у Вани (Plastmaska). Так же, покупая леопардовые втулки латунные подшипники с графитовыми вставками будьте готовы к тому, что они будут люфтить. А если будет люфт — вся конструкция будет стучать.
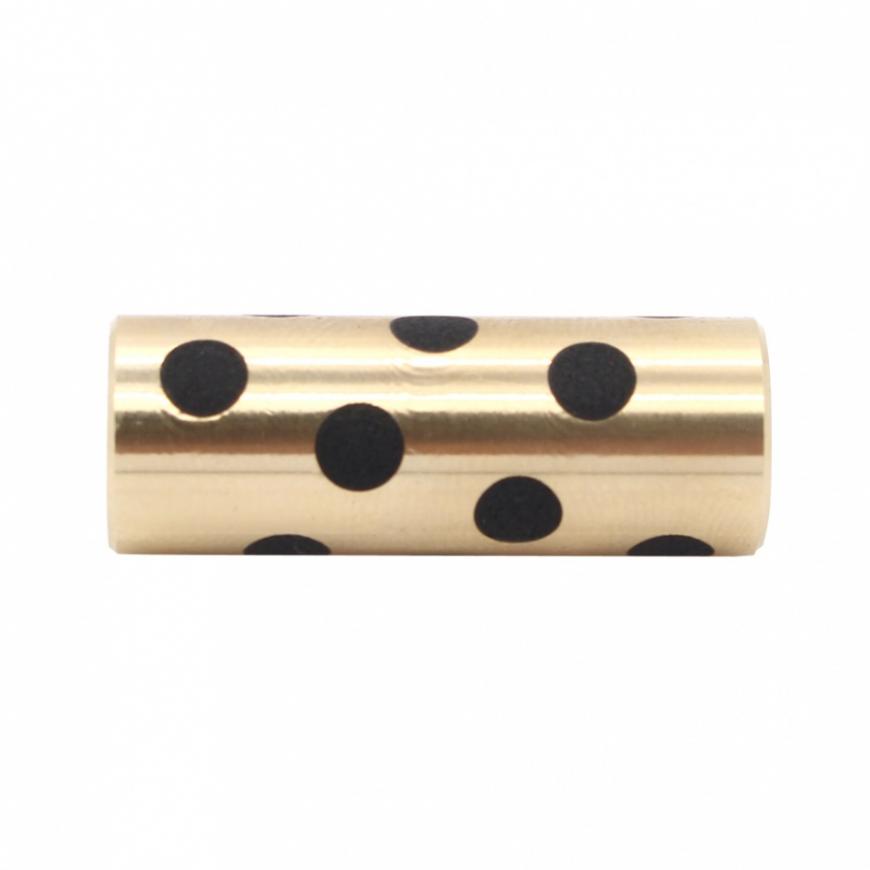
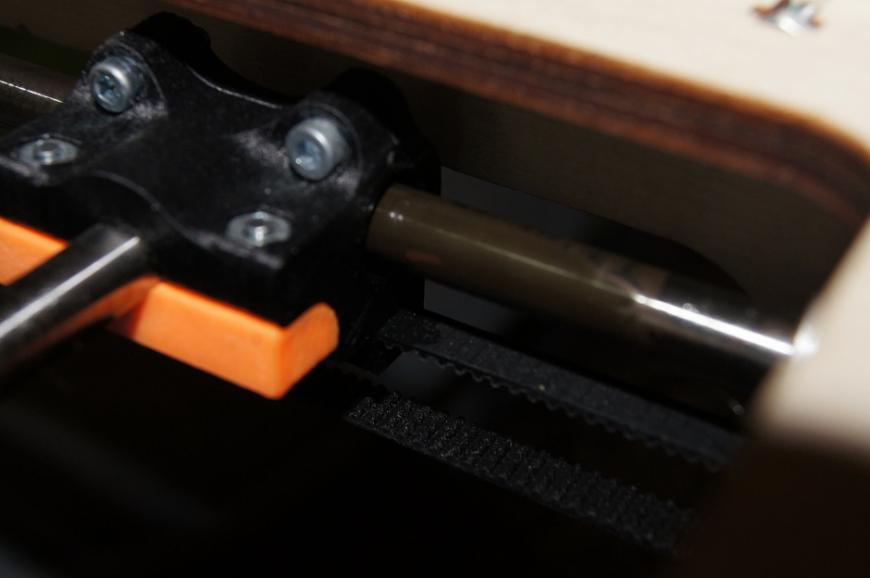
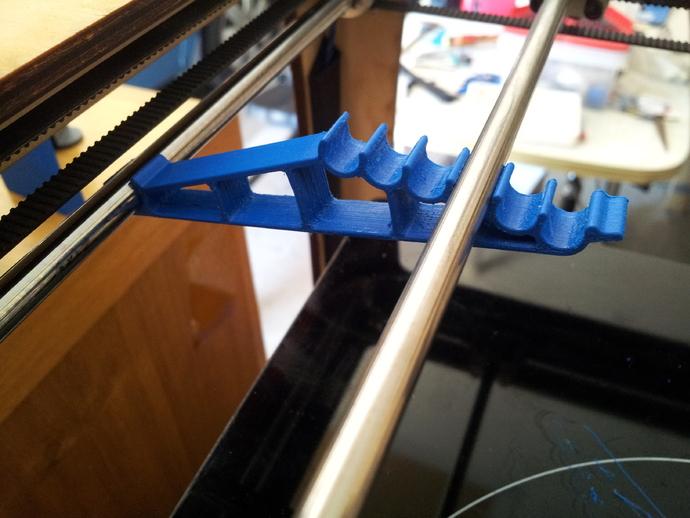
3) Конструкция не предусматривает увеличение области печати с помощью пары кусоков профиля, поэтому размеры хотенда имеют значение. Директ сложновато поставить, но можно при желании.
Калибровка стола проще некуда. Стол часто на 3 точках крепления. Перемещаем хотенд по 3 точкам и крутим барашки.
4. Кинематика, используемая фирмой Makerbot.
Так же, весьма широко распространена. В частности принтеры компании Makerbot, BQ, BCN3D ,Magnum, клон магнума — Zenit и вполне сносные реплики makerbot — Flashforge и Hori работают на данной кинематической схеме.
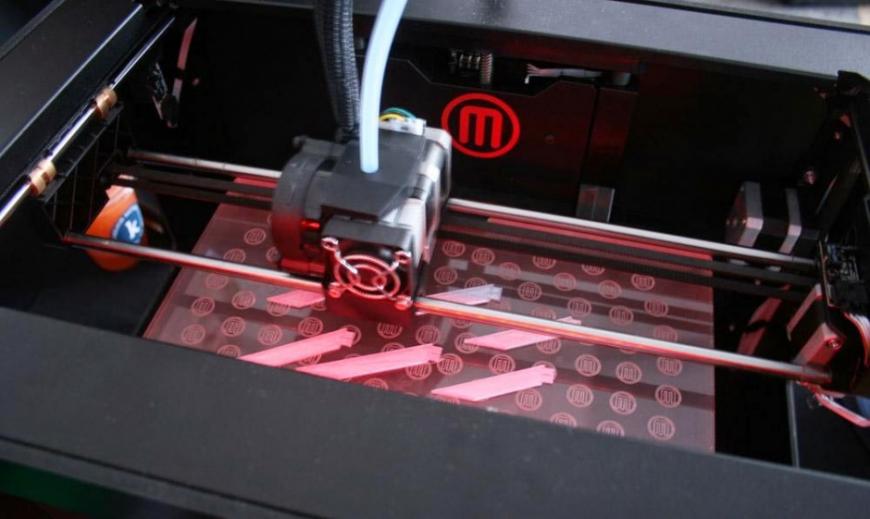
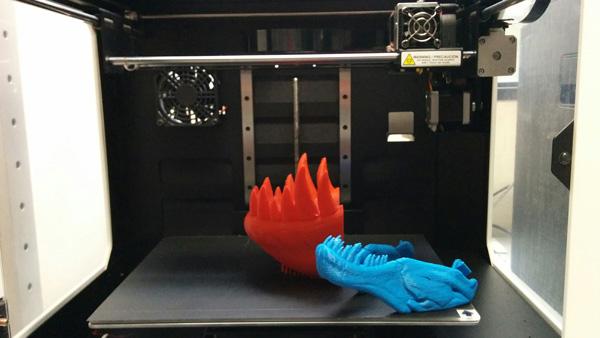
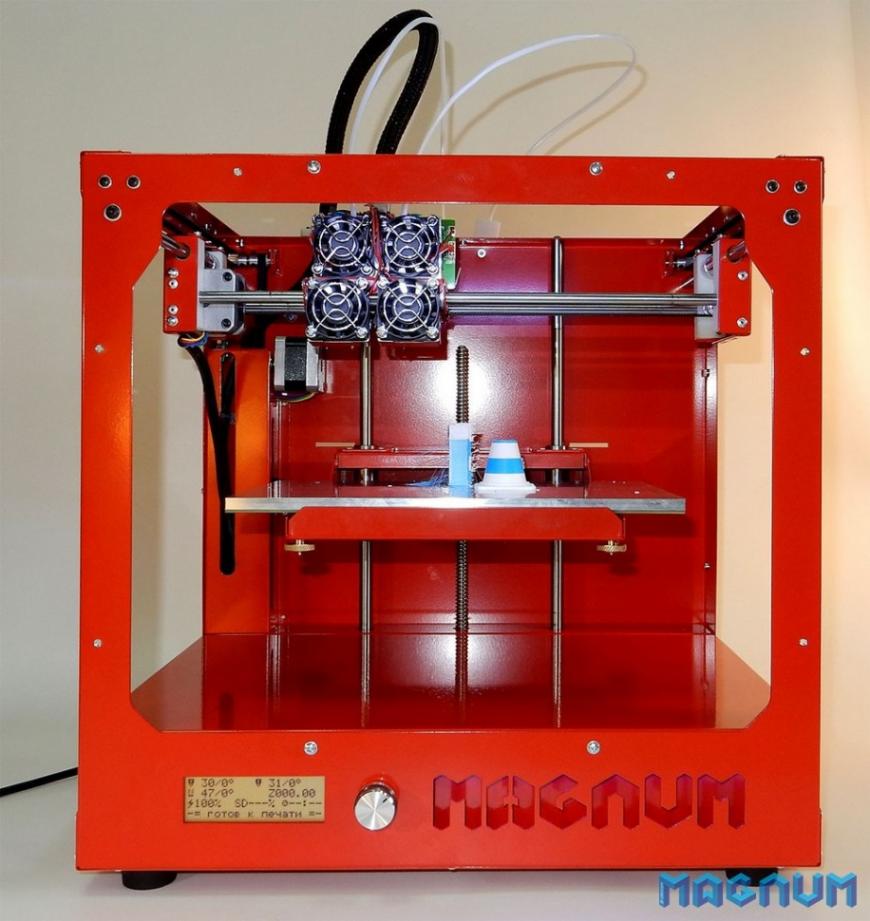

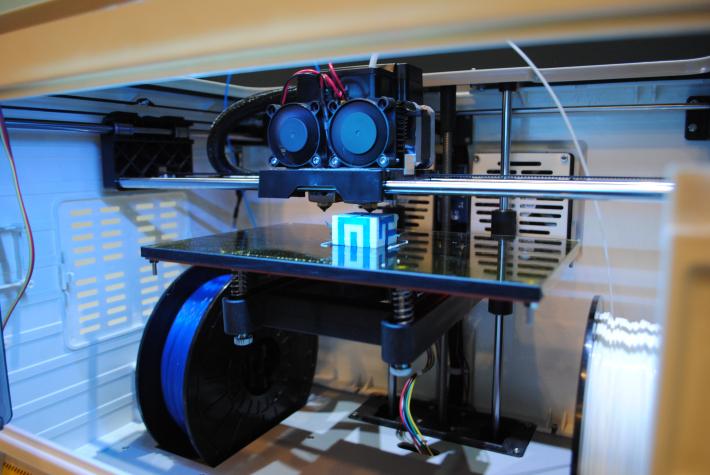
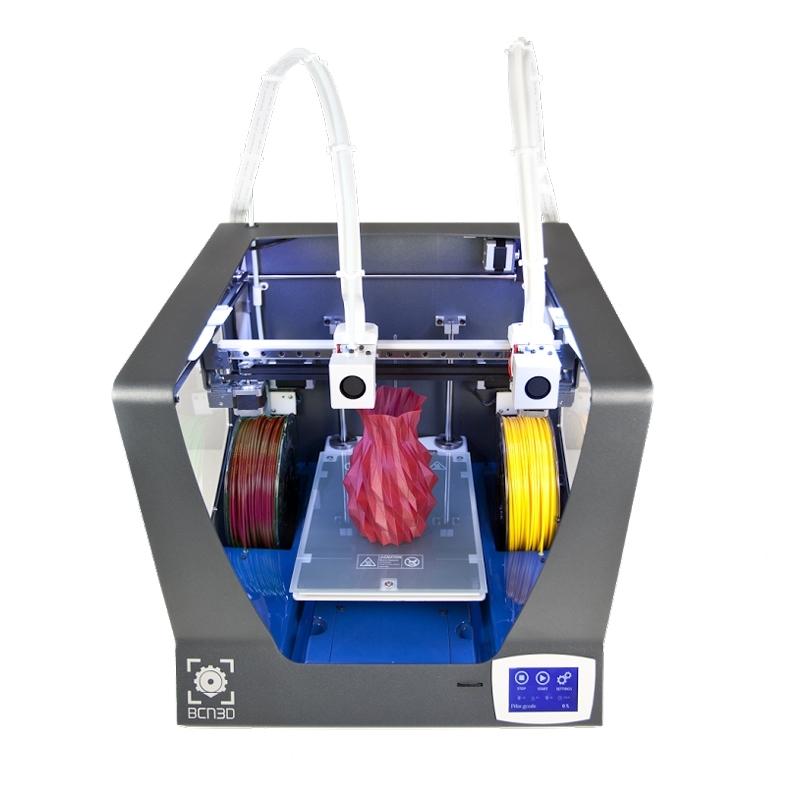
Основной недостаток заключается в том, что на катающейся балке с одной стороны висит двигатель, создавая эдакий дисбаланс. Этот недостаток компенсировали в двухэкструдерном варианте — BCN3D Sigma. Там у каждой bowden-головы для перемещения вдоль балки есть свой двигатель. И они установлены по краям балки и уравновешивают друг друга. Для равномерного перемещения каждого из краев балки применяется 2 вала, шкивы и ремни. Ремни необходимо натягивать одинаково.
Достоинства кинематики:
1) Независимое перемещение каждой из осей.
2) Движущийся по Z стол. Градиент температур не страдает ‘сдуванием’.
3) Закрытый корпус. Если не закрытый, то есть вполне нормальный с точки зрения эстетики шанс закрыть его.
4) Масштабируемость кинематики возможна. Различные BigREP и иже с ними с метровыми областями печати используют именно эту кинематику, так как различные H-bot/CoreXY будут адово звенеть по причине наличия 4-5 метровых ремней и их растяжения во время ускорений.
Недостатки кинематики:
1) Неуравновешенные массы на движущейся балке, отсюда максимальная скорость печати, с приемлемым качеством не больше 60-80 мм/с. Некоторые умудряются их уравновесить и это не столь заметно.
2) Громоздкие конструкции на валах, дабы избежать дисбалланса при перемещениях.
3) Необходимо следить, чтобы натяжения ремней справа и слева были одинаковы.
4. Кинематика H-bot/CoreXY.
Следующая по распространению. Так же, Cartesian. Два мотора неподвижны, но перемещают каретку по направляющим с помощью одного длинного куска ремня, или с помощью двух, но покороче. Математика сложнее, чем у предыдущих, так как необходимо синхронизировать поворот обоих роторов двигателя. То есть, для перемещения вдоль каждой оси нужно вращать оба мотора, а для перемещения по диагонали — всего 1.

По сути математика для вращения моторов одна и та же, а реализация в механике разная. Один из самых больших недостатков H-bot перед CoreXY состоит в том, что при перемещениях ремень стремится повернуть балку.
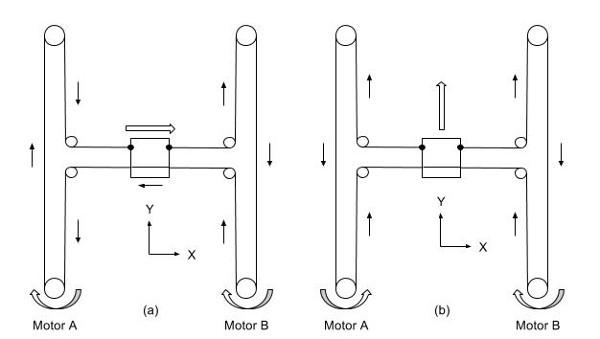
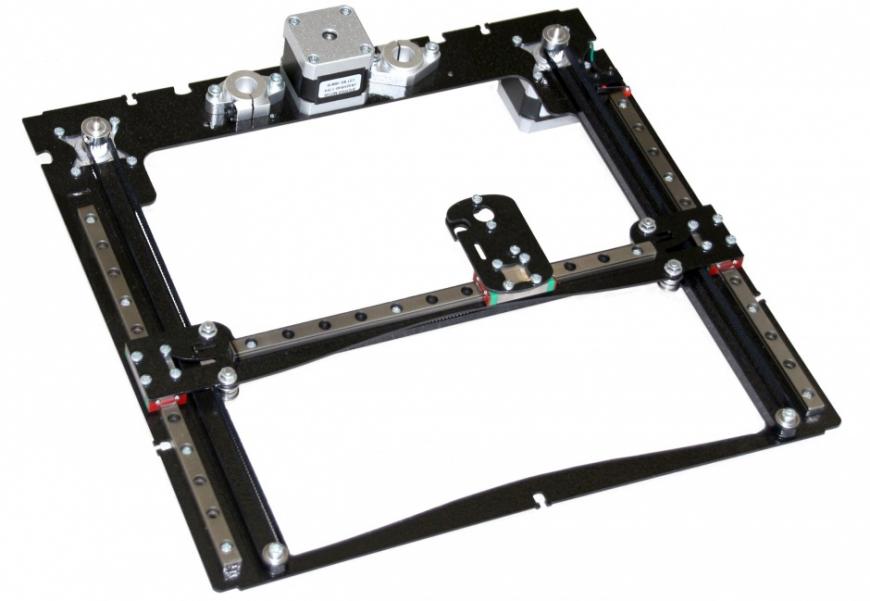
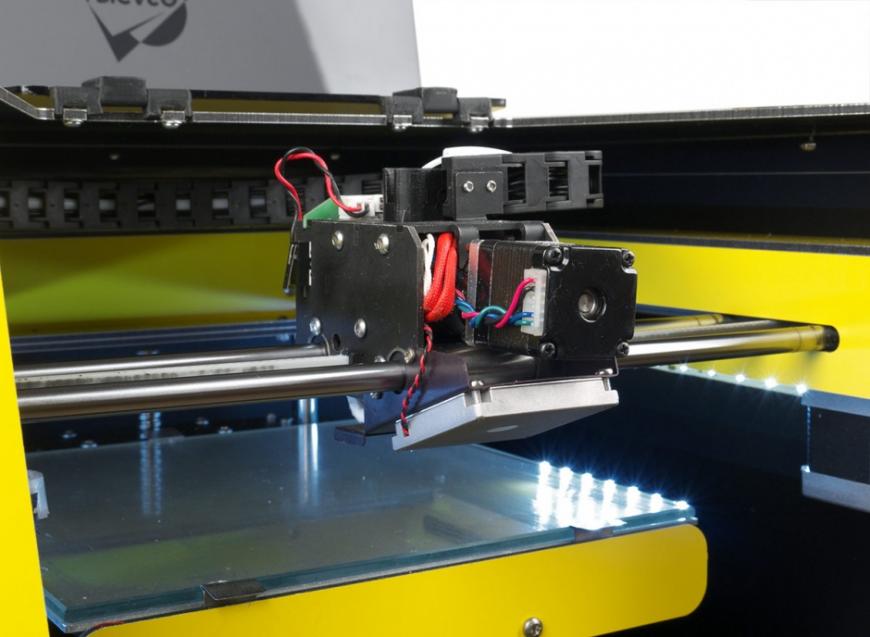
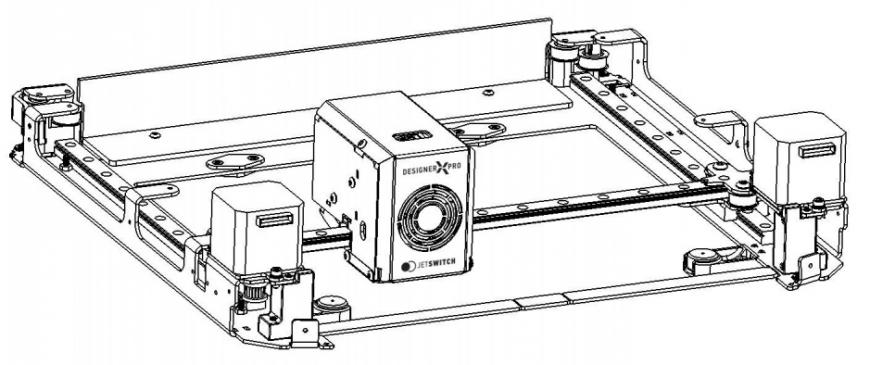
CoreXY, в отличии от H-bot, приводится в движение при помощи двух ремней.
И так, для простоты понимания, опишу положительные и отрицательные стороны каждой вариации этой кинематики.H-bot.
Достоинства:
1) Ремень необходим всего один, а схема предусматривает его работу без скручиваний.
2) Натягивать один ремень удобнее, чем 2, поэтому в этой схеме нужен всего один нормальный натяжитель.
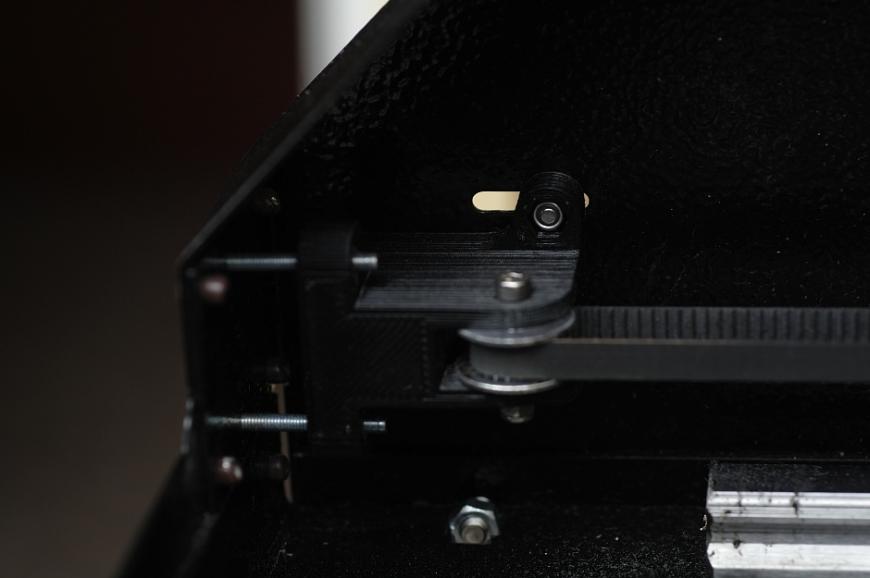
Недостатки:
1) Ремень имеет свойство растягиваться со временем, а так как величина растяжения напрямую зависит от длины, то необходимо следить за его натяжением. Иначе получатся некрасивые волны на поверхности перед остановками.
При слабой натяжке ремня каретка будет иметь такой люфт.2) Необходимо выставлять ролики строго перпендикулярно плоскости XY, так как при небольшом перекосе ролика ремень будет съедаться об буртики ролика. И мы получим такую вот бяку.
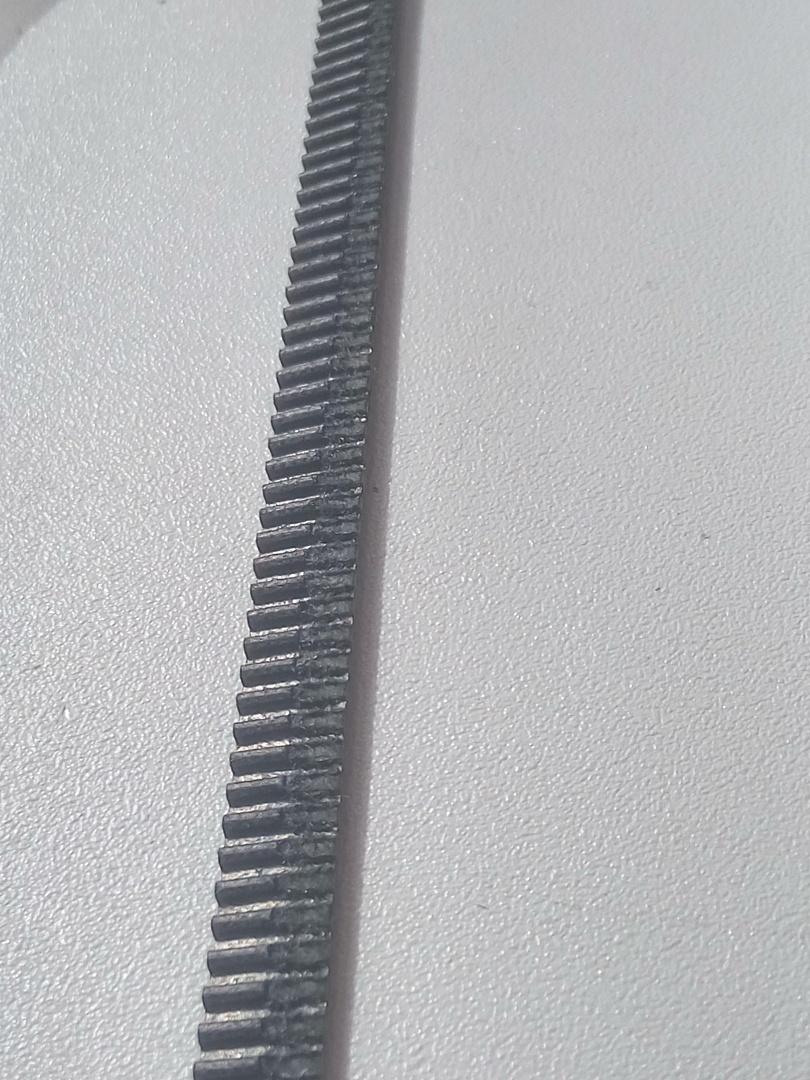
3) Сложная математика, из-за чего на скоростях выше 100 мм/с могут быть проблемы с нехваткой ресурсов 8 битных плат.
CoreXY.
Достоинства:
1) Два коротких куска ремня. Их проще найти, чем один длинный.
2) Силы уравновешивают балку, а не стремятся ее повернуть, поэтому эту кинематику можно собирать и на валах.
Недостатки:
1) Есть схемы с перекручиванием ремней и перехода ремня с одного уровня на другой — для ремня это не очень приятно. Особенно, когда один ремень трется об другой. На видео этот момент есть.
:{}
2) Сложность нятяжки ремней. Их необходимо натягивать одинаково, иначе силы нятяжки будут стремиться повернуть каретку.
3) Сложность сборки и разработки. Необходимо выдержать вертикальность роликов, относительно горизонтальности площадки для установки моторов и рельс. Небольшой перекос роликов приведет к тому, что ремень будет стремиться съехать по ролику, а если будет упираться в буртик ролика, то будет скрипеть, если буртик большой, а если маленький — то будет пытаться на него заехать, как на фото из описания h-bot.
Общий недостаток кинематики — плохая масштабируемость. То есть ставить такую кинематику для области печати больше 300*300 весьма проблемно просто из-за удлинений ремня при печати. Для небольших принтеров с большой скоростью печати — одна из лучших кинематик.
5. Delta кинематика.
Кинематика основана на движениях дельта-робота.
Только вместо захватов устанавливается хотенд. Имеет свои проблемы с настройкой, но на печать можно залипать очень долго. Редко когда устанавливают директ-экструдеры, так как эффектор (площадка для установки хотенда) часто крепится на магнитах и необходимо максимально разгрузить его. Но для уменьшения длины трубки (а конкретнее, влияния длины трубки на качество печати за счет правильной настройки ретрактов ( вытягивания пластикового прутка назад с целью уменьшения его вытекания от расширения)) на качество печати, экструдер вешают на те же каретки, но на отдельных подвесах. За счет этого уменьшается длина bowden трубки и увеличивается качество печати.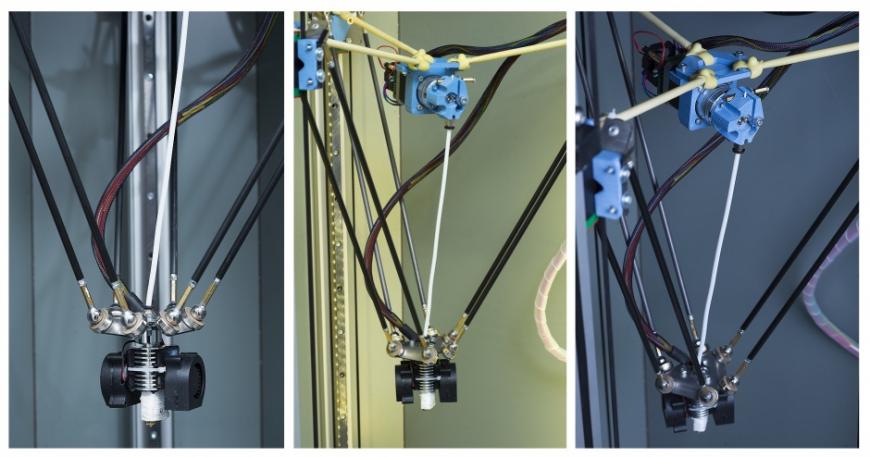
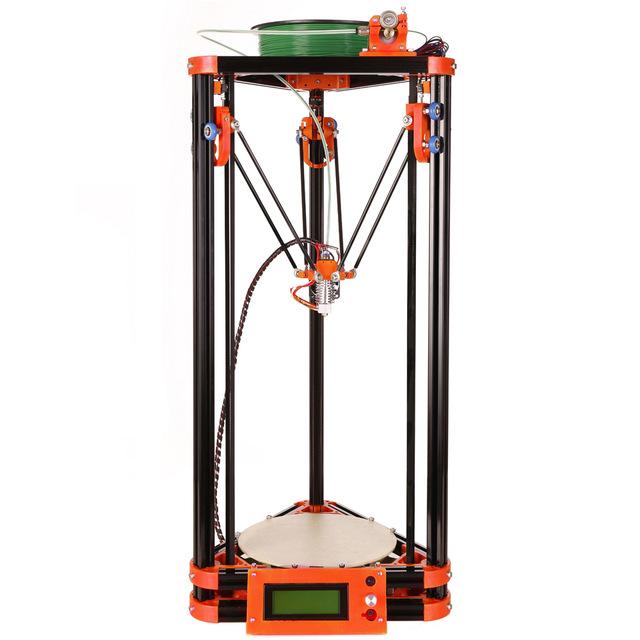
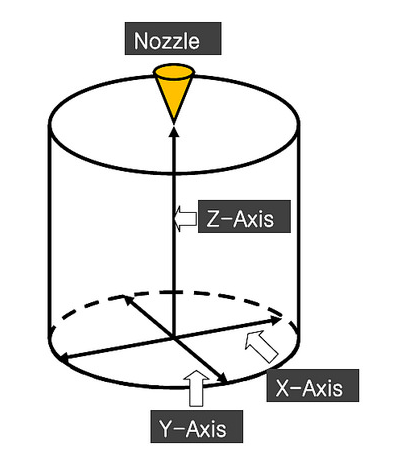
1) Легко кастомизируется. Для увеличения высоты достаточно прикупить 3 куска профиля подлиннее, и увеличить максимальную высоту в настройках.
2) Занимает мало места. Она чаще высокая, чем громоздкая по длине и ширине, за счет этого компактность.
3) Если сделать легкий эффектор ( каретка, на которой установлен хотенд), то можно добиться больших скоростей без потери качества печати.
4) Перемещение по высоте не отличается от перемещения по XY. Таким образом, нет залипания линейных подшипников на переездах стола, как у Cartesian принтеров, лишних двигателей, катающихся на балке…
5) Отсутствие выступающих частей дает возможность закрыть корпус и придать раме жесткости.
6) Эстетическая часть — на работу дельты интереснее залипать.
Недостатки:
1) Сложная математика перемещений, рекомендуется ставить сразу 32-битные платы.
2) Сложная настройка. Частая проблема в настройке — убрать так называемую ‘линзу’, ведь каждый стержень вращается с радиусом, и при некорректной настройке у вас печатаемая плоскость будет либо выпуклой,либо вогнутой линзой.
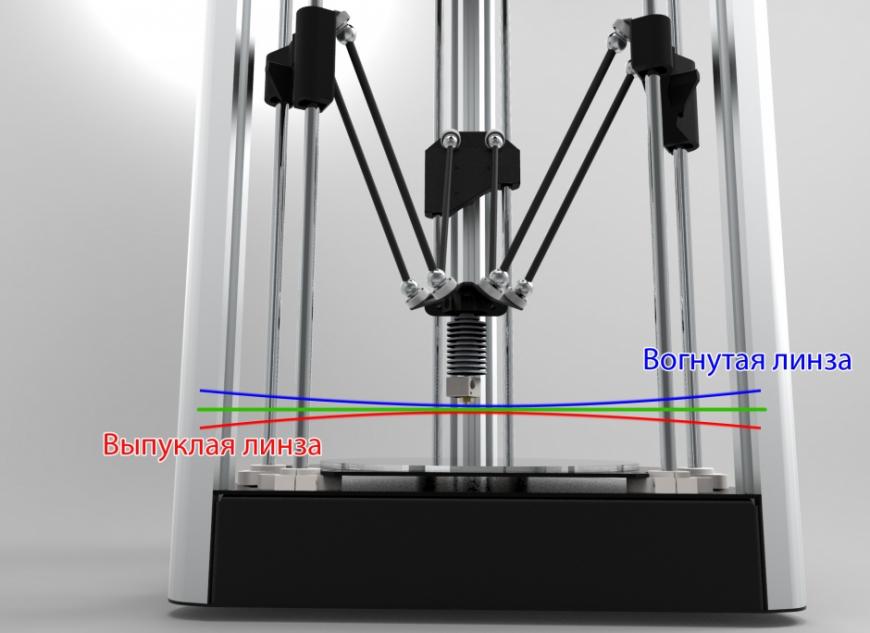
4) Сложность установки директ-экструдера. Он получается тяжелым, а так как многие дельты делаются на магнитах, то не будет возможности разогнаться. Хотя, есть одно аккуратное и легкое решение — установка готового директ-экструдера с редуктором. Как, например E3D Titan Aero или Bondtech BMG.
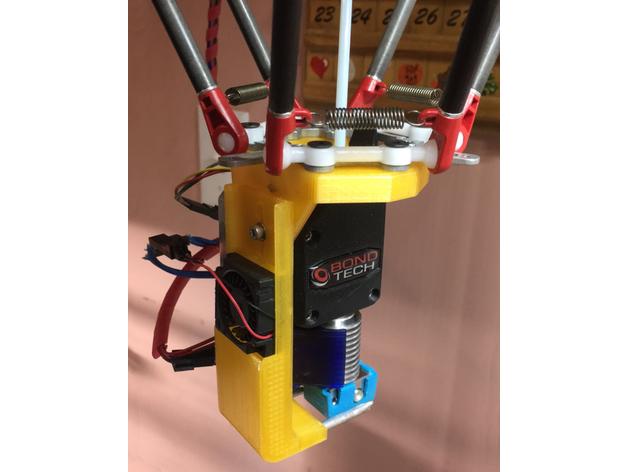
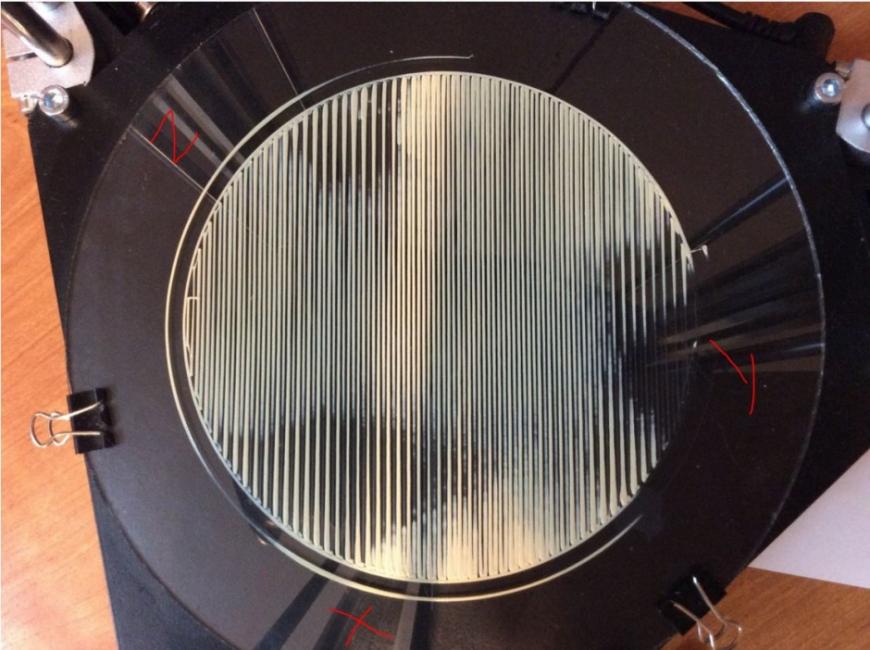
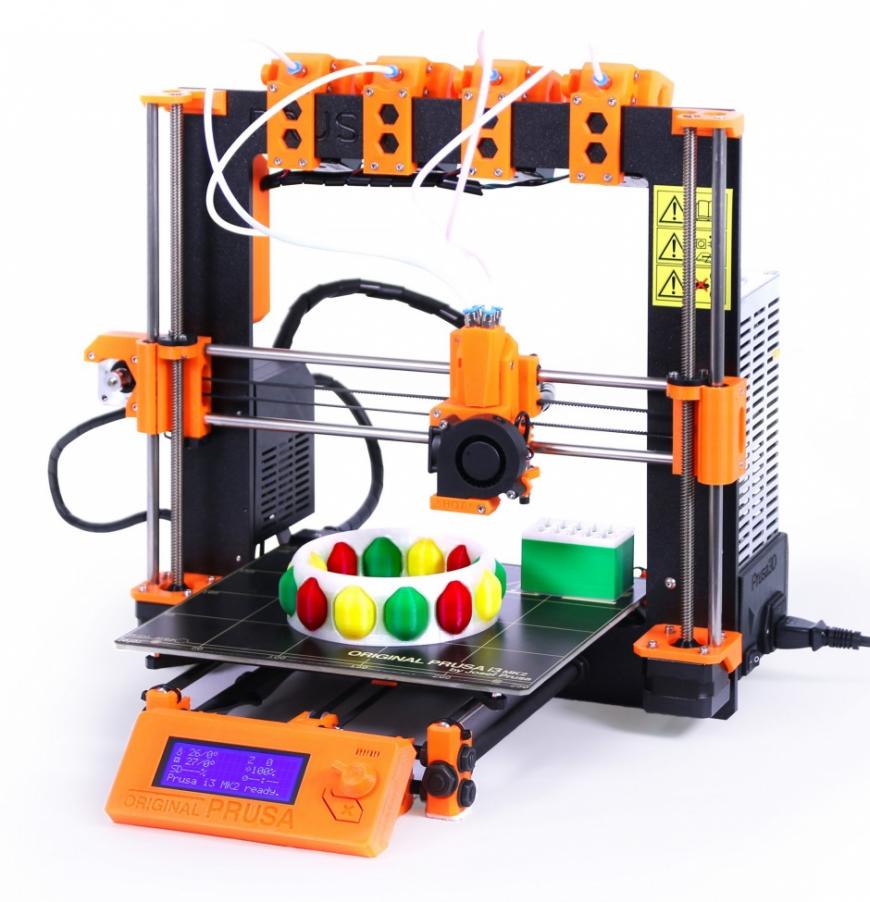
Самодельная рама для 3D принтера. Какую модель выбрать? Чертежи
При разработке своих проектов на Arduino и ЧПУ. Я часто упираюсь в то, что на своем самодельном фрезерном станк е я могу сделать только плоские заготовки. А так часто необходимо сделать изогнутую стенку или сложную объемную деталь. Меня регулярно посещает мысль, что нужен 3D-пинтер. Стоят они не очень дорого. Это вам не Перевезти оргтехнику 20т фурой
В Китае можно купить недорогие 3D принтеры:
3D принтер с доставкой
из России:
Анет A6 3D-принтер
Но как вы знаете я не ищу легких путей и люблю собирать самодельные станки с ЧПУ. Поэтому я решил собрать 3D принтер.
И так цель ясна. Теперь нужно поэтапно реализовывать задуманное. Первое что нужно будет сделать это рама (корпус) 3D принтера, на который будет крепиться вся механика и электроника.
Можно купить готовые варианты рамы , цена относительно небольшая:
Но раз я решил самодельны, значит самодельный. Сперва я планировал собрать самый простой 3D-принтер и выпилить основные части корпуса из фанеры вручную. Что то примерно вот такое:
Но посмотрев размеры раскроя, понял что основные заготовки можно будет вырезать на моем самодельном фрезерном станке с ЧПУ. Чертить с нуля достаточно долго и я загуглил вот что нашел.
1. Первая развертка предназначена для вырезки из стали 3 мм.
Есть несколько версий данного принтера. Выбрать есть из чего. Можно сходить на завод и заказать раскрой из стали или алюминия. Но это выходит в круглую копеечку. На экспрессия можно купить горазда дешевле из альтернативного материала. Конечно из стали получиться достаточно жестко и на века.
Скачать чертежи 3D-принтера P3Steel
2. Вторая версия имеет те же минусы и недостатки. Но макет сделан из МДФ. Поэтому я решил сделать так же из МДФ. Для примера. А потом на основании данного макета модернизировать чертежи под свои материалы. И почестям пересобрать. И тут я нашел третий вариант.
Скачать чертежи 3D-принтера I3 CORDOBESA Full Steel
3.Данная версия рамы 3D принтера уже предназначена для раскроя из фанеры 6 мм.
Это то что я искал. Для первой пробной рамы для 3D-принтера, я думаю будет достаточно. Тем более зная себя точно, что нибудь буду переделывать и модернизировать. А как основная база на первый взгляд неплохой вариант. А как вы считаете?
Скачать чертежи 3D-принтера WoodMAX i3
Если у вас есть варианты рам для 3D принтера пишите в комментарии. Буду благодарен!
Подписывайтесь на мой канал на Youtube и вступайте в группы в Вконтакте и Facebook.
Спасибо за внимание!
Понравилась статья? Поделитесь ею с друзьями:
Самодельный 3д принтер v3.0
Представляю вашему вниманию самодельный 3д принтер. Собран из фанеры, алюминия, пластика и Ардуино. Этот принтер уникален тем, что его кинематика подсмотрена у Ultimaker, но сделана с качественными доработками.
Это уже третий мой 3д принтер, сделанный своими руками. Первый был H-bot, второй D-bot.
С тех пор, когда узнал о 3д печати, я хотел сделать свой принтер, но не особо понимал зачем он мне нужен. Первую деталь я купил ещё в 2015 году, с мыслями о том, что может когда-нибудь я сделаю принтер. За три года незаметно накопилось деталей на cборку и в декабре 2017 я начал процесс. Первая печать произошла только в конце февраля 2018 года. С тех пор я заболел 3д-печатью.
Первый принтер был первым блином, т.е. комом. Это был хороший старт, я приобрёл бесценный опыт и напечатал детали для второго принтера. Второй принтер получился лучше, но всё равно не устраивал меня своими недостатками кинематики.
С самого начала я не ставил себе задачу сделать 3д принтер для ежедневной печати или печати на заказ. Цель: печатать изделия из пластика для собственных нужд. Хочется, конечно, чтобы качество печати было максимальным и при этом цена принтера не должна зашкаливать. Рельсовые направляющие сразу были исключены из сметы из-за цены и сложностей покупки, к тому же они шумные. Круглые линейные подшипники типа LM8UU со временем сгрызают направляющие, поэтому после долгих поисков& выбор пал на 10-ти миллиметровые стальные валы и напечатанные втулки из ABS-пластика.
Я очень давно хотел научиться моделировать свои самоделки в 3D, всё стимула не хватало. Первый принтер я пытался строить в AutoCAD. Уже после нескольких первых распечатанных деталек из пластика, я понял что надо что-то другое. Так я получил пинок изучить SolidWorks. В нём и разрабатывал все последующие модели. Меня очень вдохновила эта программа, потому как чертить очень люблю!
Принтер сначала моделировал на компьютере в 3D с учётом всех деталей. Создание виртуальной модели здорово помогает разработке, многие узлы оптимизируются ещё до их реального воплощения.
Учитывая первый опыт постройки корпуса принтера из ЛДСП, в данной версии я использовал фанеру 10 мм. Все детали были вырезаны на самодельном ЧПУ станке и покрашены белой автомобильной краской.
Пожалуй, самое интересное в этом принтере — кинематика. Я долго присматривался к Ультимейкеру. Подкупало то, что у него оси двигаются жёстко, без перекосов. Позже я узнал и о недостатках. Заключаются они в радиальном вращении направляющих, по которым также двигаются втулки. Залогом качественной печати с таким исполнением кинематики являются дорогие и качественные комплектующие. Меня это не устраивало. Мой принтер должен быть из дешевых и легкодоступных материалов. Вообще самому строить 3д принтер сложно, когда практически все детали приходится заказывать издалека.
При разработке 3д модели нового принтера я разделил вращающиеся и направляющие валы. Так линейное перемещение по осям осуществляется по неподвижным валам 10 мм. Ременная передача организована на отдельных валах диаметром 8 мм. Узлы крепления ремней на подвижных частях сделаны в одной плоскости перемещения осей, чтобы не создавать лишних рычагов, которые, кстати, способствуют износу втулок.
Я поставил задачу иметь возможность быстрой замены любых частей кинематики без необходимости разбирать половину принтера. Также все 4 мотора и электроника принтера вынесены в заднюю часть принтера, чтобы иметь возможность сделать термокамеру для 3д печати и не греть при этом то, что должно быть холодным.
Ось Z сделал из мебельных труб 16 мм и распечатанных из пластика пластин для скольжения. Двигается стол по оси с помощью обычной резьбовой шпильки М8 и муфты. Вращение от мотора передаётся на шпильку через ременную передачу.
Подогреваемый стол состоит из двух частей. Основание из фанеры, оно движется по оси Z. На основание крепится на четырёх винтах М4 и пружинах алюминиевая рамка. В рамку уложен силиконовый коврик, нагреватель и боросиликатное стекло.
Много времени и сил заняла разработка движущейся/печатающей головки, её охлаждение и обдув детали. Пришлось долго вымерять детали, чтобы нигде ничего не задевало во время движения. Для охлаждения я использовал кулеры 40*10 мм. Они работают тихо на низких оборотах и дают хороший поток воздуха. Электроника прикручена на задней стенке. Там же стоит кулер для охлаждения драйверов моторов. Кулер для охлаждения экструдера и кулер для электроники запитаны последовательно и работают в половину мощности, поэтому шум от них очень низкий. Вся электроника запитана от блока питания 12 вольт 25 ампер. Концевики все механические, работают на размыкание.
Термоблок хотэнда я залил термостойким силиконом. Хорошо ли это работает сказать не могу, но что спасает пальцы от ожогов это точно. Никаких других доработок с хотэндом я пока не проводил, всё стандартное.
Подогрев стола осуществляется самодельным нагревателем из текстолита, дорожки просто процарапал резцом под линейку, замучился, лучше бы вытравил. По опыту на каждые 10*10 см стола должно тратиться 2.5 ампера, тогда стол нагревается до 100 градусов очень быстро. Включение нагревателя осуществляется через обычное электромагнитное реле.
На текущий момент 3д принтер не имеет законченного вида, всё на этапе сборки и тестирования. Уже много идей как можно улучшить то, что есть. В целом я очень доволен кинематикой, расположением элементов, корпусом, внешним видом и удобством.
О недостатках и недоработках.
В качестве направляющих должны быть использованы стальные валы. У меня их не было, поэтому попробовал поставить алюминиевые трубки. Первая печать показала, что длинные направляющие гнутся из-за трения втулок и недостаточной жесткости алюминиевых трубок. Замена двух длинных направляющих на сталь немного улучшила ситуацию, но осталась ещё центральная направляющая. Она пока не заменена.
В качестве 8-ми миллиметровых валов для ремней планировал использовать алюминиевые трубки. Они раньше были в продаже, потом пропали. Пришлось использовать шпильки с резьбой, а это дало биение на шкивах, которое передаётся на ремень и, соответственно, влияет на качество печати.
Втулки на движущейся головке я попробовал бронзовые самосмазывающиеся. Пока особо нечего сказать про эти втулки, на принтере всего пару моделек отпечатал. Покупал 10 штук втулок, 4 из них были с люфтом. Я так думаю, что эти втулки предназначены для радиального вращения, вряд ли они годятся для линейного перемещения.
Сейчас принтер печатает плохо, это на 100% зависит от втулок и направляющих, а также от шпильки с метрической резьбой на оси Z. Есть идеи как довести геометрию печати до идеала, но об этом я буду расскажу, когда всё попробую на практике.
Ещё не получилось сделать кинематику быстроразбираемой. В следующей модификации это учту. Поставить моторы на демпферы, чтобы уменьшить шум. Не очень красиво мне удалось сделать разводку с проводами. Не нравится мне длинная трубка от экструдера к хотэнду и не нравится, что она торчит из принтера, сверху планировалась крышка из стекла. Спереди принтер будет закрываться стеклянной дверцей, пока её тоже нет. Сзади электроника будет закрываться пластиковой крышкой с прорезями для движения воздуха.
На передней панели справа четыре выключателя: сеть, свет общий, свет возле хотэнда, отключение обдува детали. Под столом расположена панель с отверстиями для светодиодов и выключателей, это ноухау для отключения неиспользуемых во время печати участков подогрева. Планируется сделать подогрев из нескольких отключаемых нагревателей, это здорово экономит электроэнергию.
Рабочий стол я сделал размером 31*22 см и планировал положить зеркало. Решил попробовать боросиликатное стекло, размер стекла заказал меньший 200*213 мм, поэтому по бокам стола получились пустые места. Печатать на боросиликатном столе без клея не получилось. Пластик совсем не хотел прилипать к этому стеклу, поэтому скорее всего вернусь к использованию зеркала.
Изначально думал, что по бокам корпуса будут окна со стеклянными дверцами. У первого корпуса из ЛДСП были эти окна, но т.к. принтер стоит между стеной и столом, толку от окошек нет. Поэтому стенки остались целыми, внутри на этих стенках будет крепление для катушки с пластиком.
Кто-то заметил, тут нет экрана с элементами управления. Поставить экран можно. Я сознательно отказался от него, т.к. просто управляю с компьютера. Необходимости печатать с флешки у меня не было и вряд ли предвидится.
На этом пока всё. А чём умолчал, отвечу в комментариях. Принтер пока отпечатал всего пару котиков на скорости 100 мм/сек. Дочь котикам несказанно рада, значит работа проделана на пользу. Есть целый список из нескольких десятков моделей, которые очень хочется распечатать в хорошем качестве. Впереди много интересных доработок, будет интересно. Всем добра!