ΠΠΎΠΆ ΠΈΠ· ΠΎΠ±ΠΎΠΉΠΌΡ ΠΏΠΎΠ΄ΡΠΈΠΏΠ½ΠΈΠΊΠ°, Π²Π°ΡΠΈΠ°Π½Ρ 1

ΠΡΠ΅ΠΌ Π·Π΄ΡΠ°Π²ΡΡΠ²ΡΠΉΡΠ΅ Π² ΠΊΡΡΠ΅ ΠΌΠ΅ΡΠ°Π»Π»ΠΈΡΠ΅ΡΠΊΠΎΠ³ΠΎ Ρ Π»Π°ΠΌΠ° Π½Π°ΡΠ΅Π» 4 ΠΊΡΡΠΊΠ° ΠΎΡ ΠΎΠ±ΠΎΠΉΠΌΡ ΠΏΠΎΠ΄ΡΠΈΠΏΠ½ΠΈΠΊΠ° ΠΈ ΡΠ΅ΡΠΈΠ» ΡΠ΄Π΅Π»Π°ΡΡ ΠΈΠ· Π½ΠΈΡ 4 Π½Π΅Π±ΠΎΠ»ΡΡΠΈΡ Π½ΠΎΠΆΠ°. Π‘ΡΠ°Π»Ρ ΠΏΠΎΠ΄ΡΠΈΠΏΠ½ΠΈΠΊΠ° Π² ΠΎΡΠ½ΠΎΠ²Π½ΠΎΠΌ ΠΈΠ· Π¨Π₯10, Π¨Π₯15, Π° ΠΏΠΎΠ΄ΡΠΈΠΏΠ½ΠΈΠΊ Π΄ΠΈΠ°ΠΌΠ΅ΡΡΠΎΠΌ ΠΎΡ 200 ΠΌΠΌ ΠΈΠ· Π¨Π₯20. Π£ ΠΌΠ΅Π½Ρ ΠΏΠΎΠ΄ΡΠΈΠΏΠ½ΠΈΠΊ ΠΈΠ· Π¨Π₯15.
Π£ΠΆΠ΅ Π½ΠΈ ΠΎΠ΄ΠΈΠ½ Π½ΠΎΠΆ Π΄Π΅Π»Π°Π» ΠΈΠ· ΠΏΠΎΠ΄ΡΠΈΠΏΠ½ΠΈΠΊΠΎΠ² ΡΠ°Π·Π½ΠΎΠ³ΠΎ Π΄ΠΈΠ°ΠΌΠ΅ΡΡΠ° ΠΈΠ· ΡΠ°Π·Π½ΡΡ ΡΡΠ°Π»Π΅ΠΉ, ΡΠ°ΠΊ ΡΡΠΎ Π΄ΡΠΌΠ°Ρ Π·Π°ΡΡΡΠ΄Π½Π΅Π½ΠΈΠΉ Π½Π΅ Π±ΡΠ΄Π΅Ρ. ΠΠ»Π°Π²Π½ΠΎΠ΅ ΠΏΡΠ°Π²ΠΈΠ»ΠΎ ΠΊΠΎΠ²ΠΊΠΈ Π½ΠΎΠΆΠ° ΠΈΠ· ΠΏΠΎΠ΄ΡΠΈΠΏΠ½ΠΈΠΊΠ° — ΡΡΠΎ ΡΠ΅ΠΌΠΏΠ΅ΡΠ°ΡΡΡΠ° Π½Π°Π³ΡΠ΅Π²Π° Π·Π°Π³ΠΎΡΠΎΠ²ΠΊΠΈ, Π²Π΅Π΄Ρ ΡΡΠ° ΡΡΠ°Π»Ρ Π½Π΅ Π»ΡΠ±ΠΈΡ ΠΏΠ΅ΡΠ΅Π³ΡΠ΅Π²Π°, ΠΈ ΠΏΠΎ ΡΡΠΎΠΌΡ Ρ Π»ΡΡΡΠ΅ Π½Π΅ Π΄ΠΎ Π³ΡΠ΅Ρ ΡΠ΅ΠΌ, ΠΏΠ΅ΡΠ΅Π³ΡΠ΅Ρ ΡΡΠ°Π»Ρ.
ΠΠ°Π³ΡΠ΅Π²Π°Ρ Π΄ΠΎ Π²ΠΈΡΠ½Π΅Π²ΠΎΠ³ΠΎ ΡΠ²Π΅ΡΠ° ΠΈ Π½Π°ΡΠΈΠ½Π°Ρ ΠΊΠΎΠ²Π°ΡΡ ΠΏΡΠΈ Π½Π°Π½Π΅ΡΠ΅Π½ΠΈΠΈ ΡΠ΄Π°ΡΠ°, Π΅ΡΠ»ΠΈ ΡΡΠ²ΡΡΠ²ΡΡ, ΡΡΠΎ ΡΡΠ°Π»Ρ ΡΡΠ°Π½ΠΎΠ²ΠΈΡΡΡ ΡΠΏΡΡΠ³ΠΎΠΉ, ΡΠΎ ΡΡΠ°Π·Ρ ΠΆΠ΅ Π½Π΅ΠΌΠ½ΠΎΠ³ΠΎ ΠΏΠΎΠ΄ΠΎΠ³ΡΠ΅Π²Π°Ρ Π·Π°Π³ΠΎΡΠΎΠ²ΠΊΡ ΠΈ ΠΏΡΠΎΠ΄ΠΎΠ»ΠΆΠ°Ρ ΠΊΠΎΠ²Π°ΡΡ. ΠΠΎΡ ΠΈ Π²ΡΠ΅ Ρ ΡΠ΅ΠΎΡΠΈΠ΅ΠΉ, ΠΏΡΠΈΡΡΡΠΏΠ°Ρ ΠΊ ΠΊΠΎΠ²ΠΊΠ΅ Π½ΠΎΠΆΠ° ΠΈΠ· ΠΎΠ±ΠΎΠΉΠΌΡ ΠΏΠΎΠ΄ΡΠΈΠΏΠ½ΠΈΠΊΠ°.
ΠΠΎΡΠ»Π΅ ΠΎΠ±ΠΆΠΈΠ³Π° Π·Π°Π³ΠΎΡΠΎΠ²ΠΊΠΈ Π½Π°ΡΠΈΠ½Π°Ρ Π²ΡΠΏΡΡΠΌΠ»ΡΡΡ Π½Π° Π½Π°ΠΊΠΎΠ²Π°Π»ΡΠ½Π΅, ΠΏΠΎΡΠ»Π΅ Π²ΡΡΠ°Π²Π½ΠΈΠ²Π°Π½ΠΈΡ Π½Π°Π³ΡΠ΅Π²Π°Ρ Π΄ΠΎ Π²ΠΈΡΠ½ΡΠ²ΠΎΠ³ΠΎ ΡΠ²Π΅ΡΠ° ΠΈ Π½Π°ΡΠΈΠ½Π°Ρ ΠΊΠΎΠ²Π°ΡΡ Π»Π΅Π·Π²ΠΈΠ΅ Π½ΠΎΠΆΠ°, Π½Π°Π½ΠΎΡΡ ΡΠΊΠΎΠ»ΡΠ·ΠΊΠΈΠ΅ ΡΠ΄Π°ΡΡ, Π²ΡΡΡΠ³ΠΈΠ²Π°Ρ ΠΎΡ ΠΎΠ±ΡΡ
Π°, Π½ΠΎ Π»Π΅Π·Π²ΠΈΡ Π½ΠΎΠΆΠ°. ΠΠ°Π³ΡΠ΅Π²Π°ΡΡ Π½ΡΠΆΠ½ΠΎ Π°ΠΊΠΊΡΡΠ°ΡΠ½ΠΎ, ΡΡΠΎΠ±Ρ Π½Π΅ ΠΏΠ΅ΡΠ΅Π³ΡΠ΅ΡΡ ΠΌΠ΅ΡΠ°Π»Π», ΠΈΠ½Π°ΡΠ΅ Π²ΡΠ΅ ΠΈΡΠΏΠΎΡΡΠΈΠΌ.
ΠΠΎΡΠ»Π΅ Π²ΡΡΡΠΆΠΊΠΈ Π»Π΅Π·Π²ΠΈΠ΅ Π½Π° ΠΎΠ±ΡΡ Π΅ 2 ΠΌΠΌ, Π° Π½Π° ΠΎΡΡΡΠΈΠ΅ 1 ΠΌΠΌ Ρ ΠΊΠΎΠ²Π°Π» Π»Π΅Π·Π²ΠΈΠ΅ ΡΡΠ°Π·Ρ Π² Π³ΠΎΡΠΎΠ²ΡΠΉ Π²ΠΈΠ΄ ΡΠ°ΠΊ, ΡΡΠΎ ΠΏΠΎΡΠ»Π΅ ΠΊΠΎΠ²ΠΊΠΈ Π±ΡΠ΄Ρ ΡΡΠ°Π·Ρ Π·Π°ΠΊΠ°Π»ΠΈΠ²Π°ΡΡ Π½ΠΎΠΆ.
ΠΠΎΡΠ»Π΅ ΠΊΠΎΠ²ΠΊΠΈ Π»Π΅Π·Π²ΠΈΡ ΠΏΡΠΈΡΡΡΠΏΠ°Ρ ΠΊ ΡΠΎΡΠΌΠΈΡΠΎΠ²ΠΊΠ΅ Ρ Π²ΠΎΡΡΠΎΠ²ΠΈΠΊΠ°, ΡΡΡΠΊΡ Π½ΠΎΠΆΠ° Ρ ΡΠ΅ΡΠΈΠ» ΡΠ΄Π΅Π»Π°ΡΡ Π΄Π΅ΠΊΠΎΡΠ°ΡΠΈΠ²Π½ΡΡ ΠΊΠΎΠ²Π°Π½ΡΡ ΡΡΡΠΊΡ. ΠΠ°Π³ΡΠ΅Π²Π°Ρ ΠΈ Π½Π°ΡΠΈΠ½Π°Ρ ΠΊΠΎΠ²Π°ΡΡ Ρ Π²ΠΎΡΡΠΎΠ²ΠΈΠΊ ΡΠΎΡΠΌΠΎΠΉ ΠΊΠ²Π°Π΄ΡΠ°ΡΠ°. ΠΠΎΡΠ»Π΅ 3 ΠΈΠ»ΠΈ 4βΡ Π½Π°Π³ΡΠ΅Π²ΠΎΠ² Π²ΡΡΡΠ³ΠΈΠ²Π°Ρ Ρ Π²ΠΎΡΡΠΎΠ²ΠΈΠΊ Π΄ΠΎ Π½ΡΠΆΠ½ΠΎΠΉ Π΄Π»ΠΈΠ½Ρ. ΠΠ°Π³ΡΠ΅Π²Π°Ρ Π΅ΡΠ΅ ΡΠ°Π·, Π΄Π°Π»Π΅Π΅ Π·Π°ΠΆΠΈΠΌΠ°Ρ Π² ΡΠΈΡΠΊΠ°Ρ , ΠΈ Π΄Π΅ΡΠΆΠ°Π² Π·Π° Ρ Π²ΠΎΡΡΠΎΠ²ΠΈΠΊ, Π½Π°ΡΠΈΠ½Π°Ρ Π·Π°ΠΊΡΡΡΠΈΠ²Π°ΡΡ ΠΈ Π·Π° Π΄Π²Π° ΡΠ°Π·Π° Π·Π°ΠΊΡΡΡΠΈΠ²Π°Ρ, ΠΊΠ°ΠΊ Π½ΡΠΆΠ½ΠΎ ΠΌΠ½Π΅. ΠΠ°Π³ΡΠ΅Π²Π°Ρ, Π° Π·Π°ΡΠ΅ΠΌ Π·Π°Π³ΠΈΠ±Π°Ρ ΡΡΡΠΊΡ ΠΏΠΎΠ΄ ΡΠ΄ΠΎΠ±Π½ΡΠΉ Ρ Π²Π°Ρ, Π²ΠΎΡ ΠΈ Π²ΡΠ΅ Ρ ΠΊΠΎΠ²ΠΊΠΎΠΉ.
Π’Π΅ΠΏΠ΅ΡΡ ΠΌΠΎΠΆΠ½ΠΎ ΠΈ Π·Π°ΠΊΠ°Π»ΠΈΠ²Π°ΡΡ Π½ΠΎΠΆ. ΠΠ°Π³ΡΠ΅Π²Π°Ρ Π΄ΠΎ ΡΠΎΠ³ΠΎ ΠΌΠΎΠΌΠ΅Π½ΡΠ° ΠΏΠΎΠΊΠ° ΠΌΠ°Π³Π½ΠΈΡ Π½Π΅ ΠΏΠ΅ΡΠ΅ΡΡΠ°Π½Π΅Ρ ΠΏΡΠΈΠ»ΠΈΠΏΠ°ΡΡ ΠΊ Π½ΠΎΠΆΡ, ΠΈ ΠΎΠΊΡΠ½Π°Ρ Π² ΠΏΠΎΠ΄ΠΎΠ³ΡΠ΅ΡΠΎΠ΅ ΠΌΠΈΠ½Π΅ΡΠ°Π»ΡΠ½ΠΎΠ΅ Π°Π²ΡΠΎΠΌΠ°ΡΠ»ΠΎ. ΠΠΎΡΠ»Π΅ Π·Π°ΠΊΠ°Π»ΠΊΠΈ ΠΎΡΡΠ°Π²Π»ΡΡ Π½Π° Π²ΡΠΊΠ»ΡΡΠ΅Π½Π½ΠΎΠΌ Π³ΠΎΡΠ½Π΅, ΠΏΡΡΡΡ ΠΎΡΡΡΠ²Π°Π΅Ρ Π±ΡΠ΄Π΅Ρ ΠΊΠ°ΠΊ ΠΎΡΠΏΡΡΠΊ. ΠΠΎΡ ΠΈ Π²ΡΠ΅ ΡΠ΅ΠΏΠ΅ΡΡ ΠΏΡΠΈΡΡΡΠΏΠ°Ρ ΠΊ ΡΠ»Π΅ΡΠ°ΡΠΊΠ΅.
Π ΡΡΠΊΡ ΡΠ΅ΡΠΈΠ» ΠΎΡΡΠ°Π²ΠΈΡΡ ΠΊΠ°ΠΊ Π΅ΡΡΡ, ΡΡΠΎΠ±Ρ Π²ΠΈΠ΄Π½ΠΎ Π±ΡΠ»ΠΎ ΠΊΠΎΠ²ΠΊΡ. ΠΠ° ΠΡΠΈΠ½Π΄Π΅ΡΠ΅, Π½Π° 120 Π±ΡΠΌΠ°Π³Π΅, ΡΠ»ΠΈΡΡΡ ΡΡΡΠΊΡ Π΄ΠΎ ΠΌΠ°Π»ΠΎΠ·Π°ΠΌΠ΅ΡΠ½ΡΡ ΡΠΈΡΠΎΠΊ. ΠΠ°Π»Π΅Π΅ Π½Π° ΡΡΠ°Π½ΠΊΠ΅ ΡΠΎΡΠΌΠΈΡΡΡ ΡΠΎΡΠΌΡ ΠΊΠ»ΠΈΠ½ΠΊΠ° ΠΏΠΎ ΡΠ°Π±Π»ΠΎΠ½Ρ. ΠΠ΅ΡΠ°Π»Π» Π±Π΅ΡΠ΅ΡΡΡ ΡΡΠΆΠ΅Π»ΠΎ, Π½ΠΎ ΡΠΏΠ°ΡΠ°Π΅Ρ ΡΡΠΎ ΠΊΠ»ΠΈΠ½ΠΎΠΊ Π½ΡΠΆΠ½ΠΎ ΠΏΡΠΎΡΡΠΎ ΠΎΡΡΠ»ΠΈΡΠΎΠ²Π°ΡΡ, Π²Π΅Π΄Ρ Ρ ΡΡΠ°Π·Ρ ΠΎΡΠΊΠΎΠ²Π°Π» Π½ΡΠΆΠ½ΡΡ ΡΠΎΠ»ΡΠΈΠ½Ρ. Π‘ΠΏΡΡΡΡ ΠΏΠΎΠ» ΡΠ°ΡΠ° Ρ Π½Π°ΠΊΠΎΠ½Π΅Ρ-ΡΠΎ Π·Π°ΠΊΠΎΠ½ΡΠΈΠ» ΡΠ»ΠΈΡΠΎΠ²Π°ΡΡ Π½Π° ΡΡΠ°Π½ΠΊΠ΅. ΠΠ°ΠΆΠΈΠΌΠ°Ρ Π½ΠΎΠΆ ΡΡΡΡΠ±ΡΠΈΠ½ΠΎΠΉ ΠΈ ΡΠ»ΠΈΡΡΡ Π²ΡΡΡΠ½ΡΡ. Π ΡΠΎΠΆΠ°Π»Π΅Π½ΠΈΡ Ρ ΠΌΠ΅Π½Ρ Π½Π΅Ρ ΠΌΠ΅Π»ΠΊΠΎΠΉ Π±ΡΠΌΠ°Π³ΠΈ, ΠΎΡΡΠ°Π»ΠΎΡΡ ΡΠΎΠ»ΡΠΊΠΎ 60, 100 ΠΈ 120, Π° Π΅ΡΠ΅ 400ΠΊΠ° ΡΠ°ΠΊ, ΡΡΠΎ Π΄ΠΎ Π±Π»Π΅ΡΠΊΠ° ΠΏΠΎΠΊΠ° Π½Π΅ ΠΏΠΎΠ»ΡΡΠΈΡΡΡ ΠΎΡΡΠ»ΠΈΡΠΎΠ²Π°ΡΡ. Π ΡΡΠ°Π²ΠΈΡΡ Π² ΠΊΠΈΡΠ»ΠΎΡΠ΅ Π½Π΅ ΠΎΡ ΠΎΡΠ°. ΠΠΎΡ ΠΈ Π²ΡΠ΅ Π½ΠΎΠΆ Π³ΠΎΡΠΎΠ².
ΠΠ»ΠΈΠ½Π° ΠΎΡ ΠΊΠΎΠ½ΡΠΈΠΊΠ° Π΄ΠΎ ΠΊΠΎΠ½ΡΠ° ΡΡΠΊΠΎΡΡΠΈ 185 ΠΌΠΌ, Π΄Π»ΠΈΠ½Π° ΠΊΠ»ΠΈΠ½ΠΊΠ° 103 ΠΌΠΌ. ΠΠΎΠΆ ΠΏΠΎΠ»ΡΡΠΈΠ»ΡΡ Π½Π΅Π±ΠΎΠ»ΡΡΠΈΠΌ, Π½ΠΎ ΡΠ΄ΠΎΠ±Π½ΡΠΌ.
ΠΠ΅ΠΊΠΎΡΠΎΡΡΠ΅ ΡΠ΅ΠΉΡΠ°Ρ Π±ΡΠ΄ΡΡ ΡΡΠΎΠ»ΠΈΡΡ, ΡΠΈΠΏΠ° ΡΡΡΠ°ΡΠ½ΡΠΉ ΠΈ ΠΈΠ· ΡΡΠ°Π»ΠΈ Π³ΠΎ.., Π° ΡΠΊΠ°ΠΆΡ ΡΠ°ΠΊ, ΡΡΠΎ ΡΠ΅Π»ΠΎΠ²Π΅ΠΊ ΠΎΡ ΠΎΠ±Π΅Π·ΡΡΠ½Ρ ΠΎΡΠ»ΠΈΡΠ°Π΅ΡΡΡ ΡΠ΅ΠΌ, ΡΡΠΎ ΠΎΠ½ Ρ ΠΎΡΡ Π±Ρ ΡΡΠΎ-ΡΠΎ Π΄Π΅Π»Π°ΡΡ ΡΡΠ°ΡΠ°Π΅ΡΡΡ, Π° Π½Π΅ Π»Π΅ΠΆΠΈΡ Π½Π° Π΄ΠΈΠ²Π°Π½Π΅ ΠΈ ΡΡΡΠΎΡΠΈΡ Π½Π΅ΠΊΡΠ°ΡΠΈΠ²ΡΠΉ ΠΊΠΎΠΌΠΌΠ΅Π½ΡΠ°ΡΠΈΠΉ, ΡΠΈΠΏΠ° Ρ Π»ΡΡΡΠ΅ ΠΌΠΎΠ³Ρ, ΠΊ ΡΡΠ°ΡΡΡΡ Π΄Π°ΠΆΠ΅ ΡΠ°ΠΊΠΈΠ΅ ΠΊΠΎΠΌΠΌΠ΅Π½ΡΠ°ΡΠΈΠΈ ΠΏΡΠΈΠ½ΠΎΡΡΡ 0.5 ΠΌΠΎΠ½Π΅Ρ Ρ ΠΎΡΡ Π½Π΅ΠΌΠ½ΠΎΠ³ΠΎ ΠΏΠΎΠ»ΡΠ·Π°.
Π‘ΡΠ°Π»Ρ Π¨Π₯15 — Π΄Π° Π½Π΅ ΡΠΏΠΎΡΡ Π½Π΅ ΠΈΠ· Π»ΡΡΡΠΈΡ , Π½ΠΎ ΡΡΡ ΠΌΠ°ΡΠΊΡ ΡΡΠ°Π»ΠΈ ΠΌΠΎΠΆΠ½ΠΎ Π½Π°ΠΉΡΠΈ Ρ ΠΎΡΡ Π³Π΄Π΅ Π΄Π°ΠΆΠ΅ ΠΏΠΎΠ΄ Π΄ΠΈΠ²Π°Π½ΠΎΠΌ, Π½ΠΎ Ρ Π½Π΅Π΅ Π΅ΡΡΡ ΠΈ ΡΠ²ΠΎΠΈ ΠΏΠ»ΡΡΡ Π΅ΡΠ»ΠΈ Π½Π΅ ΠΏΠ΅ΡΠ΅Π³ΡΠ΅Π²Π°ΡΡ Π΅Π΅, ΡΠΎ ΠΎΠ½Π° ΠΌΠ΅Π½Π΅Π΅ ΠΏΠΎΠ΄Π΄Π°Π΅ΡΡΡ ΡΠΆΠ°Π²ΡΠΈΠ½Π΅, Π½ΠΎ Π½ΡΠΆΠ½ΠΎ Π½Π΅ Π·Π°Π±ΡΠ²Π°ΡΡ ΡΡΠΎ Π»ΡΠ±ΠΎΠΉ Π½ΠΎΠΆ ΡΡΠ΅Π±ΡΠ΅Ρ ΡΡ ΠΎΠ΄Π°.
ΠΠΎΡ ΠΈ Π²ΡΠ΅ ΠΌΠΎΡ ΡΡΠ°ΡΡΡ ΠΏΠΎΠ΄ΠΎΡΠ»Π° ΠΊ ΠΊΠΎΠ½ΡΡ. ΠΡΠ±Π°Ρ Π²Π΅ΡΡ, ΡΠ΄Π΅Π»Π°Π½Π½Π°Ρ ΡΠ²ΠΎΠΈΠΌΠΈ ΡΡΠΊΠ°ΠΌΠΈ, Π»ΡΡΡΠ΅ ΡΠ΅ΠΌ ΡΡΠ°Π·Π° Ρ ΠΌΠΎΠ³Ρ Π»ΡΡΡΠ΅. ΠΡΠ΅ΠΌ ΡΠΏΠ°ΡΠΈΠ±ΠΎ ΠΈ Π΄ΠΎ Π½ΠΎΠ²ΡΡ
Π‘Π°ΠΌΠΎΠ΄Π΅Π»ΠΎΠΊ Π΄ΡΡΠ·ΡΡ.




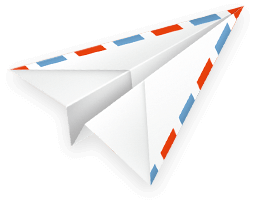
ΠΠΎΠ»ΡΡΠ°ΠΉΡΠ΅ Π½Π° ΠΏΠΎΡΡΡ ΠΏΠΎΠ΄Π±ΠΎΡΠΊΡ Π½ΠΎΠ²ΡΡ ΡΠ°ΠΌΠΎΠ΄Π΅Π»ΠΎΠΊ. ΠΠΈΠΊΠ°ΠΊΠΎΠ³ΠΎ ΡΠΏΠ°ΠΌΠ°, ΡΠΎΠ»ΡΠΊΠΎ ΠΏΠΎΠ»Π΅Π·Π½ΡΠ΅ ΠΈΠ΄Π΅ΠΈ!
*ΠΠ°ΠΏΠΎΠ»Π½ΡΡ ΡΠΎΡΠΌΡ Π²Ρ ΡΠΎΠ³Π»Π°ΡΠ°Π΅ΡΠ΅ΡΡ Π½Π° ΠΎΠ±ΡΠ°Π±ΠΎΡΠΊΡ ΠΏΠ΅ΡΡΠΎΠ½Π°Π»ΡΠ½ΡΡ Π΄Π°Π½Π½ΡΡ
Π‘ΡΠ°Π½ΠΎΠ²ΠΈΡΠ΅ΡΡ Π°Π²ΡΠΎΡΠΎΠΌ ΡΠ°ΠΉΡΠ°, ΠΏΡΠ±Π»ΠΈΠΊΡΠΉΡΠ΅ ΡΠΎΠ±ΡΡΠ²Π΅Π½Π½ΡΠ΅ ΡΡΠ°ΡΡΠΈ, ΠΎΠΏΠΈΡΠ°Π½ΠΈΡ ΡΠ°ΠΌΠΎΠ΄Π΅Π»ΠΎΠΊ Ρ ΠΎΠΏΠ»Π°ΡΠΎΠΉ Π·Π° ΡΠ΅ΠΊΡΡ. ΠΠΎΠ΄ΡΠΎΠ±Π½Π΅Π΅ Π·Π΄Π΅ΡΡ.ΠΠ΅Π»Π°Π΅ΠΌ Π½ΠΎΠΆ ΠΈΠ· ΠΎΠ±ΠΎΠΉΠΌΡ ΠΏΠΎΠ΄ΡΠΈΠΏΠ½ΠΈΠΊΠ° ΡΠ²ΠΎΠΈΠΌΠΈ ΡΡΠΊΠ°ΠΌΠΈ
ΠΡΠΎΡ ΠΏΠΎΡΡ ΠΌΠΎΠΆΠ΅Ρ ΡΠΎΠ΄Π΅ΡΠΆΠ°ΡΡ ΠΏΠ°ΡΡΠ½Π΅ΡΡΠΊΠΈΠ΅ ΡΡΡΠ»ΠΊΠΈ. ΠΡΠΎ ΠΎΠ·Π½Π°ΡΠ°Π΅Ρ, ΡΡΠΎ Ρ Π·Π°ΡΠ°Π±Π°ΡΡΠ²Π°Ρ Π½Π΅Π±ΠΎΠ»ΡΡΡΡ ΠΊΠΎΠΌΠΈΡΡΠΈΡ Π·Π° ΡΡΡΠ»ΠΊΠΈ, ΠΈΡΠΏΠΎΠ»ΡΠ·ΡΠ΅ΠΌΡΠ΅ Π±Π΅Π· ΠΊΠ°ΠΊΠΈΡ -Π»ΠΈΠ±ΠΎ Π΄ΠΎΠΏΠΎΠ»Π½ΠΈΡΠ΅Π»ΡΠ½ΡΡ Π·Π°ΡΡΠ°Ρ Π΄Π»Ρ Π²Π°Ρ. ΠΠΎΠΏΠΎΠ»Π½ΠΈΡΠ΅Π»ΡΠ½ΡΡ ΠΈΠ½ΡΠΎΡΠΌΠ°ΡΠΈΡ ΡΠΌΠΎΡΡΠΈΡΠ΅ Π² ΠΌΠΎΠ΅ΠΉ ΠΏΠΎΠ»ΠΈΡΠΈΠΊΠ΅ ΠΊΠΎΠ½ΡΠΈΠ΄Π΅Π½ΡΠΈΠ°Π»ΡΠ½ΠΎΡΡΠΈ.
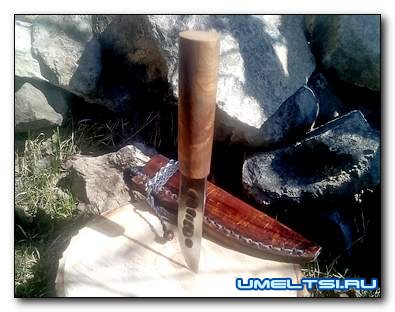
ΠΠΎΠΆ ΠΈΠ· ΠΏΠΎΠ΄ΡΠΈΠΏΠ½ΠΈΠΊΠ° Π΄Π΅Π»Π°Π΅ΡΡΡ Π² Π΄ΠΎΡΡΠ°ΡΠΎΡΠ½ΠΎ ΠΊΡΠΎΠΏΠΎΡΠ»ΠΈΠ²ΡΠΉ ΡΠΏΠΎΡΠΎΠ±. ΠΡΠ»ΠΈ Π΄Π»Ρ ΠΈΠ·Π³ΠΎΡΠΎΠ²Π»Π΅Π½ΠΈΡ ΡΠ°ΠΌΠΎΠ΄Π΅Π»ΡΠ½ΠΎΠ³ΠΎ Π½ΠΎΠΆΠ° ΠΈΠ· ΡΠ΅ΡΡΠΎΡΡ ΠΌΠΎΠΆΠ½ΠΎ ΠΈΡΠΏΠΎΠ»ΡΠ·ΠΎΠ²Π°ΡΡ ΠΌΠ΅ΡΠΎΠ΄ ΠΎΡΠΏΡΡΠΊΠ°, ΠΌΠ΅Ρ Π°Π½ΠΈΡΠ΅ΡΠΊΡΡ ΠΎΠ±ΡΠ°Π±ΠΎΡΠΊΡ ΠΌΠ΅ΡΠ°Π»Π»Π° ΠΈ ΠΏΠΎΡΠ»Π΅Π΄ΡΡΡΡΡ Π·Π°ΠΊΠ°Π»ΠΊΡ, ΡΠΎ Π½ΠΎΠΆ ΠΈΠ· ΠΏΠΎΠ΄ΡΠΈΠΏΠ½ΠΈΠΊΠ° ΠΏΠΎΠ»ΡΡΠΈΡΡΡ ΡΠΎΠ»ΡΠΊΠΎ ΠΏΡΡΠ΅ΠΌ ΠΊΠΎΠ²ΠΊΠΈ.
ΠΡΠΎΠ±Π΅Π½Π½ΠΎΡΡΡ ΡΡΠΎΠ³ΠΎ ΠΏΡΠΎΡΠ΅ΡΡΠ° ΡΠΎΡΡΠΎΠΈΡ Π² ΡΠΎΠΌ, ΡΡΠΎ ΠΏΠΎΠ΄ΡΠΈΠΏΠ½ΠΈΠΊ ΠΈΠΌΠ΅Π΅Ρ ΠΊΡΡΠ³Π»ΡΡ ΠΎΠ±ΠΎΠΉΠΌΡ, Π° Π΄Π»Ρ ΡΠ°ΡΠΏΡΡΠΌΠ»Π΅Π½ΠΈΡ Π΅Π΅ Π½Π° ΠΌΠ΅ΡΠ°Π»Π»ΠΈΡΠ΅ΡΠΊΡΡ ΠΏΠΎΠ»ΠΎΡΠΊΡ ΠΏΠΎΠ΄ΠΎΠΉΠ΄Π΅Ρ ΡΠΎΠ»ΡΠΊΠΎ Π»ΠΈΡΡ ΠΎΠ΄ΠΈΠ½ Π²Π°ΡΠΈΠ°Π½Ρ β ΡΠΊΠΎΠ²Π°ΡΡ.
ΠΠΎΠ²ΠΊΠ° Π½ΠΎΠΆΠ° ΠΈΠ· ΠΏΠΎΠ΄ΡΠΈΠΏΠ½ΠΈΠΊΠ°
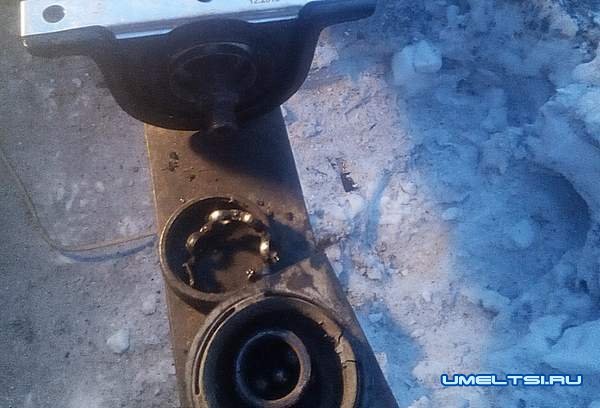
Π Π°ΡΠΏΠΈΠ»ΠΈΠ²Π°ΡΡ ΠΏΠΎΠ΄ΡΠΈΠΏΠ½ΠΈΠΊ ΡΠ΅ΠΊΠΎΠΌΠ΅Π½Π΄ΡΠ΅ΡΡΡ Π½Π°ΠΈΡΠΊΠΎΡΠΎΠΊ β ΠΊΠΎΠ³Π΄Π° Π±ΡΠ΄Π΅ΠΌ ΠΊΠΎΠ²Π°ΡΡ, Π½ΠΎΡΠΈΠΊ ΡΠΌΠΎΠΆΠ΅ΠΌ ΡΡΠΎΡΠΌΠΈΡΠΎΠ²Π°ΡΡ Π² Π±ΠΎΠ»Π΅Π΅ Π»Π΅Π³ΠΊΠΈΠΉ ΡΠΏΠΎΡΠΎΠ±.
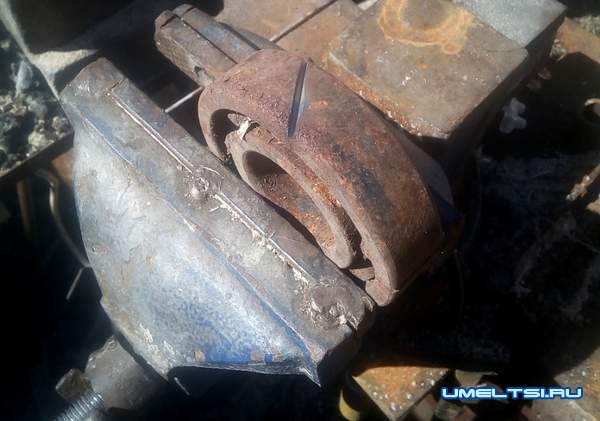
ΠΠ²ΡΠΎΡ ΠΈΡΠΏΠΎΠ»ΡΠ·ΠΎΠ²Π°Π» ΡΠΏΠ»Π°Π² Π¨Ρ 15 β ΡΡΠΎ ΡΡΠ°Π»Ρ, ΠΊΠΎΡΠΎΡΠ°Ρ Π»Π΅Π³ΠΈΡΠΎΠ²Π°Π½Π° Ρ ΡΠΎΠΌΠΎΠΌ. ΠΠ΅ΡΠ΅Π΄ ΡΠ΅ΠΌ, ΠΊΠ°ΠΊ ΠΏΡΠΈΡΡΡΠΏΠ°ΡΡ ΠΊ ΠΊΠΎΠ²ΠΊΠ΅, ΡΠΏΠ»Π°Π² ΠΎΡΠΆΠΈΠ³Π°Π΅ΠΌ, ΠΎΡΡΠ°Π²Π»ΡΠ΅ΠΌ Π² ΠΏΠ΅ΡΠΈ ΠΈΠ»ΠΈ Π³ΠΎΡΠ½Π΅, ΡΡΠΎΠ±Ρ ΠΌΠ΅Π΄Π»Π΅Π½Π½ΠΎ ΠΎΡΡΡΠ» β ΠΏΡΠΈΠΌΠ΅ΡΠ½ΠΎ 20β60 Π³ΡΠ°Π΄ΡΡΠΎΠ² Π² ΡΠ°Ρ. ΠΠΎ ΠΎΡΠΆΠΈΠ³Ρ ΡΡΠ°Π»Ρ ΠΏΡΠΈΠΎΠ±ΡΠ΅ΡΠ°Π΅Ρ ΠΏΠ»Π°ΡΡΠΈΡΠ½ΠΎΡΡΡ, ΡΠ΅ΠΏΠ΅ΡΡ Π΅Π΅ ΠΊΠΎΠ²Π°ΡΡ ΡΠ΄ΠΎΠ±Π½Π΅Π΅.
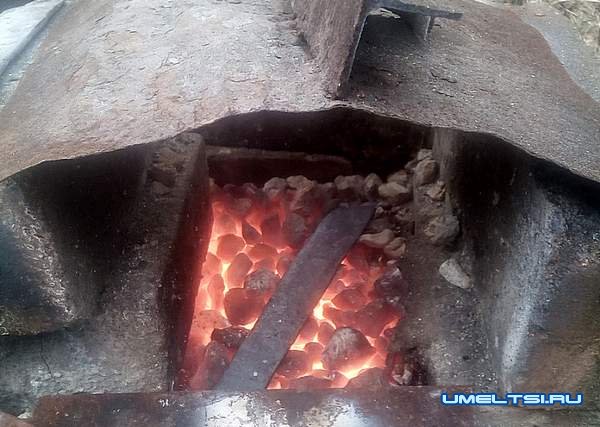
ΠΠ±ΠΎΠΉΠΌΡ Π²ΡΠΏΡΡΠΌΠ»ΡΠ΅ΠΌ, ΡΠΎΡΠΌΠΈΡΡΠ΅ΠΌ ΠΊΠ»ΠΈΠ½ΠΎΠΊ. Π§ΡΠΎΠ±Ρ ΠΎΠΏΡΠ΅Π΄Π΅Π»ΠΈΡΡ ΡΡΠ΅Π±ΡΠ΅ΠΌΡΡ ΡΠ΅ΠΌΠΏΠ΅ΡΠ°ΡΡΡΡ ΠΊΠΎΠ²ΠΊΠΈ ΡΡΠ°Π»ΠΈ Π¨Ρ 15 β Π° ΡΡΠΎ Π² ΠΏΡΠ΅Π΄Π΅Π»Π°Ρ 800β¦1100Β°C, ΡΡΠΎΠΈΡ ΠΈΡΠΏΠΎΠ»ΡΠ·ΠΎΠ²Π°ΡΡ ΠΏΠΈΡΠΎΠΌΠ΅ΡΡ. ΠΠΎ Π΅ΡΠ»ΠΈ ΡΠ°ΠΊΠΎΠ²ΠΎΠ³ΠΎ ΠΏΡΠΈΠ±ΠΎΡΠ° Π½Π΅Ρ, ΡΡΠΎΠ²Π΅Π½Ρ Π½Π°Π³ΡΠ΅Π²Π° ΠΎΠΏΡΠ΅Π΄Π΅Π»ΡΠ΅ΠΌ ΠΏΠΎ ΡΠ²Π΅ΡΡ ΠΊΠ°Π»Π΅Π½ΠΈΡ β Π³Π΄Π΅-ΡΠΎ ΠΎΡ Π²ΠΈΡΠ½Π΅Π²ΠΎ-ΠΊΡΠ°ΡΠ½ΠΎΠ³ΠΎ Π΄ΠΎ ΡΠ΅ΠΌΠ½ΠΎ-ΠΆΠ΅Π»ΡΠΎΠ³ΠΎ.
ΠΠΎΠ³Π΄Π° ΠΏΡΠΎΡΠ΅ΡΡ ΠΊΠΎΠ²ΠΊΠΈ ΠΎΠΊΠΎΠ½ΡΠ΅Π½, Π΄Π΅Π»Π°Π΅ΡΡΡ Π½ΠΎΡΠΌΠ°Π»ΠΈΠ·Π°ΡΠΈΡ, Π² ΠΏΡΠΎΡΠΈΠ²Π½ΠΎΠΌ ΡΠ»ΡΡΠ°Π΅ Π² ΠΌΠ΅ΡΠ°Π»Π»Π΅ ΠΎΡΡΠ°Π½ΡΡΡΡ Π½Π°ΠΏΡΡΠΆΠ΅Π½ΠΈΡ ΠΈ ΠΏΡΠΈ Π»ΡΡΡΠ΅ΠΌ ΠΈΡΡ ΠΎΠ΄Π΅ Π²ΠΎ Π²ΡΠ΅ΠΌΡ Π·Π°ΠΊΠ°Π»ΠΊΠΈ ΠΊΠ»ΠΈΠ½ΠΎΠΊ ΠΏΠΎΠ²Π΅Π΄Π΅Ρ, Π° Π² Ρ ΡΠ΄ΡΠ΅ΠΌ β Π»ΠΎΠΏΠ½Π΅Ρ Π½Π° ΠΌΠΎΡΠΎΠ·Π΅, Π²ΠΎΠ·ΠΌΠΎΠΆΠ½ΠΎ Ρ Π½Π°Π½Π΅ΡΠ΅Π½ΠΈΠ΅ΠΌ ΡΡΠ°Π²ΠΌ. Π§ΡΠΎΠ±Ρ ΠΏΡΠΎΠ²Π΅ΡΡΠΈ Π½ΠΎΡΠΌΠ°Π»ΠΈΠ·Π°ΡΠΈΡ, Π½Π°Π³ΡΠ΅Π²Π°Π΅ΠΌ ΠΊΠ»ΠΈΠ½ΠΎΠΊ Π΄ΠΎ 800β¦950Β°C, ΡΠ°ΠΊΡΡ ΡΠ΅ΠΌΠΏΠ΅ΡΠ°ΡΡΡΡ Π²ΡΠ΄Π΅ΡΠΆΠΈΠ²Π°Π΅ΠΌ Π½Π΅Π΄ΠΎΠ»Π³ΠΎ β ΠΈ Π½Π° Π²ΠΎΠ·Π΄ΡΡ , Π½Π° ΡΠΎΠ²Π½ΡΡ ΠΏΠΎΠ²Π΅ΡΡ Π½ΠΎΡΡΡ, ΡΡΠΎΠ±Ρ ΠΎΡΡΡΠ».
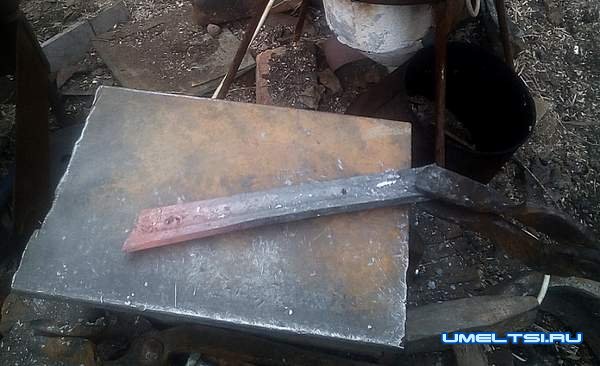
ΠΠ°Π»ΡΡΠ΅ ΠΌΠΎΠΆΠ½ΠΎ ΠΏΠ΅ΡΠ΅Ρ ΠΎΠ΄ΠΈΡΡ ΠΊ ΡΠ»Π΅ΡΠ°ΡΠ½ΠΎΠΉ ΠΎΠ±ΡΠ°Π±ΠΎΡΠΊΠ΅. Π§Π΅ΡΠ½ΠΎΠ²ΡΠ΅ ΡΠΏΡΡΠΊΠΈ Π΄Π΅Π»Π°Π΅ΠΌ ΠΏΡΡΠ΅ΠΌ ΠΊΠΎΠ²ΠΊΠΈ, ΠΎΡΡΠ°Π»ΡΠ½ΠΎΠ΅ β Ρ ΠΏΠΎΠΌΠΎΡΡΡ Π³ΡΠΈΠ½Π΄Π΅ΡΠ° ΠΈΠ»ΠΈ Π±ΠΎΠ»Π³Π°ΡΠΊΠΈ. ΠΠ»Π°Π²Π½ΠΎΠ΅ β ΡΠΎΠ»ΡΠΈΠ½Ρ ΡΠΏΡΡΠΊΠΎΠ² Π΄ΠΎΠ»ΠΆΠ½Π° Π±ΡΡΡ Π½Π΅ ΠΌΠ΅Π½ΡΡΠ΅ 1 ΠΌΠΌ, Π² ΠΏΡΠΎΡΠΈΠ²Π½ΠΎΠΌ ΡΠ»ΡΡΠ°Π΅ Π²ΠΎ Π²ΡΠ΅ΠΌΡ Π·Π°ΠΊΠ°Π»ΠΊΠΈ Π»Π΅Π·Π²ΠΈΠ΅ Π±ΡΠ΄Π΅Ρ Π²Π΅ΡΡΠΈ.
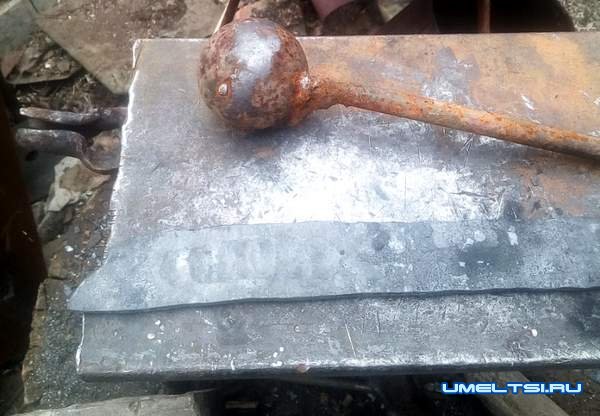
Π’Π΅ΠΏΠ΅ΡΡ β Π½Π°Π²Π΅ΡΠ½ΠΎΠ΅, ΠΊΠ»ΡΡΠ΅Π²ΠΎΠΉ ΠΌΠΎΠΌΠ΅Π½Ρ Π² ΠΈΠ·Π³ΠΎΡΠΎΠ²Π»Π΅Π½ΠΈΠΈ Π½ΠΎΠΆΠ°. ΠΡΠΎ ΡΠ΅ΡΠΌΠΈΡΠ΅ΡΠΊΠ°Ρ ΠΎΠ±ΡΠ°Π±ΠΎΡΠΊΠ°.
ΠΠ»Ρ Π·Π°ΠΊΠ°Π»ΠΊΠΈ ΠΌΠ΅Π΄Π»Π΅Π½Π½ΠΎ Π½Π°Π³ΡΠ΅Π²Π°Π΅ΠΌ ΠΊΠ»ΠΈΠ½ΠΎΠΊ Π΄ΠΎ 830Β°C β ΡΠ²Π΅ΡΠ»ΠΎ-ΠΊΡΠ°ΡΠ½ΠΎΠ³ΠΎ ΡΠ²Π΅ΡΠ°. ΠΠ»Ρ ΠΎΠΏΡΠ΅Π΄Π΅Π»Π΅Π½ΠΈΡ Π½ΡΠΆΠ½ΠΎ ΡΠ΅ΠΌΠΏΠ΅ΡΠ°ΡΡΡΡ ΠΌΠΎΠΆΠ½ΠΎ ΠΈΡΠΏΠΎΠ»ΡΠ·ΠΎΠ²Π°ΡΡ ΠΌΠ°Π³Π½ΠΈΡ β Π΅ΡΠ»ΠΈ ΠΌΠ΅ΡΠ°Π»Π» Π±ΠΎΠ»ΡΡΠ΅ Π½Π΅ ΠΌΠ°Π³Π½ΠΈΡΠΈΡΡΡ, Π·Π½Π°ΡΠΈΡ Π΄ΠΎΡΡΠΈΠ³Π½ΡΡΠ° Π½ΠΈΠΆΠ½ΡΡ ΡΠ΅ΠΌΠΏΠ΅ΡΠ°ΡΡΡΠ° Π·Π°ΠΊΠ°Π»ΠΊΠΈ. ΠΠΎΡΠ»Π΅ ΡΠΎΠ³ΠΎ ΠΊΠ°ΠΊ ΠΏΡΠΈ ΡΠ°ΠΊΠΎΠΉ ΡΠ΅ΠΌΠΏΠ΅ΡΠ°ΡΡΡΠ΅ ΡΠΎΠ±Π»ΡΠ΄Π΅Π½Π° Π²ΡΠ΄Π΅ΡΠΆΠΊΠ° 1 ΠΌΠΈΠ½ΡΡΠ° Π½Π° ΠΊΠ°ΠΆΠ΄ΡΠΉ ΠΌΠΌ ΡΠΎΠ»ΡΠΈΠ½Ρ ΠΊΠ»ΠΈΠ½ΠΊΠ° β ΠΎΡ Π»Π°ΠΆΠ΄Π°Π΅ΠΌ Π² ΠΌΠ°ΡΠ»Π΅. ΠΡΠΈ ΡΡΠΎΠΌ ΠΌΠ°ΡΠ»ΠΎ Π΄ΠΎΠ»ΠΆΠ½ΠΎ Π±ΡΡΡ ΠΏΠΎΠ΄ΠΎΠ³ΡΠ΅ΡΠΎ ΠΏΡΠΈΠΌΠ΅ΡΠ½ΠΎ Π΄ΠΎ 50Β°C.
ΠΠ΅ ΠΌΠ΅Π½ΡΡΡΡ Π²Π°ΠΆΠ½ΠΎΡΡΡ ΠΈΠΌΠ΅Π΅Ρ ΠΏΡΠΎΡΠ΅ΡΡ ΠΎΡΠΏΡΡΠΊΠ° ΠΌΠ΅ΡΠ°Π»Π»Π° β ΠΌΠΎΠΆΠ½ΠΎ ΡΠ΄Π΅Π»Π°ΡΡ Π² Π΄ΡΡ ΠΎΠ²ΠΊΠ΅, t200Β°C, ΠΏΡΠΎΠ΄ΠΎΠ»ΠΆΠΈΡΠ΅Π»ΡΠ½ΠΎΡΡΡ β ΠΏΠΎΠ»ΡΠΎΡΠ° ΡΠ°ΡΠ°. ΠΠ΄Π΅ΡΡ Π³Π»Π°Π²Π½ΠΎΠ΅, ΡΡΠΎΠ±Ρ ΡΡΠΎΠ³ΠΎ Π½Π΅ Π²ΠΈΠ΄Π΅Π»Π° ΠΆΠ΅Π½Π° =)
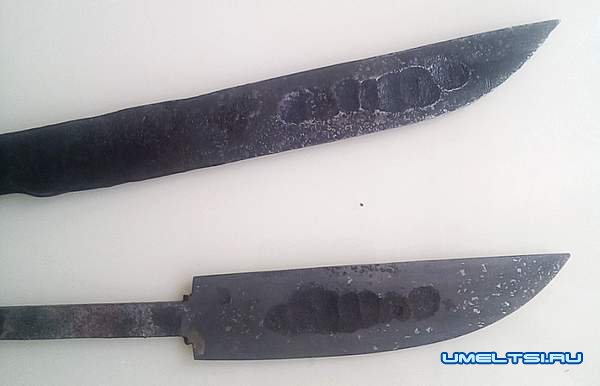
Π Π΅Π·ΡΠ»ΡΡΠ°Ρ β Π² ΠΌΠ΅ΡΡ ΡΠ²Π΅ΡΠ΄ΡΠΉ ΠΊΠ»ΠΈΠ½ΠΎΠΊ, Π½Π°Π΄ΡΠΈΠ»Ρ ΠΌΠΎΠΆΠ½ΠΎ Π΅Π΄Π²Π° Π·Π°ΡΠ΅ΠΏΠΈΡΡ, ΠΏΡΠΈ Π½Π°Π³ΡΡΠ·ΠΊΠ΅ ΠΏΡΡΠΆΠΈΠ½ΠΈΡ.
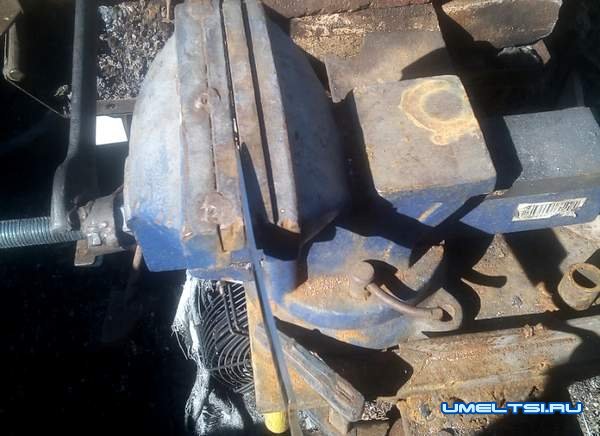
ΠΠ°Π»ΡΡΠ΅ ΠΏΠ΅ΡΠ΅ΠΉΠ΄Π΅ΠΌ ΠΊ ΡΡΠΊΠΎΡΡΠΈ. Π ΠΊΠ°ΡΠ΅ΡΡΠ²Π΅ ΠΌΠ°ΡΠ΅ΡΠΈΠ°Π»Π° ΡΡΠΊΠΎΡΡΠΊΠΈ Π°Π²ΡΠΎΡ Π²Π·ΡΠ» Π±Π΅ΡΠ΅Π·ΠΎΠ²ΡΠΉ ΡΡΠ²Π΅Π»Ρ, ΠΎΡΠ²Π°ΡΠ΅Π½Π½ΡΠΉ Π² ΡΠΎΠ»Π΅Π½ΠΎΠΉ Π²ΠΎΠ΄Π΅ Ρ Ρ Π²ΠΎΠΉΠ½ΡΠΌΠΈ ΠΎΠΏΠΈΠ»ΠΊΠ°ΠΌΠΈ.
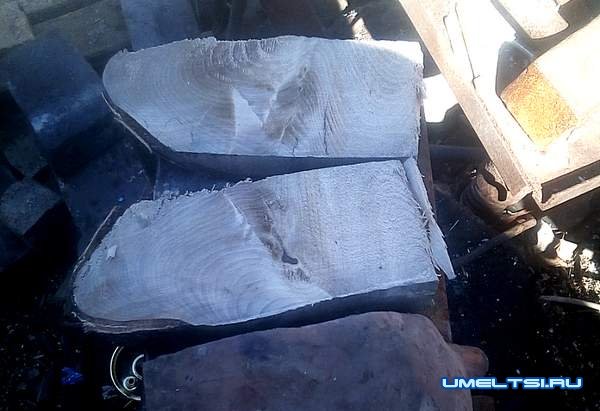

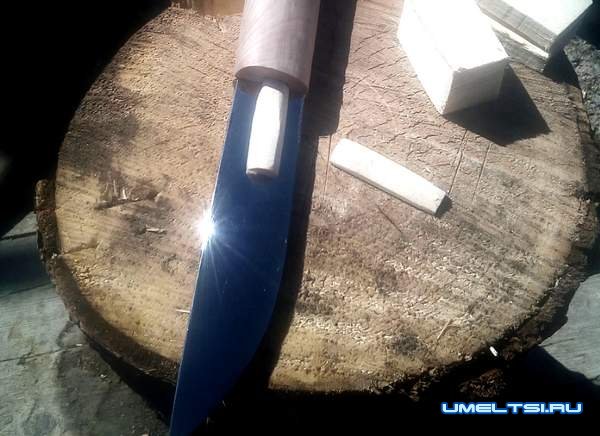
ΠΠΎΡΠΎΠ²Π°Ρ ΡΡΠΊΠΎΡΡΡ ΠΏΡΠΎΠΏΠΈΡΡΠ²Π°Π΅ΡΡΡ β Π΄Π»Ρ ΡΡΠΎΠ³ΠΎ Π±Π΅ΡΠ΅ΠΌ Π³ΠΎΡΡΡΠ΅Π΅ Π»ΡΠ½ΡΠ½ΠΎΠ΅ ΠΌΠ°ΡΠ»ΠΎ.

ΠΠ»Ρ ΠΏΠΎΠ»Π½ΠΎΡΠ΅Π½Π½ΠΎΠ³ΠΎ Π½ΠΎΠΆΠ° Π½ΡΠΆΠ½ΠΎ ΡΠΎΠΎΡΠ²Π΅ΡΡΡΠ²ΡΡΡΠ΅Π΅ ΠΎΠ΄Π΅ΡΠ½ΠΈΠ΅ β ΡΠΎ Π΅ΡΡΡ Π½ΠΎΠΆΠ½Ρ.
Π―ΠΊΡΡΡ Π΄Π»Ρ ΠΈΠ·Π³ΠΎΡΠΎΠ²Π»Π΅Π½ΠΈΡ Π½ΠΎΠΆΠ΅Π½ Π΄Π»Ρ ΡΠ²ΠΎΠΈΡ ΠΊΠ»ΠΈΠ½ΠΊΠΎΠ² ΠΈΡΠΏΠΎΠ»ΡΠ·ΡΡΡ Π±ΡΡΠΈΠΉ Ρ Π²ΠΎΡΡ. Π Π½Π°ΡΠΈΡ ΡΠΈΡΠΎΡΠ°Ρ Ρ Π²ΠΎΡΡΡ, Π΄Π° ΠΈ Π±ΡΠΊΠΈ Π² Π΄Π΅ΡΠΈΡΠΈΡΠ΅, Π½ΠΎ Π·Π°ΡΠΎ Π΄ΠΎΡΡΠ°ΡΠΎΡΠ½ΠΎ Π±Π΅ΡΠ΅ΡΡΡ. Π ΡΠΎΠΆΠ°Π»Π΅Π½ΠΈΡ, ΠΏΠΎ ΡΠΎΡΠΎΠ³ΡΠ°ΡΠΈΡΠΌ Π΄Π΅ΠΉΡΡΠ²ΡΠ΅Ρ ΠΎΠ³ΡΠ°Π½ΠΈΡΠ΅Π½ΠΈΠ΅, ΠΏΠΎΡΡΠΎΠΌΡ Π΄Π»Ρ ΡΠ΅Ρ , ΠΊΡΠΎ Π±ΡΠ΄Π΅Ρ ΠΈΠ½ΡΠ΅ΡΠ΅ΡΠΎΠ²Π°ΡΡΡΡ, ΡΠ΄Π΅Π»Π°Ρ ΠΏΡΠΎΠ΄ΠΎΠ»ΠΆΠ΅Π½ΠΈΠ΅ β ΠΎ Π½ΠΎΠΆΠ½Π°Ρ .
ΠΠΎΠΆ ΠΈΠ· ΠΎΠ±ΠΎΠΉΠΌΡ ΠΏΠΎΠ΄ΡΠΈΠΏΠ½ΠΈΠΊΠ°, Π½ΠΎΠΌΠ΅Ρ 2

ΠΡΠ΅ΠΌ Π·Π΄ΡΠ°Π²ΡΡΠ²ΡΠΉΡΠ΅, Π² ΡΠ΅Π³ΠΎΠ΄Π½ΡΡΠ½Π΅ΠΉ ΡΡΠ°ΡΡΠ΅ Ρ Ρ ΠΎΡΡ ΠΏΠΎΠΊΠ°Π·Π°ΡΡ ΡΠ²ΠΎΠΉ Π²ΡΠΎΡΠΎΠΉ Π²Π°ΡΠΈΠ°Π½Ρ Π½ΠΎΠΆΠ° ΠΈΠ· Π½Π΅Π±ΠΎΠ»ΡΡΠΎΠ³ΠΎ ΠΏΠΎΠ΄ΡΠΈΠΏΠ½ΠΈΠΊΠ°. Π‘ΡΠ°Π»Ρ Π·Π°Π³ΠΎΡΠΎΠ²ΠΊΠΈ Π¨Π₯15. Π’Π°ΠΊΠ°Ρ ΡΡΠ°Π»Ρ ΠΎΡΠ΅Π½Ρ ΡΠ°ΡΠΏΡΠΎΡΡΡΠ°Π½Π΅Π½Π°, ΠΈ ΠΏΠΎ-ΡΡΠΎΠΌΡ Π»ΡΠ±ΠΎΠΉ Π½ΠΎΠ²ΠΈΡΠΎΠΊ, ΠΊΠ°ΠΊ Ρ ΠΌΠΎΠΆΠ΅Ρ ΠΈΠ· Π½Π΅Π΅ ΠΊΠΎΠ²Π°ΡΡ Π½ΠΎΠΆ. Π£ ΠΌΠ΅Π½Ρ Π² ΠΊΡΠ·Π½Π΅ Π»Π΅ΠΆΠΈΡ Π΄Π΅ΡΡΡΠΎΠΊ Π½ΠΎΠΆΠ΅ΠΉ ΠΈΠ· ΡΠ°Π·Π½ΡΡ ΠΏΠΎΠ΄ΡΠΈΠΏΠ½ΠΈΠΊΠΎΠ² Π²Π΅Π΄Ρ ΡΡΠ°Π»Ρ Π¨Π₯15 Π½Π΅ ΠΊΠ°ΠΏΡΠΈΠ·Π΅Π½ Π² ΠΊΠΎΠ²ΠΊΠ΅, ΠΈ ΠΏΠΎΡΡΠΎΠΌΡ Ρ ΡΠ°ΡΡΠΎ ΠΊΡΡ Π½ΠΎΠΆΠΈ ΠΈΠ· Π¨Π₯15.
ΠΠ΄Π½ΠΎΠΌΡ Π½ΠΎΠΆΡ ΡΠΆΠ΅ Π±ΠΎΠ»Π΅Π΅ ΠΏΡΡΠΈ Π»Π΅Ρ, Ρ ΠΈΡΠΏΠΎΠ»ΡΠ·ΡΡ Π΅Π³ΠΎ Π΄Π»Ρ ΡΠ΅ΠΏΡ, ΠΈ ΠΈΠ½ΠΎΠ³Π΄Π° ΡΠ΅Π³ΠΎ Π½ΠΈΠ±ΡΠ΄Ρ ΠΎΡΡΠ΅Π·Π°ΡΡ, ΡΠΎΡΡ Π΅Π³ΠΎ ΡΠ΅Π΄ΠΊΠΎ, ΠΏΠΎΡΠ»Π΅ ΠΊΠ°ΠΆΠ΄ΠΎΠ³ΠΎ ΠΈΡΠΏΠΎΠ»ΡΠ·ΠΎΠ²Π°Π½ΠΈΡ ΠΏΡΠΎΡΠΈΡΠ°Ρ ΡΡΡ ΠΎΠΉ ΡΡΡΠΏΠΊΠΎΠΉ ΠΈ Π²ΡΠ΅ ΡΡΠΎΠ³ΠΎ Ρ Π²Π°ΡΠ°Π΅Ρ, ΡΡΠΎΠ±Ρ Π½ΠΎΠΆ Π±Π»Π΅ΡΡΠ΅ΡΡ ΠΊΠ°ΠΊ Ρ ΠΊΠΎΡΠ° …
ΠΡΠΈ ΡΠ°Π±ΠΎΡΠ΅ Ρ Π¨Π₯15 Π³Π»Π°Π²Π½ΠΎΠ΅ ΡΡΠ»ΠΎΠ²ΠΈΠ΅ — ΡΡΠΎ ΡΠΎΠ±Π»ΡΠ΄Π΅Π½ΠΈΠ΅ ΡΠ΅ΠΌΠΏΠ΅ΡΠ°ΡΡΡΡ ΠΏΡΠΈ ΠΊΠΎΠ²ΠΊΠ΅. ΠΠ΅ΡΠ°Π»Π» Π½Π°Π³ΡΠ΅Π²Π°Π΅ΡΡΡ Π΄ΠΎ ΡΠ²Π΅ΡΠ»ΠΎ-Π²ΠΈΡΠ½Π΅Π²ΠΎΠ³ΠΎ ΡΠ²Π΅ΡΠ° — ΡΡΠΎ Π³Π΄Π΅-ΡΠΎ 500 ΠΈΠ»ΠΈ 580Β°C. ΠΡΠΈ ΠΊΠΎΠ²ΠΊΠ΅ Π½Π΅ Π½ΡΠΆΠ½ΠΎ ΡΠΎΡΠΎΠΏΠΈΡΡΡΡ ΡΠ°ΡΠΊΠΎΠ²Π°ΡΡ Π½ΠΎΠΆ Π·Π° ΠΏΠ°ΡΡ Π½Π°Π³ΡΠ΅Π²ΠΎΠ² Π»ΡΡΡΠ΅ Π»ΠΈΡΠ½ΠΈΠΉ ΡΠ°Π· Π½Π°Π³ΡΠ΅ΡΡ ΡΠ΅ΠΌ Π²Ρ ΠΏΠ΅ΡΠ΅ΠΆΠΆΠ΅ΡΠ΅ ΠΈΠ»ΠΈ ΡΠΎΠ·Π΄Π°Π΄ΠΈΡΠ΅ ΠΌΠΈΠΊΡΠΎ ΡΡΠ΅ΡΠΈΠ½Ρ, ΠΊΠΎΡΠΎΡΡΠ΅ ΠΈΡΠΏΠΎΡΡΡΡ Π²Π°ΡΠΈ ΡΡΠ°ΡΠ°Π½ΠΈΡ.
Π ΠΎΠ±ΡΠ΅ΠΌ Ρ Π²Π°ΡΠΈΡ Π±ΠΎΠ»ΡΠ°ΡΡ ΠΏΡΠΈΡΡΡΠΏΠ°Ρ ΠΊ ΠΊΠΎΠ²ΠΊΠ΅.
ΠΠΎΠ½Π°Π΄ΠΎΠ±ΠΈΡΡΡ
- ΠΠΎΠ»Π³Π°ΡΠΊΠ°
- ΠΡΠΈΠ½Π΄Π΅Ρ
- ΠΠ°ΠΆΠ΄Π°ΡΠ½Π°Ρ Π±ΡΠΌΠ°Π³Π°
- ΠΠΎΠ΄ΡΠΈΠΏΠ½ΠΈΠΊ
- ΠΡΠ·Π½Π΅ΡΠ½ΠΎΠ΅ ΠΎΠ±ΠΎΡΡΠ΄ΠΎΠ²Π°Π½ΠΈΠ΅
ΠΠ΅ΡΠ΅Π΄ ΠΊΠΎΠ²ΠΊΠΎΠΉ Ρ ΠΎΡΠΆΡΠ³, ΠΌΠ΅ΡΠ°Π»Π» ΠΈ ΠΏΠΎΡΡΠΎΠΌΡ ΡΡΠ°Π·Ρ ΠΏΡΠΈΡΡΡΠΏΠ°Ρ ΠΊ ΠΊΠΎΠ²ΠΊΠ΅ Π±Π΅Π· ΠΎΡΠΆΠΈΠ³Π°. ΠΠ°Π³ΡΠ΅Π²Π°Ρ Π΄ΠΎ ΡΠ²Π΅ΡΠ»ΠΎ Π²ΠΈΡΠ½ΡΠ²ΠΎΠ³ΠΎ ΡΠ²Π΅ΡΠ° ΠΏΠΎΠ΄ΡΠΈΠΏΠ½ΠΈΠΊ ΠΈ Π½Π° Π½Π°ΠΊΠΎΠ²Π°Π»ΡΠ½Π΅ Π²ΡΡΠ°Π²Π½ΠΈΠ²Π°Ρ Π² ΡΠΎΠ²Π½ΡΡ ΠΏΠΎΠ»ΠΎΡΡ. ΠΡΠΈ Π½Π°Π³ΡΠ΅Π²Π΅ ΠΏΠΎΠ΄Π΄ΡΠ² Π½Π° ΠΌΠΈΠ½ΠΈΠΌΠ°Π»ΡΠ½ΠΎΠΉ ΡΠΈΠ»Π΅, ΡΠ°ΠΊ Π΄ΠΎΠ»ΡΡΠ΅ Π³ΡΠ΅Π΅ΡΡΡ, Π½ΠΎ Π·Π°ΡΠΎ ΡΠΎΡΠ½ΠΎ Π½Π΅ ΠΏΠ΅ΡΠ΅Π³ΡΠ΅Ρ.

ΠΠΎΠ²ΠΊΡ Π½Π°ΡΠΈΠ½Π°Ρ Ρ Π»Π΅Π·Π²ΠΈΡ. ΠΠΎΡΠ»Π΅ Π½Π°Π³ΡΠ΅Π²Π° Π½Π°Π½ΠΎΡΡ ΡΠ΄Π°ΡΡ Π½Π΅ΡΠΈΠ»ΡΠ½ΡΠ΅, Π½ΠΎ Ρ ΠΎΡΡΡΠΆΠΊΠΎΠΉ ΠΎΡ ΡΠ΅Π½ΡΡΠ° Π΄ΠΎ Π»Π΅Π·Π²ΠΈΡ. Π‘Π½Π°ΡΠ°Π»Π° Π½ΡΠΆΠ½ΠΎ ΡΠ°ΡΠΊΠΎΠ²Π°ΡΡ Π΄ΠΎΠ», ΠΊΠΎΡΠΎΡΡΠΉ Π² ΡΠ΅Π½ΡΡΠ΅ ΠΏΠ»Π°ΡΡΠΈΠ½Ρ, ΠΏΠΎ ΠΊΠΎΡΠΎΡΠΎΠΌΡ ΡΠΊΠΎΠ»ΡΠ·ΡΡ ΡΠ°ΡΠΈΠΊΠΈ. ΠΠ½Π°ΡΠ΅ Π΅ΡΠ»ΠΈ Π½Π°ΡΠ°ΡΡ ΡΠ΄Π°ΡΡΡΡ ΠΏΠΎ ΠΎΠ±ΡΡ Ρ ΠΏΠ»Π°ΡΡΠΈΠ½Π° Π½Π°ΡΠ½Π΅Ρ ΡΠΊΠ»Π°Π΄ΡΠ²Π°ΡΡΡΡ ΠΏΡΠΈ ΠΊΠΎΠ²ΠΊΠ΅ Ρ ΠΊΠΎΠ½ΡΠΈΠΊΠ° ΠΈ Π²ΠΎΠ²ΡΠ΅ ΠΏΠΎΠΉΠ΄Π΅Ρ ΡΡΠ΅ΡΠΈΠ½Π°, ΠΏΠΎ-ΡΡΠΎΠΌΡ Π΅ΡΠ»ΠΈ ΡΠ΅ΡΠΈΠ» ΠΊΠΎΠ²Π°ΡΡ Ρ ΠΊΠΎΠ½ΡΠΈΠΊΠ° Π»Π΅Π·Π²ΠΈΡ, ΡΠΎ ΠΈΠ»ΠΈ Π·Π°ΡΠ°Π½Π΅Π΅ Π½ΡΠΆΠ½ΠΎ ΠΎΡΠΏΠΈΠ»ΠΈΡΡ ΠΏΠΎΠ΄ ΡΠ³Π»ΠΎΠΌ ΠΈΠ»ΠΈ ΡΠ½Π°ΡΠ°Π»Π° Π·Π°ΠΊΠΎΠ²Π°ΡΡ ΡΡΠΎΡ Π΄ΠΎΠ», Π° ΠΏΠΎΡΠΎΠΌ ΡΠΆΠ΅ ΠΊΠΎΠ²Π°ΡΡ Π»Π΅Π·Π²ΠΈΠ΅.
ΠΠΎΡΠ»Π΅ Π½Π°Π³ΡΠ΅Π²Π° Π½Π°Π½ΠΎΡΡ ΠΏΡΡΡ ΠΈΠ»ΠΈ ΡΠ΅ΠΌΡ ΡΠ΄Π°ΡΠΎΠ² ΠΈ ΡΠ½ΠΎΠ²Π° Π½Π°Π³ΡΠ΅Π²Π°Ρ — ΡΡΠΎ Π½Π°Π·ΡΠ²Π°Π΅ΡΡΡ ΠΊΠΎΠ²ΠΊΠ° ΠΏΡΠΈ Π½ΠΈΠ·ΠΊΠΈΡ ΡΠ΅ΠΌΠΏΠ΅ΡΠ°ΡΡΡΠ°Ρ . ΠΡΡ ΡΡΠ°Π·Ρ Π΄ΠΎ Π½ΡΠΆΠ½ΠΎΠΉ ΡΠΎΠ»ΡΠΈΠ½Ρ 2 ΠΌΠΌ. ΠΠΎΡΠ»Π΅ ΠΊΠΎΠ²ΠΊΠΈ Π»Π΅Π·Π²ΠΈΡ ΠΏΡΠΈΡΡΡΠΏΠ°Ρ ΠΊ ΡΠΎΡΠΌΠΈΡΠΎΠ²ΠΊΠ΅ Ρ Π²ΠΎΡΡΠΎΠ²ΠΈΠΊΠ°.
ΠΠΎΠΆ Π±ΡΠ΄Π΅Ρ Ρ Π²ΡΠ°Π΄Π½ΠΎΠΉ ΡΡΠΊΠΎΡΡΡΡ ΠΈ ΠΏΠΎΡΡΠΎΠΌΡ ΡΡΠ°Π·Ρ ΡΠΎΡΠΌΠΈΡΡΡ Π½ΡΠΆΠ½ΡΡ ΡΠΎΠ»ΡΠΈΠ½Ρ. Π’Π°ΠΊ ΠΊΠ°ΠΊ Ρ ΡΡΠ°Π·Ρ ΠΊΠΎΠ²Π°Π» Π΄ΠΎ Π½ΡΠΆΠ½ΠΎΠΉ ΡΠΎΠ»ΡΠΈΠ½Ρ, ΡΠΎ ΡΡΠ°Π·Ρ ΠΏΡΠΎΠΈΠ·Π²ΠΎΠΆΡ Π·Π°ΠΊΠ°Π»ΠΊΡ. Π ΡΠ΅ΡΠΈ ΠΎΡΠ΅Π½Ρ ΠΌΠ½ΠΎΠ³ΠΎ ΡΠΏΠΎΡΠΎΠ² ΠΎ ΡΠΎΠΌ, ΠΊΠ°ΠΊ ΠΏΡΠ°Π²ΠΈΠ»ΡΠ½ΠΎ Π·Π°ΠΊΠ°Π»ΡΡΡ Π¨Π₯15 ΠΈ Π² ΡΠ΅ΠΌ. ΠΠΈΡΠ½ΠΎ Ρ ΠΏΡΠΎΠ±ΠΎΠ²Π°Π» ΡΠ°Π·Π½ΡΠ΅ Π²Π°ΡΠΈΠ°Π½ΡΡ ΠΎΡΠΎΠ±ΠΎΠΉ ΡΠ°Π·Π½ΠΈΡΡ Ρ Π½Π΅ Π·Π°ΠΌΠ΅ΡΠΈΠ» Π»ΠΈΡΡ ΡΡ, ΡΡΠΎ ΠΏΡΠΈ Π·Π°ΠΊΠ°Π»ΠΊΠ΅ Π² Π²ΠΎΠ΄Π΅ Π½ΠΎΠΆ Π²ΡΠ΅ ΡΠ°Π²Π½ΠΎ ΠΎΡΡΠ°Π΅ΡΡΡ Ρ ΡΡΠΏΠΊΠΈΠΌ, Ρ Π½Π΅ Π·Π½Π°Ρ Π² ΡΠ΅ΠΌ ΡΠ΅ΠΊΡΠ΅Ρ, Π½ΠΎ Π½Π΅ΠΊΠΎΡΠΎΡΡΠ΅ ΠΏΡΠΎΠΈΠ·Π²ΠΎΠ΄ΡΡ Π·Π°ΠΊΠ°Π»ΠΊΡ Π² ΡΠΎΠ»ΡΡΠΊΠ΅ ΠΈ ΡΡΠ²Π΅ΡΠΆΠ΄Π°ΡΡ, ΡΡΠΎ Π½ΠΎΠΆ ΠΏΠΎΠ»ΡΡΠ°Π΅ΡΡΡ Π³ΠΈΠ±ΠΊΠΈΠΌ ΠΈ ΠΌΠ΅Π½Π΅Π΅ Ρ ΡΡΠΏΠΊΠΈΠΌ, Ρ ΡΠ°ΠΊ ΠΈ Π½Π΅ ΡΠ°Π·ΠΎΠ±ΡΠ°Π²ΡΠΈΡΡ Π² ΡΡΠΎΠΌ, Π²ΡΠ΅ΠΌ Π·Π°ΠΊΠ°Π»ΠΈΠ²Π°Ρ Π¨Π₯15 Π² ΠΏΠΎΠ΄ΠΎΠ³ΡΠ΅ΡΠΎΠΌ Π°Π²ΡΠΎ ΠΌΠ°ΡΠ»Π΅. ΠΠ»Π°Π²Π½ΠΎΠ΅ ΠΏΠΎΡΠ»Π΅ Π·Π°ΠΊΠ°Π»ΠΊΠΈ ΠΏΡΠΎΠΈΠ·Π²Π΅ΡΡΠΈ Π΄ΠΎΠ»Π³ΠΈΠΉ, Π½ΠΎ ΠΊΠ°ΡΠ΅ΡΡΠ²Π΅Π½Π½ΡΠΉ ΠΎΡΠΏΡΡΠΊ, ΡΠΎΠ³Π΄Π° Π½ΠΎΠΆ Π±ΡΠ΄Π΅Ρ ΠΌΠ΅Π½Π΅Π΅ Ρ ΡΡΠΏΠΊΠΈΠΌ.
ΠΠΎΡΠ»Π΅ ΡΠΎΠ³ΠΎ ΠΊΠ°ΠΊ Π½ΠΎΠΆ Π½Π°Π³ΡΠ΅Π»ΡΡ Π΄ΠΎ Π½ΡΠΆΠ½ΠΎΠΉ Π½Π΅ΠΌΠ°Π³Π½ΠΈΡΠ½ΠΎΠΉ ΡΠ΅ΠΌΠΏΠ΅ΡΠ°ΡΡΡΡ, ΠΎΡΠΏΡΡΠΊΠ°Ρ ΠΊΠ»ΠΈΠ½ΠΎΠΊ Π² ΠΌΠ°ΡΠ»ΠΎ ΠΏΠΎΠΊΠ° Π½Π΅ ΠΏΠ΅ΡΠ΅ΡΡΠ°Π½Π΅Ρ Π±ΡΠ»ΡΠΊΠ°ΡΡ ΠΌΠ°ΡΠ»ΠΎ. ΠΡΠΏΡΡΠΊ ΠΌΠ΅ΡΠ°Π»Π»Π° ΠΏΡΠΎΠΈΠ·Π²ΠΎΠΆΡ Π½Π° ΠΎΡΠΊΠ»ΡΡΡΠ½Π½ΠΎΠΌ Π³ΠΎΡΠ½Π΅, Π·Π°ΠΊΡΡΠ² ΠΊΠΈΡΠΏΠΈΡΠ°ΠΌΠΈ, ΡΠ°ΠΊ ΠΎΠ½ ΠΎΡΡΡΠ²Π°Π΅Ρ ΡΠ°ΡΠ° Π΄Π²Π°, ΡΡΠΈ. ΠΡ Π²ΠΎΡ Ρ ΠΊΠΎΠ²ΠΊΠΎΠΉ Π²ΡΠ΅ ΡΠ΅ΠΏΠ΅ΡΡ ΠΏΡΠΈΡΡΡΠΏΠ°Ρ ΠΊ ΡΠ»Π΅ΡΠ°ΡΠΊΠ΅





ΠΠ° ΠΡΠΈΠ½Π΄Π΅ΡΠ΅ ΡΠ»ΠΈΡΡΡ ΠΏΠΎΠ²Π΅ΡΡ Π½ΠΎΡΡΡ Π½ΠΎΠΆΠ°, ΠΈ Π²ΡΠ²ΠΎΠΆΡ ΡΠΏΡΡΠΊΠΈ. ΠΠ΅ΠΌΠ½ΠΎΠ³ΠΎ ΡΠ΅ΡΠΈΠ» ΠΎΡΡΠ°Π²ΠΈΡΡ ΠΊΠΎΠ²ΠΊΠΈ Π½Π° Π»Π΅Π·Π²ΠΈΠΈ. ΠΡΡΠ»ΠΈΡΠΎΠ²Π°Π² Π²ΡΠ΅ ΡΡΠΎΡΠΎΠ½Ρ ΠΏΡΠΈΡΡΡΠΏΠ°Ρ ΠΊ ΠΈΠ·Π³ΠΎΡΠΎΠ²Π»Π΅Π½ΠΈΡ ΡΡΠΊΠΎΡΡΠΈ
ΠΠ»Ρ ΠΈΠ·Π³ΠΎΡΠΎΠ²Π»Π΅Π½ΠΈΡ ΡΡΠΊΠΎΡΡΠΈ Π²Π·ΡΠ» ΠΊΡΡΠΎΠΊ ΡΡΡ ΠΎΠΉ Π±Π΅ΡΠ΅Π·Ρ, ΠΌΠ½Π΅ Π½ΡΠ°Π²ΠΈΡΡΡ ΡΠ°Π±ΠΎΡΠ°ΡΡ Ρ Π±Π΅ΡΠ΅Π·ΠΎΠΉ, ΠΎΡΠΎΠ±Π΅Π½Π½ΠΎ ΠΌΠ½Π΅ Π½ΡΠ°Π²ΠΈΡΡΡ ΡΡΠΊΠΎΡΡΡ ΠΈΠ· Π±Π΅ΡΠ΅ΡΡΡ — ΠΎΡΠ΅Π½Ρ ΠΊΡΠ°ΡΠΈΠ²ΠΎ, Π° Π² ΡΡΠΊΠ΅ ΠΊΠ°ΠΊ ΡΠ΅ΠΏΠ»ΠΎ Π»Π΅ΠΆΠΈΡ — Π²ΠΎΠΎΠ±ΡΠ΅ ΡΠΊΠ°Π·ΠΊΠ°. Π ΡΠ°ΠΊ ΠΎΡΠΏΠΈΠ»ΠΈΠ² Π½ΡΠΆΠ½ΡΠΉ ΠΊΡΡΠΎΠΊ ΡΠ½ΠΈΠΌΠ°Ρ ΠΊΠΎΡΡ, Π΄Π°Π»Π΅Π΅ ΠΏΡΠΎΡΠ²Π΅ΡΠ»ΠΈΠ» Π² ΡΠ΅Π½ΡΡΠ΅ ΠΎΡΠ²Π΅ΡΡΡΠΈΠ΅ ΠΈ Π²ΡΠ΅ΠΌΠ΅Π½Π½ΠΎ Π·Π°Π±ΠΈΠ» Ρ Π²ΠΎΡΡΠΎΠ²ΠΈΠΊ. ΠΠ° ΡΡΠ°Π½ΠΊΠ΅ ΡΠΎΡΠΌΠΈΡΡΡ Π½ΡΠΆΠ½ΡΡ ΡΠΎΡΠΌΡ Π±Π΅Π· Π²ΡΡΠΊΠΈΡ ΡΠ΅ΡΡΠ΅ΠΆΠ΅ΠΉ ΠΏΡΠΎΡΡΠΎ ΡΠΎΡΡ ΠΈ ΠΏΡΠΈΠΌΠ΅ΡΡΡ ΠΊ ΡΡΠΊΠ΅. ΠΡ Π²ΠΎΡ Π²ΡΠΎΠ΄Π΅ Π²ΡΠ΅. ΠΠΎΡΠ»Π΅ ΡΠ»ΠΈΡΠΎΠ²ΠΊΠΈ ΡΠΊΠ»Π΅ΠΈΠ²Π°Ρ ΡΡΠΊΠΎΡΡΡ Π½Π° ΡΠΏΠΎΠΊΡΠΈΠ΄Π½ΡΠΉ ΠΊΠ»Π΅ΠΉ. ΠΠ»Ρ Π·Π°ΡΠΈΡΡ ΡΡΡΠΊΠΈ ΠΎΡ Π²Π»Π°Π³ΠΈ ΠΏΡΠΎΠΏΠΈΡΡΠ²Π°Ρ Π² Π½Π°ΡΡΡΠ°Π»ΡΠ½ΠΎΠΌ Π²ΠΎΡΠΊΠ΅ Π½Π° ΠΏΠ°ΡΠΎΠ²ΠΎΠΉ Π±Π°Π½Π΅ 2 ΡΠ°ΡΠ°.
ΠΡ Π²ΠΎΡ ΠΈ Π²ΡΠ΅, Π½ΠΎΠΆ ΠΈΠ· ΠΎΠ±ΠΎΠΉΠΌΡ ΠΏΠΎΠ΄ΡΠΈΠΏΠ½ΠΈΠΊΠ° Π½ΠΎΠΌΠ΅Ρ 2 — Π³ΠΎΡΠΎΠ². ΠΠΈΠ½ΠΈΠΌΡΠΌ Π·Π°ΡΡΠ°Ρ, ΠΌΠ΅ΡΠ°Π»Π» Π½Π°ΡΠ΅Π», Π° Π΄Π΅ΡΠ΅Π²ΠΎ ΡΠΎΡΠ»ΠΎ. ΠΡΠ΅ΠΌ ΡΠΏΠ°ΡΠΈΠ±ΠΎ Π·Π° Π²Π½ΠΈΠΌΠ°Π½ΠΈΠ΅ ΠΈ Π΄ΠΎ Π½ΠΎΠ²ΡΡ Π‘Π°ΠΌΠΎΠ΄Π΅Π»ΠΎΠΊ Π΄ΡΡΠ·ΡΡ
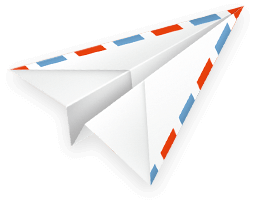
ΠΠΎΠ»ΡΡΠ°ΠΉΡΠ΅ Π½Π° ΠΏΠΎΡΡΡ ΠΏΠΎΠ΄Π±ΠΎΡΠΊΡ Π½ΠΎΠ²ΡΡ ΡΠ°ΠΌΠΎΠ΄Π΅Π»ΠΎΠΊ. ΠΠΈΠΊΠ°ΠΊΠΎΠ³ΠΎ ΡΠΏΠ°ΠΌΠ°, ΡΠΎΠ»ΡΠΊΠΎ ΠΏΠΎΠ»Π΅Π·Π½ΡΠ΅ ΠΈΠ΄Π΅ΠΈ!
*ΠΠ°ΠΏΠΎΠ»Π½ΡΡ ΡΠΎΡΠΌΡ Π²Ρ ΡΠΎΠ³Π»Π°ΡΠ°Π΅ΡΠ΅ΡΡ Π½Π° ΠΎΠ±ΡΠ°Π±ΠΎΡΠΊΡ ΠΏΠ΅ΡΡΠΎΠ½Π°Π»ΡΠ½ΡΡ Π΄Π°Π½Π½ΡΡ
Π‘ΡΠ°Π½ΠΎΠ²ΠΈΡΠ΅ΡΡ Π°Π²ΡΠΎΡΠΎΠΌ ΡΠ°ΠΉΡΠ°, ΠΏΡΠ±Π»ΠΈΠΊΡΠΉΡΠ΅ ΡΠΎΠ±ΡΡΠ²Π΅Π½Π½ΡΠ΅ ΡΡΠ°ΡΡΠΈ, ΠΎΠΏΠΈΡΠ°Π½ΠΈΡ ΡΠ°ΠΌΠΎΠ΄Π΅Π»ΠΎΠΊ Ρ ΠΎΠΏΠ»Π°ΡΠΎΠΉ Π·Π° ΡΠ΅ΠΊΡΡ. ΠΠΎΠ΄ΡΠΎΠ±Π½Π΅Π΅ Π·Π΄Π΅ΡΡ.ΠΠΎΠΆ ΠΈΠ· Π½Π΅Π±ΠΎΠ»ΡΡΠΎΠ³ΠΎ ΠΏΠΎΠ΄ΡΠΈΠΏΠ½ΠΈΠΊΠ°

ΠΡΠ΅ΠΌ Π·Π΄ΡΠ°Π²ΡΡΠ²ΡΠΉΡΠ΅!!! ΠΡΠ»ΠΎ ΡΠ²ΠΎΠ±ΠΎΠ΄Π½ΠΎΠ΅ Π²ΡΠ΅ΠΌΡ ΠΏΠ°ΡΡ ΡΠ°ΡΠΎΠ² — ΡΠ΅ΡΠΈΠ» ΡΠ΄Π΅Π»Π°ΡΡ Π½ΠΎΠΆ. ΠΠ· ΠΊΡΡΠΈ ΠΌΠ΅ΡΠ°Π»Π»Π° Π²ΡΠ±ΡΠ°Π» Π½Π΅Π±ΠΎΠ»ΡΡΠΎΠΉ ΠΏΠΎΠ΄ΡΠΈΠΏΠ½ΠΈΠΊ, Π±ΡΠ΄Ρ ΠΊΠΎΠ²Π°ΡΡ Π½ΠΎΠΆ ΠΈΠ· Π½Π΅Π³ΠΎ.
ΠΠΎΠ½Π°Π΄ΠΎΠ±ΠΈΡΡΡ ΠΈΠ½ΡΡΡΡΠΌΠ΅Π½Ρ
- ΠΡΠ΅Π»Ρ
- ΠΠΎΠ»Π³Π°ΡΠΊΠ°
- Π¨Π»ΠΈΡΠΎΠ²Π°Π»ΡΠ½ΡΠΉ ΡΡΠ°Π½ΠΎΠΊ
- ΠΠ°ΠΏΠΈΠ»ΡΠ½ΠΈΠΊ
- ΠΠ΅ΡΠ°Π»Π» Π΄Π»Ρ Π½ΠΎΠΆΠ°
- ΠΠΎΡΠ½
- ΠΠ΅ΡΠ΅Π²ΠΎ Π΄Π»Ρ ΡΡΠΊΠΎΡΡΠΈ

ΠΠ΅ΡΠ΅Π΄ ΠΊΠΎΠ²ΠΊΠΎΠΉ ΠΎΠ±ΠΆΠΈΠ³Π°Ρ Π² Π³ΠΎΡΠ½Π΅, Π½Π°Π³ΡΠ΅Π²Π°Ρ Π΄ΠΎ Π²ΠΈΡΠ½Π΅Π²ΠΎΠ³ΠΎ ΡΠ²Π΅ΡΠ° ΠΈ ΠΎΡΡΠ°Π²Π»ΡΡ ΠΎΡΡΡΠ²Π°ΡΡ Π½Π° ΠΏΠ΅ΡΠΊΠ΅. ΠΠΎΡΠ»Π΅ ΠΎΠ±ΠΆΠΈΠ³Π° ΠΊΠΎΠ²Π°ΡΡ Π±ΡΠ΄Π΅Ρ Π»Π΅Π³ΡΠ΅ ΠΌΠ΅ΡΠ°Π»Π» ΠΏΠΎΡΠ»Π΅ ΠΎΠ±ΠΆΠΈΠ³Π°, ΠΏΠΎΡΠ΅ΡΡΠ» Π·Π°ΠΊΠ°Π»ΠΊΡ ΠΈ ΡΡΠ°Π» ΠΌΡΠ³ΠΊΠΈΠΌ. ΠΠΎΠ»Π³Π°ΡΠΊΠΎΠΉ Π΄Π΅Π»Π°Ρ ΡΠ°ΡΠΏΠΈΠ» ΠΏΠΎΠ΄ΡΠΈΠΏΠ½ΠΈΠΊΠ° ΠΏΠΎΠΏΠ΅ΡΠ΅ΠΊ. ΠΠ°Π³ΡΠ΅Π²Π°Ρ ΠΏΠΎΠ΄ΡΠΈΠΏΠ½ΠΈΠΊ ΠΈ Π½Π° Π½Π°ΠΊΠΎΠ²Π°Π»ΡΠ½Π΅ ΡΠ°ΡΠΏΡΡΠΌΠ»ΡΡ.ΠΡΠ΅ ΡΠ°Π· Π½Π°Π³ΡΠ΅Π²Π°Ρ ΠΈ ΠΏΡΠΎΠΊΠΎΠ²Π°Π² ΠΏΡΠΈΠΌΠ΅ΡΠ½ΡΡ ΡΠΎΡΠΌΡ Π½ΠΎΠΆΠ°.

ΠΡΠΎΠΊΠΎΠ²Π°Π² Ρ Π²ΠΎΡΡΠΎΠ²ΠΈΠΊ — ΠΏΠΎΠ΄ΡΠ°Π²Π½ΠΈΠ²Π°Ρ Π²ΡΠ΅ Π΅ΡΠ΅ ΡΠ°Π·

ΠΡ Π²ΠΎΡ ΠΈ Π²ΡΠ΅.
ΠΠ°ΠΊΠ°Π»ΠΊΠ° ΠΈ ΠΎΡΠΏΡΡΠΊ. ΠΠΎΡΠ»Π΅ ΠΊΠΎΠ²ΠΊΠΈ Π½ΠΎΠΆΠ° ΠΎΡΡΠ΅Π·Π°Ρ Π²ΡΠ΅ Π»ΠΈΡΠ½Π΅Π΅, Π½Π΅ΠΌΠ½ΠΎΠ³ΠΎ ΡΠ»ΠΈΡΡΡ ΠΈ ΠΏΡΠΈΡΡΡΠΏΠ°Ρ ΠΊ Π·Π°ΠΊΠ°Π»ΠΊΠ΅. ΠΠ°Π³ΡΠ΅Π²Π°Ρ Π΄ΠΎ ΡΠΎΠ³ΠΎ, ΠΊΠ°ΠΊ ΠΏΠ΅ΡΠ΅ΡΡΠ°Π½Π΅Ρ ΠΌΠ°Π³Π½ΠΈΡΠΈΡΡΡΡ ΠΈ ΠΎΠΊΡΠ½Π°Ρ Π² ΠΏΠΎΠ΄ΠΎΠ³ΡΠ΅ΡΠΎΠ΅ ΠΌΠ°ΡΠ»ΠΎ ΠΈ Π²ΡΠ΅. ΠΠΎΡΠ»Π΅ Π·Π°ΠΊΠ°Π»ΠΊΠΈ Π½ΠΎΠΆ ΡΡΠ°Π» Ρ
ΡΡΠΏΠΊΠΈΠΌ Π΄Π»Ρ ΠΏΡΠΈΠ΄Π°Π½ΠΈΡ Π΅ΠΌΡ ΠΊΡΠ΅ΠΏΠΎΡΡΠΈ ΡΡΠ΅Π±ΡΠ΅ΡΡΡ ΠΎΡΠΏΡΡΠΊ ΠΌΠ΅ΡΠ°Π»Π»Π°. ΠΡΠΏΡΡΠΊ ΠΏΡΠΎΠΈΠ·Π²ΠΎΠΆΡ Π² Π΄ΡΡ
ΠΎΠ²ΠΊΠ΅ 2 ΡΠ°ΡΠ° ΠΏΡΠΈ 200Β°C ΠΈ Π΄Π°Ρ ΠΎΡΡΡΡΡ Ρ Π΄ΡΡ
ΠΎΠ²ΠΊΠΎΠΉ, ΠΏΠΎΡΠ»Π΅ ΡΠ»ΠΈΡΡΡ Π½Π΅ΠΌΠ½ΠΎΠ³ΠΎ.

Π€ΠΎΡΠΌΠΈΡΡΡ ΠΊΠ»ΠΈΠ½ ΠΈ ΡΠ»ΠΈΡΡΡ ΠΏΠΎΠ²Π΅ΡΡ Π½ΠΎΡΡΡ ΠΎΡ ΠΊΡΡΠΏΠ½ΠΎΠΉ Π΄ΠΎ ΠΌΠ΅Π»ΠΊΠΎΠΉ Π½Π°ΠΆΠ΄Π°ΡΠ½ΠΎΠΉ Π±ΡΠΌΠ°Π³ΠΈ.

ΠΠ° Ρ Π²ΠΎΡΡΠΎΠ²ΠΈΠΊ ΠΏΡΠΈΠ²Π°ΡΠΈΠ²Π°Ρ ΠΊΡΡΠΎΠΊ Π±ΠΎΠ»ΡΠ° Ρ ΡΠ΅Π·ΡΠ±ΠΎΠΉ Π΄Π»Ρ ΠΊΡΠ΅ΠΏΠ»Π΅Π½ΠΈΡ ΡΡΠΊΠΎΡΡΠΈ.

ΠΠ»Ρ ΡΡΠΊΠΎΡΡΠΈ Π½Π°ΡΠ΅Π» ΠΊΠ°ΠΏ ΠΊΠ»Π΅Π½Π°, Π½ΠΎ Π΅Π³ΠΎ Π΄Π»ΠΈΠ½Ρ ΠΌΠ½Π΅ Π½Π΅ Ρ Π²Π°ΡΠΈΠ»ΠΎ, ΠΏΡΠΈΡΠ»ΠΎΡΡ Π΄Π΅Π»Π°ΡΡ ΠΈΠ· ΠΊΡΡΠΎΡΠΊΠ° ΠΊΠ°ΠΏΠ° Π±Π΅ΡΠ΅Π·Ρ. Π Π·Π°Π³ΠΎΡΠΎΠ²ΠΊΠ΅ ΠΏΡΠΎΡΠ²Π΅ΡΠ»ΠΈΠ²Π°Ρ ΠΎΡΠ²Π΅ΡΡΡΠΈΠ΅, ΠΈ ΡΠΌΠ°Π·Π°Π² Π²ΡΠ΅ ΠΊΠ»Π΅Π΅ΠΌ, Π·Π°Π±ΠΈΠ²Π°Ρ Π±ΡΡΡΠΎΠΊ Π½Π° Ρ Π²ΠΎΡΡΠΎΠ²ΠΈΠΊ. ΠΠ΅ΠΆΠ΄Ρ Π΄Π΅ΡΠ΅Π²ΠΎΠΌ ΠΏΠΎΠ΄ΠΊΠ»Π°Π΄ΡΠ²Π°Ρ ΠΌΠ΅Π΄Π½ΡΡ ΠΏΠ»Π°ΡΡΠΈΠ½Ρ. Π¨Π»ΠΈΡΡΡ ΠΏΡΠΈΠΌΠ΅ΡΠ½ΡΡ ΡΠΎΡΠΌΡ.

ΠΡΠΎΡ ΠΎΠΆΡ Π²ΡΠ΅ Π½Π°ΠΆΠ΄Π°ΡΠ½ΠΎΠΉ Π±ΡΠΌΠ°Π³ΠΎΠΉ.

Π’Π΅ΠΏΠ΅ΡΡ ΠΏΠΎΡΠ»Π΅ ΡΠ»ΠΈΡΠΎΠ²ΠΊΠΈ Π²Π°ΡΡ ΡΡΠΊΠΎΡΡΡ Π² Π½Π°ΡΡΡΠ°Π»ΡΠ½ΠΎΠΌ Π²ΠΎΡΠΊΠ΅ Π΄Π²Π° ΡΠ°ΡΠ°.

ΠΡ Π²ΠΎΡ ΠΈ Π²ΡΠ΅, Π½ΠΎΠΆ Π³ΠΎΡΠΎΠ²! ΠΡΠ΅ΠΌ ΡΠΏΠ°ΡΠΈΠ±ΠΎ Π·Π° Π²Π½ΠΈΠΌΠ°Π½ΠΈΠ΅ ΠΈ Π΄ΠΎ Π½ΠΎΠ²ΡΡ Π‘Π°ΠΌΠΎΠ΄Π΅Π»ΠΎΠΊ Π΄ΡΡΠ·ΡΡ.


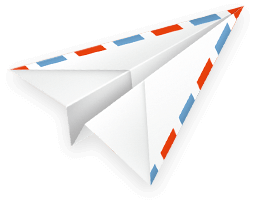
ΠΠΎΠ»ΡΡΠ°ΠΉΡΠ΅ Π½Π° ΠΏΠΎΡΡΡ ΠΏΠΎΠ΄Π±ΠΎΡΠΊΡ Π½ΠΎΠ²ΡΡ ΡΠ°ΠΌΠΎΠ΄Π΅Π»ΠΎΠΊ. ΠΠΈΠΊΠ°ΠΊΠΎΠ³ΠΎ ΡΠΏΠ°ΠΌΠ°, ΡΠΎΠ»ΡΠΊΠΎ ΠΏΠΎΠ»Π΅Π·Π½ΡΠ΅ ΠΈΠ΄Π΅ΠΈ!
*ΠΠ°ΠΏΠΎΠ»Π½ΡΡ ΡΠΎΡΠΌΡ Π²Ρ ΡΠΎΠ³Π»Π°ΡΠ°Π΅ΡΠ΅ΡΡ Π½Π° ΠΎΠ±ΡΠ°Π±ΠΎΡΠΊΡ ΠΏΠ΅ΡΡΠΎΠ½Π°Π»ΡΠ½ΡΡ Π΄Π°Π½Π½ΡΡ
Π‘ΡΠ°Π½ΠΎΠ²ΠΈΡΠ΅ΡΡ Π°Π²ΡΠΎΡΠΎΠΌ ΡΠ°ΠΉΡΠ°, ΠΏΡΠ±Π»ΠΈΠΊΡΠΉΡΠ΅ ΡΠΎΠ±ΡΡΠ²Π΅Π½Π½ΡΠ΅ ΡΡΠ°ΡΡΠΈ, ΠΎΠΏΠΈΡΠ°Π½ΠΈΡ ΡΠ°ΠΌΠΎΠ΄Π΅Π»ΠΎΠΊ Ρ ΠΎΠΏΠ»Π°ΡΠΎΠΉ Π·Π° ΡΠ΅ΠΊΡΡ. ΠΠΎΠ΄ΡΠΎΠ±Π½Π΅Π΅ Π·Π΄Π΅ΡΡ.ΠΠΎΠΆ ΠΈΠ· ΠΎΠ±ΠΎΠΉΠΌΡ ΠΏΠΎΠ΄ΡΠΈΠΏΠ½ΠΈΠΊΠ°, Π²Π°ΡΠΈΠ°Π½Ρ 3

ΠΡΠ΅ΠΌ Π·Π΄ΡΠ°Π²ΡΡΠ²ΡΠΉΡΠ΅.
Π‘Π΅Π³ΠΎΠ΄Π½Ρ ΡΡΠ΅ΡΡΡ ΡΡΠ°ΡΡΡ Π½Π° ΡΠ΅ΠΌΡ Π½ΠΎΠΆ ΠΈΠ· Π¨Π₯15 ΠΈΠ»ΠΈ Π½ΠΎΠΆ ΠΈΠ· ΠΎΠ±ΠΎΠΉΠΌΡ ΠΏΠΎΠ΄ΡΠΈΠΏΠ½ΠΈΠΊΠ°. ΠΠ°ΠΊ Ρ Π³ΠΎΠ²ΠΎΡΠΈΠ» ΡΠ°Π½Π΅Π΅, ΡΡΠΎ ΠΏΠΎΠ΄ΡΠΈΠΏΠ½ΠΈΠΊΠΈ Π±ΡΠ²Π°ΡΡ ΡΠ°Π·Π½ΡΠ΅, ΠΌΠ°ΡΠΊΡ ΡΡΠ°Π»ΠΈ ΠΏΠΎΠ΄ΡΠΈΠΏΠ½ΠΈΠΊΠ° ΠΌΠΎΠΆΠ½ΠΎ ΠΎΠΏΡΠ΅Π΄Π΅Π»ΠΈΡΡ ΡΠ°ΡΡΠΈΡΡΠΎΠ²Π°Π² Π½Π°Π΄ΠΏΠΈΡΠΈ Π½Π° ΡΠ°ΠΌΠΎΠΉ ΠΎΠ±ΠΎΠΉΠΌΠ΅. Π¨Π₯15 ΡΠ°ΠΌΡΠΉ ΡΠ°ΡΠΏΡΠΎΡΡΡΠ°Π½ΡΠ½Π½ΡΠΉ Π²ΠΈΠ΄ ΡΡΠ°Π»ΠΈ Π΄Π»Ρ ΠΏΠΎΠ΄ΡΠΈΠΏΠ½ΠΈΠΊΠ°. Π‘ΡΠ°Π»Ρ Π΄Π»Ρ ΠΏΠΎΠ΄ΡΠΈΠΏΠ½ΠΈΠΊΠ° Π΄ΠΎΠ»ΠΆΠ½Π° Π±ΡΡΡ ΡΡΡΠΎΠΉΡΠΈΠ²ΠΎΠΉ ΠΊ ΠΈΠ·Π½ΠΎΡΡ ΠΈ ΠΈΠΌΠ΅Π½Π½ΠΎ ΠΏΠΎ-ΡΡΠΎΠΌΡ ΠΎΠ½Π° Π±ΠΎΠΈΡΡΡ ΡΠ΄Π°ΡΠ½ΠΎΠΉ Π½Π°Π³ΡΡΠ·ΠΊΠΈ, Π²Π΅Π΄Ρ ΠΏΠΎΠ΄ΡΠΈΠΏΠ½ΠΈΠΊ Π½Π΅ Π΄ΠΎΠ»ΠΆΠ΅Π½ ΠΈΡΠΏΡΡΡΠ²Π°ΡΡ ΡΠ΄Π°ΡΡ, ΠΏΠΎΡΡΠΎΠΌ ΡΡΠ°Π»Ρ ΠΎΠ±ΠΎΠΉΠΌΡ ΡΠ°ΠΊΠ°Ρ Ρ ΡΡΠΏΠΊΠ°Ρ.
ΠΡΡΡΡΡ ΡΠΏΠΎΡΡ, ΡΡΠΎ Π²Π½ΡΡΡΠ΅Π½Π½ΡΡ ΠΎΠ±ΠΎΠΉΠΌΠ° ΠΏΡΠΎΡΠ½Π΅Π΅ ΡΠ΅ΠΌ Π½Π°ΡΡΠΆΠ½Π°Ρ, ΠΏΠΎ ΠΌΠ½Π΅ ΡΡΠ°Π»Ρ Π² ΠΎΠ±Π΅ΠΈΡ ΠΎΠ±ΠΎΠΉΠΌΠ°Ρ ΠΎΠ΄ΠΈΠ½Π°ΠΊΠΎΠ²Π°Ρ, Π½ΠΎ Π²ΠΎΡ ΡΠ°ΡΠΈΠΊΠΈ ΠΈΠ»ΠΈ ΡΠΎΠ»ΠΈΠΊΠΈ Π² ΠΏΠΎΠ΄ΡΠΈΠΏΠ½ΠΈΠΊΠ΅ Π³ΠΎΡΠ°Π·Π΄ΠΎ ΠΏΡΠΎΡΠ½Π΅Π΅ ΡΠ°ΠΌΠΈΡ ΠΎΠ±ΠΎΠΉΠΌ. ΠΠ· ΡΠ°ΡΠΈΠΊΠΎΠ² ΠΏΠΎΠ΄ΡΠΈΠΏΠ½ΠΈΠΊΠ° ΡΠΎΠΆΠ΅ Π΄Π΅Π»Π°ΡΡ Π½ΠΎΠΆΠΈ. ΠΠΎΠ»ΡΡΠΈΠ΅ ΡΠ°ΡΠΈΠΊΠΈ, ΠΏΡΠΈΠ²Π°ΡΠΈΠ² ΠΊ Π½ΠΈΠΌ ΡΡΡΠΊΡ, ΡΠ°ΡΠΊΠΎΠ²ΡΠ²Π°ΡΡ Π² ΠΏΠΎΠ»ΠΎΡΡ, Π° ΠΌΠ΅Π»ΠΊΠΈΠ΅ ΡΠ²Π°ΡΠΈΠ²Π°ΡΡ Π² ΡΡΡΠ±Π΅ — ΡΠ°ΠΊΠΈΠ΅ Π½ΠΎΠΆΠΈ ΠΊΡΠ΅ΠΏΠΊΠΈΠ΅, ΠΈΠ·Π½ΠΎΡΠΎΡΡΠΎΠΉΠΊΠΈΠ΅ ΠΈ ΠΏΡΠΈ ΠΏΡΠ°Π²ΠΈΠ»ΡΠ½ΠΎΠΉ Π·Π°ΠΊΠ°Π»ΠΊΠ΅ Π΄Π΅ΡΠΆΠ°ΡΡ Ρ ΠΎΡΠΎΡΠΈΠ΅ ΡΠ΄Π°ΡΠ½ΡΠ΅ Π½Π°Π³ΡΡΠ·ΠΊΠΈ, Π½ΠΎ ΠΎ ΡΠ°ΠΊΠΈΡ Π½ΠΎΠΆΠ°Ρ ΠΌΡ ΠΏΠΎΠ³ΠΎΠ²ΠΎΡΠΈΠΌ ΠΏΠΎΠ·ΠΆΠ΅. Π ΡΠ°ΠΊ ΠΏΡΠΈΡΡΡΠΏΠ°Ρ ΠΊ ΠΊΠΎΠ²ΠΊΠ΅.
ΠΠΎΠ½Π°Π΄ΠΎΠ±ΠΈΡΡΡ
- ΠΠΎΠ»ΠΊΠ°ΡΠΊΠ°
- ΠΠ°ΠΆΠ΄Π°ΡΠ½Π°Ρ Π±ΡΠΌΠ°Π³Π°
- ΠΠ±ΠΎΠΉΠΌΠ° ΠΏΠΎΠ΄ΡΠΈΠΏΠ½ΠΈΠΊΠ°
- ΠΡΠ·Π½Ρ
ΠΠ΅ΡΠ΅Π΄ ΠΊΠΎΠ²ΠΊΠΎΠΉ Ρ Π·Π°ΡΠ°Π½Π΅Π΅ ΠΎΠ±ΠΆΠΎΠ³ ΠΏΡΠΈ ΡΠ΅ΠΌΠΏΠ΅ΡΠ°ΡΡΡΠ΅ ΡΠ°Π·ΠΌΠ°Π³Π½ΠΈΡΠΈΠ²Π°Π½ΠΈΡ, ΡΠ°ΠΊ ΠΌΠ΅ΡΠ°Π» ΠΏΠΎΡΠ΅ΡΡΠ΅Ρ ΡΠ²ΠΎΡ Π·Π°ΠΊΠ°Π»ΠΊΡ ΠΈ ΡΡΠ°Π½Π΅Ρ ΠΌΡΠ³ΠΊΠΈΠΌ Π΄Π»Ρ ΠΊΠΎΠ²ΠΊΠΈ. Π¨Π₯15 Π½Π΅ Π»ΡΠ±ΠΈΡ ΠΏΠ΅ΡΠ΅Π³ΡΠ΅Π²Π° ΠΈ ΠΈΠΌΠ΅Π½Π½ΠΎ ΠΏΠΎ-ΡΡΠΎΠΌΡ Ρ ΠΏΡΠΎΠΈΠ·Π²ΠΎΠΆΡ ΠΊΠΎΠ²ΠΊΡ ΠΏΡΠΈ Π½ΠΈΠ·ΠΊΠΈΡ ΡΠ΅ΠΌΠΏΠ΅ΡΠ°ΡΡΡΠ°Ρ — ΡΡΠΎ Π² ΠΏΡΠ΅Π΄Π΅Π»Π°Ρ 500 ΠΈΠ»ΠΈ 600Β°C. ΠΡΠΈ ΠΎΡΡΡΠ²Π°Π½ΠΈΠΈ ΡΡΠ°Π·Ρ Π½Π°Π³ΡΠ΅Π²Π°Ρ Π΅ΡΠ΅ ΡΠ°Π·, Π¨Π₯15 Π½Π΅Π»ΡΠ·Ρ ΠΊΠΎΠ²Π°ΡΡ Π½Π° ΡΠΈΠ»ΡΠ½ΠΎ ΠΎΡΡΡΠ²ΡΡΡ ΠΈΠ½Π°ΡΠ΅ ΠΎΠ½Π° Π΄Π°ΡΡ ΡΡΠ΅ΡΠΈΠ½Ρ ΠΈ Π½ΠΎΠΆ Π±ΡΠ΄Π΅Ρ ΠΈΡΠΏΠΎΡΡΠ΅Π½.
ΠΠ΅Π·Π²ΠΈΠ΅ ΡΠ΅ΡΠΈΠ» ΡΠ΄Π΅Π»Π°ΡΡ ΠΏΠΎΡΠΈΡΠ΅, Π° Ρ
Π²ΠΎΡΡΠΎΠ²ΠΈΠΊ ΠΏΠΎ ΠΌΠ΅Π½ΡΡΠ΅, ΡΡΠΊΠΎΡΡΡ Π±ΡΠ΄Π΅Ρ Π²ΡΠ°Π΄Π½ΠΎΠΉ. ΠΠ°Π³ΡΠ΅Π²Π°Ρ Π΄ΠΎ ΡΠ²Π΅ΡΠ»ΠΎ-Π²ΠΈΡΠ½ΡΠ²ΠΎΠ³ΠΎ ΡΠ²Π΅ΡΠ° ΠΈ ΡΠ°ΡΠΏΡΡΠΌΠ»ΡΡ ΠΏΠΎΠ΄ΡΠΈΠΏΠ½ΠΈΠΊ. ΠΠΎΡΠ»Π΅ ΡΠΎΠ³ΠΎ, ΠΊΠ°ΠΊ ΡΠ°ΡΠΏΡΡΠΌΠΈΠ», Π½Π°ΡΠΈΠ½Π°ΡΡ ΠΊΠΎΠ²Π°ΡΡ Π»Π΅Π·Π²ΠΈΠ΅ ΡΠ°ΠΊ, ΠΊΠ°ΠΊ ΠΏΠΎΠ΄ΡΠΈΠΏΠ½ΠΈΠΊ ΠΌΠ°Π»Π΅Π½ΡΠΊΠΎΠ³ΠΎ Π΄ΠΈΠ°ΠΌΠ΅ΡΡΠ° ΡΡΠ°Π·Ρ ΠΊΡΡ Π΄ΠΎ 2 ΠΌΠΌ ΡΠΎΠ»ΡΠΈΠ½Ρ. ΠΠΎΡΠ»Π΅ ΡΠ°ΡΠΊΠΎΠ²ΠΊΠΈ Π»Π΅Π·Π²ΠΈΡ ΠΊΡΡ ΡΠΎΡΠΌΡ Ρ
Π²ΠΎΡΡΠΎΠ²ΠΈΠΊΠ° Π΄ΠΎ Π½ΡΠΆΠ½ΠΎΠΉ Π΄Π»ΠΈΠ½Ρ. ΠΠ° 8 Π½Π°Π³ΡΠ΅Π²ΠΎΠ² Ρ ΠΏΠΎΠ»Π½ΠΎΡΡΡΡ ΡΠ°ΡΠΊΠΎΠ²Π°Π» ΠΏΡΠΈΠΌΠ΅ΡΠ½ΡΡ ΡΠΎΡΠΌΡ Π½ΠΎΠΆΠ°.
Π’Π°ΠΊ ΠΊΠ°ΠΊ Π½ΠΎΠΆ ΡΡΠ°Π·Ρ ΡΠ°ΡΠΊΠΎΠ²Π°Π½ Π΄ΠΎ Π½ΡΠΆΠ½ΠΎΠΉ ΡΠΎΠ»ΡΠΈΠ½Ρ, ΡΡΠ°Π·Ρ ΠΏΠΎΡΠ»Π΅ ΠΊΠΎΠ²ΠΊΠΈ ΠΏΡΠΎΠΈΠ·Π²ΠΎΠΆΡ Π·Π°ΠΊΠ°Π»ΠΊΡ Π»Π΅Π·Π²ΠΈΡ. Π ΡΠ΅ΡΠΈ Π½Π°ΡΠ΅Π» ΠΌΠ΅ΡΠΎΠ΄ Π·Π°ΠΊΠ°Π»ΠΊΠΈ Π¨Π₯15 Π² ΡΠΎΠ»ΡΡΠΊΠ΅ ΠΈ ΡΠ΅ΡΠΈΠ» ΠΏΠΎΡΠΊΡΠΏΠ΅ΡΠΈΠΌΠ΅Π½ΡΠΈΡΠΎΠ²Π°ΡΡ, Π½Π°Π»ΠΈΠ» Π² ΠΏΠΎΡΡΠ΄Ρ ΠΏΠΎΠ΄ΠΎΠ³ΡΠ΅ΡΡΡ ΡΠΎΠ»ΡΡΠΊΡ, Π° ΡΠ²Π΅ΡΡ Ρ Π³ΡΠ°ΠΌΠΌ Π΄Π΅ΡΡΡΡ ΠΌΠ°ΡΠ΅Π», Π½Π°Π³ΡΠ΅Π» Π½ΠΎΠΆ Π΄ΠΎ ΡΠ°Π·ΠΌΠ°Π³Π½ΠΈΡΠΈΠ²Π°Π½ΠΈΡ ΠΈ Π·Π°ΠΊΠ°Π»ΠΈΠ» Π½ΠΎΠΆ, ΠΏΡΠΎΠ²Π΅ΡΠΈΠ» Π½Π° ΡΡΠ΅ΠΊΠ»Π΅, Π½ΠΎ Π½ΠΎΠΆ Π½Π΅ ΡΠ°ΡΠ°ΠΏΠ°Π΅Ρ, ΠΏΡΠΎΠΈΠ·Π²Π΅Π» Π·Π°ΠΊΠ°Π»ΠΊΡ Π΅ΡΠ΅ ΡΠ°Π·, ΡΠΎΠ»ΡΠΊΠΎ Π½Π°Π³ΡΠ΅Π² ΠΏΡΠΎΠ²Π΅ΡΡΠ» ΡΠΆΠ΅ ΡΠΎΠ»ΡΡ, Π²Π΅Π΄Ρ ΠΏΠΎΠ²Π°ΡΠ΅Π½Π½Π°Ρ ΡΠΎΠ»Ρ ΠΏΠ»Π°Π²ΠΈΡΡΡ Π² ΡΠ°ΠΉΠΎΠ½Π΅ 800Β°C, ΠΏΠΎΡΠ»Π΅ ΡΠΎΠ³ΠΎ ΠΊΠ°ΠΊ Π½Π°Π³ΡΠ΅Π», ΠΎΠΊΡΠ½ΡΠ» Π² ΡΠΎΠ»ΡΡΠΊΡ — Π΄ΡΡΠ·ΡΡ Π±ΡΠ΄ΡΡΠ΅ Π²Π½ΠΈΠΌΠ°ΡΠ΅Π»ΡΠ½Ρ: ΡΠΎΠ»ΡΡΠΊΠ° ΠΎΡΠ΅Π½Ρ Ρ ΠΎΡΠΎΡΠΎ Π³ΠΎΡΠΈΡ ΠΏΡΠΈ Π·Π°ΠΊΠ°Π»ΠΊΠ΅. ΠΡΠΎΠ²Π΅ΡΠΈΠ» Π½Π° ΡΡΠ΅ΠΊΠ»Π΅ Π²ΡΠ΅ Π²ΡΠΎΠ΄Π΅ ΡΠ°ΡΠ°ΠΏΠ°Π΅Ρ.
ΠΡΠΊΠ»ΡΡΠ°Ρ Π³ΠΎΡΠ½ ΠΈ ΠΎΡΡΠ°Π²Π»ΡΡ Π½Π° ΠΏΠΎΡΡΠΈ ΠΏΡΠΎΠ³ΠΎΡΠ΅Π²ΡΠΈΡ ΡΠ³Π»ΡΡ , ΡΠ°ΠΊ ΠΎΠ½ Ρ ΠΌΠ΅Π½Ρ ΠΏΡΠΎΠ»Π΅ΠΆΠ°Π» 2.5 ΡΠ°ΡΠ°, Π½Π°ΠΊΡΡΡΡΠΉ ΠΊΠΈΡΠΏΠΈΡΠ°ΠΌΠΈ, ΡΠ°ΠΊ Ρ ΠΏΡΠΎΠΈΠ·Π²Π΅Π» ΠΎΡΠΏΡΡΠΊ ΠΌΠ΅ΡΠ°Π»Π»Π°. Π₯ΠΎΡΠΎΡΠΎ ΡΠ°ΠΊ ΡΠ°Π·ΠΌΠ°Ρ Π½ΡΠ»ΡΡ ΠΈ ΠΊΠΈΠ½ΡΠ» ΠΎΠ± ΠΏΠΎΠ» Π½ΠΎΠΆ, Π° ΠΎΠ½ Π²ΡΠΆΠΈΠ». ΠΡ Π²ΠΎΡ Π² ΠΊΡΠ·Π½Π΅ Π²ΡΠ΅ Π΄Π΅Π»Π° Π·Π°Π²Π΅ΡΡΠ΅Π½Ρ ΠΏΡΠΈΡΡΡΠΏΠ°Ρ ΠΊ ΡΠ»Π΅ΡΠ°ΡΠ½ΡΠΌ ΡΠ°Π±ΠΎΡΠ°ΠΌ.





ΠΠ° Π³ΡΠΈΠ½Π΄Π΅ΡΠ΅ ΡΠ»ΠΈΡΡΡ Π²ΡΡ ΠΏΠΎΠ²Π΅ΡΡ Π½ΠΎΡΡΡ Π½ΠΎΠΆΠ° ΠΈ Π²ΡΠ²ΠΎΠΆΡ Π½ΡΠΆΠ½ΡΡ ΡΠΎΡΠΌΡ ΠΊΠ»ΠΈΠ½ΠΊΠ°. ΠΠ°Π»Π΅Π΅ ΠΏΠΎΠΌΠ΅Π½ΡΠ² Π½Π°ΠΆΠ΄Π°ΡΠ½ΡΡ Π±ΡΠΌΠ°Π³Ρ Π½Π° Π±ΠΎΠ»Π΅Π΅ ΠΌΠ΅Π»ΠΊΡΡ, ΡΠΎΡΠΌΠΈΡΡΡ ΠΊΠ»ΠΈΠ½, ΠΏΠΎΡΠ»Π΅ Π·Π°ΡΠ°ΡΠΈΠ²Π°Ρ Π½Π° ΡΠΈΠ»ΠΊΠ΅. ΠΠΎΠ»ΠΎΡΠ½ΠΎ Π»Π΅Π·Π²ΠΈΡ Π½Π΅ ΡΡΠ°Π» ΡΠ»ΠΈΡΠΎΠ²Π°ΡΡ Π² Π·Π΅ΡΠΊΠ°Π»ΠΎ, ΠΏΡΠΎΡΡΠΎ ΡΠ±ΡΠ°Π» ΠΊΡΡΠΏΠ½ΡΠ΅ ΡΠΈΡΠΊΠΈ 120 ΠΈ 400 Π±ΡΠΌΠ°Π³ΠΎΠΉ, Π²Π΅Π΄Ρ Π½ΠΎΠΆ Π΄Π»Ρ Ρ ΠΎΠ·ΡΠΉΡΡΠ²Π΅Π½Π½ΡΡ Π½ΡΠΆΠ΄. Π’Π΅ΠΏΠ΅ΡΡ ΠΏΡΠΈΡΡΡΠΏΠ°Ρ ΠΊ ΡΡΠΊΠΎΡΡΠΈ.


ΠΠ»Ρ ΡΡΠΊΠΎΡΡΠΈ Π²Π·ΡΠ» ΡΠ°ΠΌΠΎΠ΅ ΡΠ°ΡΠΏΡΠΎΡΡΡΠ°Π½ΡΠ½Π½ΠΎΠ΅ Π΄Π΅ΡΠ΅Π²ΠΎ Π±Π΅ΡΠ΅Π·Ρ. ΠΡΡΠ΅Π·Π°Π² ΠΊΡΡΠΎΠΊ Π½ΡΠΆΠ½ΠΎΠΉ Π΄Π»ΠΈΠ½Ρ ΡΠ½ΠΈΠΌΠ°Ρ ΠΊΠΎΡΡ Π½Π° ΡΡΠ°Π½ΠΊΠ΅ ΡΠ½ΠΈΠΌΠ°Ρ Π²ΡΠ΅ Π»ΠΈΡΠ½Π΅Π΅. Π ΡΠ΅Π½ΡΡΠ΅ ΠΏΡΠΎΡΠ²Π΅ΡΠ»ΠΈΠ²Π°Ρ ΠΎΡΠ²Π΅ΡΡΡΠΈΠ΅ Π·Π°Π»ΠΈΠ² Π² Π½Π΅Π³ΠΎ ΠΊΠ»Π΅ΠΉ Π·Π°Π±ΠΈΠ²Π°Ρ Ρ Π²ΠΎΡΡΠΎΠ²ΠΈΠΊ ΠΈ ΠΎΡΡΠ°Π²Π»ΡΡ Π½Π° Π½ΠΎΡΡ ΠΏΠΎΠ΄ ΠΏΡΠ΅ΡΡΠΎΠΌ ΡΠΎΡ Π½ΡΡΡ. ΠΠ° ΡΠ»Π΅Π΄ΡΡΡΠΈΠΉ Π΄Π΅Π½Ρ Π²ΡΠ΅ ΡΠΊΠ»Π΅Π΅Π½ΠΎ, ΠΏΡΠΈΡΡΡΠΏΠ°Ρ ΠΊ ΡΠ»ΠΈΡΠΎΠ²ΠΊΠ΅ Π½Π° ΠΡΠΈΠ½Π΄Π΅ΡΠ΅. ΠΡΠ΅Π΄Π°Π² Π½ΡΠΆΠ½ΡΡ ΡΠΎΡΠΌΡ ΡΡΡΠΊΠ΅ — ΡΠ»ΠΈΡΡΡ ΠΌΠ΅Π»ΠΊΠΎΠΉ Π½Π°ΠΆΠ΄Π°ΡΠ½ΠΎΠΉ. Π Π°ΡΡΠΎΠΏΠΈΠ² Π²ΠΎΡΠΊ Π½Π° ΠΏΠ°ΡΠΎΠ²ΠΎΠΉ Π±Π°Π½Π΅ ΠΏΡΠΎΠΏΠΈΡΡΠ²Π°Ρ ΡΡΡΠΊΡ 2 ΡΠ°ΡΠ°. ΠΠΎΡ ΠΈ Π²ΡΠ΅, ΠΏΠΎΡΠ»Π΅ ΠΏΡΠΎΠΏΠΈΡΠΊΠΈ Π²ΠΎΡΠΊΠΎΠΌ ΡΡΠΊΠΎΡΡΡ Π½Π΅ Π±ΠΎΠΈΡΡΡ Π²Π»Π°Π³ΠΈ.
ΠΡ Π²ΠΎΡ ΠΈ Π²ΡΠ΅ Π½ΠΎΠΆ Π³ΠΎΡΠΎΠ² Π±Π΅Π· Π·Π°ΡΡΠ°Ρ, Π° Π³Π»Π°Π²Π½ΠΎΠ΅ ΡΠ²ΠΎΠΈΠΌΠΈ ΡΡΠΊΠ°ΠΌΠΈ Π²ΡΠ΅ΠΌ ΡΠΏΠ°ΡΠΈΠ±ΠΎ Π·Π° Π²Π½ΠΈΠΌΠ°Π½ΠΈΠ΅ ΠΈ Π΄ΠΎ Π½ΠΎΠ²ΡΡ
Π‘Π°ΠΌΠΎΠ΄Π΅Π»ΠΎΠΊ Π΄ΡΡΠ·ΡΡ
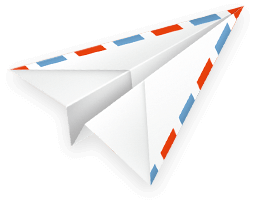
ΠΠΎΠ»ΡΡΠ°ΠΉΡΠ΅ Π½Π° ΠΏΠΎΡΡΡ ΠΏΠΎΠ΄Π±ΠΎΡΠΊΡ Π½ΠΎΠ²ΡΡ ΡΠ°ΠΌΠΎΠ΄Π΅Π»ΠΎΠΊ. ΠΠΈΠΊΠ°ΠΊΠΎΠ³ΠΎ ΡΠΏΠ°ΠΌΠ°, ΡΠΎΠ»ΡΠΊΠΎ ΠΏΠΎΠ»Π΅Π·Π½ΡΠ΅ ΠΈΠ΄Π΅ΠΈ!
*ΠΠ°ΠΏΠΎΠ»Π½ΡΡ ΡΠΎΡΠΌΡ Π²Ρ ΡΠΎΠ³Π»Π°ΡΠ°Π΅ΡΠ΅ΡΡ Π½Π° ΠΎΠ±ΡΠ°Π±ΠΎΡΠΊΡ ΠΏΠ΅ΡΡΠΎΠ½Π°Π»ΡΠ½ΡΡ Π΄Π°Π½Π½ΡΡ
Π‘ΡΠ°Π½ΠΎΠ²ΠΈΡΠ΅ΡΡ Π°Π²ΡΠΎΡΠΎΠΌ ΡΠ°ΠΉΡΠ°, ΠΏΡΠ±Π»ΠΈΠΊΡΠΉΡΠ΅ ΡΠΎΠ±ΡΡΠ²Π΅Π½Π½ΡΠ΅ ΡΡΠ°ΡΡΠΈ, ΠΎΠΏΠΈΡΠ°Π½ΠΈΡ ΡΠ°ΠΌΠΎΠ΄Π΅Π»ΠΎΠΊ Ρ ΠΎΠΏΠ»Π°ΡΠΎΠΉ Π·Π° ΡΠ΅ΠΊΡΡ. ΠΠΎΠ΄ΡΠΎΠ±Π½Π΅Π΅ Π·Π΄Π΅ΡΡ.ΠΠΎΠΆ ΠΈΠ· ΠΏΠΎΠ΄ΡΠΈΠΏΠ½ΠΈΠΊΠ° ΡΠ²ΠΎΠΈΠΌΠΈ ΡΡΠΊΠ°ΠΌΠΈ
ΠΠΎΠΏΡΠΎΡ Π·Π°Π΄Π°Π΅Ρ ΠΠ°Π»Π΅ΡΠΈΠΉ, ΠΠΎΡΠΊΠΎΠ²ΡΠΊΠ°Ρ ΠΎΠ±Π»Π°ΡΡΡ:
ΠΠ΅Π΄Π°Π²Π½ΠΎ ΡΡΠ»ΡΡΠ°Π» ΠΎΡ Π·Π½Π°ΠΊΠΎΠΌΠΎΠ³ΠΎ, ΡΡΠΎ ΠΈΠ· ΠΏΠΎΠ΄ΡΠΈΠΏΠ½ΠΈΠΊΠ° ΠΌΠΎΠΆΠ½ΠΎ ΠΈΠ·Π³ΠΎΡΠΎΠ²ΠΈΡΡ ΠΎΡΠ»ΠΈΡΠ½ΡΠΉ Π½ΠΎΠΆ. ΠΠ΅Π½Ρ ΠΎΡΠ΅Π½Ρ Π·Π°ΠΈΠ½ΡΠ΅ΡΠ΅ΡΠΎΠ²Π°Π»ΠΎ ΡΡΠΎ, ΠΏΠΎΡΠΊΠΎΠ»ΡΠΊΡ Π»ΡΠ±Π»Ρ Π²ΡΠ΅ ΠΌΠ°ΡΡΠ΅ΡΠΈΡΡ ΡΠ²ΠΎΠΈΠΌΠΈ ΡΡΠΊΠ°ΠΌΠΈ. Π₯ΠΎΡΠ΅Π»ΠΎΡΡ Π±Ρ ΠΏΠΎΠ΄ΡΠΎΠ±Π½Π΅Π΅ ΡΠ·Π½Π°ΡΡ ΠΎΠ± ΡΡΠΎΠΉ ΡΠ΅Ρ Π½ΠΎΠ»ΠΎΠ³ΠΈΠΈ.
ΠΡΠ΅Π΄ΠΎΡΡΠ°Π²Π»ΡΠ΅ΠΌ ΡΠ»ΠΎΠ²ΠΎ Π½Π°ΡΠ΅ΠΌΡ ΡΠΊΡΠΏΠ΅ΡΡΡ:
ΠΠΎΠ΄ΡΠΈΠΏΠ½ΠΈΠΊΠΈ ΠΈΠ·Π³ΠΎΡΠΎΠ²Π»ΡΡΡ ΠΈΠ· ΡΡΠ°Π»ΠΈ Π²ΡΡΠΎΠΊΠΎΠ³ΠΎ ΠΊΠ°ΡΠ΅ΡΡΠ²Π°, ΠΏΠΎΡΠΊΠΎΠ»ΡΠΊΡ ΠΎΠ½ΠΈ ΡΠ°Π±ΠΎΡΠ°ΡΡ Π² ΡΡΡΠ΄Π½ΡΡ ΡΡΠ»ΠΎΠ²ΠΈΡΡ ΠΈ Π½Π΅ ΡΠ΅ΡΡΡΡ ΡΠ²ΠΎΠΈΡ Ρ Π°ΡΠ°ΠΊΡΠ΅ΡΠΈΡΡΠΈΠΊ ΠΏΡΠΈ Π·Π½Π°ΡΠΈΡΠ΅Π»ΡΠ½ΡΡ Π½Π°Π³ΡΡΠ·ΠΊΠ°Ρ . ΠΡΠ»ΠΈ Π²ΡΠΊΠΎΠ²Π°ΡΡ ΠΈΠ· Π½Π΅Π³ΠΎ Π½ΠΎΠΆ, ΠΌΠΎΠΆΠ½ΠΎ ΠΏΠΎΠ»ΡΡΠΈΡΡ ΠΎΡΠ»ΠΈΡΠ½ΡΠΉ ΠΈΠ½ΡΡΡΡΠΌΠ΅Π½Ρ. ΠΠ½ Π½Π΅ ΠΏΠΎΡΠ΅ΡΡΠ΅Ρ ΠΎΡΡΡΠΎΡΡ Π² ΡΠ°ΠΌΡΡ ΡΡΡΠ΄Π½ΡΡ ΡΡΠ»ΠΎΠ²ΠΈΡΡ ΡΠΊΡΠΏΠ»ΡΠ°ΡΠ°ΡΠΈΠΈ.
ΠΠ»Ρ ΠΊΠΎΠ²ΠΊΠΈ Π½ΠΎΠΆΠ° ΠΈΠ· ΠΏΠΎΠ΄ΡΠΈΠΏΠ½ΠΈΠΊΠ° Π½Π΅ΠΎΠ±Ρ ΠΎΠ΄ΠΈΠΌΠΎ ΡΠ»Π΅Π΄ΠΎΠ²Π°ΡΡ ΠΏΡΠ΅Π΄ΡΡΠ°Π²Π»Π΅Π½Π½ΠΎΠΉ ΠΈΠ½ΡΡΡΡΠΊΡΠΈΠΈ:
- ΠΡΠΈ ΠΏΠΎΠΌΠΎΡΠΈ Π±ΠΎΠ»Π³Π°ΡΠΊΠΈ Π½Π΅ΠΎΠ±Ρ ΠΎΠ΄ΠΈΠΌΠΎ ΠΎΡΡΠ΅Π·Π°ΡΡ Π·Π°Π³ΠΎΡΠΎΠ²ΠΊΡ Π½ΡΠΆΠ½ΠΎΠΉ Π΄Π»ΠΈΠ½Ρ, ΠΈΡΠΏΠΎΠ»ΡΠ·ΡΡ ΠΎΠ±ΠΎΠΉΠΌΡ ΠΏΠΎΠ΄ΡΠΈΠΏΠ½ΠΈΠΊΠ°. ΠΡΠΆΠ½ΠΎ ΡΡΠΈΡΡΠ²Π°ΡΡ Π·Π°ΠΏΠ°Ρ Π² 1-2 ΡΠΌ.
- ΠΠΎΠ»ΡΡΠ΅Π½Π½ΡΡ Π·Π°Π³ΠΎΡΠΎΠ²ΠΊΡ Π½Π΅ΠΎΠ±Ρ ΠΎΠ΄ΠΈΠΌΠΎ ΠΏΡΠΈΠ²Π°ΡΠΈΡΡ ΠΊ ΠΏΡΡΡΠΊΡ Π°ΡΠΌΠ°ΡΡΡΡ, ΠΈΡΠΏΠΎΠ»Π½ΡΡΡΠ΅ΠΉ ΡΠΎΠ»Ρ ΡΡΠΊΠΎΡΡΠΊΠΈ.
- ΠΠΎΠ²ΠΊΠ° ΠΎΡΡΡΠ΅ΡΡΠ²Π»ΡΠ΅ΡΡΡ ΠΏΡΠΈ Π΄ΠΎΡΡΠ°ΡΠΎΡΠ½ΠΎ Π½ΠΈΠ·ΠΊΠΈΡ ΡΠ΅ΠΌΠΏΠ΅ΡΠ°ΡΡΡΠ°Ρ , ΡΡΠΎΠ±Ρ ΠΌΠ°ΡΠ΅ΡΠΈΠ°Π» ΠΈΠ·ΠΌΠ΅Π½ΠΈΠ»ΡΡ ΠΎΡ ΡΠ²Π΅ΡΠ»ΠΎ-ΠΊΡΠ°ΡΠ½ΠΎΠ³ΠΎ Π΄ΠΎ Π±ΠΎΠ»Π΅Π΅ ΡΠ΅ΠΌΠ½ΠΎΠ³ΠΎ ΠΎΡΡΠ΅Π½ΠΊΠ°.
- ΠΠ΅ΡΠ΅Π΄ Π·Π°ΠΊΠ°Π»ΠΊΠΎΠΉ ΠΎΡΡΡΠ΅ΡΡΠ²Π»ΡΠ΅ΡΡΡ ΠΎΠ±Π΄ΠΈΡΠΊΠ° Π½Π° ΡΠΎΡΠΈΠ»Π΅ ΠΈΠ»ΠΈ ΠΏΡΠΈ ΠΏΠΎΠΌΠΎΡΠΈ Π½Π°ΠΏΠΈΠ»ΡΠ½ΠΈΠΊΠ°.
- ΠΠ»Ρ ΡΠ»ΡΡΡΠ΅Π½ΠΈΡ Ρ Π°ΡΠ°ΠΊΡΠ΅ΡΠΈΡΡΠΈΠΊ Π½ΠΎΠΆΠ° ΡΠ΅ΠΊΠΎΠΌΠ΅Π½Π΄ΡΠ΅ΡΡΡ ΠΏΡΠΎΠΈΠ·Π²Π΅ΡΡΠΈ Π½ΠΎΡΠΌΠ°Π»ΠΈΠ·Π°ΡΠΈΡ ΠΌΠ΅ΡΠ°Π»Π»Π°. ΠΠ»Ρ ΡΡΠΎΠ³ΠΎ Π΅Π³ΠΎ ΡΠ°Π·ΠΎΠ³ΡΠ΅Π²Π°ΡΡ Π΄ΠΎ 750Β°Π‘, ΠΆΠ΄ΡΡ 5 ΠΌΠΈΠ½ΡΡ ΠΈ ΠΎΡ Π»Π°ΠΆΠ΄Π°ΡΡ Π½Π° Π²ΠΎΠ·Π΄ΡΡ Π΅. Π’Π°ΠΊΠΈΠ΅ ΠΌΠ°Π½ΠΈΠΏΡΠ»ΡΡΠΈΠΈ ΠΏΠΎΠ²ΡΠΎΡΡΡΡ 2-4 ΡΠ°Π·Π°.
- ΠΡΠΎΠΈΠ·Π²ΠΎΠ΄ΠΈΡΡΡ Π·Π°ΠΊΠ°Π»ΠΊΠ°. Π§Π°ΡΠ΅ Π²ΡΠ΅Π³ΠΎ ΡΡΠΎ ΠΎΡΡΡΠ΅ΡΡΠ²Π»ΡΠ΅ΡΡΡ ΠΏΡΠΈ ΡΠ΅ΠΌΠΏΠ΅ΡΠ°ΡΡΡΠ΅ 830Β°Π‘. ΠΠ»Ρ ΠΎΠΏΡΠ΅Π΄Π΅Π»Π΅Π½ΠΈΡ ΠΏΠΎΠ΄Ρ ΠΎΠ΄ΡΡΠ΅Π³ΠΎ ΠΌΠΎΠΌΠ΅Π½ΡΠ° Π΄Π»Ρ Π·Π°ΠΊΠ°Π»ΠΊΠΈ ΠΈΡΠΏΠΎΠ»ΡΠ·ΡΡΡ ΠΌΠ°Π³Π½ΠΈΡ. ΠΠΎΠ³Π΄Π° ΡΡΠ°Π»Ρ ΠΏΠ΅ΡΠ΅ΡΡΠ°Π»Π° ΠΌΠ°Π³Π½ΠΈΡΠΈΡΡΡΡ, ΠΌΠΎΠΆΠ½ΠΎ ΠΏΡΠΈΡΡΡΠΏΠ°ΡΡ ΠΊ Π΄Π°Π½Π½ΠΎΠΌΡ ΠΏΡΠΎΡΠ΅ΡΡΡ. Π’Π΅ΠΌΠΏΠ΅ΡΠ°ΡΡΡΠ° ΠΏΠ»Π°Π²Π»Π΅Π½ΠΈΡ ΠΏΠΎΠ²Π°ΡΠ΅Π½Π½ΠΎΠΉ ΡΠΎΠ»ΠΈ ΡΠΎΡΡΠ°Π²Π»ΡΠ΅Ρ 800Β°Π‘. ΠΠΎΡΡΠΎΠΌΡ Π΅Ρ ΠΏΠΎΡΡΠΏΠ°ΡΡ Π·Π°Π³ΠΎΡΠΎΠ²ΠΊΡ, ΡΡΠΎΠ±Ρ ΠΏΡΠΈΠΌΠ΅ΡΠ½ΠΎ ΠΎΠΏΡΠ΅Π΄Π΅Π»ΠΈΡΡ ΠΌΠΎΠΌΠ΅Π½Ρ Π΄ΠΎΡΡΠΈΠΆΠ΅Π½ΠΈΡ ΠΎΠΏΡΠΈΠΌΠ°Π»ΡΠ½ΡΡ Ρ Π°ΡΠ°ΠΊΡΠ΅ΡΠΈΡΡΠΈΠΊ Π΄Π»Ρ Π·Π°ΠΊΠ°Π»ΠΊΠΈ.
- ΠΠ°ΠΊΠ°Π»ΠΊΠ° ΠΏΡΠΎΠΈΡΡ ΠΎΠ΄ΠΈΡ Π² ΠΌΠ°ΡΠ»Π΅, ΡΠ΅ΠΌΠΏΠ΅ΡΠ°ΡΡΡΠ° ΠΊΠΎΡΠΎΡΠΎΠ³ΠΎ Π΄ΠΎΡΡΠΈΠ³Π°Π΅Ρ 50-60Β°Π‘. ΠΠ°Π³ΠΎΡΠΎΠ²ΠΊΡ ΠΏΠΎΠΌΠ΅ΡΠ°ΡΡ Π² Π΅ΠΌΠΊΠΎΡΡΡ Ρ ΠΏΠΎΠ΄Π³ΠΎΡΠΎΠ²Π»Π΅Π½Π½ΡΠΌ Π²Π΅ΡΠ΅ΡΡΠ²ΠΎΠΌ Π½Π° 1 ΡΠ°Ρ. ΠΡΠ΅ ΡΡΠΎ Π²ΡΠ΅ΠΌΡ Π΅Π΅ Π½Π΅Π»ΡΠ·Ρ ΡΠ΅Π²Π΅Π»ΠΈΡΡ ΠΈ ΠΏΡΠΈΡΠ»ΠΎΠ½ΡΡΡ ΠΊ ΡΡΠ΅Π½ΠΊΠ°ΠΌ ΡΠ΅Π·Π΅ΡΠ²ΡΠ°ΡΠ°.
- ΠΠΎΡΠ»Π΅ Π·Π°ΠΊΠ°Π»ΠΊΠΈ ΠΏΡΠΎΠ²ΠΎΠ΄ΡΡ ΠΎΡΠΏΡΡΠΊ. ΠΠΎΠΆ ΠΏΠΎΠΌΠ΅ΡΠ°ΡΡ Π² Π΄ΡΡ ΠΎΠ²ΠΊΡ ΠΏΡΠΈ ΡΠ΅ΠΌΠΏΠ΅ΡΠ°ΡΡΡΠ΅ 160-200Β°Π‘ Π½Π° 2 ΡΠ°ΡΠ°. ΠΠ»Ρ ΠΎΡ Π»Π°ΠΆΠ΄Π΅Π½ΠΈΡ ΠΏΡΠΎΡΡΠΎ Π³Π°ΡΡΡ ΠΎΠ³ΠΎΠ½Ρ.
- ΠΠ»Ρ Π·Π°ΡΠΎΡΠΊΠΈ Π½ΠΎΠΆΠ° ΠΈΡΠΏΠΎΠ»ΡΠ·ΡΠ΅ΡΡΡ Π°Π»ΠΌΠ°Π·Π½ΡΠ΅ Π±ΡΡΡΠΊΠΈ, Π΄Π»Ρ ΡΠ»ΠΈΡΠΎΠ²ΠΊΠΈ β Π°Π»ΠΌΠ°Π·Π½Π°Ρ ΠΏΠ°ΡΡΠ°. Π ΠΏΡΠΎΡΠ΅ΡΡΠ΅ Π΄Π°Π½Π½ΠΎΠΉ ΠΎΠ±ΡΠ°Π±ΠΎΡΠΊΠΈ ΠΌΠΎΠΆΠ΅Ρ ΡΡΡΠ°ΡΠΈΡΡΡΡ Π΄ΠΎ 2 ΠΌΠΌ ΡΠΎΠ»ΡΠΈΠ½Ρ Π·Π°Π³ΠΎΡΠΎΠ²ΠΊΠΈ, ΡΡΠΎ Π²ΠΏΠΎΠ»Π½Π΅ Π½ΠΎΡΠΌΠ°Π»ΡΠ½ΠΎ.
ΠΡΠ»ΠΈ ΡΠ»Π΅Π΄ΠΎΠ²Π°ΡΡ Π²ΡΠ΅ ΠΏΡΠ°Π²ΠΈΠ»ΡΠ½ΠΎ ΠΈ Π² ΡΠΎΡΠ½ΠΎΡΡΠΈ ΡΠ»Π΅Π΄ΠΎΠ²Π°ΡΡ ΠΈΠ½ΡΡΡΡΠΊΡΠΈΠΈ, ΠΏΠΎΠ»ΡΡΠ΅Π½Π½ΡΠΉ Π½ΠΎΠΆ ΡΠΌΠΎΠΆΠ΅Ρ ΠΏΠΎΡΠ°ΡΠ°ΠΏΠ°ΡΡ ΡΡΠ΅ΠΊΠ»ΠΎ. Π ΠΏΡΠΎΡΠ΅ΡΡΠ΅ ΡΠΊΡΠΏΠ»ΡΠ°ΡΠ°ΡΠΈΠΈ ΠΎΠ½ Π½Π΅ ΡΡΠΏΠΈΡΡΡ ΠΈ Π½Π΅ ΡΠ°Π·ΡΡΡΠ°Π΅ΡΡΡ ΠΏΡΠΈ Π½Π°Π³ΡΡΠ·ΠΊΠ°Ρ ΠΈΠ·Π³ΠΈΠ±Π°ΡΡΠ΅Π³ΠΎ Ρ Π°ΡΠ°ΠΊΡΠ΅ΡΠ°. ΠΡΠ΅Π΄ΡΡΠ°Π²Π»Π΅Π½Π½ΡΠΌ ΡΠΏΠΎΡΠΎΠ±ΠΎΠΌ Π»Π΅Π³ΡΠ΅ Π²ΡΠ΅Π³ΠΎ Π΄Π΅Π»Π°ΡΡ Π½ΠΎΠΆ Ρ Π½Π°ΠΊΠ»Π°Π΄Π½ΡΠΌΠΈ ΡΡΠΊΠΎΡΡΠΊΠ°ΠΌΠΈ.
ΠΠΈΠ΄Π΅ΠΎ: ΠΠΎΠ²ΠΊΠ° Π½ΠΎΠΆΠ° ΠΈΠ· ΡΠ°ΡΠΈΠΊΠ° ΠΎΡ ΠΏΠΎΠ΄ΡΠΈΠΏΠ½ΠΈΠΊΠ°
ΠΠ°ΠΊ ΡΠ΄Π΅Π»Π°ΡΡ Π½ΠΎΠΆ ΠΈΠ· ΠΏΠΎΠ΄ΡΠΈΠΏΠ½ΠΈΠΊΠ°
ΠΠ»Ρ ΡΠΎΠ³ΠΎ ΡΡΠΎ Π±Ρ ΡΠ΄Π΅Π»Π°ΡΡ Π½ΠΎΠΆ ΠΈΠ· ΠΏΠΎΠ΄ΡΠΈΠΏΠ½ΠΈΠΊΠ° ΠΏΡΠΈΠ΄Π΅ΡΡΡ ΠΏΠΎΡΡΡΠ΄ΠΈΡΡΡΡ. ΠΡΠ»ΠΈ ΡΠ°ΠΌΠΎΠ΄Π΅Π»ΡΠ½ΡΠΉ Π½ΠΎΠΆ ΠΈΠ· ΡΠ΅ΡΡΠΎΡΡΒ ΠΌΠΎΠΆΠ½ΠΎ ΠΈΠ·Π³ΠΎΡΠΎΠ²ΠΈΡΡ ΠΏΡΡΠ΅ΠΌ ΠΎΡΠΏΡΡΠΊΠ°, ΠΌΠ΅Ρ Π°Π½ΠΈΡΠ΅ΡΠΊΠΎΠΉ ΠΎΠ±ΡΠ°Π±ΠΎΡΠΊΠΈ ΠΌΠ΅ΡΠ°Π»Π»Π° ΠΈ ΠΏΠΎΡΠ»Π΅Π΄ΡΡΡΠ΅ΠΉ Π·Π°ΠΊΠ°Π»ΠΊΠΈ, ΡΠΎ Π½ΠΎΠΆ ΠΈΠ· ΠΏΠΎΠ΄ΡΠΈΠΏΠ½ΠΈΠΊΠ° ΠΌΠΎΠΆΠ½ΠΎ ΡΠΎΠ»ΡΠΊΠΎ ΡΠΊΠΎΠ²Π°ΡΡ.
ΠΠ΅Π»ΠΎ Π² ΡΠΎΠΌ, ΡΡΠΎ ΠΎΠ±ΠΎΠΉΠΌΠ° ΠΏΠΎΠ΄ΡΠΈΠΏΠ½ΠΈΠΊΠ° ΠΊΡΡΠ³Π»Π°Ρ, Π° ΡΠ°ΡΠΏΡΡΠΌΠΈΡΡ Π΅Π΅ Π½Π° ΠΏΠΎΠ»ΠΎΡΠΊΡ ΠΌΠ΅ΡΠ°Π»Π»Π° ΠΌΠΎΠΆΠ½ΠΎ ΡΠΎΠ»ΡΠΊΠΎ Ρ ΠΏΠΎΠΌΠΎΡΡΡ ΠΊΠΎΠ²ΠΊΠΈ.
ΠΠ»Ρ ΠΈΠ·Π³ΠΎΡΠΎΠ²Π»Π΅Π½ΠΈΡ Π½ΠΎΠΆΠ° ΡΠ²ΠΎΠΈΠΌΠΈ ΡΡΠΊΠ°ΠΌΠΈ ΠΌΠΎΠΆΠ½ΠΎ ΠΈΡΠΏΠΎΠ»ΡΠ·ΠΎΠ²Π°ΡΡ Π½Π΅ ΡΠΎΠ»ΡΠΊΠΎ ΠΎΠ±ΠΎΠΉΠΌΡ ΠΏΠΎΠ΄ΡΠΈΠΏΠ½ΠΈΠΊΠ°, Π½ΠΎ ΠΈ ΡΠ°ΡΠΈΠΊΠΈ ΠΈΠ»ΠΈ ΡΠΎΠ»ΠΈΠΊΠΈ ΠΈΠ· Π½Π΅Π³ΠΎ.
ΠΠΎΠ΄ΡΠΈΠΏΠ½ΠΈΠΊΠΎΠ²Π°Ρ ΡΡΠ°Π»Ρ ΠΎΡΠ΅Π½Ρ Ρ ΠΎΡΠΎΡΠ΅Π³ΠΎ ΠΊΠ°ΡΠ΅ΡΡΠ²Π°, Π²Π΅Π΄Ρ ΠΏΠΎΠ΄ΡΠΈΠΏΠ½ΠΈΠΊΠΈ ΡΠ°Π±ΠΎΡΠ°ΡΡ Π² ΠΎΡΠ΅Π½Ρ ΠΆΠ΅ΡΡΠΊΠΈΡ ΡΡΠ»ΠΎΠ²ΠΈΡΡ ΠΈ ΠΏΠΎΠ΄ Π±ΠΎΠ»ΡΡΠΎΠΉ Π½Π°Π³ΡΡΠ·ΠΊΠΎΠΉ, ΡΠ°ΠΊ ΡΡΠΎ Π»Π΅Π·Π²ΠΈΠ΅ Π½ΠΎΠΆΠ° ΠΎΡΠΊΠΎΠ²Π°Π½Π½ΠΎΠ³ΠΎ ΠΈΠ· ΠΏΠΎΠ΄ΡΠΈΠΏΠ½ΠΈΠΊΠ° ΠΏΠΎΠ»ΡΡΠ°Π΅ΡΡΡ Ρ Ρ ΠΎΡΠΎΡΠΈΠΌΠΈ ΠΌΠ΅Ρ Π°Π½ΠΈΡΠ΅ΡΠΊΠΈΠΌΠΈ ΡΠ²ΠΎΠΉΡΡΠ²Π°ΠΌΠΈ. Π’Π°ΠΊΠΎΠ΅ Π»Π΅Π·Π²ΠΈΠ΅ Ρ ΠΎΡΠΎΡΠΎ Π΄Π΅ΡΠΆΠΈΡ Π·Π°ΡΠΎΡΠΊΡ ΠΈ Π½Π΅ Π»ΠΎΠΌΠ°Π΅ΡΡΡ.
ΠΠΎΡΠΌΠΎΡΡΠΈΡΠ΅ Π²ΠΈΠ΄Π΅ΠΎ — ΠΈΠ·Π³ΠΎΡΠΎΠ²Π»Π΅Π½ΠΈΠ΅ Π½ΠΎΠΆΠ° ΠΈΠ· ΠΏΠΎΠ΄ΡΠΈΠΏΠ½ΠΈΠΊΠ° ΠΌΠ΅ΡΠΎΠ΄ΠΎΠΌ ΠΊΠΎΠ²ΠΊΠΈ.
ΒΠ€Π°ΠΊΡΠΈΡΠ΅ΡΠΊΠΈ ΡΠ°ΠΊΠΎΠΉ Π½ΠΎΠΆ ΠΈΠ· ΠΏΠΎΠ΄ΡΠΈΠΏΠ½ΠΈΠΊΠ° ΠΌΠΎΠΆΠ΅Ρ Π²ΡΠΊΠΎΠ²Π°ΡΡ Π»ΡΠ±ΠΎΠΉ ΠΆΠ΅Π»Π°ΡΡΠΈΠΉ, Π² ΠΊΠΎΠ²ΠΊΠ΅ Π½ΠΎΠΆΠ΅ΠΉ Π½Π΅Ρ Π½ΠΈΠΊΠ°ΠΊΠΈΡ ΡΠ΅ΠΊΡΠ΅ΡΠΎΠ².
ΠΡΡΠ°ΡΠΈ, Ρ
ΠΎΡΠΎΡΠΎ Π·Π°ΡΠΎΡΠ΅Π½Π½ΡΠΉ ΠΈ ΠΏΡΠ°Π²ΠΈΠ»ΡΠ½ΠΎ Π·Π°ΠΊΠ°Π»Π΅Π½Π½ΡΠΉ Π½ΠΎΠΆΒ ΠΈΠ· ΠΏΠΎΠ΄ΡΠΈΠΏΠ½ΠΈΠΊΠ° ΠΌΠΎΠΆΠ΅Ρ ΡΠ΅Π·Π°ΡΡ ΡΡΠ΅ΠΊΠ»ΠΎ!
ΠΠ΅ Π²Π΅ΡΠΈΡΠ΅? ΠΠΎΡΠΌΠΎΡΡΠΈΡΠ΅ Π²ΠΈΠ΄Π΅ΠΎ Π½ΠΈΠΆΠ΅, Π² Π½Π΅ΠΌ ΡΠ°ΡΡΠΊΠ°Π·ΡΠ²Π°Π΅ΡΡΡ ΠΊΠ°ΠΊ ΠΎΡΠΊΠΎΠ²Π°ΡΡ ΡΠ°ΠΌΠΎΠ΄Π΅Π»ΡΠ½ΡΡ Π±ΡΠΈΡΠ²Ρ ΠΈΠ· ΠΏΠΎΠ΄ΡΠΈΠΏΠ½ΠΈΠΊΠ°. Π Π² ΠΊΠΎΠ½ΡΠ΅ ΠΏΡΠΎΠ²ΠΎΠ΄ΠΈΡΡΡ ΡΠ΅ΡΡ Π½Π° ΡΠ΅Π·ΠΊΡ ΡΡΠ΅ΠΊΠ»Π°, Π° ΡΠ°ΠΊ ΠΆΠ΅ Π±ΡΠΈΡΡΠ΅ Π±ΠΎΡΠΎΠ΄Ρ.
Π‘ΠΎΠ³Π»Π°ΡΠΈΡΠ΅ΡΡ, Π±ΡΠΈΡΠ²Π° — ΡΡΠΎ Π³ΠΎΡΠ°Π·Π΄ΠΎ Π±ΠΎΠ»Π΅Π΅ «ΡΠΎΠ½ΠΊΠΈΠΉ» ΠΈΠ½ΡΡΡΡΠΌΠ΅Π½Ρ ΡΠ΅ΠΌ ΠΎΠ±ΡΡΠ½ΡΠΉ ΡΠ°ΠΌΠΎΠ΄Π΅Π»ΡΠ½ΡΠΉ Π½ΠΎΠΆ. ΡΠ΅ΠΌ Π½Π΅ ΠΌΠ΅Π½Π΅Π΅ — ΠΈΠ·Π³ΠΎΡΠΎΠ²Π»Π΅Π½Π½Π°Ρ Ρ ΠΏΠΎΠΌΠΎΡΡΡ ΠΊΠΎΠ²ΠΊΠΈ Π±ΡΠΈΡΠ²Π° ΠΏΡΠ΅ΠΊΡΠ°ΡΠ½ΠΎ Π±ΡΠ΅Π΅Ρ ΠΈ ΡΠ΅ΠΆΠ΅Ρ ΡΡΠ΅ΠΊΠ»ΠΎ!
ΠΡΠΎΠ±Π΅Π½Π½ΠΎΡΡΠΈ ΠΈΠ·Π³ΠΎΡΠΎΠ²Π»Π΅Π½ΠΈΡ Π½ΠΎΠΆΠ° ΠΈΠ· ΠΏΠΎΠ΄ΡΠΈΠΏΠ½ΠΈΠΊΠ°
1.ΠΠ±ΠΎΠΉΠΌΠ° ΠΏΠΎΠ΄ΡΠΈΠΏΠ½ΠΈΠΊΠ° ΡΠ°ΡΠΏΠΈΠ»ΠΈΠ²Π°Π΅ΡΡΡ Π±ΠΎΠ»Π³Π°ΡΠΊΠΎΠΉ Π½Π° Π·Π°Π³ΠΎΡΠΎΠ²ΠΊΠΈ Π½Π΅ΠΎΠ±Ρ ΠΎΠ΄ΠΈΠΌΠΎΠΉ Π΄Π»ΠΈΠ½Ρ.2. ΠΠΎΠ²ΠΊΠ° Π²Π΅Π΄Π΅ΡΡΡ ΠΏΡΠΈ Π΄ΠΎΡΡΠ°ΡΠΎΡΠ½ΠΎ Π½ΠΈΠ·ΠΊΠΎΠΉ ΡΠ΅ΠΌΠΏΠ΅ΡΠ°ΡΡΡΠ΅ ΠΎΡ ΡΠ²Π΅ΡΠ»ΠΎΠΊΡΠ°ΡΠ½ΠΎΠ³ΠΎ Π΄ΠΎ ΡΠ΅ΠΌΠ½ΠΎΠΊΡΠ°ΡΠ½ΠΎΠ³ΠΎ.
3. ΠΠ±Π΄ΠΈΡΠΊΡ Π΄Π΅Π»Π°Π΅ΠΌ ΠΏΠ΅ΡΠ΅Π΄ Π·Π°ΠΊΠ°Π»ΠΊΠΎΠΉ Π½Π° ΡΠΎΡΠΈΠ»Π΅ ΠΈΠ»ΠΈ Π»Π΅Π½ΡΠ΅.
4. ΠΠ΅Π»Π°ΡΠ΅Π»ΡΠ½ΠΎ ΠΏΡΠΎΠΈΠ·Π²Π΅ΡΡΠΈ Π½ΠΎΡΠΌΠ°Π»ΠΈΠ·Π°ΡΠΈΡ — ΡΠ°Π·ΠΎΠ³ΡΠ΅Π² Π΄ΠΎΒ Β 750-770Π‘, Π·Π°ΡΠ΅ΠΌ Π²ΡΠ΄Π΅ΡΠΆΠΊΠ° 5-7 ΠΌΠΈΠ½ ΠΈ ΠΎΡ Π»Π°ΠΆΠ΄Π΅Π½ΠΈΠ΅ Π½Π° Π²ΠΎΠ·Π΄ΡΡ Π΅. ΠΡΠΎΠ²ΠΎΠ΄ΠΈΡΡΡ 2-4 ΡΠ°Π·Π°.
5. ΠΠ°ΠΊΠ°Π»ΠΊΠ°. ΠΠ°ΠΊΠ°Π»ΠΊΠ° ΡΠ°ΠΌΠΎΠ΄Π΅Π»ΡΠ½ΠΎΠ³ΠΎ Π½ΠΎΠΆΠ° ΠΈΠ· ΠΏΠΎΠ΄ΡΠΈΠΏΠ½ΠΈΠΊΠ° ΠΏΡΠΎΠΈΠ·Π²ΠΎΠ΄ΠΈΡΡΡ ΠΏΡΠΈ ΡΠ΅ΠΌΠΏΠ΅ΡΠ°ΡΡΡΠ΅ 830Π‘. ΠΠΏΡΠ΅Π΄Π΅Π»ΡΡΡ ΡΠ΅ΠΌΠΏΠ΅ΡΠ°ΡΡΡΡ ΠΌΠΎΠΆΠ½ΠΎ ΠΏΠΎ ΠΌΠ°Π³Π½ΠΈΡΡ — ΠΏΡΠΈΠΊΠ»Π°Π΄ΡΠ²Π°Π΅ΡΡ ΠΊ Π·Π°Π³ΠΎΡΠΎΠ²ΠΊΠ΅ ΠΈ ΠΊΠ°ΠΊ ΠΏΠ΅ΡΠ΅ΡΡΠ°Π»ΠΎ ΠΌΠ°Π³Π½ΠΈΡΠΈΡΡΡΡ — ΠΏΠΎΡΠ° Π·Π°ΠΊΠ°Π»ΠΈΠ²Π°ΡΡ.
ΠΠΎΠΆΠ½ΠΎ ΠΏΡΠ΅Π΄Π²Π°ΡΠΈΡΠ΅Π»ΡΠ½ΠΎ ΠΎΡΠΈΠ΅Π½ΡΠΈΡΠΎΠ²Π°ΡΡΡΡ ΠΏΠΎ ΠΏΠΎΠ²Π°ΡΠ΅Π½Π½ΠΎΠΉ ΡΠΎΠ»ΠΈ — ΡΠ΅ΠΌΠΏΠ΅ΡΠ°ΡΡΡΠ° ΠΏΠ»Π°Π²Π»Π΅Π½ΠΈΡ ΡΠΎΠ»ΠΈ 800 Π³ΡΠ°Π΄ΡΡΠΎΠ². ΠΠΎΡΡΠΏΠ°Π΅ΠΌ Π·Π°Π³ΠΎΡΠΎΠ²ΠΊΡ ΡΠΎΠ»ΡΡ ΠΈ ΠΊΠ°Π»ΠΈΠΌ, ΠΊΠ°ΠΊ ΡΠΎΠ»Ρ Π½Π° ΠΊΠ»ΠΈΠ½ΠΊΠ΅ Π½Π°ΡΠ°Π»Π° ΠΏΠ»Π°Π²ΠΈΡΡΡΡ, ΡΠΎ Π±Π΅ΡΠ΅ΡΡΡ ΠΌΠ°Π³Π½ΠΈΡ ΠΈ ΠΏΡΠΎΠ²Π΅ΡΡΠ΅ΡΡΡ Π΄ΠΎΡΡΠΈΠΆΠ΅Π½ΠΈΠ΅ ΡΠ΅ΠΌΠΏΠ΅ΡΠ°ΡΡΡΡ Π·Π°ΠΊΠ°Π»ΠΊΠΈ.
6. ΠΠ°ΠΊΠ°Π»ΠΊΠ° ΠΏΡΠΎΠΈΠ·Π²ΠΎΠ΄ΠΈΡΡΡ Π² ΠΌΠ°ΡΠ»Π΅. Π’Π΅ΠΌΠΏΠ΅ΡΠ°ΡΡΡΠ° ΠΌΠ°ΡΠ»Π° 45-60 Π³ΡΠ°Π΄ΡΡΠΎΠ². ΠΡΠ΄Π΅ΡΠΆΠ°ΡΡ Π² ΠΌΠ°ΡΠ»Π΅ Π½Π°Π΄ΠΎ Π² ΡΠ΅ΡΠ΅Π½ΠΈΠΈ ΡΠ°ΡΠ°, ΠΏΡΠΈ ΡΡΠΎΠΌ Π½Π΅Π»ΡΠ·Ρ Π±ΠΎΠ»ΡΠ°ΡΡ Π·Π°Π³ΠΎΡΠΎΠ²ΠΊΡ ΠΈ ΠΏΡΠΈΡΠ»ΠΎΠ½ΡΡΡ Π΅Π΅ ΠΊ ΡΡΠ΅Π½ΠΊΠ°ΠΌ.
7. ΠΠΎΡΠ»Π΅ Π·Π°ΠΊΠ°Π»ΠΊΠΈ Π½Π°Π΄ΡΠΈΠ»Ρ Π΄ΠΎΠ»ΠΆΠ΅Π½ ΡΠΊΠΎΠ»ΡΠ·ΠΈΡΡ ΠΏΠΎ ΡΡΠ°Π»ΠΈ. Π ΠΊΠ»ΠΈΠ½ΠΎΠΊ — ΡΠ°ΡΠ°ΠΏΠ°ΡΡ ΡΡΠ΅ΠΊΠ»ΠΎ.
8. ΠΠΎΡΠ»Π΅ Π·Π°ΠΊΠ°Π»ΠΊΠΈ Π½Π΅ΠΎΠ±Ρ ΠΎΠ΄ΠΈΠΌΠΎ ΠΏΡΠΎΠΈΠ·Π²Π΅ΡΡΠΈ ΠΎΡΠΏΡΡΠΊ, Π΄Π»Ρ ΡΡΠΎΠ³ΠΎ ΡΠ°ΠΌΠΎΠ΄Π΅Π»ΡΠ½ΡΠΉ Π½ΠΎΠΆ ΠΈΠ· ΠΏΠΎΠ΄ΡΠΈΠΏΠ½ΠΈΠΊΠ° ΠΊΠ»Π°Π΄Π΅ΡΡΡ Π² Π΄ΡΡ ΠΎΠ²ΠΊΡ Π½Π° 2 ΡΠ°ΡΠ° ΠΈ Π³ΡΠ΅Π΅ΡΡΡ Π΄ΠΎ ΡΠ΅ΠΌΠΏΠ΅ΡΠ°ΡΡΡΡ 160-200 Π³ΡΠ°Π΄ΡΡΠΎΠ². Β ΠΡ Π»Π°ΠΆΠ΄Π΅Π½ΠΈΠ΅ ΠΏΡΠΎΠΈΠ·Π²ΠΎΠ΄ΠΈΡΡΡ ΠΏΡΠΎΡΡΡΠΌ ΠΎΡΠΊΠ»ΡΡΠ΅Π½ΠΈΠ΅ΠΌ Π΄ΡΡ ΠΎΠ²ΠΊΠΈ.
Π§Π΅ΠΌ ΡΠΎΠ»ΡΠ΅ Π½ΠΎΠΆ — ΡΠ΅ΠΌ ΠΌΠ΅Π½ΡΡΠ΅ ΠΌΠΎΠΆΠ½ΠΎ ΡΡΠ°Π²ΠΈΡΡ ΡΠ΅ΠΌΠΏΠ΅ΡΠ°ΡΡΡΡ. ΠΡΠΏΡΡΠΊ ΡΠΌΠ΅Π½ΡΡΠ°Π΅Ρ Ρ ΡΡΠΏΠΊΠΎΡΡΡ Π»Π΅Π·Π²ΠΈΡ, Π½ΠΎ ΡΠ½ΠΈΠΆΠ°Π΅Ρ Π·Π°ΠΊΠ°Π»ΠΊΡ. ΠΠΎΠ»Π΅Π΅ ΡΠΎΠ»ΡΡΡΠΉ ΠΊΠ»ΠΈΠ½ΠΎΠΊ Π²ΡΠ΄Π΅ΡΠΆΠΈΠ²Π°Π΅Ρ Π½Π°Π³ΡΡΠ·ΠΊΡ Π½Π° ΠΈΠ·Π»ΠΎΠΌ Π·Π° ΡΡΠ΅Ρ ΡΠ²ΠΎΠΈΡ Π³Π°Π±Π°ΡΠΈΡΠΎΠ², ΡΠ°ΠΊ ΡΡΠΎ ΠΌΠΎΠΆΠ½ΠΎ ΠΎΡΠΏΡΡΠΊΠ°ΡΡ ΠΏΡΠΈ ΠΌΠ΅Π½ΡΡΠ΅ΠΉ ΡΠ΅ΠΌΠΏΠ΅ΡΠ°ΡΡΡΠ΅.
9. ΠΠ°ΡΠΎΡΠΊΠ° ΡΠ°ΠΌΠΎΠ΄Π΅Π»ΡΠ½ΠΎΠ³ΠΎ Π½ΠΎΠΆΠ° ΠΈΠ· ΠΏΠΎΠ΄ΡΠΈΠΏΠ½ΠΈΠΊΠ° ΠΏΡΠΎΠΈΠ·Π²ΠΎΠ΄ΠΈΡΡΡ Π½Π° Π°Π»ΠΌΠ°Π·Π½ΡΡ Π±ΡΡΡΠΊΠ°Ρ . Π° ΡΠ»ΠΈΡΠΎΠ²ΠΊΠ° Π²Π΅Π΄Π΅ΡΡΡ Ρ ΠΏΠΎΠΌΠΎΡΡΡ Π°Π»ΠΌΠ°Π·Π½ΠΎΠΉ ΠΏΠ°ΡΡΡ.
ΠΡΠ°Π²ΠΈΠ»ΡΠ½ΠΎ ΠΈΠ·Π³ΠΎΡΠΎΠ²Π»Π΅Π½Π½ΡΠΉ Π½ΠΎΠΆ ΠΈΠ· ΠΏΠΎΠ΄ΡΠΈΠΏΠ½ΠΈΠΊΠ° ΡΠ°ΡΠ°ΠΏΠ°Π΅Ρ ΡΡΠ΅ΠΊΠ»ΠΎ, Π½Π΅ ΡΡΠΏΠΈΡΡΡ ΠΈ Π½Π΅ Π»ΠΎΠΌΠ°Π΅ΡΡΡ ΠΏΡΠΈ ΠΈΠ·Π³ΠΈΠ±Π°ΡΡΠΈΡ Π½Π°Π³ΡΡΠ·ΠΊΠ°Ρ .