Полка из ОСБ своими руками
Плиты ОСБ дают возможность очень быстро и совсем недорого осуществить любую фантазию в оформлении пространства, будь то мебель, перегородки в комнате или пол. Полка из ОСБ своими руками делается очень быстро и просто, ее поверхность не требует никаких отделочных материалов и прослужит долгие годы, радуя своей оригинальностью и натуральностью. Сегодня мы познакомим вас с основными характеристиками и видами плит ОСБ, а также расскажем, как можно использовать этот материал для оформления интерьера дома.
к содержанию ↑Виды и характеристики плит ОСБ
Многослойная плита на основе древесной стружки классифицируется по степени прочности. Индекс прочности указывается в цифрах. Для строительных работ используют:
- ОСБ-2. Материал прекрасно подходит для внутренних работ и сухих помещений, поскольку эти плиты имеют низкую влагостойкость.
- ОСБ-3. Это — универсальный материал с повышенными характеристиками. Используется как для внутренних работ, так и для внешних.
- ОСБ-4. Плиты наиболее прочные и влагостойкие. Изделия используют для несущих конструкций в условиях повышенной влажности.
Преимущества плит ОСБ:
- Небольшой вес.
- Повышенная прочность.
- Высокая влагостойкость.
- Простота использования и монтажа.
- Низкая стоимость.
Применение
Среди самых популярных идей применения плит:
- Полы из ОСБ. Для них рекомендуются изделия стандарта ОСБ-3. Укладывают полы из древесной стружки на бетонную стяжку или на специальные деревянные лаги.
- Мебель. Из плит ОСБ можно сделать любой предмет мебели: книжный стеллаж, эргономичный стол, полки, шкаф, кухонный гарнитур, журнальный столик, обувницу, даже подиум для кровати.
- Фасады мебели. Оригинальная идея — фасад шкафа из OSB со сквозными отверстиями. Такой дизайн придает интерьеру дополнительную изюминку.
- Панно на стену. Оригинально смотрится стена, украшенная плитами из ОСБ.
- Витрина в магазине. Современно и стильно выглядит витрина из плит в оформлении торгового пространства.
- Подвесной потолок.
Особенности работы с материалом:
- Производятся плиты в стандартных размерах 244х122 см. Из одной плиты можно сделать целый книжный стеллаж. При расчетах необходимого количества материала, следует продумать точное расположение деталей и плит, чтобы избежать большого количества отходов.
- В качестве инструмента для раскроя плиты лучше использовать циркулярную пилу, так как только она дает идеально ровные края, которые очень трудно получить, работая электрическим лобзиком.
Важно! Стандартные квартиры обладают дефицитом свободной площади, поэтому многие хозяева предпочитают моделировать и делать предметы интерьера самостоятельно по индивидуальным размерам и формам. Кроме того, мебель можно встроить в угол и сэкономить на материалах. Хотя мебель из ОСП своими руками требует декорирования, она получается намного дешевле готовых аналогов.
Далее мы расскажем, как сделать встроенный шкаф из ОСБ своими руками, поскольку этот предмет мебели требует намного больше подготовки, времени и сил, чем полка из ОСб своими руками или стол.
к содержанию ↑Как сделать встраиваемый шкаф-купе самостоятельно?
Встроенный шкаф можно смоделировать в онлайн-программе, которая не только предложит дизайн мебели, но и поможет рассчитать количество, стоимость материалов, фурнитуры и расходников. Чаще всего шкаф строится из мебельных щитов, не требующих облицовки. Но если вы решили использовать ОСБ, то поверхность фасада шкафа лучше обклеить крафт-бумагой.
Важно! Если вы хотите сделать шкаф сложной конфигурации, то используйте гипсокартон, который способен гнуться по шаблонам до любых форм.
Для квартир небольшой площади встроенный шкаф-купе — отличный выход, поскольку он очень вместительный, к тому же, зрительно расширяет пространство. Кроме того, встраиваемая мебель очень рационально использует пространство. Экономия и повышенная прочность достигается за счет использования несущих конструкций здания вместо нескольких деталей шкафа. Например:
- Низ мебели замещается облицовкой пола.
- Крыша — плитой перекрытия.
- Боковую стенку заменяет стена.
- Задняя стенка — стена помещения.
Материалы для работы
Для изготовления шкафа глубиной 60 см, шириной 190 см, встраиваемого в угол стандартной квартиры с высотой потолка 2,5 метра, понадобится следующее количество материалов:
- Для дверей: плита 2439х952 мм.
Важно! При расчете учитывался регулировочный зазор по высоте 45 мм, нахлест полотен для купе 20 мм и толщина материала 16 мм.
- Боковая панель: лист 2484х600 мм.
- Крыша: плита 1900х600 мм.
- Перегородка: лист 2484х500 мм.
- Полки размером 934х500 мм.
- Двухполосные направляющие. Приобретите комплект из двух штук по 95 см каждая.
- Штанга для вешалок 934 мм.
- Сетка для обуви той же длины, что и штанга.
- Крепеж: 32 уголка, 64 метиза.
- Материал для декорирования фасада мебели (декоративная лента для лицевой кромки всех деталей, лак, крафт-бумага или самоклейка).
- Фурнитура. После сборки шкафа монтируются противопыльные щетки-шлегели, позиционеры.
Этапы работы
Технология изготовления встраиваемой конструкции выглядит следующим образом:
- Проектирование (чертеж, набросок или полноценный проект).
- Перенос чертежа на стену. Это — самый ответственный этап, поскольку от него зависит ресурс и стоимость шкафа.
- Установка боковой стенки и перегородки. Если шкаф имеет высоту от плиты до плиты, то щиты крепятся к потолку, полу и задней стенке. Если конструкция ниже, то детали скрепляются крышей.
- Установка полок, ящиков и штанг. Если вы планируете съемные полки, то прикрепите их на специальную фурнитуру. Если планируете жесткую фиксацию, то используйте уголки. Чтобы конструкция была более устойчивой и надежной, лучше использовать жесткую фиксацию.
- Монтаж дверей. Для традиционных шкафов используйте распашные конструкции, для шкафов-купе — раздвижные модификации дверей.
- Декорирование плит ОСБ или покрытие поверхности бесцветным лаком.
к содержанию ↑Важно! Используйте для встраиваемой мебели только раздвижные двери, поскольку самостоятельно установить распашные двери гораздо сложнее, чем навесить на направляющие дверные полотна, так как:
- в стене, которая выполняет роль боковой стенки, невозможно сделать выборку под фурнитуру мебельных петель;
- не каждый домашний мастер имеет в наличии фрезер для выборки глухого отверстия большого диаметра.
Советы по изготовлению встраиваемой мебели:
- Если вы планируете трехстворчатый шкаф, то используйте следующую схему: на ближних направляющих перемещается средняя дверь, в дальних — две боковые створки. Технология расчета ширины створок в этом случае сохраняется — нахлест 20 мм с каждого края полотна.
- При проектировании шкафа из ОСБ учитывайте следующие эксплуатационные особенности: оптимальная высота бельевых полок — 30 см, для обувных полок возможны произвольные размеры отделения, планку для вешалок ставьте на индивидуальную высоту.
- При изготовлении шкафа обязательно выдерживайте горизонталь и вертикаль опорных поверхностей. Все детали фиксируйте друг с другом по вертикальному отвесу.
Важно! Не делайте зазоры между плоскостями несущих конструкций и направляющими. Используйте декоративную планку, чтобы замаскировать отсутствие горизонтали как пола, так и потолка.
- При значительных неровностях стен детали разделите на несколько частей для упрощения подгонки.
- Учитывайте характеристики напольного покрытия при опирании на них полотен дверей.
- Если вы планируете зеркала внутри конструкции, то можно закрепить их простейшими скобами и отделить полимерными, войлочными или резиновыми прокладками.
Важно! Стеклянные полки также укладывайте через прокладки, а для светопрозрачных дверок используйте специальную фурнитуру.
- Производите раскладку деталей на плитах ОСБ вручную или в любом графическом редакторе, чтобы снизить расход кроя. Не забывайте учитывать ширину пропила и радиусы поворота электролобзика.
Видеоматериал
Недорого, стильно и современно можно сделать любую мебель из ОСБ своими руками. Главное преимущество плит — отсутствие дополнительной обработки поверхности. Оригинальные по своей конструкции шкафы из плит придадут пространству лофтовый акцент. И даже если комната оформлена в классическом стиле, то ничто не мешает комбинировать его с индустриальным OSB. Удачи!
Поделиться в соц. сетях:
serviceyard.net
|
funer.ru
Стеллаж из фанеры своими руками
Приветствую, Самоделкины!Когда на улице плохая погода самое время немного прибраться на мансарде и в мастерской, что собственно говоря и решил сделать мастер-самодельщик Максим Козлов (YouTube канал «Maxim Kozlov»). Дочитав эту статью до конца, вы узнаете, как своими руками можно изготовить стеллаж для хранения рыболовных принадлежностей.
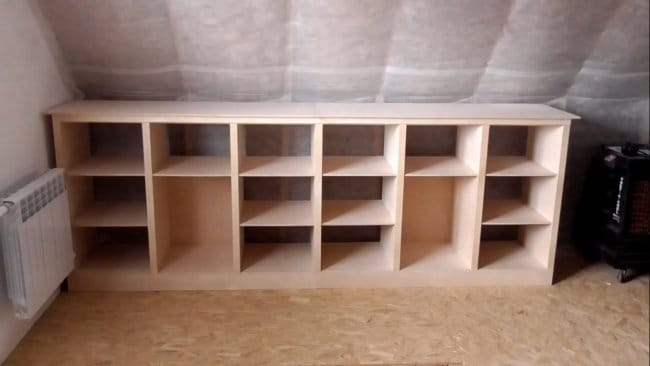
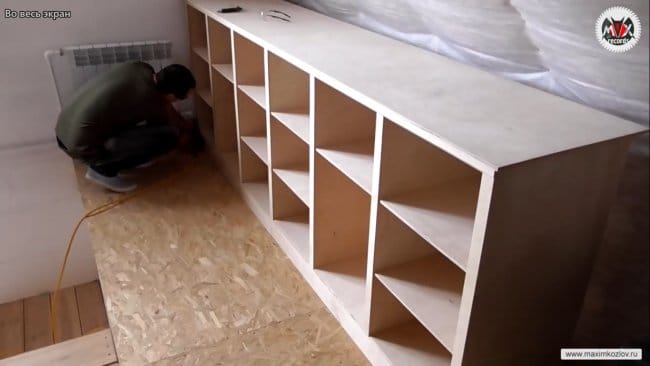
Основным материалом данной самоделки будет фанера. Собственно, сам стеллаж было решено делать из вот этих листов шлифованной десятки, которые оказались не очень хорошего качество, так как даже хранясь плашмя их довольно прилично покрутило.
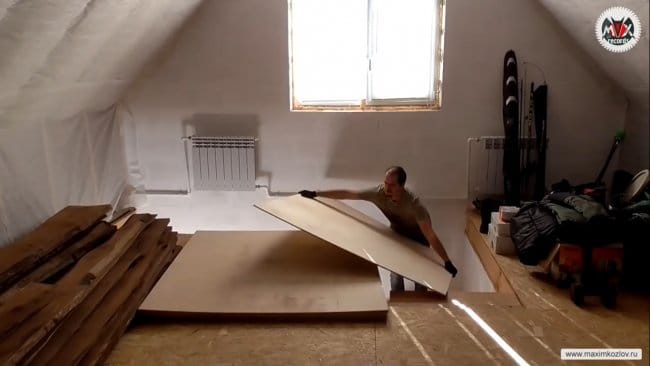
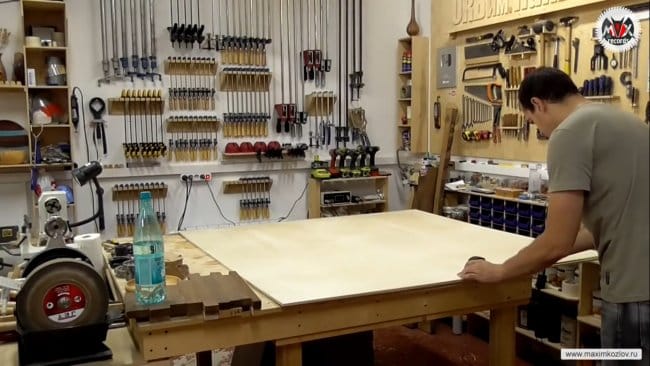
По этой самой причине автор решил с ними не церемониться. Все листы необходимо распустить на 3 равных полосы по 500мм каждая, что соответствует глубине стеллажа.
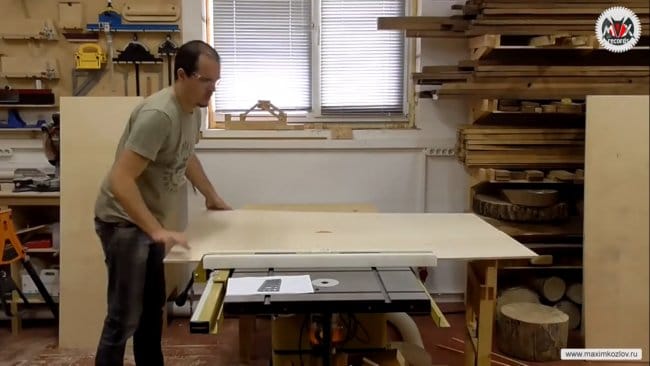
При торцевом раскрое полос фанеры автор приноровился использовать толкатель, который очень успешно позволяет вести такую заготовку позволяя не отрывать ее от параллельного упора. Для этой цели вполне сгодится любой прижим, хоть от фуганка, хоть от фрезерного стола, лишь бы на основе была резина, а не наждачка, как в данном случае, ибо тут все же может проскользнуть и тогда линия пиления будет испорчена.
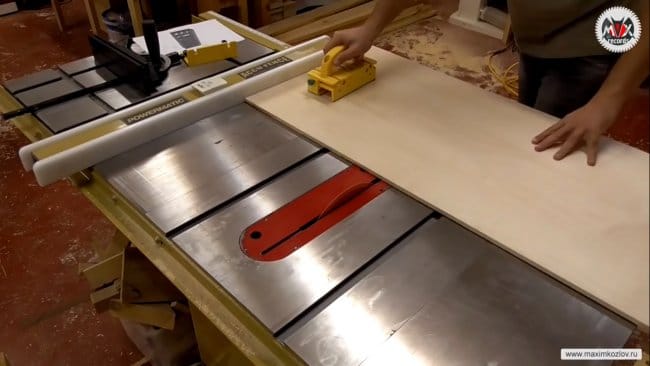
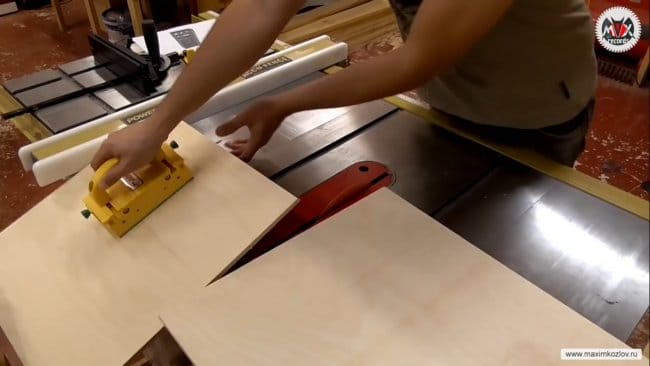
Помимо этого, данный метод особенно хорош в случае с такой кривой фанерой. При помощи этого же прижима мастер успешно расправлял фанерный лист во время пиления. Таким образом можно работать со стандартами квадратными листами фанеры на обычном распиловочном станке с не меньшей точностью чем на форматнике.
Единственно, как не просчитывай ориентацию листа и раскрой, со сколами ничего не поделаешь и получившиеся после пиления заготовки нуждаются в дополнительной обработке наждачной бумагой. Автор всегда старается, чтобы все сколы были на черновой, невидимой глазу стороне, поэтому удаление оных по сути нужно только для качественной сборки.
Во времена стоковых дисков для продольного пиления сколы можно было легко получить и с обеих сторон. В этом случае линию реза необходимо заклеивать, например, малярным скотчем. Переходя к сборке деталей стеллажа, мастер сделал на столе сборочный стапель. О подобных приспособлениях всегда стоит задуматься, когда количество изделий, либо сборочных узлов, начинает измеряться десятками и более. В данном случае стоит подумать про какой-то сборочный кондуктор, чтобы облегчить себе жизнь и поддерживать точность изделия.
В этот раз перед автором была задача разбить стеллаж на 6 независимых частей. Это необходимо для удобства подъема изделия на мансарду. Поэтому он придумал систему стоек из той же самой фанеры.
Сам стеллаж было решено собирать по классике, когда в изделии нет никаких пазов и прочего. Все зазоры и прочий конструктив задаются самой фанерой, ну а монтаж в данном случае производится на шпильку. Нет, не на гвоздь, а именно на микрошпильку, так как шпилька для относительно тонкой фанеры просто идеальна. Держится она на ней очень прочно, а в случае выхода за пределы листа, ее легко подрезать, торцы ей не расщепить, а следы монтажа при этом практически невозможно заметить. К тому же помогая в некоторых местах клеем, такого соединение будет более чем достаточно.
Далее автор пристрелил крайние стойки к глухим боковым стенкам стеллажа, что дало старт процессу сборки самих колонн. Если что-то не понятно, можете скачать подробный чертеж. Но по сути по данной технологии можно изготавливать практически любые шкафы и стеллажи из листового материала, обходясь лишь обыкновенным распиловочным станком и монтажным инструментом имеющимся практически у каждого мастера, а тем более самодельщика. Ну а уже по итогам отделки можно добиться практически любого внешнего вида. В этом деле как видите очень многое решает именно отделка, ну а для самого изделия главное — это правильные пропорции, надежность конструкции и неприхотливость к погодным условиям. Этого у фанеры как раз не занимать.
Конечно на данном этапе все эти звенья стеллажа выглядит откровенно хлипкими, по сути оно так и есть, но при сборке воедино и добавления задней подшивки все становится монолитным. Стоит повториться, что в данном случае автор главной задачей обозначил возможность перемещения изделия в одно лицо, а фанера, как известно, штука довольно тяжелая.
В данном проекте автор использовал фанеру шлифованную с одной стороны, которой она и смотрела на нас. По большому счету дополнительная шлифовка в данном случае, например, под покраску здесь совершенно ни к чему, а это в свою очередь позволяет сэкономить немалое количество времени и сил.
Две из шести колонн стеллажа было решено сделать с двумя полками. Это сделано для того, чтобы имелась возможность для хранения довольно крупных вещей. А заодно именно в этих секциях давайте сделаем подшивку для дополнительной жесткости. В качестве подшивки будем использовать все ту же 10-миллиметровую фанеру, которую необходимо отпилить четко по размеру ниши так, чтобы она вставала туда с натягом.
Двух таких ребер жесткости будет вполне достаточно для всего стеллажа. Стеллаж как раз отличает от шкафа не только отсутствие двери и меньшая глубина, но и отсутствие задней стенки, по этой причине в данном случае приходится обходиться только ребрами жесткости.
В результате автор совершенно спокойно поднял все части по отдельности наверх и принялся за процесс стягивания. Стяжку он производил при помощи саморезов. Получилось весьма прочно, к тому же данные саморезы имеют нечто похожее на пресс шайбу.
Разумеется, сначала все это дело необходимо выровнять, стянуть струбцинами, а уже только после этого можно засверливаться и скручивать саморезами. На данном этапе было решено обойтись без клея, так как хотелось, чтобы всегда была возможность разборки, модификации, либо переноса всей конструкции.
После того, как все было стянуто по фасадной части, можно было прокинуть всю конструкцию и пройтись по тылам.
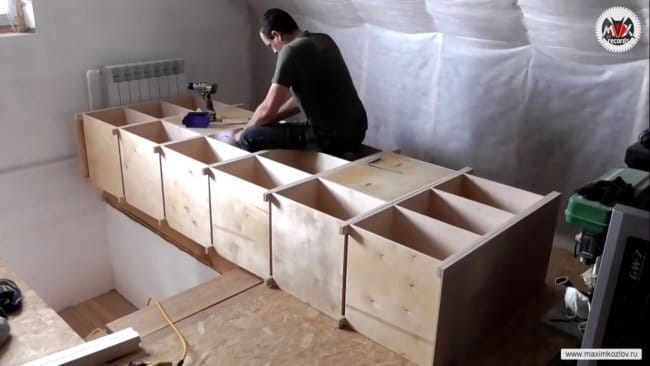
Гарнитурчик получился довольно-таки тяжелый, как никак все же ушли без малого практически все 8 листов фанеры, а это около 120кг. Поэтому ронять и ставить получившееся изделие на место нужно очень аккуратно.
Перед установкой столешниц, к торчащим окончанием стоек необходимо пристрелить ребра жесткости, чтобы не допустить прогибания.
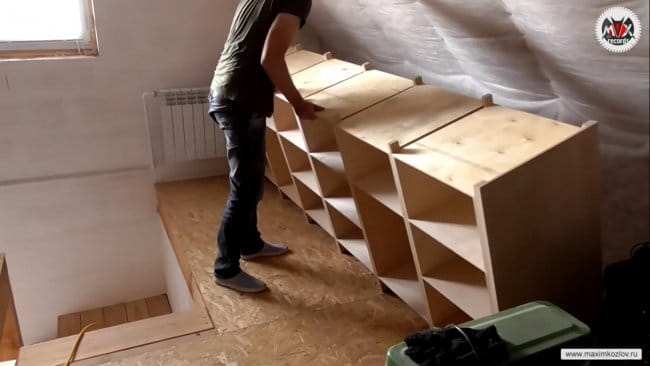
Далее можно приступать к распилу последнего фанерного листа.
Ну а заключительными элементами были детали цоколей и подстолье, которые помимо эстетической составляющей придавали дополнительную жесткость всей конструкции.
Изначально мастер хотел заморочиться и закрыть все это дело термодеревом, в том числе все торцы фанеры, но для мастерской как-то жаба задушила, да и к тому же уже была применена открытая стяжка. Но тем не менее эти элементы все же было решено задекорить, добавив скос под 45 градусов, что натолкнуло автора на мысль закрыть и торцы стоек стеллажа остатками 6мм фанеры, которая оставалась от одного из предыдущих проектов.
Материала конечно ушло немало, но получилось довольно много места для хранения, причем не только для рыболовных принадлежностей, но и всякой другой мелочевки. Красить стеллаж автор не стал, так как стало жалко рисунок фанеры, да и времени. На этом все. Благодарю за внимание. До новых встреч!
Видеоролик автора:
Источник
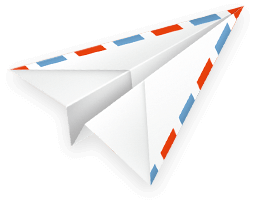
Получайте на почту подборку новых самоделок. Никакого спама, только полезные идеи!
*Заполняя форму вы соглашаетесь на обработку персональных данных
Становитесь автором сайта, публикуйте собственные статьи, описания самоделок с оплатой за текст. Подробнее здесь.usamodelkina.ru